Нормы времени и нормы выработки при контактной сварке
При контактной сварке под нормой времени понимают время, необходимое для выполнения единицы работы. За единицу работы обычно принимают одно свариваемое изделие. Нормой выработки в этом случае будет количество изделий, свариваемых в час или за смену.
Норма времени при контактной сварке складывается так же, как и в случае электродуговой сварки, из основного, вспомогательного, подготовительно-заключительного времени, времени обслуживания рабочего места и времени отдыха.
Основное время — время работы контактной машины при изготовлении изделия. Основное время зависит от степени механизации контактной машины и ее мощности. Основное время обычно имеет меньшее значение при работе на механизированных контактных машинах.
Вспомогательное время — время, затрачиваемое на установку заготовок, их центровку, зажатие (при стыковой сварке), перемещение (главным образом при точечной сварке) и др.
Вспомогательное время зависит от конструкции зажимных устройств, требуемой точности при сварке и наличия приспособлений, фиксирующих заготовки.
Подготовительно-заключительное время — время, затрачиваемое на получение задания, инструкций и сдачу работы. Подготовительно-заключительное время при контактной сварке имеет сравнительно небольшое значение.
Время обслуживания рабочего места — время, затрачиваемое на подготовку машины к сварке (смена электродов, их зачистка, зачистка контактов контактора).
При нормировании контактной сварки основное и вспомогательное время можно определять по таблицам. Подготовительно-заключительное время, время обслуживания рабочего места и время отдыха составляют 10—20% от суммы основного и дополнительного времени. Ниже приводятся данные для определения основного и дополнительного времени при стыковой, точечной и шовной сварке.
Таблица 123.Основное время при стыковой сварке оплавлением.
Диаметр заготовки в мм | Время непрерывного оплавления и осадки при сварке на автоматах в мин. | Время подогрева, оплавления и осадки при сварке на машинах с неавтоматическим управлением в мин. |
6 | 0,067 | 0,067 |
10 | 0,183 | 0,133 |
16 | 0,117 | 0,7 |
22 | 0,166 | 0,35 |
28 | 0,267 | 5,45 |
35 | 0,416 | 0,7 |
50 | 0,583 | — |
70 | 0,75 | — |
100 | 1,0 | — |
Таблица 124.Вспомогательное время в минутах при стыковой сварке на машинах с рычажными зажимами.
Оснастка зажимов | Вес сваренной детали в кг | |||
до 1 | 1—3 | 3—5 | 5—7,5 | |
С упорами и фиксаторами | 0,2—0,25 | 0,25—0,35 | 0,35—0,45 | 0,45—0,55 |
Без упоров, но с фиксаторами | 0,3—0,35 | 0,35—0,45 | 0,45—0,55 | 0,55—0,65 |
Стыковая сварка. Основное время при стыковой сварке оплавлением можно определять по данным табл. 123, а вспомогательное время по табл. 124.
Точечная сварка. Основное время при точечной сварке определяется по формуле:
где n — число точек в детали;
t1 — основное (машинное) время на сварку одной точки.
Вспомогательное время при точечной сварке на универсальных одноточечных машинах стационарного типа определяется по данным табл. 125.
Таблица 125.Вспомогательное время в минутах при точечной сварке.
№ п/п | Краткая характеристика детали | Вес детали в кг | ||
до 1 | 1—3 | 3—5 | ||
1 | Собранная деталь, готовая для сварки | 0,18 | 0,21 | 0,25 |
2 | Простая деталь, собираемая из двух взаимно сопрягающихся заготовок без приспособления | 0,22 | 0,30 | 0,35 |
3 | Деталь, собираемая из двух заготовок по шаблону | 0,27 | 0,32 | 0,37 |
4 | Деталь, собираемая из двух заготовок по шаблону с креплением быстродействующим зажимом | 0,34 | 0,40 | 0,40 |
Шовная сварка.
Основное время при шовной сварке определяется по формуле:
где l —длина шва на детали в м; v — скорость сварки в м/мин.
Вспомогательное время при шовной сварке определяется по данным табл. 126.
Таблица 126.Вспомогательное время в минутах при шовной сварке.
Вес детали в кг | До 3 | 3—5 | 5—10 | 10—15 |
Значение вспомогательного времени | 0,30 | 0,38 | 0,50 | 0,60 |
Снижение затрат на сварку
Многие компании всегда выбирают сварочное оборудование и материалы с самой низкой стоимостью. Это можно понять, но они могут упускать из внимания тот факт, что вместо того, чтобы пытаться что-то выгадать на стоимости разовой покупки, гораздо эффективнее экономить на производительности. Сокращение общих затрат на сварку и повышение производительности позволят вам экономить средства год за годом.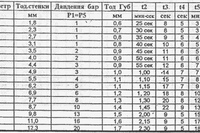
Если обратиться к типичной модели производственного модуля, можно заметить, что к материалам относится лишь 20% стоимости сварки, тогда как подавляющая часть затрат – более 80 процентов – соответствует трудовым и накладным расходам. Следовательно, если компания сэкономит 10% от стоимости сварочных материалов, компания выиграет лишь два процента от общей стоимости сварки. Но если компания сможет сэкономить 10 процентов от трудовых и накладных затрат, она выиграет 8% от общей стоимости сварки в соответствующем производственном модуле. То же самое относится и к процессу ручной или полуавтоматической сварки углеродистой стали.
Ниже перечислено 10 шагов, которые компании могут предпринять для того, чтобы сократить затраты на сварку и получить выгоду благодаря повышению эффективности.
1. Проведите анализ снабжения точек сварки расходными материалами и аксессуарами
Во многих цехах оператору часто приходится идти за новым контактным наконечником, катушкой проволоки или другими сварочными аксессуарами в инструментальную кладовую или на склад. Это приводит к ненужной потере драгоценного рабочего времени в производственном модуле и падению производительности в целом. Чтобы повысить производительность работы и максимально сократить простой, компаниям нужно разместить возле сварочной станции хотя бы минимальный запас всех необходимых материалов, в том числе защитного газа, флюса и проволоки. Также производительность можно повысить, используя катушки большего объема, например, заменив катушки весом 25 фунтов на катушки весом 44 или 60 фунтов или даже виды упаковки еще большего размера, например, катушки или барабаны весом 1000 фунтов. Такое незначительное изменение означает, что на замену катушек станет уходить меньше времени, которое будет постоянно суммироваться на протяжении недель, месяцев и годов.
Помимо этого, в цехах нужно обращать внимание на уровень расхода защитного газа. На горелке можно разместить простое устройство, называемое импульсной турбиной, которое будет отображать цифровые показания пиков давления газа и скорости расхода. При высоком расходе могут оказаться целесообразными инвестиции в устройства импульсной защиты, которые позволят понизить давление газа, устранить пики и сократить ненужные траты.
Также потенциальным источником убытков могут быть утечки в системе подачи газа. Проанализировав объем закупаемых каждый год расходных материалов и входящую в него долю газа, компания может оценить, насколько заметные убытки она несет. Для этого у производителей и дистрибьюторов сварочных материалов можно узнать средние показатели расхода газа. При подозрении на слишком высокие потери можно воспользоваться простым способом выявления утечек – отключить на выходные систему подачи газа. Отметьте объем газа в вечер пятницы и затем еще раз утром понедельника, и тогда Вы сможете узнать, убывал ли газ во время отключения системы.
2. Проведите анализ эффективности работы с материалами
Также затраты на сварку можно сократить, более логично организовав доставку материалов к сварочной станции. В качестве примера можно привести компанию, которая занималась производством бетономешалок. В процессе производства компания изготовляла 10 деталей для одной секции бетономешалок и затем переходила к изготовлению 10 деталей для другой секции, и так далее. По мере производства деталей их ставили на пол цеха. Когда наступало время сварки, оператору приходилось самостоятельно отыскивать и сортировать нужные ему детали. Когда сторонний эксперт обратил на это внимание, компания стала укладывать каждую деталь на тележку. Таким образом все детали для изготовления одной мешалки стали храниться вместе и при необходимости могли быть быстро перемещены в зону сварки.
Такой сценарий также применим к компаниям, которые привлекают для изготовления определенных деталей сторонние предприятия. Хотя доставка деталей по партиям обычно бывает дороже, она с лихвой окупится благодаря снижению временных затрат, так как Вам не придется организовывать и искать нужные детали на этапе сварки.
Подсчитайте, сколько операций приходится совершить с каждой деталью – тогда Вы сможете понять, насколько много на это уходит времени. Чтобы измерить такой неочевидный параметр, сварщиков можно попросить оставлять после каждого контакта с деталью отметку мелом. Многие компании оказываются поражены, узнав, насколько часто приходится поднимать, переносить и опускать каждую деталь в процессе производства. В одном из случаев перенос сварочного цеха ближе к станции термической обработки позволил избавиться от четырех лишних операций с каждой деталью. Другими словами, максимальное сокращение числа операций с каждой деталью и более эффективная организация производственной линии или модуля может привести к значительному снижению общих затрат.
3. Не допускайте наложения швов излишне большого сечения
Одним из «смертных грехов» каждого сварочного цеха является наложение швов излишне большого сечения. Другими словами, когда по чертежу требуется шов шириной 1/4 дюйма (6,3 мм), в большинстве цехов накладывают шов шириной 5/16 дюйма (7,9 мм). Почему? Во-первых, у них может не быть галтельных шаблонов и они могут не знать точную ширину шва, а во-вторых, лишний материал может быть добавлен «для перестраховки», чтобы быть уверенным, что в месте сварки достаточно наплавленного металла.
Однако слишком большое сечение приводит к огромному перерасходу материалов. Вернемся к нашему примеру. При ширине шва 6,3 мм большинство сварщиков будет тратить по 0,13 фунтов сварочного материала на фут. Шов шириной 7,9 мм требует 0,20 фунтов сварочного материала на фут – то есть на 56% больше, чем действительно нужно. Более того, нужно учесть дополнительный труд при наплавлении более широкого шва. Кроме того, что компании приходится больше платить за лишний, растрачиваемый впустую расходный материал, швы с избыточным наплавленным металлом более уязвимы к деформациям и искривлениям из-за более высокого тепловложения. Каждому сварщику рекомендуется предоставить галтельный шаблон, который позволил бы ему создавать швы точно указанной ширины. Также для борьбы с наложением швов излишне большого сечения можно использовать проволоку меньшего диаметра.
4. Совершенствование существующих процессов и процедур сварки
Попробуйте повысить эффективность уже существующего процесса сварки. Например, для этого можно проанализировать такие параметры, как диаметр проволоки, скорость подачи проволоки, напряжение тока, скорость перемещения, тип газа, способ переноса металла и т. д. Например, если раньше в цеху проводилась сварка с применением короткой дуги и смеси защитного газа в пропорции 75/25, может оказаться более эффективным перейти к процессу с другим газом и струйным переносом металла. В зависимости от состояния деталей также может потребоваться изменение самого процесса работы. Например, если на детали образуется оксид, может быть более разумно перейти к процессу, который позволил бы устранить связанные с загрязнением проблемы вместо того, чтобы отчищать перед сваркой каждую деталь. Ваш поставщик сварочных материалов должен хорошо разбираться в самых последних технологиях и быть способен предоставить консультацию по новым процессам, оборудованию и расходным материалам, которые помогли бы вам оптимизировать процесс сварки в цеху.
5. Оптимизация подготовки соединений
В некоторых случаях при подготовке к сварке может быть эффективнее создать соединение с двумя симметричными скосами одной кромки, чем с односторонним скосом. Для любых материалов толщиной больше 3/4 дюйма (1,9 см) рекомендуются два симметричных скоса одной кромки. Даже такое простое изменение рабочей процедуры может сэкономить много сварочного материала. При толщине пластины 1,9 см на сварку соединения с двумя скосами кромки требуется 1,45 фунта сварочного металла на фут, а для одностороннего скоса – 1,95 фунта на фут.
6. Устранение ненужных точек сварки
Попробуйте изменить конструкцию продукта таким образом, чтобы устранить все лишние точки сварки. К примеру, одна компания, которая занималась производством контейнеров, изначально имела чертеж, который предполагал приварку ручек с каждой стороны контейнера. Сделав простое изменение и заменив их на подъемные пазы, они смогли избавиться от нужды приваривать ручки – и сэкономить таким образом свое время и деньги. В другом случае вместо открытого уголка стали использовать закрытый, что означало снижение расходования металла на заполнение уголка на 1/3.
7. Старайтесь использовать сварку вместо литья
Мы уже упомянули о том, что для повышения эффективности нужно попробовать уменьшить число точек сварки, но как насчет добавления новых? В некоторых случаях может оказаться более затратоэффективным приваривать металлические детали к изделию вместо того, чтобы отливать полностью всё изделие из какого-нибудь дорогого сплава или экзотического металла. Например, компания, которой раньше приходилось прибегать к литью отдельных деталей из сплава с высоким содержанием алюминия, обнаружила, что 50 процентов узла можно изготовить из стандартной конструкционной стали, что позволило сэкономить на материале и таким образом значительно снизить общую стоимость. При этом компании удалось изменить чертеж узла таким образом, чтобы сделать его еще более эффективным.
8. Попробуйте избавиться от дорогостоящего ведения записей
Многие компании полностью «увязают» в ведении деловой документации. С этим могут помочь сегодняшние высокие технологии. Например, Lincoln Electric может предложить программу ArcWorks, которая способна документировать рабочие процедуры, создавать схемы для всеобщего доступа в мастерской, хранить данные о квалификации операторов и многое другое. Такое ПО можно адаптировать к индивидуальным потребностям каждой отдельной компании. Она позволит быстро выявлять и устранять потери и ошибки.
9. Применение роботов и жесткой автоматизации
Сегодняшние технологии способны значительно усовершенствовать процесс производства. Если объем производимых компанией изделий настолько велик, что он позволит окупить потраченные на новое оборудование средства, на предприятии можно установить роботизированные системы сварки. Также они хорошо подходят для тех ситуаций, когда изготавливается большой объем деталей достаточно схожей конструкции, чтобы их мог производить один робот.
Если применение роботов представляется нецелесообразным, для повышения эффективности или качества работы можно прибегнуть к установке креплений или жесткой автоматизации производства. Например, одна компания установила крепления и зажимы для фиксации резервуаров во время сварки. В другом случае автопроизводитель принял решение о необходимости автоматизации из-за большого объем производимых деталей и сложности положений и углов сварки.
10. Проведите проверку безопасности
Хотя это может и не привести к немедленному снижению стоимости сварки, работа с соблюдением техники безопасности в долгосрочной перспективе позволит сократить затраты благодаря меньшему числу несчастных случаев. Например, сюда входят крепления для газовых баллонов для предотвращения их падения, установка предохранительных затворов, которые не допустят обратного поступления горючей смеси при кислородно-газовой резке и маркировка труб для предотвращения несчастных случаев.
Заключение
Это лишь некоторые пункты, на которые Компания Lincoln Electric обращает внимание в рамках своей Программы гарантированного снижения расходов. Эта программа предполагает посещение предприятия экспертами Lincoln для проведения аудита. После проверки они составляют список возможных способов снижения затрат, а предприятие оценивает их приоритет и выбирает наиболее подходящие. Представители Lincoln подсчитывают потенциальную экономию и даже гарантируют определенную сумму сокращения затрат в случае принятия предложенных ими решений. Если этой экономии достичь не удастся, Lincoln компенсирует разницу.
Как говорится, «скупой платит дважды» – всегда старайтесь сократить затраты на сварку и повысить эффективность и производительность работы – ведь такая экономия будет приносить результаты год за годом.
Техника выполнения сварных швов покрытым электродом
Техника выполнения сварных швов
Под техникой выполнения сварных швов понимают выбор режимов сварки и приемы манипулирования электродом.
Возбуждение электрической дуги
Зажигание дуги является одной из основных операций сварочного процесса. Зажигание производится каждый раз до начала процесса сварки, повторное возбуждение дуги — в процессе сварки при ее обрыве.
Возбуждение сварочной дуги производится путем касания торцом электрода поверхности свариваемого изделия с быстрым последующим отводом торца электрода от поверхности изделия. При этом если зазор не слишком велик, происходит мгновенное появление тока и установление столба дуги. Прикосновение электрода к изделию должно быть кратковременным, так как иначе он приварится к изделию («прилипнет»).
Отрывать «прилипший» электрод следует резким поворачиванием его вправо и влево. Возбуждение дуги может производиться либо серией возвратно-поступательных движений с легким прикосновением к поверхности свариваемого металла и последующим отводом от поверхности изделия на 2-4 мм, либо путем царапающих движений торцом электрода по поверхности изделия, которые напоминают чирканье спички. Используйте наиболее удобный для вас способ.
После возбуждения дуги электрод должен выдерживаться некоторое время Точке начала наплавки, пока не сформируется сварной шов и не произойдет расплавление основного металла. Одновременно с расплавлением электрода необходимо равномерно подавать его в сварочную ванну, поддерживая тем самым оптимальную длину дуги. Показателями оптимальной длины дуги является резкий потрескивающий звук, ровный перенос капель металла через дуговой промежуток, малое разбрызгивание.
Длина дуги значительно влияет на качество сварки. Короткая дуга горит устойчиво и спокойно. Она. обеспечивает получение высококачественного шва, так как расплавленный металл электрода быстро проходит дуговой промежуток и меньше подвергается окислению и азотированию. Но слишком короткая дуга может вызывать «прилипание» электрода, дуга прерывается, нарушается процесс сварки. Длинная дуга горит неустойчиво с характерным шипением. Глубина проплавления недостаточная, расплавленный металл электрода разбрызгивается и больше окисляется и азотируется. Шов получается бесформенным, а металл шва содержит большое количество оксидов.
Если во время сварки по какой-либо причине сварочная дуга погаснет, то применяется специальная техника повторного зажигания дуги, обеспечивающая начало сварки с хорошим сплавлением и внешним видом. При повторном зажигании дуга должна возбуждаться на передней кромке кратера, затем через весь кратер переводиться на противоположную кромку, на только что наплавленный металл, и после этого снова вперед, в направлении проводившейся сварки. Если электрод при повторном зажигании дуги не буде достаточно далеко отведен назад, между участками начала и конца сварки останется углубление. Если же при повторном зажигании электрод отвести слишком далеко назад, то на поверхности сварного валика образуется высокий наплыв.
Положение и перемещение электрода при сварке. В процессе сварки электроду сообщаются следующие движения:
- поступательное по оси электрода в сторону сварочной ванны, при этом для сохранения постоянства длины дуги скорость движения должна соответствовать скорости плавления электрода;
- перемещение вдоль линии свариваемого шва, которое называют скоростью сварки; скорость этого движения устанавливается в зависимости от тока, диаметра электрода, скорости его плавления, вида шва и других факторов;
- перемещение электрода поперек шва для получения шва шире, чем ниточный валик, так называемого уширенного валика.
При слишком большой скорости сварки наплавленные валики получаются узкими, с малой выпуклостью, с крупными чешуйками. При слишком медленной скорости перемещения электрода сварной валик имеет слишком большую выпуклость, шов неровный по форме, с наплывами по краям.
Положение электрода при сварке должно соответствовать рис. 2. Сварка осуществляется в направлении как слева направо, так и справа налево, от себя и на себя.
Рис. 2. Угол наклона электрода: а — в горизонтальной плоскости; б- в вертикальной плоскости.
В конце шва нельзя резко обрывать сварочную дугу и оставлять на поверхности металла кратер, являющийся концентратором напряжений и зоной с повышенным содержанием вредных примесей. Во избежание образования кратера необходимо прекратить перемещение электрода, т. е. произвести задержку на 1-2c, затем сместиться назад на 5 мм и быстрым движением вверх и назад оборвать дугу.
При неправильном завершении сварки в месте окончания шва, где погасла дуга, всегда образуется глубокий кратер. Кратер может служить показателем глубины проплавления, однако в конце сварки и наплавки данные кратеры должны заполняться и завариваться. Это производится путем возбуждения дуги в кратере, установления короткой дуги и выдержки в таком положении электрода, вплоть до заполнения расплавленным металлом кратера. Не рекомендуется заваривать кратер, несколько раз обрывая и возбуждая дугу, ввиду образования оксидных и шлаковых загрязнений металла.
Сварной шов, образованный в результате двух движений торца электрода (поступательного и вдоль линии шва), называют «ниточным». Его ширина при оптимальной скорости сварки составляет (0,8-1,5)dэ. Ниточным швом заполняют корень шва, сваривают тонкие заготовки, выполняют наплавочные работы и производят подварку подрезов.
Для наплавки валика без поперечных колебаний электрода необходимо возбудить дугу, растянуть ее и некоторое время удержать на одном месте для прогрева основного металла. Затем постепенно уменьшать длину дугового промежутка, пока не образуется сварочная ванна соответствующего размера. Она должна хорошо сплавиться с основным металлом до того момента, когда начнется поступательное движение электрода в направлении сварки. При этом рекомендуется выполнять небольшие перемещения электродом вдоль оси шва. Однако большинство сварщиков предпочитают перемещать электрод вдоль оси шва без каких-либо продольных колебаний, определяя скорость сварки по формированию валика.
При наплавке валиков на обратной полярности некоторые электроды имеют склонность к образованию подрезов. Для предотвращения проявления этой тенденции не следует перемещать сварочную дугу, располагающуюся за кратером, пока не будет наплавлено достаточное количество металла, чтобы сварной шов получил требуемый размер и подрез был заполнен наплавленным металлом.
Поперечные колебания электрода по определенной траектории, совершаемые с постоянной частотой и амплитудой и совмещенные с перемещением вдоль шва, позволяют получить сварной шов требуемой ширины. Поперечные колебательные движения конца электрода определяются формой разделки, размерами и положением шва, свойствами свариваемого материала, навыком сварщика. Широкие швы (1,5-5)d3 получают с помощью поперечных колебаний, изображенных на рис. 3.
Рис. 3. Основные способы поперечных движений торца электрода
Для выполнения уширенного валика необходимо установить электрод в положение, показанное на рис. 4. При этом следует иметь в виду, что поперечные колебания совершаются электрододержателем, положение электрода в любой точке шва строго параллельно его первоначальному положению. Угол наклона электрода в вертикальной и горизонтальной плоскости не должен изменяться при колебательных движениях по поверхности шва.
Рис. 4. Положение электрода при наплавке валиков с поперечными колебаниями
Колебания электрода должны производиться с амплитудой, не превышающей три диаметра используемого электрода. Во время процесса формирования валика расплавленный слой должен поддерживаться в расплавленном состоянии. Если перемещать электрод слишком далеко и задерживать его возвращение, то возможны охлаждение и кристаллизация металла сварочной ванны. Это приводит к появлению в металле сварного шва шлаковых включений и ухудшает его внешний вид.
При сварке необходимо внимательно наблюдать за сварочной ванной, следить за ее шириной и глубиной проплавления, при этом не перемещать электрод слишком быстро. В конце каждого перемещения на мгновение останавливать электрод. Амплитуда поперечных колебаний должна быть немного меньше требуемой ширины наплавляемого валика.
При сварке на прямой полярности, как правило, не возникает проблем с подрезами. При сварке на обратной полярности могут возникнуть проблемы с появлением подрезов. Проблему подрезов можно преодолеть путем более длительной выдержки сварочной дуги в крайних точках поперечных перемещений, а также путем выполнения данных перемещений с амплитудой, не превышающей требуемую для получения нужной ширины наплавленного валика.
Выпуклость сварного шва будет меньше, чем при сварке на прямой полярности, проплавление будет более глубоким. Шлака будет несколько меньше, он будет менее текучим и будет закристаллизовываться немного быстрее, чем при сварке на прямой полярности.
На вертикальной поверхности узкие горизонтальные валики наплавляются, как правило, на обратной полярности, при этом сварочный ток не должен быть слишком большим.
Сварка должна производиться на короткой дуге. При сварке следует уделять внимание тому, чтобы металл сварочной ванны не вытекал вниз или не образовывал наплыв на нижней кромке. Для этого необходимо совершать возвратно-поступательные движения электродом в направлении оси сварного шва. Каждый новый валик должен перекрывать ранее наплавленный соседний с ним валик не менее чем на 45-55%. Для предотвращения образования подрезов необходимо производить колебания электрода в пределах выпуклости сварного валика.В большинстве случаев выполнение сварки в вертикальном положении производится снизу вверх, особенно для ответственных стыков. Данная техника сварки широко используется при строительстве трубопроводов высокого давления, в кораблестроении, при сооружении сосудов высокого давления и при строительных работах.
Наплавка узких валиков на поверхность, находящуюся в вертикальном положении, при сварке снизу вверх производится на обратной полярности сварочного тока, при этом сварочный ток не должен иметь слишком высокое значение. Положение электрода должно соответствовать изображенному на рис. 5. Необходимо использовать возвратно-поступательные перемещения электрода. Наплавка валиков должна производиться при короткой дуге, в верхней части траектории колебаний электрода, дугу следует растягивать, но нельзя допускать ее обрыва в данной области.
Рис. 5. Положение электрода при наплавке узких валиков без поперечных колебаний электрода в вертикальном положении снизу вверх
Подобный тип перемещений электрода позволяет наплавленному металлу кристаллизоваться, образуя ступеньку, на которую наплавляется следующая порция электродного металла. Некоторые сварщики предпочитают поддерживать постоянную сварочную ванну, которую они медленно выводят снизу вверх, применяя при этом небольшие колебательные движения электродом. Данный способ ведения процесса сварки приводит к наплавке валика с большой выпуклостью, а также к появлению вероятности трещин металла сварного шва.
Методика выполнения сварки с продольными колебаниями электрода позволяет получить более плоский с невысокой выпуклостью сварной шов, а также уменьшает опасность возникновения шлаковых включений.
Сварка в вертикальном положении сверху вниз достаточно редко встречается в промышленности, особенно при обычных работах. Область применения данного способа ведения сварочного процесса обычно ограничивается сварочными работами при строительстве магистральных трубопроводов и при сварке тонколистового проката. При наплавке на плоскую поверхность данный способ ведения сварки приводит к получению не очень глубокого проплавления, существует также опасность появления шлаковых включений.
Наплавка узких валиков в вертикальном положении сверху вниз производится на обратной полярности, при этом следует обратить особое внимание на установку сварочного тока. Положение электрода должно соответствовать изображенному на рис. 6.
Рис. 6. Положение электрода при наплавке узких валиков без поперечных колебаний электрода в вертикальном положении сверху вниз.
В процессе сварки необходимо поддерживать очень короткую дугу, с тем, чтобы шлак не затекал в головную часть сварочной ванны. Поперечные колебания электрода, как правило, не применяются, поэтому скорость перемещения достаточно велика. Этим и объясняется малая ширина наплавленных таким образом валиков, а также их малая выпуклость. Подрезы почти не встречаются.
Сварка с поперечными колебаниями электрода в вертикальном положении очень часто применяется при сооружении трубопроводов высокого давления, сосудов высокого давления, при сварке судовых конструкций, а также при изготовлении металлоконструкций. Данная техника сварки очень часто применяется для сварки многопроходных швов в разделку, а также угловых швов, находящихся вертикальном положении.
Наплавку валиков с поперечными колебаниями электрода в вертикальном положении, как правило, выполняют снизу вверх на обратной полярности сварочного тока. Сварка на прямой полярности в данном положении используется крайне редко. Еще реже производится сварка в положении сверху вниз.
При наплавке валиков с поперечными колебаниями электрода в вертикальном положении сварочный ток не должен быть слишком велик, однако он должен быть достаточным для хорошего проплавления. Положение электрода должно хотя бы приблизительно соответствовать изображенному на рис. 7.
В нижней части соединения наплавляется полка шириной не более 12 мм, при этом смешение электрода от оси сварного шва не должно превышать 3 мм. Перемещение электрода должно производиться по траектории (рис. 7б). Для предотвращения появления подрезов необходимо делать кратковременные остановки электрода во время выхода его на боковые кромки сварного шва.
Рис. 7. Положение электрода при наплавке валиков в вертикальном положении снизу вверх с поперечными колебаниями электрода (а) и траектория движения электрода (б).
Сварку можно также производит путем поддержания постоянного перемещения сварочной ванны, при этом нужно быть очень осторожным, чтобы не допустить вытекания расплавленного металла сварочной ванны. При соблюдении этого условия перемещение электрода вверх может производиться по любой из сторон сварного соединения, при этом необходимо производить <растяжение> сварочной дуги, но не допускать ее обрыва. Нельзя держать сварочную дугу слишком долго вне кратера — это может привести к охлаждению кратера и вызовет избыточное разбрызгивание металла перед швом.
При наплавке валиков на прямой полярности, сварочный ток должен быть несколько выше, чем при сварке на обратной полярности. Поскольку при сварке на прямой полярности выше производительность наплавки, а также больше количество шлака, скорость перемещения электрода должна быть выше. Подрезы не составляют сколь-нибудь значительной проблемы, поэтому отпадает необходимость задержки электрода на боковых поверхностях свариваемых кромок.
Наплавка валиков в вертикальном положении с поперечными колебаниями электрода в вертикальном положении сверху вниз производится на обратной полярности, при этом следует обратить особое внимание на установку сварочного тока. Положение электрода должно соответствовать изображенному на рис. 8. В процессе сварки необходимо поддерживать очень короткую дугу, с тем, чтобы шлак не затекал в головную часть сварочной ванны. Для предотвращения появления подрезов необходимо делать кратковременные остановки электрода во время выхода его на боковые кромки сварного шва.
Рис. 8. Положение электрода при наплавке валиков в вертикальном положении сверху вниз с поперечными колебаниями электрода (а) и траектория движения электрода (б)
Несмотря на то, что в настоящее время в промышленности взят курс на полное исключение сварки в потолочном положении за счет соответствующего позиционирования, на сегодняшний день каждый сварщик должен уметь вести сварочные работы в этом пространственном положении. Сварка в потолочном положении распространена при строительстве трубопроводов, в судостроении и при строительно-монтажных работах.
Рис. 9. Положение электрода при наплавке узких валиков в потолочном положении
Наплавка узких валиков в потолочном положении может производиться как на обратной, так и на прямой полярности. Величина сварочного тока при обратной полярности такая же, как при сварке в вертикальном положении. При сварке на прямой полярности эта величина несколько выше. Положение электрода должно соответствовать изображенному на рис. 9. Сварщик должен находиться в таком положении, чтобы иметь возможность наблюдать за наплавкой металла и за сварочной дугой. Особенно это важно при сварке труб, однако часто бывает так, что направление сварки должно быть направлено на сварщика.
Во время процесса сварки на обратной полярности необходимо поддерживать короткую дугу, сварочная ванна не должна быть слишком сильно перегрета. При сварке на прямой полярности длина дуги должна быть несколько длиннее. Небольшие колебания электрода вперед-назад относительно направления сварки служат для предварительного подогрева сварного шва, кроме того, они способствуют предотвращению подтекания расплавленного шлака в головную часть сварочной ванны. Некоторые сварщики при сварке на прямой полярности предпочитают перемещать электрод во время сварки очень маленькими участками, при этом необходимо обращать внимание на опасность получения сварного шва с большой выпуклостью, а также на образование толстой корки шлака. При сварке на прямой полярности опасность появления подрезов практически исключена.
Во многих случаях при выполнении сварных соединений в потолочном положении, возникает необходимость в наплавке валиков с поперечными колебаниями электрода. Это значительно сложнее, чем наплавка узких валиков.
Наплавка валиков с поперечными колебаниями электрода в потолочном положении, производится на обратной полярности. Величина сварочного тока не должна быть слишком большой. Положение электрода должно соответствовать изображенному на рис. 10а. Большое значение имеет поддержание короткой дуги, а также стабильности дугового промежутка по всей ширине наплавляемого валика.
Наплавку можно производит путем перемещения всей сварочной ванны, однако при этом необходимо быть очень осторожным, чтобы не допустить приобретения расплавленным металлом сварочной ванны слишком высокой текучести, что, в конечном счете, приведет к вытеканию сварочной ванны. Если данное препятствие будет устранено, то электрод можно перемещать вперед вдоль любой из свариваемых кромок (рис. 106). При этом допускается удлинение дуги, без ее обрыва.
Нельзя допускать, чтобы сварочная дуга находилась в кратере больше времени, чем необходимо для его полной заварки. Электрод должен быстро перемещаться поперек лицевой стороны сварного шва, с тем, чтобы не допустить избыточного перегрева металла, наплавленного в средней части сварного шва.
При сварке в потолочном положении могут возникнуть проблемы, связанные с подрезами. Они решаются с помощью задержек электрода на боковых кромках соединения. Рекомендуется не превышать ширины сварного шва свыше 20 мм.
Рис. 10. Положение электрода при наплавке валиков с поперечными колебаниями электрода в потолочном положении (а) и траектория перемещения электрода (б)
Сварка торцевого соединения в нижнем положении
Торцевые соединения широко применяются в конструкциях сосудов, не подвергаемых воздействию высокого давления. Торцевые соединения — это очень экономичные соединения, но они не выдерживают значительных растягивающих или изгибающих нагрузок. Для выполнения данного соединения требуется мало электродов, поскольку доля наплавленного металла в металле сварного шва мала. Выполнение сварки торцевого соединения не представляет каких-либо затруднений и может производиться в широком диапазоне сварочных режимов, как на прямой полярности, так и на обратной.
Во время сварки для полного охвата всей поверхности соединения рекомендуется производить небольшие поперечные колебания электрода. Однако следует помнить об опасности увлечения такими колебаниями. При излишне широких колебаниях электрода металл начнет свешиваться с краев соединения. Следует быть внимательным при расплавлении обеих кромок и при обеспечении хорошего проплавления.
Сварка стыкового соединения без скоса кромок в нижнем положении
Данный тип сварного соединения широко используется в промышленности для конструкций обычного назначения. При двухсторонней сварке металла, толщина которого не превышает 6 мм, данное соединение будет весьма прочным. Однако, как правило, такие соединения свариваются только с одной стороны. В этом случае прочность будет определяться глубиной проплавления, которая, в свою очередь, зависит от диаметра применяемых электродов, величины сварочного тока, величины зазора между деталями, а также от толщины свариваемых деталей. При односторонней сварке получение полного проплавления без зазора между свариваемыми кромками для металла толщиной свыше 5 мм весьма проблематично.
Сварка стыкового соединения без скоса кромок для обеспечения повышенного тепловложения, производится на обратной полярности. При сварке необходимо обеспечивать возвратно-поступательные перемещения электрода вдоль оси шва. Это будет приводить к предварительному подогреву металла перед сварным швом, сведет к минимуму риск получения прожога и обеспечит вытеснение расплавленного шлака на поверхность сварочной ванны, что исключит вероятность образования неметаллических шлаковых включений в металле сварного шва.
В процессе сварки особенно важно поддержание постоянства скорости и равномерности перемещения электрода вдоль оси шва, а также величины зазора между электродом и изделием (длины дуги). При слишком высокой скорости перемещения электрода шов получается узкий, образуются подрезы. При слишком малой скорости сварки сварочная ванна разогревается до температуры, при которой возможен прожог.
Слишком длинная дуга приводит к ухудшению внешнего вида шва, к ухудшению проплавления, к избыточному разбрызгиванию и низким показателям механических свойств металла сварного шва.
Сварка в нижнем положении таврового соединения (сварка в «лодочку») однопроходным угловым швом
При образовании углового шва во избежание непровара свариваемые поверхности наклоняют к горизонтальной плоскости под углом 45° — сварка «в лодочку» (рис. 11а), а при наклоне под углом 30 или 60° — в несимметричную «одочку» (рис. 116). Сварка производится на повышенных значениях сварочного тока, как на прямой, так и на обратной полярности тока. Сварка на обратной полярности производится короткой дугой, при этом возможно появление подрезов. Положение электрода при сварке должно соответствовать изображенному на рис. 11в
Рис. 11. Положение электрода при сварке «в лодочку»: a — сварка в симметричную «лодочку»; б — сварка в несимметричную ; в — пространственное положение электрода
При начале процесса сварки электрод должен быть выведен на кромку свариваемой пластины. После подогрева кромки пластины растянутой дугой начинается наложение сварного шва требуемой ширины и глубины проплавления. При этом производятся небольшие возвратно-поступательные перемещения электродом в направлении оси сварного шва. Это обеспечивает предварительный подогрев корневой части сварного шва и предотвращает подтекание расплавленного шлака перед головной частью сварочной ванны.
Электрод должен направляться непосредственно в корень сварного шва, нельзя допускать, чтобы сварочная дуга вышла на поверхность пластины за пределами области формирования сварного шва. Не допускается наплавка слишком большого количества металла за один проход.
Сварка в нижнем положении таврового соединения (сварка в «лодочку») многопроходным угловым швом.
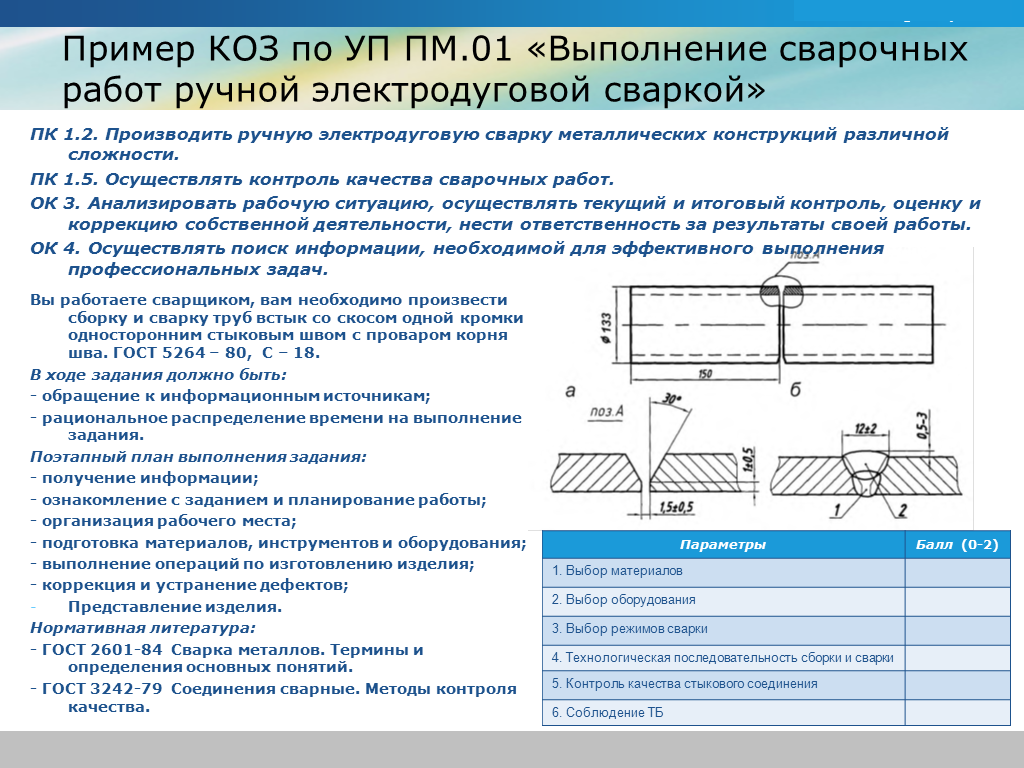
Очень часто при сварке таврового соединения в нижней) положении необходимо производить многопроходную сварку. Однопроходные угловые швы должны иметь катеты, которые превышают диаметр используемого электрода не более чем на 1,5-3,0 мм. При многопроходной сварке угловых швов число слоев определяют, исходя из диаметра электрода, при этом толщина каждого слоя не должна превышать (0,8-1,2)dэ.
Поскольку тавровое соединение в нижнем положении образует кромки, подобно стыковому соединению со скосом кромок, сварка может выполняться с использованием техники сварки с поперечными колебаниями электрода, при этом ширина шва не должна превышать (1,5-5)dэ. Если слой сварного шва превышает допустимую ширину шва, то наплавка каждого слоя производится необходимым количеством валиков.
При сварке данного соединения первый проход выполняется электродом толщиной 4-6 мм без поперечных колебаний. Последующие проходы выполняются электродами меньшего диаметра. При сварке этих проходов необходимо применять поперечные колебания электрода, при этом амплитуда колебаний электрода не должна превышать допустимой ширины шва.
При сварке на обратной полярности поддерживается несколько меньшая длина дуги, чем на прямой полярности. При этом необходимо тщательно контролировать процесс сварки, с тем, чтобы избежать появления возможных подрезов. Для этого можно применять задержки электрода в крайних точках амплитуды поперечных колебаний электрода при одновременном тщательном контроле ширины сварного шва и амплитуды поперечных колебаний электрода.
Перед наплавкой каждого слоя или валика необходимо тщательно очищать от шлака поверхность сварного шва, в противном случае неизбежно появление шлаковых включений. В начале и при возобновлении сварки необходимо тщательно заваривать кратеры сварных валиков.
Сварка углового соединения с наружным углом в нижнем положении
Угловые соединения с наружными угловыми швами встречаются намного реже, чем стыковые, нахлесточные и тавровые соединения. Это соединение является в высшей степени технологичным, поскольку его очень просто подготовить к сварке, а параметры режима сварки напоминают применяемые при сварке стыковых соединений со скосом кромок.
Для обеспечения максимальной прочности в сварном соединении необходимо получить проплавление с обратной стороны. Добавление внутреннего углового шва к наружному значительно повышает прочность всего углового соединения. Как уже отмечалось, стоимость подготовки подобного соединения весьма невелика, однако при сварке подобных соединений из металла большой толщины значительную величину затрат составит стоимость электродов.
Сварку углового соединения с наружным углом в нижнем положении выполняют на обратной полярности. При сварке данного соединения положение электрода должно соответствовать изображенному на рис. 12. При первом проходе используется техника сварки, применяемая при наложении узкого шва, без поперечных колебаний. Значение сварочного тока не должно быть слишком большим. Сварной шов при первом проходе должен обеспечить полное проплавление обратной стороны соединения и хорошее сплавление с обеими пластинами. Большое значение для достижения этой цели имеет поддержание короткой дуги.
Рис. 12. Положение электрода при сварке углового соединения с наружным углом в нижнем положении
При выполнении второго, третьего и последующих проходов сварочный ток следует установить на повышенный режим. При выполнении данных проходов используется техника поперечных колебаний электрода. Третий проход должен производиться с более широкой амплитудой колебаний, чем второй. Техника выполнения второго и последующих проходов аналогична выполнению данных проходов при сварке в «лодочку» многопроходным угловым швом.
Во время сварки необходимо следить за ограничением ширины поперечных колебаний электрода. Для устранения подрезов рекомендуется производить кратковременную остановку электрода в крайних точках траектории поперечных колебаний. Удостоверьтесь в том, что достигается хорошее сплавление с ранее наложенными слоями и с обеими поверхностями пластины. Последний проход не должен иметь слишком большую высоту. После каждого прохода необходимо тщательно очистить наплавленный металл от шлаковой корки.
Сварка стыкового соединения со скосом кромок на подкладке в нижнем положении
Данный тип сварного соединения достаточно часто применяется при сварке трубопроводов, сосудов высокого давления и корабельных конструкций.
Сварка данного соединения производится на обратной полярности. Для первого прохода устанавливается невысокое значение сварочного тока. Положение электрода должно соответствовать изображенному на рис. 13. Сварка производится узким валиком без поперечных колебаний электрода. Во время сварки необходимо следить за тем, чтобы обеспечить хорошее сплавление с подкладкой и поверхностями разделки в корневой части соединения. Поверхность шва должна быть максимально плоской.
Рис. 13. Положение электрода при сварке стыкового соединения со скосом кромок на подкладке в нижнем положении
Второй, третий и последующие проходы могут производиться при повышенных значениях сварочного тока. Перемещение вдоль оси шва не должно быть слишком быстрым, иначе поверхность шва будет неровной, с крупными чешуйками, могут появиться поры. Поперечные перемещения электрода должны ограничиваться требуемой шириной шва. Это обеспечит исключение появления подрезов. Во время сварки важно следить за длиной дуги, тщательно удалять шлак с наложенных слоев, следить за тем, чтобы наложенный сварной шов имел сплавление с предыдущими слоями и со свариваемыми кромками. При наложении последнего слоя используйте кромки разделки в качестве показателя при определении требуемой ширины шва.
Сварка стыкового соединения со скосом кромок в нижнем положении
Данный вид соединения часто встречается при сварке трубопроводов, а также при сварке ответственных соединений.
Сварка данного соединения производится на обратной полярности. Положение электрода должно соответствовать изображенному на рис. 14.
Рис. 14. Положение электрода при сварке стыкового соединения со скосом кромок в нижнем положении
На рис. 15а показан порядок наложения слоев/валиков при сварке стыкового соединения со скосом кромок в нижнем положении. Первый проход предназначен для сварки корня шва и выполняется обычно электродами диаметром 3 мм, при этом сварочный ток не должен быть слишком велик. Сварка производится на короткой дуге с возвратно-поступательными движениями относительно линии сварного шва, при этом необходимо следить, чтобы сам электрод все время оставался в зазоре корневой области сварного соединения. Во время сварки нельзя допускать прерывания дуги при перемещении электрода вперед и нужно следить за тем, чтобы капли металла не падали перед швом, это может помешать проведению процесса сварки, его продвижению вперед. На обратной стороне стыка должен образовываться небольшой валик. Лицевая поверхность первого прохода должна иметь минимальную выпуклость.
Рис. 15. Сварка стыкового соединения со скосом кромок в нижнем положении: a — порядок наложения слоев; б — траектория движения электрода при выполнении последнего прохода; в — сварное соединение
Второй и последующие проходы производятся при повышенных значениях сварочного тока и электродами большего диаметра. Наплавка производится с поперечными колебаниями электрода, при этом важно обеспечить постоянство и равномерность колебаний и перемещения электрода вдоль оси шва, в противном случае полученный сварной шов будет не однороден по качеству и внешнему виду. Во время сварки необходимо следить за тем, чтобы избежать появления подрезов (рис. 156). Необходимо получить сплавление с ранее наплавленными слоями, а также с боковыми кромками разделки свариваемого изделия. Лицевая сторона второго и последующих слоев должна иметь плоскую поверхность. Необходимо тщательно очищать каждый слой от шлака по всей его длине.
Заключительный проход выполняется тем же типом электрода, что и предыдущие. Техника выполнения такая же, и при выполнении второго и последующих проходов, за исключением того, что при заключительном проходе амплитуда поперечных колебаний электрода будет больше. Для контроля за шириной облицовочного шва необходимо использовать скошенные кромки стыкового соединения. Поверхность облицовочного шва должна быть слегка выпуклой.
Сварка нахлесточного соединения в нижнем положении
Данный тип соединения широко используется в промышленности, в частности в резервуарах, строительных и судовых конструкциях. Нахлесточное соединение очень экономично, оно не требует каких-либо значительных затрат на подготовку и сборку. Максимальная прочность нахлесточного соединения достигается при его двухсторонней сварке угловым швом.
Сварка данного соединения производится как на прямой, так и на обратной полярности, при этом сварочный ток не должен быть слишком большим. Положение электрода должно соответствовать изображенному на рис. 16.
Рис. 16. Сварка нахлесточного соединения в нижнем положении: a — подготовка соединения к сварке; б — положение электрода при сварке однопроходным швом равных толщин; в — положение электрода при втором и третьем проходе при выполнении многопроходного шва; г — положение электрода при сварке разных толщин
Для сварки нахлесточного соединения в нижнем положении на прямой полярности требуется поддержание очень короткой дуги, а на обратной полярности — еще более короткой. Дуга должна быть сориентирована в направлении корня соединения и горизонтальной поверхности пластины. Во время сварки необходимо совершать, относительно оси сварного, шва небольшие возвратно-поступательные колебания электрода. Это способствует предварительному подогреву соединения перед движущейся сварочной дугой, обеспечивает создание полноразмерной выпуклости и покрывает шлаковой коркой хвостовую часть сварочной ванны.
Абсолютно необходимым для получения качественного соединения является полное проплавление в корне шва и хорошее сплавление с обеими поверхностями двух пластин. При сварке на прямой полярности верхняя кромка верхней пластины имеет тенденцию к прожогу, поэтому при сварке следует постоянно опасаться как недозаполнения наплавленного валика, так и того, что сварочная дуга недостаточно коротка. Подрезы появляются очень редко.
При сварке на обратной полярности следует обратить внимание на поддержание более короткой дуги, а также на устранение возможного подреза, как на плоской поверхности пластины, так и вдоль верхней кромки верхней пластины. Для уменьшения вероятности появления подрезов, перемещение дуги должно быть ограничено размерами сварного шва.
Сварка нахлесточного соединения в горизонтальном положении
Сварка нахлесточного соединения в горизонтальном положении однопроходным угловым швом на прямой полярности часто применяется в конструкциях резервуаров и строительных конструкциях.
При сварке данного соединения сварочный ток не должен быть слишком большим. Электрод необходимо направлять в корень шва. Положение электрода во время сварки должно соответствовать изображенному на рис. 17. Сварку лучше всего производить с небольшими возвратно-поступательными перемещениями электрода в направлении оси сварного шва, можно также применять незначительные поперечные колебания электрода. Сварочная ванна не должна быть слишком перегрета, ибо это приводит к появлению трещин в металле сварного шва.
Рис. 17. Положение электрода при сварке нахлесточного соединения в горизонтальном положении
При сварке следует обращать особое внимание на перемещения электрода, с тем, чтобы не допустить появления прожогов кромки пластины, а также на то, чтобы сварочная дуга не контактировала с поверхностью вертикальной пластины вне пределов сварного шва, в противном случае неизбежно появление подрезов.
Сварка таврового соединения в нижнем положении
Большую долю швов, выполняемых на практике сварщиком, составляют угловые швы, выполняемые в нижнем положении. Технология сварки может включать как однопроходную, так и многопроходную сварку всеми типами электродов. Несмотря на то, что электроды, предназначенные для сварки на обратной полярности, не являются лучшим типом электродов для выполнения однопроходных угловых швов, использование этих электродов в подобных целях является достаточно распространенной практикой.
При сварке таврового соединения в нижнем положении на прямой полярности сварочный ток должен быть достаточным для получения обширной сварочной ванны. При сварке на обратной полярности сварочный ток должен быть несколько меньше. Положение электрода при сварке на прямой полярности должно соответствовать изображенному на рис. 18а, на обратной полярности — рис. 18б.
Рис. 18. Положение электрода при сварке таврового соединения в нижнем положении: a — на прямой полярности; б — на обратной полярности
Электрод должен быть направлен в корень сварного соединения. При сварке на обратной полярности длина дуги должна быть меньше. Перемещение электрода должно производиться равномерно на всем протяжении стыка, не теряя сварочной ванны.
Однако некоторые сварщики предпочитают использовать при этом небольшие возвратно-поступательные перемещения электрода в направлении оси шва. Это может оказать положительное влияние в виде предварительного подогрева свариваемых кромок и корневой части соединения, находящихся перед движущимся электродом, улучшит формирование наплавленного металла на вертикальной плоскости пластины, а также будет способствовать предотвращению подтекания расплавленного шлака в головную часть сварочной ванны. При сварке на прямой полярности подрезы никогда не являются проблемой. Сварка на обратной полярности требует обеспечения повышенных мер по исключению подрезов.
Сварка таврового соединения в нижнем положении многопроходным швом
Крупные угловые швы очень часто выполняются путем многократного наложения узких валиков без поперечных колебаний электрода. В большинстве случаев облицовочный слой или последний валик выполняются без поперечных колебаний электрода, в некоторых случаях требуется, чтобы последний проход выполнялся с поперечными колебаниями. В частности, таковы требования при сварке трубопроводов и сосудов высокого давления. Сварка может выполняться как на прямой, так и на обратной полярности сварочного тока.
При выполнении данного соединения сварочный ток устанавливается таким же, как и при сварке узким однопроходным швом. Положение электрода будет изменяться в зависимости от последовательности наложения слоев (рис. 19а). Перемещение электрода аналогично перемещению при сварке однопроходным швом. Расположение или раскладка валиков по сторонам должны производиться таким образом, чтобы облицовочный слой точно соответствовал заданному размеру катета углового шва. Порядок наложения слоев показан на рис. 19б.
Рис. 19. Положение электрода при сварке таврового соединения многопроходным швом в нижнем положении (а) и порядок наложения слоев (б)
Техника выполнения облицовочного слоя достаточно сложна. Сварочный ток не должен быть слишком мал. Положение электрода должно соответствовать изображенному на рис. 20а. Чешуйки укладываются в диагональной плоскости. Наложение капель металла производится только при движении электрода вниз. Перемещение электрода вверх должно производиться быстро, на максимально растянутой дуге, но без обрыва дуги.
Рис. 20. Положение электрода при выполнении облицовочного слоя (а) и траектория колебательных движений электрода (б)
Указателями ширины перемещения электрода при сварке облицовочного слоя могут служить две параллельные кромки ранее выполненных сварных валиков. Для предотвращения появления подрезов необходимо проводить задержки электрода на верхней и нижней кромках сварного шва. Необходимо помнить, что при многопроходной сварке требуется тщательная очистка от шлаковой корки каждого наложенного слоя.
При сварке на обратной полярности могут возникнуть значительные затруднения, связанные с появлением подрезов. Избавиться от этих проблем можно всеми ранее описанными способами.
Сварка таврового соединения в нижнем положении многопроходным швом с применением поперечных колебаний электрода
На практике довольно часто встречаются случаи, когда необходимо производить сварку угловых швов большого сечения в нижнем положении. Обычно для этого используют многопроходную сварку с применением техники поперечных колебаний электрода. Наиболее часто такие швы встречаются при судостроительных и монтажных работах.
Сварка данного типа соединения производится на обратной полярности. Сварочный ток устанавливается большим. Положение электрода должно соответствовать изображенному на рис. 21. Первый проход выполняется так же, как и в случае обычной однопроходной сварки угловых швов. Поверхность первого валика должна быть максимально плоской.
Рис. 21. Положение электрода при сварке таврового соединения многопроходным швом в нижнем положении с применением поперечных колебаний электрода
Второй шов накладывается с поперечными колебаниями электрода поверх первого. Электрод должен направляться на вертикальную пластину, с тем, чтобы обеспечить перенос металла с электрода на эту поверхность. Поперечные колебания электрода не должны выходить за пределы требуемой ширины выполняемого шва. В противном случае возможно появление подрезов. Необходимо обеспечить хорошее сплавление накладываемых швов с поверхностью ранее наплавленных слоев и с поверхностью свариваемой пластины.
Сварка стыкового соединения со скосом кромок на подкладке в горизонтальном положении
Данное соединение, а также пространственное положение, в котором оно находится, очень часто встречается при сварке труб, резервуаров, а также при судостроительных работах.
Сварка производится на обратной полярности как узкими валиками без поперечных колебаний, так и с поперечными колебаниями электрода. Первый проход выполняется на повышенных значениях сварочного тока без поперечных колебаний электрода. Положение электрода должно соответствовать изображенному на рис. 22. При сварке необходимо обеспечить гарантированное сплавление с подкладкой, а также с кромками корневой части соединения.
Рис. 22. Положение электрода при сварке стыкового соединения со скосом кромок на подкладке в горизонтальном положении
Второй и все последующие проходы могут выполняться с еще большими значениями сварочного тока. Положение электрода при сварке узкими валиками без поперечных колебаний электрода должно соответствовать изображенному на рис. 22. Очень важно, чтобы все швы имели хорошее сплавление с поверхностью ранее наложенных слоев, а также с поверхностью кромок разделки. Необходимо следить за предотвращением появления подрезов.
Сварка стыкового соединения со скосом кромок в горизонтальном положении
Данное соединение, а также пространственное положение, в котором оно находится, очень часто встречается при сварке труб, а также ответственных стыковых соединений. При выполнении некоторых работ иногда предъявляются требования к тому, чтобы данные швы выполнялись с поперечными колебаниями электрода, однако в большинстве случаев применяется сварка узкими валиками без поперечных колебаний электрода.
Сварка производится на обратной полярности. Сварочный ток при первом проходе не должен быть слишком велик. Положение электрода при сварке узкими валиками без поперечных колебаний должно соответствовать рис. 23, а при сварке с поперечными колебаниями — рис. 24а.
Рис. 23. Положение электрода при сварке стыкового соединения со скосом кромок в горизонтальном положении: узкими валиками без поперечных колебаний электрода.
При сварке необходимо поддерживать короткий дуговой промежуток, заставляя электродный металл наплавляться непосредственно в зазоре корневой части соединения. При сварке можно использовать возвратно-поступательные перемещения электрода. При перемещениях вперед нельзя допускать, чтобы сварочная дуга обрывалась.
Необходимо во время таких перемещений обеспечить предварительный подогрев металла перед наплавляемым швом. Одновременно следует следить за тем, чтобы расплавленный металл сварочной ванны достаточно быстро застывал и не стекал на нижнюю пластину. На обратной стороне соединения должно быть полное проплавление.
Для второго и последующих проходов сварочный ток может быть значительно увеличен. Можно использовать сварку узкими валиками, без поперечных колебаний. можно также использовать сварку с поперечными колебаниями электрода (рис. 24б). Важно обеспечить гарантированное сплавление всех проходов с поверхностью всех предшествующих проходов, а также с поверхностями свариваемых пластин. Во время сварки необходимо следить за появлением подрезов.
Рис. 24. Положение электрода при сварке стыкового соединения со скосом кромок в горизонтальном положении: a — сварка с поперечными колебаниями электрода; б — пример поперечных движений торца электрода
Сварка стыкового соединения со скосом одной кромки в горизонтальном положении
Наиболее часто, при выполнении стыковых соединений в горизонтальном положении скашивают кромку только у верхнего листа. Дугу возбуждают на горизонтальной кромке нижнего листа, перемещают затем на скошенную кромку верхнего листа. Техника сварки ничем не отличается от описанной выше, за исключением порядка наложения слоев.
Сварка нахлесточного соединения в вертикальном положении снизу вверх. При выполнении ответственных сварочных работ с использованием нахлесточных соединений, находящихся в вертикальном положении, как правило, сварку производят снизу вверх. Такая сварка имеет место при выполнении сварочных работ в судостроении, при изготовлении сосудов высокого давления, а также при изготовлении металлоконструкций.
При сварке небольших толщин, а также для выполнения первых проходов в многопроходных сварных швах, выполняемых при сварке нахлесточных соединений, применяются однопроходные угловые швы. При выполнении данных швов необходимо установить не очень большое значение сварочного тока. Положение электрода должно соответствовать изображенному на рис. 25.
Рис. 25. Положение электрода при сварке нахлесточного соединения в вертикальном положении снизу вверх
На нижней части соединения образуется полка из наплавленного металла, имеющая размеры, соответствующие размерам сварного шва. Следует применять возвратно-поступательные перемещения электрода. При переносе электродного металла следует поддерживать короткую дугу, при переходе вверх дугу следует растянуть, не допуская при этом ее обрыва. Когда электрод находится над сварочной ванной, можно производить небольшие поперечные перемещения электрода. Это способствует лучшему формированию сварного шва. Во время сварки необходимо следить за тем, чтобы перемещения электрода всегда сохранялись в пределах ширины шва таким образом, чтобы кромка верхней пластины не прожигалась, а на плоской поверхности пластины не появлялись подрезы.
Для выполнения сварных швов нахлесточных соединений большой толщины применяется многопроходная или однопроходная сварка с поперечными перемещениями электрода. При многопроходной сварке первый проход выполняется узким валиком без поперечных перемещений электрода. При выполнении второго прохода сварочный ток должен быть достаточным для обеспечения гарантированного проплавления в корневой части соединения и сплавления с кромками. Положение электрода и траектория движения электрода должны соответствовать изображенному на рис. 26а. При этом, сохраняя электрод над поверхностью сварочной ванны, нужно перемещать ее вверх, одновременно сдвигая сварочную ванну в стороны, поочередно то влево, то вправо.
Рис. 26. Положение электрода при сварке нахлесточного соединения в вертикальном положении снизу вверх многопроходным угловым швом (а) и однопроходным угловым швом с поперечным перемещением электрода (б)
Равномерные перемещения сварочной ванны, выполняемые в процессе сварки, позволяют получить ровную, с малой выпуклостью поверхность сварного шва. Кратковременные остановки в крайних точках поперечных колебаний предотвратят появление подрезов, но нужно быть крайне осторожным, чтобы при этом кромка верхней пластины не прожигалась.
Сварку нахлесточного соединения можно производить также однопроходным угловым швом с поперечными колебаниями электрода. Положение электрода и траектория движения электрода должны соответствовать изображенному на рис. 26б. Техника сварки аналогична выполнению второго прохода при многопроходной сварке. Отличие заключается в том, что электрод необходимо располагать под большим углом к нижней пластине и задержки перемещения выполнять только на нижней пластине.
Сварка таврового соединения в вертикальном положении однопроходным угловым швом
Сварка данного соединения часто встречается в производственной практике. Сварка вертикальных стыков чаще всего производится снизу вверх, хотя встречаются и случаи, когда необходимо выполнять сварку сверху вниз. Выбор количества проходов определяется назначением данного соединения, а также толщиной свариваемых пластин.
При выполнении сварки таврового соединения в вертикальном положении однопроходным угловым швом без поперечных перемещений электрода сварочный ток должен быть достаточно большим, с тем, чтобы обеспечить хорошее проплавление в корневой части соединения, а также с поверхностями пластин. Положение электрода должно приблизительно соответствовать изображенному на рис. 27.
Рис. 27. Положение электрода при сварке таврового соединения в вертикальном положении однопроходным угловым швом
Сварка производится на обратной полярности с колебаниями электрода вверх-вниз. В момент переноса электродного металла необходимо поддерживать короткую дугу, при перемещении электрода вверх дугу следует растянуть, однако при этом не допускать обрыва дуги. Необходимо периодически производить отвод электрода от сварочной ванны, с тем, чтобы избежать перегрева свариваемого металла и последующего его растрескивания или вытекания сварочной ванны. Вместе с тем необходимо удерживать сварочную ванну на одном месте, вплоть до момента, пока не будет получено требуемое проплавление, сплавление со свариваемыми кромками и образование сварного шва требуемого контура без подрезов.
Сварку таврового соединения в вертикальном положении можно производить также однопроходным угловым швом с поперечными колебаниями электрода. Положение электрода и траектория движения электрода должны соответствовать изображенному на рис.выполняется без поперечных перемещений электрода или в некоторых случаях с небольшими поперечными колебаниями (рис. 29б).Положение электрода при втором проходе должно соответствовать изображенному на рис. 30. Сварочный ток должен быть достаточным для обеспечения гарантированного проплавления в корневой части соединения и сплавления с кромками.
Рис. 30. Положение электрода при сварке таврового соединения в вертикальном положении многопроходным
Во время сварки необходимо сохранять электрод над поверхностью сварочной ванны, перемещать сварочную ванну вверх, одновременно сдвигая ее в стороны, поочередно то влево, то вправо. Равномерные перемещения сварочной ванны, выполняемые в процессе сварки, позволяют получить ровную, с малой выпуклостью поверхность сварного шва, а кратковременные остановки электрода в крайних точках поперечных перемещений предотвратят появление подрезов. Во время сварки необходимо поддерживать короткую дугу, но избегать касания электрода с расплавленным металлом сварочной ванны.
При использовании электрода большого диаметра необходимо увеличить сварочный ток. Положение электрода при сварке третьего прохода аналогично второму проходу. При применении электрода большого диаметра и при увеличении сварочного тока желательно ускорять перемещение электрода вверх при достижении сварочной ванной крайней точки траектории поперечных колебаний. При этом необходимо обращать внимание на продолжение горения дуги во время всех этих перемещений. При перемещении дуги вверх ее необходимо растягивать. После достаточного охлаждения сварочной ванны электрод возвращается к кратеру, и производится наплавка дополнительного металла.
Во время сварки необходимо поддерживать постоянство ширины траектории поперечных колебаний, следить за тем, чтобы она не превышала ширину законченного шва.
Сварка стыкового соединения со скосом кромок на подкладке в вертикальном положении
Данный тип соединения довольно часто встречается при строительстве трубопроводов, сосудов высокого давления, а также в судовых конструкциях. Сварка производится на обратной полярности снизу вверх.
Первый проход. Сварочный ток должен быть большим. Положение электрода должно соответствовать изображенному на рис. 31. При сварке используется техника наплавки узких валиков, без поперечных колебаний, в вертикальном положении. Шов должен иметь хорошее сплавление с подкладкой и с поверхностями обеих кромок в своей корневой части.
При сварке необходимо следить за тем, чтобы лицевая поверхность шва была максимально плоской. Если в сварном соединении зазор в корне очень широк, то необходимо сделать два или три прохода, чтобы выполнить подварочный шов. В процессе сварки необходимо обращать внимание на то, чтобы все наложенные слои имели хорошее сплавление друг с другом.
Рис. 31. Положение электрода при сварке стыкового соединения со скосом кромок на подкладке в вертикальном положении
Второй проход. Сварочный ток не должен быть слишком велик. При выполнении шва используется техника сварки с поперечными колебаниями электрода. В качестве направляющих, по которым можно определять ширину этих поперечных колебаний, используются кромки ранее наплавленных валиков. При выполнении сварки необходимо следить за тем, чтобы поверхность сварного шва была плоской, избегать появления подрезов. Сварной шов не должен образовывать острые кромки, поскольку в таких кромках могут образовываться зашлаковки.
Третий проход. Величина сварочного тока должна быть такой, чтобы обеспечивалось как хорошее проплавление и сплавление, так и малая выпуклость сварного шва. Поперечные колебания электрода не должны выходить за пределы скошенных кромок разделки. Во избежание появления подрезов необходима задержка электрода в крайних точках траектории поперечных колебаний. Для предотвращения появления излишней выпуклости сварного шва скорость сварки должна быть достаточно большой.
Сварка стыкового соединения без скоса кромок в вертикальном положении
Сварка данного соединения производится снизу вверх на обратной полярности многопроходным швом. Техника сварки корневого прохода с большим зазором в стыковом соединении без скоса кромок достаточно сложна.
Первый проход. Сварочный ток должен быть не слишком большим, но вместе с тем он должен быть достаточным для гарантированного проплавления корневой части соединения и образования на обратной стороне стыка достаточной выпуклости. Положение электрода должно соответствовать изображенному на рис. 32. При сварке первого прохода используется техника сварки узкими валиками без поперечных колебаний электрода; Необходимо добиваться получения на обратной стороне корня шва небольшой выпуклости.
Рис. 32. Положение электрода при сварке стыкового соединения без скоса кромок в вертикальном положении
Второй проход. Значение сварочного тока и положение электрода практически не отличаются от аналогичных показателей при сварке первого прохода. Нельзя производить поперечные колебания со слишком большой амплитудой. Скорость перемещения электрода должна быть такой, чтобы не возникала избыточная выпуклость шва и не образовывались подрезы.
Сварка соединения с наружным угловым швом
Данные сварные соединения часто встречаются на практике. Сварка производится на обратной полярности снизу вверх с использованием техники поперечных колебаний электрода, кроме того, благодаря тому, что свариваемые кромки не скошены, в данном случае достаточнонеглубокое проплавление.
Первый проход. Сварочный ток не должен быть слишком велик. Положение электрода должно соответствовать изображенному на рис. 33. Используется техника выполнения корневого прохода с возвратно-поступательными перемещениями электрода.
Рис. 33. Положение электрода при сварке соединения с наружным угловым швом в вертикальном положении
Второй и третий проходы. Сварочный ток необходимо увеличить по сравнению с первым проходом. Во время сварки необходимо следить за обеспечением хорошего сплавления с ранее наплавленными слоями, а также со свариваемыми кромками основного металла, обращать внимание на возможность появления подрезов. Лицевая поверхность швов должна быть плоской.
Четвертый проход. Значение сварочного тока и положение электрода аналогичны использовавшимся при сварке предыдущих проходов. При сварке использовать технику поперечных колебаний электрода. Лицевая поверхность шва должна иметь небольшую выпуклость. В качестве границы шва использовать кромки пластин.
Рис. 34. Сварка стыкового соединения со скосом кромок в вертикальном положении (а) и траектория движения электрода (б)
Сварка стыкового соединения со скосом кромок
Данные сварные соединения очень часто встречаются при сварке труб и ответственных стыковых соединений. Сварка производится на обратной полярности снизу вверх многопроходным швом с поперечными колебаниями электрода.
Первый проход. Сварочный ток должен быть достаточно большим. Положение электрода должно соответствовать изображенному на рис. 34а. Используется техника сварки корневого шва, при которой применяются колебания электрода вверх-вниз. Допускается выполнять сварку с небольшими поперечными перемещениями электрода (рис. 34б).
Перемещения электрода вверх должны производиться на расстояние, не превышающее 50 мм. Необходимо следить, чтобы при этих перемещениях не происходил обрыв дуги. Необходимо обеспечить полное проплавление по всей обратной стороне соединения. Лицевая поверхность шва должна быть максимально плоской.
Второй и третий проходы. Сварочный ток может быть увеличен. Положение электрода аналогично использовавшемуся при сварке первого прохода. Используется техника сварки с поперечными колебаниями электрода. На рис. 34б показана траектория движения электрода. Для получения однородного по качеству и внешнему виду сварного шва следует поддерживать постоянство продольных и поперечных перемещений электрода.
Поперечные перемещения электрода должны производиться быстро, с тем, чтобы предотвратить появление избыточной выпуклости в центральной части сварного шва. На протяжении всего времени сварки необходимо поддерживать короткую дугу, следить за тем, чтобы перемещения электрода оставались в пределах ширины сварного шва. Для предотвращения появления подрезов применять остановки электрода в крайних точках траектории их перемещения.
В некоторых случаях сварку стыкового соединения со скосом кромок можно производить сверху вниз (рис. 35а) или однопроходным швом с поперечными колебаниями (рис. 356). Техника выполнения однопроходным швом аналогична выполнению второго и третьего прохода при многопроходной сварке.
Рис. 35. Сварка стыкового соединения со скосом кромок сверху вниз (а) и траектория перемещения электрода при однопроходной сварке с поперечными колебаниями (б)
Сварка таврового соединения в потолочном положении однопроходным угловым швом
Данное сварное соединение и положение при сварке очень часто встречается в судостроении и при изготовлении металлоконструкций.
Сварка таврового соединения в потолочном положении однопроходным угловым швом производится на обратной полярности, при этом сварочный ток не должен быть слишком большим. Положение электрода должно соответствовать изображенному на рис. 36а. Во время сварки используются возвратно-поступательные перемещения электрода. При наплавке металла необходимо поддерживать короткую дугу. При перемещении вперед дуга не должна обрываться.
Рис. 36. Положение электрода при сварке таврового соединения в потолочном положении однопроходным угловым швом
Во время сварки нужно уделять особое внимание обеспечению хорошего сплавления и проплавления в корневой части соединения, а также с боковыми кромками. Нельзя допускать подтекания шлака в головную часть сварочной ванны, для предотвращения появления избыточной высоты и выпуклости сварного шва не допускать перегрева сварочной ванны.
Сварка таврового соединения в потолочном положении многопроходным угловым швом.
При необходимости выполнения сварки угловым швом в потолочном положении больше чем за один проход применяется техника сварки без поперечных колебаний электрода. Сварку выполняют на обратной полярности, при этом сварочный ток не должен быть слишком велик. Положение электрода должно соответствовать изображенному на рис. 37а.
Рис. 37. Положение электрода при сварке таврового соединения в потолочном положении многопроходным угловым швом (а) и порядок наложения слоев (б)
Последовательность наложения слоев приведена на рис. 37б. У сварщиков, имеющих малый опыт, могут возникнуть некоторые сложности с соблюдением правильных пропорций швов. Однако с опытом эти трудности будут преодолены. Каждый проход должен иметь хорошее сплавление со смежными валиками и с поверхностью свариваемых кромок. Лицевая поверхность каждого прохода должна быть максимально плоской.
Сварка нахлесточного соединения однопроходным угловым швом в потолочном положении
Данное сварное соединение и положение при сварке очень часто встречается при сооружении резервуара и в судостроении. Из-за габаритов и характерных особенностей этих объектов их кантовка для проведения сварки не целесообразна. Большинство подобных работ выполняется на обратной полярности, однако имеются также случаи, когда необходимо сваривать нахлесточное соединение в потолочном положении и на прямой полярности.
Величина сварочного тока при сварке на обратной полярности не должна быть слишком большой. При сварке на прямой полярности величина сварочного тока должна быть несколько выше, чем при сварке аналогичного соединения на обратной полярности. Положение электрода должно соответствовать изображенному на рис. 38.
Рис. 38. Положение электрода при сварке нахлесточного соединения однопроходным угловым
При сварке можно применять колебательные перемещения электрода в направлении сварки. При перемещении электрода вперед необходимо следить, чтобы не произошло обрыва сварочной дуги. Такие перемещения электрода служат для предварительного подогрева кромок перед наплавкой на них электродного металла и способствуют предотвращению перегрева сварочной ванны, тем самым препятствуют образованию наплывов и избыточной выпуклости. Кроме того, такие перемещения электрода и сварочной дуги вызывают оттеснение шлака в хвостовую часть сварочной ванны. При сварке нельзя допускать выхода сварочной дуги на поверхность верхней пластины, и следует следить, чтобы сварочная дуга при своих перемещениях не выходила за границы наружной поверхности сварного шва.
При сварке на прямой полярности несколько затруднен контроль за шлаком. Сварной шов имеет тенденцию к образованию избыточной выпуклости, а также к вытеканию сварочной ванны на вертикальную поверхность кромки пластины. Подрезы не встречаются.
Сварка таврового соединения многопроходным угловым швом с поперечными колебаниями в потолочном положении
Сварщику в своей практике не раз приходится встречаться с необходимостью выполнения в потолочном положении угловых швов большого сечения электродами большого диаметра.
Первый проход. Сварочный ток должен быть достаточно большим. Положение электрода должно соответствовать изображенному на рис. 39а. Длина сварочной дуги должна быть небольшой, при сварке необходимо использовать поперечные колебания электрода (рис. 39б). Перемещения электрода должны производиться быстрыми скользящими движениями, в то же время необходимо следить за тем, чтобы при этом не происходило значительное увеличение длины дуги.
Во время проведения сварки нужно обращать внимание на поддержание стабильного горения сварочной дуги, не допускать ее обрыва. После кристаллизации кратера возвратиться к нему и переварить кратер. Это способствует предотвращению перегрева сварочной ванны и появлению трещин в металле сварного шва. Происходит предварительный подогрев корневой части сварного шва до того, как на него будет наплавлен электродный металл. Кроме того, такая техника сварки приводит к оттеснению шлака в верхнюю часть наплавленного металла. Улучшается возможность для контроля за наплавленным металлом и сварочной дугой, предотвращается появление подрезов, наплывов и избыточной выпуклости сварного шва, улучшается внешний вид поверхности сварного шва, она становится более однородной.
Рис. 39. Положение электрода при сварке таврового соединения многопроходным угловым швом с поперечными колебаниями в потолочном положении (а) и траектория движения электрода (б)
Второй проход. Второй проход выполняется так же, как и первый, с тем только отличием, что за второй проход наплавляется большее количество электродного металла. Выполнение второго прохода, как правило, вызывает у сварщиков большие сложности, чем первого.
Сварка стыкового соединения со скосом кромок на подкладке многопроходным швом в потолочном положении.
Данный тип сварного соединения и условия проведения сварки часто встречаются при сварке труб и резервуаров, когда сварка выполняется на кольцевых подкладках.
Первый проход. Сварка производится на обратной полярности. Сварочный ток должен быть достаточно большим. Положение электрода должно соответствовать изображенному на рис. 40. Для обеспечения хорошего переноса металла необходимо поддержание короткой дуги. Перемещения электрода должны носить скользящий характер. Необходимо обращать внимание на обеспечение гарантированного сплавления в области подкладки и между кромками в корневой части соединения. Лицевая поверхность сварного шва по возможности должна иметь минимальную выпуклость.
Второй и последующие проходы. Сварочный ток остается по-прежнему большим. Сварка производится с использованием техники скользящих перемещений электрода, без поперечных его перемещений. Если металл начинает перегреваться, необходимо удлинить дугу и переместить электрод вперед, пока кратер с перегретой сварочной ванной не остынет.
Рис. 40. Положение электрода при сварке стыкового соединения со скосом кромок на подкладке многопроходным швом в потолочном положении и порядок наложения слоев
Необходимо обеспечить гарантированное сплавление как с поверхностями ранее наплавленных валиков, так и со стенками разделки. Следует обращать внимание на безусловную необходимость очистки от шлака поверхности шва после каждого прохода.
Сварка стыкового соединения без разделки кромок многопроходным швом в потолочном положении
Подобное соединение в таком пространственном положении встречается крайне редко. Выполнить качественно такой сварной шов весьма трудно, для этого необходима определенная тренировка. Сварка производится на обратной полярности.
Первый проход. Сварочный ток не должен быть слишком большим. Положение электрода должно соответствовать изображенному на рис. 41. Сварочная дуга должна быть короткой. Для обеспечения полного проплавления с обратной стороны электрод должен все время находиться в зазоре между свариваемыми кромками. Кроме того, такое положение электрода обеспечивает сплавление с корневыми кромками свариваемых пластин. При сварке используются возвратно-поступательные перемещения электрода.
Рис. 41. Положение электрода при сварке стыкового соединения без разделки кромок многопроходным швом в потолочном положении
Второй проход. Сварочный ток не должен быть слишком большим. При сварке необходимо поддерживать короткую дугу и производить небольшие колебательные перемещения электрода, выполняемые легкими скольжениями, следить за тем, чтобы поперечные колебания электрода не имели слишком большой ширины.
Сварка стыкового соединения со скосом кромок многопроходным швом в потолочном положении
Данный тип сварного соединения и условия, в которых она выполняется, часто встречается при сварке труб и металлоконструкций из листового проката.
Сварка стыкового соединения со скосом кромок многопроходным швом производится на обратной полярности с поперечными колебаниями электрода. Сварочный ток при первом проходе не должен быть слишком большим, но при этом должен обеспечивать гарантированное проплавление с обратной стороны. Положение электрода должно соответствовать изображенному на рис. 42. Выполнение первого, корневого, прохода аналогично сварке первого прохода в ранее рассмотренных соединениях. Лицевая поверхность сварного шва должна быть плоской. С обратной стороны должен образовываться небольшой валик.
Рис. 42. Положение электрода при сварке стыкового соединения со скосом кромок многопроходным швом в потолочном положении
Второй и последующие проходы. Сварочный ток должен быть несколько больше, чем при первом проходе. Применяется техника сварки с поперечными колебаниями электрода. Перемещения электрода в поперечном направлении должны производиться быстрыми движениями, с тем чтобы в центральной части сварного шва не получалась слишком большая выпуклость. Кроме того, траектория поперечных перемещений электрода не должна выходить за пределы ширины сварного шва.
Для предотвращения появления подрезов используется задержка электрода в крайних точках траектории поперечных колебаний. Необходимо помнить, что подрезы появляются в результате «вылизывания» дугой металла на поверхности пластины с последующим ненаплавлением электродного металла на это место.
Особенности проведения сварочных работ в холодное время года
Сварочные работы уже давно не считаются привилегией исключительно профессионалов. В настоящее время такой способ соединения металлов активно используется и в быту. При этом все большую популярность приобретают сварочные инверторы. Это вполне объяснимо: они легкие, компактные, удобные в эксплуатации и обеспечивают отличное качество швов. Чаще всего сварочные работы проводятся в теплое время года. Можно ли делать это при отрицательных температурах? Попробуем разобраться.
Сварочные работы зимойВлияние температуры на процесс сварки металлов
Низкие температуры действительно оказывают влияние на процесс сварки. Расплавленный металл остывает и кристаллизуется с большей скоростью. Это означает, что из сварочной ванны не успевают выйти все растворенные газы или перейти в шлак неметаллические включения. Подобная ситуация может привести к образованию трещин или пор в швах. Известна такая статистика: при понижении температуры с +20 °С до -50 °С время пребывания сварочной ванны в жидком состоянии уменьшается на 10 %. Это, в свою очередь, приводит к тому, что половина из всех выявляемых дефектов относится именно к неметаллическим включениям.
При низких температурах повышается отвод тепла от зоны сварки. Это ухудшает проплавление кромок соединяемых элементов и может привести к образованию еще одного серьезного дефекта – непровара. Дополнительную опасность несет конденсация влаги на электродах или металле. Вода является источником водорода, который способствует образованию пор в швах. Кроме того, при низких температурах ухудшаются показатели пластичности сталей и механических свойств швов.
Все приведенные выше факты правдивы, но они в полной мере проявляются при экстремально низких температурах (от -40 °С и ниже). Бытовая сварка крайне редко требует работы в столь сложных условиях. Как правило, речь идет о температуре не ниже -10 °С. Дополнительно следует учитывать, что чаще всего для бытовых целей используются углеродистые стали. При толщине соединяемых элементов не более 16 мм работать с ними в обычном порядке можно до температуры -30 °С. Для низколегированных сталей этот показатель при той же толщине несколько меньше и составляет -15 °С.
Самая низкая температура поддерживается в открытом космическом пространстве. Она составляет -273 °С, но даже в таких условиях возможно выполнение сварочных работ. Впервые они были проведены в 1984 году советскими космонавтами С. Савицкой и В. Джанибековым. Для этой цели использовался специально созданный аппарат электронно-лучевой сварки.
Влияние температуры на сварочный инвертор
Низкие температуры могут влиять не только на металлы, но и на сварочные инверторы. Одним из главных врагов такой техники является влага. Ее появление внутри аппарата может привести к закорачиванию электронных компонентов и их выходу из строя. Низкие температуры при определенных условиях могут способствовать образованию конденсата в сварочных инверторах.
Точка росы
В этой связи важно вспомнить о понятии точка росы. Фактически это максимальная температура поверхности, при которой на ней появляется влага в виде конденсата. По-другому это утверждение можно перефразировать так: если поверхность холоднее точки росы, то конденсат на ней выпадет. Данная величина не является постоянной и напрямую зависит от влажности. Чем она выше, тем ближе точка росы к фактической температуре. Например, в душе при стопроцентной влажности зеркало запотевает при комнатной температуре. Обратная ситуация в герметичном оконном стеклопакете. Там влажность близка к нулю, поэтому конденсата не наблюдается никогда.
В сварочном инверторе влага может конденсироваться только в одном случае: если он постоял какое-то время на морозе, а затем попал в более теплое помещение. В такой ситуации его категорически запрещается использовать сразу. Инвертор должен постоять полтора-два часа, чтобы его температура сравнялась с температурой окружающей среды, а появившийся конденсат испарился. Если же аппарат из теплого помещения выносится на мороз, конденсат в нем образоваться не может и на работоспособности устройства это никак не отразится.
Как выполнять сварочные работы в морозы?
В целом сварочные работы при температуре не ниже -10 °С можно выполнять обычными бытовыми инверторами без каких-либо отрицательных последствий для качества швов, прочности соединений или работоспособности самой техники. При более сильных морозах следует использовать полупрофессиональные или профессиональные модели, специально предназначенные для эксплуатации при низких температурах. Они комплектуются электронными элементами, устойчивыми к холоду.
Дополнительно следует выделить несколько мероприятий, которые рекомендуется выполнять при проведении сварочных работ в зимний период:
- По возможности избегать пересечений сварных швов и резких переходов толщин металла.
- Сварочные работы начинать с швов, дающих максимальную усадку (стыковых).
- Минимизировать объем наплавленного металла.
- Во время работы сварочный ток увеличивать на 10-15 % и одновременно примерно на такую же величину уменьшать скорость перемещения электрода.
- По возможности начинать и заканчивать сварку на выводных планках.
- Тщательно зачищать кромки свариваемых элементов.
- Вместо прихваток использовать, например, струбцины или другие аналогичные приспособления.
- Применять не склонные к образованию пор типы электродов, обеспечивающие высокую пластичность швов: Э50А, Э46А или Э42А с основным покрытием. Перед использованием их необходимо тщательно прокалить.
Влияние отрицательных температур на сварщика
Отрицательные температуры могут влиять не только на металлы или технику, но и непосредственно на сварщиков. Трудоспособность в таких условиях снижается, а значит, возрастает риск появления дефектов. Оптимальным способом избежать подобной ситуации является использование специальной зимней защитной одежды. Не меньшего внимания заслуживают сварочные маски.
Наибольшей популярностью в настоящее время пользуются «хамелеоны». Их главным элементом является светофильтр. Он состоит из нескольких слоев жидких кристаллов и поляризационных пленок. Светофильтр реагирует на интенсивность светового излучения и срабатывает автоматически. Для затемнения ему необходимо не более 0,001 секунды. Этого вполне достаточно для надежной защиты глаз от губительного воздействия ультрафиолетового излучения, возникающего во время сварки.
Время срабатывания светофильтра «хамелеона» увеличивается при уменьшении температуры окружающей среды. При -5 °С оно составляет уже не 0,001 с, а 0,005-0,009 с. Как правило, такие маски предназначены для использования при температуре не ниже -10 °С. В этом случае они гарантируют надежную защиту глаз. При более низких температурах светофильтр может попросту не успевать срабатывать.
Заключение
Таки образом, зима вовсе не является преградой для выполнения сварочных работ. При температуре до -10 °С для этой цели вполне подойдут обычные бытовые инверторы. Для организации сварочных работ в более сильные морозы необходимо приобретение специализированной техники.
Поделитесь с друзьями:Время вспомогательное сварке — Энциклопедия по машиностроению XXL
Основное и вспомогательное время на сварку 1 пог. лг V-образного стыкового шва без подварки [c.469]Основное и вспомогательное время на сварку 1 пог. [c.470]
Время сварки. Техническое время (основное + вспомогательное) сварки для малоуглеродистой стали определяется как t = мин м. [c.542]
Норма времени на сварку включает основное время, вспомогательное время и время на обслуживание рабочего места, отдых и естественные надобности. Основное время — это время, используемое непосредственно на сварку, т. е. время горения дуги. Оно подсчитывается с учетом производительности оборудования и режимов сварки. Вспомогательное время складывается из затрат времени на подготовительно-заключительные операции получение задания, производственный инструктаж и сдачу работы) на установку детали на рабочее место, поворот ее в процессе сварки, зачистку шва, регулирование режима и т. д. Для ручной сварки основное время составляет от 50 до 70% для заводских условий и от 40 до 60% на строительных площадках. [c.248]
Для увеличения производительности необходимо увеличить количество металла, наплавляемого в единицу времени. С этой целью можно использовать наряду с двухдуговой автоматическую сварку трехфазной дугой. Применение сварки трехфазной дугой позволяет уменьшить количество слоев шва, сократить машинное и вспомогательное время. Проблема сварки металла большой толщины решена в последние годы применением способа электрошлаковой сварки с принудительным формированием шва. [c.78]
Вспомогательное время при сварке конструкций тратится на [c.392]
Вспомогательное время при сварке швов затрачивается на смену присадочной проволоки приварку прутка к огарку в процессе сварки осмотр и очистку кромок шва, на его измерение. [c.398]
Вспомогательное время при сварке конструкции идет на установку, закрепление, снятие ее перемещение сварщика, клеймение шва. Устанавливают вспомогательное время по таб- [c.398]
Циклограмма работы трубоэлектросварочного стана показывает, что вспомогательное время, затрачиваемое на загрузку трубной заготовки, выгрузку сваренной трубы, на установку трубной заготовки в стане и другие операции (кроме процесса сварки) составляет 30 сек. Время собственно сварки лежит в пределах 15—30 сек. Производительность стана составляет примерно 60 труб в час. [c.120]
Норма времени, кроме основного времени ( о), необходимого для выполнения собственно сварки (машинного времени), включает ряд других составляющих времени, необходимого для проведения ряда дополнительных работ подготовительно-заключительное время ( ), вспомогательное время (Q, время на обслуживание рабочего места и время на отдых и естественные надобности ( отэ)- [c.328]
Основные требования. Установка должна иметь достаточно высокую производительность, оправдывающую её применение. Производительность установки определяется скоростью сварки и коэфициентом использования сварочных головок. Последний равен отношению машинного времени сварки к суммарному времени, затрачиваемому на сварку и на вспомогательные операции. Машинное время зависит от скорости сварки и длины шва, а вспомогательное время—от конструктивной схемы установки и организации работ на ней. [c.212]
Вспомогательное время при автоматической сварке нормируется по двум группам элементов 1) связанных со свариваемым швом и [c.473]
При контактной сварке вспомогательное время подразделяется на время, зависящее от типа сварочной машины, и время, зависящее от свариваемых деталей. Оно, как правило, определяется на основе данных хронометража. [c.478]
С помощью контактной сварки изготавливают до 90 % конструкций, свариваемых давлением, и около 50 % всех сварных конструкций. Это объясняется преимуществами контактной сварки перед другими способами высокой производительностью (время сварки одной точки или стыка составляет 0,02… 1,0 с), малым расходом вспомогательных материалов (воды, воздуха), высоким качеством и надежностью сварных соединений при небольшом числе управляемых параметров режима, что снижает требования к квалификации сварщика. Это экологически чистый процесс, легко поддающийся механизации и автоматизации. [c.281]
Разнообразны материалы, применяемые в сварных конструкциях, каждый из них по-своему реагирует на попытки сварить их, поэтому даже в традиционных способах сварки приходится все время изобретать новые приемы, новые вспомогательные материалы, приспособления, оборудование. Со многими из них вы познакомились в этом учебном пособии. [c.387]
При рассмотрении сварочных операций различают механизацию и автоматизацию основных и вспомогательных работ. Механизация основных работ, например применительно к дуговой сварке, включает подачу присадочных, защитных и вспомогательных материалов в зону плавления и перемещение сварочного инструмента (или группы инструментов) вдоль линии соединения во время сварки. При автоматизации основных работ (той же дуговой сварки) автоматическое управление выполняет следующие функции возбуждение дугового процесса с изменением параметров [c.30]
Эффективность сварки несколькими головками следует повышать прежде всего сокращением тех затрат времени, доля которых в величине наибольшая. Например, при дуговой сварке сравнительно коротких швов, когда время /д относительно невелико, обычно целесообразно автоматизировать все или большинство перечисленных выше вспомогательных действий и приемов и обеспечить возможность одновременного обслуживания всех сварочных головок. При сварке швов большой длины в ряде случаев можно ограничиться частичной автоматизацией установки для сварки несколькими головками, причем в первую очередь должно быть автоматизировано направление сварочных инструментов на линию соединения, без которого практически невозможно осуществить обслуживание нескольких головок одним оператором. [c.45]
Комплексно-автоматизированное производство — способ выполнения производственного процесса, при котором все основные и вспомогательные операции, в том числе управление и регулирование осуществляются машинами, механизмами так, что заданная производительность и качество продукции достигаются без участия человека. Человек лишь наблюдает за работой специальных устройств или систем управления. Автоматическая (механизированная) поточная линия — ряд машин (автоматов, полуавтоматов), расположенных по технологическому циклу и соединенных транспортными устройствами. Следует отметить, что термины «автоматическая сварка» и соответственно «сварочный автомат» несколько условны и не отражают того, что сварочный автомат работает без участия человека, как это понимается в машиностроении. В то же время определение «сварочные станки-автоматы» соответствует принятому в машиностроении понятию «станок-автомат», которое обозначает агрегат, работающий по автоматическому циклу. [c.53]
В РТК с одним манипулятором изделия существует очередность работы робота и сварочного оборудования или загрузочно-разгру-зочного устройства (при отсутствии многостаночного обслуживания). Поэтому РТК с одним манипулятором изделия целесообразно применять только в тех случаях, когда время сварки значительно больше времени загрузки-выгрузки. При двух манипуляторах изделия в то время, когда на одном из них производится сварка, на другом выполняются разгрузочные, загрузочные, сборочные и другие работы. Если время сварки равно времени перечисленных вспомогательных работ, то обеспечивается полная загрузка оборудования и оператора. [c.142]
Основное время для всех типов сварочных установок, при прочих равных условиях (длина шва, тип материала, глубина проплавления, параметры пучка, скорость сварки и др.) одинаковое, а вспомогательное изменяется в очень больших пределах в зависимости от конструкции установок, что существенно влияет на производительность. Для универсальных установок периодического действия, предназначенных для сварки одного изделия за одну откачку сварочной камеры, основное время составляет приблизительно 5%. Остальное время затрачивается на выполнение вспомогательных операций. Увеличить производительность установок можно двумя путями сокращением времени выполнения каждой вспомогательной операции или выполнением вспомогательных операций параллельно со сваркой изделия. [c.355]
Автоматизация установок для электроннолучевой сварки является одним из важнейших направлений их совершенствования и позволяет добиться существенного повышения качества сварных соединений. Как уже отмечалось, время выполнения подготовительных и вспомогательных операций и диагностирования состояния функциональных систем таких установок превышает обычно время на проведение собственно технологических операций. Использование систем автоматического и программного управления дает возможность повысить производительность труда и надежность функционирования установок, а также обеспечивает высокую воспроизводимость технологического процесса. Кроме того, системы управления с использованием вычислительной техники расширяют технологические возможности сварочных установок. [c.360]
Вспомогательное время затрачивается рабочим на выполнение различных вспомогательных действий, обеспечивающих основную работу (на установку, закрепление и снятие обрабатываемой детали перестановку инструмента промеры обрабатываемого изделия поворот детали при сварке и т. п.). [c.350]
Вспомогательное время при точечной сварке [c.97]
Вспомогательное время при шовной сварке [c.98]
Вспомогательным называется время, затрачиваемое рабочим на определенные действия, связанные с обеспечением выполнения основной работы. К таким действиям относятся установка, крепление и снятие детали, наладка оборудования и управление им в период работы, перестановка инструмента (замена электродов), обмер детали и взятие пробных стружек, подача детали к месту сборки, очистка шва от шлака и поворот детали при сварке и наплавке, завеска деталей в ванну при гальванических покрытиях и т. д. [c.348]
Нормативы основного, вспомогательного и неполного оперативного времени построены так же, как и при электродуговой сварке. Продолжительность Го и определяют с учетом толщины свариваемых листов, номера наконечника горелки и диаметра присадочного материала. Вспомогательное время назначают по нормативам в зависимости от вида вспомогательных работ и массы свариваемых изделий. [c.372]
Автоматическая электросварка, упрощая технику выполнения процесса сварки и повышая его производительность, требует в то же время повышения общей культуры и лучшей организации всех подготовительных операций, предшес1вующих сварке. В первую очередь это относится к повышению качества подготовки деталей к сварке, сборке свариваемых узлов и др. Внедрение автоматической сварки должно сопровождаться максимальной механизацией всех элементов процесса путём оборудования рабочего места индивидуальными подъёмно-транспортными устройствами, специальными приспособлениями для установки, поворота, враш,ения и т. д. При разработке технологического процесса, установлении технических норм и организации труда на участках автоматической сварки следует исходить из необходимости наибольшего использования автомата и выполнения элементов вспомогательной работы во время автоматической сварки. Последнее может быть успешно достигнуто в условиях серийного и массового производства путём оснащения рабочего места несколькими приспособлениями-дублёрами для крепления свариваемых узлов, придав им линейное или кольцевое расположение. [c.472]
Три нормировании вспомогательного времени следует обязательно исходить из необходимости наибольшего использования сварочного автомата. Наибольший коэфициент использования может быть достигнут при условии а) выполнения элементов вспомогательной работы во время автоматической сварки, т. е путём перекрытия их (например, при работе с двумя приспособлениями, во время сварки узла в первом приспособлении, во втором из них может производиться удаление сваренного узла, а также установка и крепление следуюнхего комплекта свариваемых деталей) и б) освобождение сварщика от выполнения неперекрываемых элементов вспомогательной работы путём передачи их вспо- [c.473]
Гука или кадданной передачи), этот-механизм служит для передачи вращательного движения между валами, оси которых пересекаются, Нешироко применяется в автомобилях, станках, приборах (входное и выходное звенья 1,3 выполнены в виде вилок, звено 2 — в виде крестовины, звено 4 — стойка О — точка пересечения осей) ж — структурная схема основного рычажного механизма одного из видов промышленного робота, это механизм с незамкнутой кинематической цепью AB DEF (звенья I—5 — подвижные, б — стойка, f —охват). Промышленные роботы в настоящее время находят все более широкое применение для выполнения самых различных технологических и вспомогательных операций сборки, сварки, окраски, загрузки и т. п. [c.28]
Время, затраченное на вспомогательные работы, зависит от разнообразных организационных факторов, главнейшими из которых являются а) организация подготовительных работ, б) порядок снабжения сварщика электродами, в) смена электродов, г) тип применяемых приспособлений и степень механизации работ по перекантовке изделия в требуемое для сварки положение, д) квалификация сварщика. [c.467]
Вспомогательное время, связанное со свариваемым швом, включает время на смену электродов, зачистку кромок, очистку шва от шлака, на промеры и осмотр шва. Время на смену электродов для сварки данного шва равно произведению времени смеиы одного электрода на количество электродов, расходуемых на шов. Время на смену одного электрода при нормальном электрододержателе может быть принято для сварки нижних швов равным 0,18 мин., а для потолочных швов — 0,25 мин. [c.468]
Пример оформления технологического процесса сборки и сварки на операционных картах согласно ЕСТД показан на рис. 185. В операционных картах применены следующие условные обозначения ОК -операционная карта О — переход операции К/М — комплектующие детали и материалы Р — режимы МИ — масса изделия Т — инструмент То — основное время на переход Тв — вспомогательное время на переход ОПП — обозначение подразделения (кладовой, склада), откуда поступают детали, сборочные единицы, материалы или куда поступают обработанные детали, узлы ЕВ — единицы измерения величины (массы, длины и т.п.) ЕН — единица нормирования, на которую устанавливается норма расхода материала (например, 1,10,100) КИ — количество деталей, сборочных единиц, применяемых при сборке изделия Н. расх. — норма расхода материала P — режим сварки ПС -обозначение положения сварки по ГОСТ 11969-79 ДС — диаметр сопла для сварки в защитных газах со струйной защитой, мм 4 — расстояние от торца сопла до поверхности свариваемых деталей /э — вылет электрода, мм U — напряжение дуги I — сила сварочного тока Ус -скорость сварки V — скорость подачи присадочного материала доз -расход защитного газа. [c.369]
Многопозиционные установки и станки для сварки круговых швов. Применение многопозиционных установок и станков так же, как и многоголовочной и много дуговой сварки, уменьшает объем вспомогательных работ и значительно повышает производительность труда и оборудования. Многопозиционные установки и станки для сварки круговых швов существенно отличаются от однопозиционных. Они бывают последовательного, параллельного, последовательно-параллельного действия и роторные. В многопозиционной установке или станке время зафузки в одной позиции совмещается со временем сварки в другой. Схемы некоторых компоновок многопозиционных установок и станков с вертикальной осью вращения приведены на рис. 1.28. Установка, скомпонованная по рис. 1.28, а, имеет одну сварочную позицию, а остальные используются для загрузки и выгрузки деталей. Установка, скомпонованная по рис. 1.28, 5, имеет две сварочные (их может быть и больше) и по [c.89]
При выборе типа установки следует учитывать, что в связи с высокой производительностью процесса ЭШС при большой массе свариваемых деталей и малосерийном характере производства основная часть времени (около 70…80%) в общем цикле производства сварной детали приходится на вспомогательные и подготовительно-сборочные операции. Для существенного сокращения вспомогательного времени следует применять установки второго и первого классов, что позволяет сократить вспомогательное время (до 30% общего времени сварки). Однако такие установки имеют высокую стоимость, и целесообразность их применения определяется загрузкой. [c.149]
В последнее время много внимания уделялось вопросам механизации вспомогательных операций, сопутствующих сварке. Одним из важнейших узлов является узел гратосъема. Многие стыковые машины снабжаются специальными блоками и приборами контроля параметров процесса сварки, которые позволяют с большей достоверностью оценить качество сварных соединений без применения разрушающих методов контроля. [c.187]
В последние годы широкое распространение получили установки «тактового типа», у которых время выполнения всех вспомогательных операций сокращено до минимума за счет уменьшения объема камер, времени откачки, в том числе за счет выполнения сварки в промежуточном вакууме. Такие установки начали применяться на заводах автомобильной промышленности, в частности при изготовлении деталей автоматических коробок скоростей и трансмиссий. Установки имеют в большинстве случаев разъемные камеры. Одна часть камеры (обычно верхняя), в которой смонтирована пушка, неподвижно закрепляется на станине и снабжается по разъему вакуумным уплотнением. Другая часть — несушая гнездо для закрепления изделия (или изделий), может перемешаться относительно неподвижной части, что создает удобство перезагрузки свариваемых деталей и доступ к механизмам их перемешений. Совмешение пучка со свариваемым стыком достигается благодаря точности изготовления и монтажа механизмов перемешения изделия и стабильности положения пучка. Ручные механизмы корректировки положения стыка используются при на- [c.356]
Многоточечная сварка. Детали располагают за пределами внешнего контура машины, что позволяет вести сварку узлов весьма больших габаритных размеров на машинах с небольшим контуром пр,и небольших потерях мощиссти и энергии. Свар.ку осуществляют сразу одной. или несколькими парами электродов пр.н неподвижном изделии, что резко снижает. М1ашинное и вспомогательное время. Характеристика наиболее распространенных способов многоточечной сварки дана в табл. 2. [c.71]
Вшомагательное время — это время, затрачиваемое на подноаку деталей и установку их в машину на центровку, зажатие и перемещение деталей на включение машины, снятие деталей с машины и переноску их яа складочное место. В табл. 66—68 приведены ориентировочные данные вспомогательного времени для стыковой, точечной и ш-оаной сварки. Время иа обслуживание рабочего места и перерывы может быть ориентировочно определено по табл. 69. [c.97]
Движение Электрода при Сварке
Ни для кого не секрет, что во время сварки металла выполняется движение электродов. Эти движения зачастую называют колебательными. Существует множество технологических подходов к выполнению сварочных работ металла. Электроду в процессе сварки, независимо от применяемого способа, сообщается движение в трёх разных направлениях.
Первое движение называют поступательным, при котором движение идёт по оси электрода. Зависимо от скорости плавления, поступательное движение поддерживает постоянную длину дуги, которая не должна выходить за пределы 0.5-1.2 диаметра электрода. Длина дуги зависит от марки электрода и условий сварки. Формирование шва ухудшается при уменьшении длины дуги, а также возникает вероятность короткого замыкания (сокращенно КЗ). Увеличение же дуги является причиной повышения разбрызгивания металла электрода и снижения качества сварного шва по форме и его свойствам (механическим).
Вторым движением является смещение электрода вдоль оси с целью образования шва. Диаметр электрода, сила тока(постоянным или переменным) и скорость плавления электрода определяют скорость движения электрода. В случае отсутствия поперечных смещений электрода, шов получается узкий (ниточный), ширина которого равна приблизительно 1.5 диаметра применяемого электрода. Данный шов используют при сварке тонких металлических листов.
Последним движением является смещение электрода поперек для корректировки ширины шва и глубины плавления металла. Данные колебательные движения предполагают высокую квалификацию сварщика и его навыков, а также определяются характеристиками свариваемого материала, положением и размером шва. Ширина шва, при использовании поперечных колебательных движений варьируется в пределах 1.5-5 диаметра используемого электрода.
Грамотное и технически правильное перемещение электрода – главная задача и условие для получения качественного шва при выполнении сварочных работ. Важна определённая методика выполнения колебательных движений электрода, а также рациональность его перемещения. Для выполнения качественного шва существует несколько общих способов, применяемых в любых ситуациях, с помощью которых сварщик выполняет движения во время сварки. Это движения «ёлочкой» (а), углом (б), «движение по спирали» (в), «движение полумесяцем» (г). Рис.1
При сварке вертикального углового сварочного шва наиболее удобно показать все способы колебательных движений электрода, к тому же это очень часто применяемая операция в сварке изделий из проката. При этом мы опустим все вопросы, связанные с разделкой кромок и подготовкой поверхностей перед сваркой.
С применением колебательных движений электрода полумесяцем или по спирали , изначально наплавляют электродом полочку на кромки, а после мелкими порциями без пропусков и разрывов наплавляют металл, рекомендуется выполнять сварку непрерывно. Дальнейшая сварка металла производится постепенно со смещением электрода выше, за собой оставляя, готовый сварочный шов. Другая схема колебательного движения при сварке – углом , предусматривает колебательные движения электрода с применением попеременного смещения вверх-вниз, без разрывов наплавливают на кромки металл с равномерным перемещением электрода вверх.
Методика «ёлочкой» характеризуется движением электрода вверх, затем вправо, после этого по короткой траектории спускают вниз влево. Желательно чтобы капля металла застывала при каждом отдельном этапе сварки между кромками. После, ушедший электрод двигают вверх влево и опять спускают из точки подъёма, но теперь вниз вправо. Такими постепенными движениями с непрерывными отдельными порциями, и выполняется шов сварки.
Правила и время проведения сварочных работ
Каждому человеку хотя бы раз в жизни приходится на время отложить все свои дела и приступить к выполнению мужских обязанностей — ремонту. Сварочные работы — неотъемлемая часть починки или ремонта. Будь то обновление труб, или просто ремонт стула. На первый взгляд неопытному человеку может показаться, что для правильного осуществления и проведения сварочных работ не требуются особые знания, но это очень серьезное заблуждение. Если не знать основные правила, то можно не только испортить предмет сварки, но и навредить собственному организму.
Как подготовиться к проведению сварочных работ
Первое и одно из главных правил — это техника безопасности. Не забывайте, что вы будете иметь дело с опасными инструментами, от которых постоянно будут отлетать искры. Следовательно, вам просто необходимо запастись соответствующим костюмом.
Специалисты советуют использовать брезент в качестве защиты от нежелательных иск. В специализированных магазинах можно приобрести брюки, куртку, перчатки из брезента.
Куртку лучше всего заправить в брюки, таким образом, вы защитите себя от случайных травм. Но одежда еще не самое главное. Одной из распространенных травм во время сварки является ожог роговицы глаза. Случиться это может абсолютно случайно. Один раз «поймаете зайчика» и все.
Чтобы защитить себя от подобных ожогов, лучше всего приобрести специальный шлем или маску для сварки. Если их найти не удалось, то на крайний случай подойдут и солнечные очки со стеклянными линзами.
Необходимо также убедиться, что рядом с местом проведения сварки есть запас воды, чтобы в случае чего можно было бы затушить пожар. Уберите все горючие жидкости и вещества, а также легко воспламеняющиеся предметы.
Для избавления от окалины после сварки вам понадобиться молоток (желательно тяжелее 300 грамм).
Место сварки должно быть хорошо защищено от ветра, сквозняка, но в тоже время необходимо, чтобы в помещении была бы правильно организована вентиляция воздуха: во время нагрева металлов выделяется огромное количество вредных веществ. Если комната будет не проветриваемая, то все эти вещества попадут на предметы или же вам в организм. Включать вентилятор или любые другие «дующие» приборы строго настрого запрещено: разлетающиеся искры могут послужить причиной ожога и пожара.
В зависимости от того, какой материал именно будет подвергаться обработки, следует учесть и время нагрева. Если этот фактор будет учтен неправильно, то очень возможно, что спустя короткий промежуток времени вам придется начинать сварку заново.
У многих начинающих сварщиков и непрофессионалов возникает один и тот же вопрос, сколько времени следует нагревать полипропиленовые трубы при сварке.
Все зависит от диаметра трубы: чем он больше, тем дольше, следовательно, надо нагревать. Так, например, полипропиленовую трубу диаметром двадцать сантиметров нагревать следует всего лишь пять секунд, а диаметром девяносто сантиметров — сорок секунд.
Время следует засекать непосредственно с того момента, когда труба и фитинг натянуты на паяльник. После завершения сварки на шве останется окалина. Избавиться от нее можно при помощи молотка. Опытные мастер, ударив молотком по шву, понимает, насколько хорошо или плоха была проведена сварка.
Скорость сварки
Скорость сварки также очень важно учитывать еще до начала работ. Чем быстрее все будет проведено, тем меньше вредных веществ будет выделено в воздух.
При высокой скорости сварки, шов, скорее всего, получится не ровным и не гладким. Если вы варите трубы, то особенно важна равномерность перехода от одного сантиметра к другому. Постарайтесь сделать так, чтобы шов везде был одинаковой ширины и толщины.
Но только очень опытные мастера могут быстро проводить сварку таким образом, чтобы это не влияло на качество шва. Помните, что главное не скорость сварки, а качество. Движения должны быть плавными и уверенными. Если чувствуете, что начали затекать руки, или глаза уже сильно болят от зайчиков, то закончите данный шов и сделайте небольшой перерыв.
Но основной залог того, что вам удастся правильно и прочно сварить два металла — это опыт. Именно поэтому начинающим мастерам всегда советуют потренироваться на ненужных деталях. Лучше, если они будут не слишком толстыми. Прочувствуйте аппарат, поймите, какие моменты получаются лучше, а какие хуже. Только после всего этого можно приступать к настоящей сварки, в противном случае, возможно, что вы не почините, а наоборот окончательно испортите нужную вещь.
При небольшой тренировки вполне возможно, что в скором времени у вас начнут получаться настоящие творения из металлов. Но наша основная цель — это не искусство, а прочность и качество. Особенно, если дело касается важных вещей, например, таких как системы водоснабжения или электроснабжения. При неправильной сварки возможен не только быстрый выход систем из строя, но и довольно неприятные последствия.
В каких же случаях стоит самостоятельно попробовать сварить металлы? Если вы хотите стать мастером и только учитесь, то вам не однократно придется совершать ошибки по скорости сварки. Но это является нормальным процессом обучения любому делу. Ученики часто пытаются осуществить заказ быстрее, чем учитель, но в итоге работу приходится переделывать с нуля. Поэтому не забывайте, что скорость сварки — это конечно хорошо, но не основное, чему надо учиться.
Если же вы далеко не специалист и особого желания становиться им нет, если вам просто надо на быструю руку осуществить сварочные работы, то лучше рассудить, сможете ли вы это сделать самостоятельно или лучше обратиться к профессиональному сварщику.
Но главное во время сварки — это всегда соблюдать правила безопасности!
Урок 9 — Оценка и сравнение затрат на металл сварного шва
Урок 9 — Оценка и сравнение затрат на металл сварного шва © АВТОРСКИЕ ПРАВА 2000 ГРУППА ЭСАБ, ИНК.УРОК IX 9,7 ДРУГОЕ ПОЛЕЗНЫЕ ФОРМУЛЫ Информация, обсуждаемая ниже, поможет вам в других полезных расчетах: ОБЩЕЕ НЕОБХОДИМО ФУНТОВ ЭЛЕКТРОДОВ (См. ПРИМЕР 1) Перед выполнением расчетов необходимо определить следующую информацию / переменные: (1) Предлагаемый метод расчета стоимости (2) Поток расчета стоимости текущего метода Порошковая дуговая сваркаГаз Металл Дуговая сварка
E71T-1 .045 Диаметр. при 180 А
(3)ЭР70С-3 .045 Диаметр. при 125 А
(4)
Фактический Тарифы на оплату труда и O / H для вашего клиента
30.00 $Фактический Тарифы на оплату труда и O / H для вашего клиента
30.00 $Депонирование Тариф в фунтах в час
4.9Депонирование Тариф в фунтах в час
2,8Операционная Фактор
45%Операционная Фактор
50%Электрод Стоимость за фунт
1.44 год $Электрод Стоимость за фунт
0,66 $Депонирование Эффективность
85%Депонирование Эффективность
96%Газ Тип
СО2Газ Тип
75% Ar / 25% CO2Газ Расход
35 годГаз Расход
30Газ Стоимость за кубический фут
0.03 $Газ Стоимость за кубический фут
0,11 $Оборудование Стоимость
— $Подготовлено Для:
ИМЯ ИНФОРМАЦИЯ
Имя клиента:
ИМЯ ИНФОРМАЦИЯ Дата: (1) Предлагаемый метод расчета стоимости (2) Результат расчета стоимости настоящего метода Формулы для расчета Поток Газ для дуговой сварки порошковой краской Дуговая сварка металла (Стоимость
Редукция)
Увеличение труда и знак равно
Труда & Накладные расходы / Hr
знак равно 30,00 долл. США знак равно 30,00 долл. США знак равно 13,605 $ 30,00 долл. США=
30,00
знак равно 21 429 долл. США (7,823 долл. США ) Накладные расходы ОсаждениеОценить (фунты / час)
Икс Операционная Фактор 4.9 Икс 0,45 знак равно 2.205 2,8 Икс 0,5=
1,4
Электрод Электрод Стоимость / фунт = 1,44 знак равно 1,6940,66
знак равно 0,688 1,007 долл. США Осаждение КПД 0,850,96
Тип газа = CO2 Газ Тип = 75% Ar / 25% CO2 газ Газ Расход (куб.футов / час) X Стоимость газа / куб. Фут = 3 5 Икс 0,03 знак равно 1.05 знак равно 0,214 30
Х
0.11
=
3,3
знак равно 1,179 (0,964 доллара США ) Скорость осаждения (фунты и / час) 4.92,8
Сумма из вышеперечисленного Переменная стоимость / фунт депонирования Сварной металл = 15,514 долл. США Общий Переменная стоимость / фунт депонирования Сварной металл = 23,295 долл. США ( $ 7,781) Т итого Всего фунтов = Отложение Эффективность Вес / фут сварного шва x Число футов сварного шва Подстановка значений из примера 1:.814 х 1,280 .630 = 1,631 фунт СВАРКА НЕОБХОДИМОЕ ВРЕМЯ (См. ПРИМЕР 1) Сварка Время = Вт / фут сварного шва x футов наплавленного шва Коэффициент x замещение рабочего фактора значения в Примере 1: .814 х 1,280 5,36 х 0,30 = 1 042 1 608 = 648 часов.Что такое время дуговой сварки и вы его переоцениваете?
Повышение производительности сварщика
Распространенная ошибка — завышение времени горения сварочной дуги.Производственные предприятия могут быть удивлены, обнаружив, что среднее время горения дуги при полуавтоматической сварке составляет всего от 10 до 12 процентов.
Когда компании не думают о том, как уменьшить время дуговой сварки, они упускают из виду ключевые способы повышения производительности и прибыли. Время горения дуги напрямую влияет на количество деталей, выходящих за дверь каждый день.
Показатель времени зажигания дуги не включает время, затрачиваемое на сборку детали, подготовку материала к сварке, очистку или шлифование после сварки, но это шаги, которые могут значительно увеличить время процесса в целом.Чтобы найти способы сократить время горения дуги, важно учитывать действия, выполняемые до и после сварки, а не только во время самой сварки.
Изучите несколько советов по увеличению производительности в производственных приложениях, в которых используется газовая дуговая сварка (GMAW).
Совет № 1: Обратите внимание на подгонку детали
Задолго до того, как сварщик зажжет дугу, правильная подгонка деталей является определяющим фактором его эффективности при сварке. Сварщик может отвечать за сборку детали или это может быть кто-то другой, участвующий в операции.Проблемы с подгонкой деталей можно даже проследить вплоть до стадии проектирования или проектирования.
Если вы потратите время на последовательную и равномерную сборку деталей, это позволит устранить зазоры между деталями и впоследствии окупится за счет экономии времени. Когда между свариваемыми деталями имеются большие или неравномерные зазоры, это замедляет работу сварщика и увеличивает количество брызг, что требует больше времени для послеварочного шлифования.
Совет № 2: Используйте правильный процесс сварки
Идея изменения процесса сварки может вызывать затруднения у некоторых производителей.Может потребоваться дополнительное обучение и повторное утверждение любых изменений в Спецификации процедуры сварки (WPS). Но переключение процесса может дать значительный результат в производительности в правильных приложениях.
Варианты процесса сварки включают стандартный GMAW, модифицированный GMAW с коротким замыканием или многочисленные процессы импульсного GMAW. Если на предприятии есть большие зазоры в деталях, которые невозможно исправить при подгонке, например, модифицированный процесс GMAW короткого замыкания является хорошим решением, поскольку он предлагает превосходные возможности заполнения зазоров.
Импульсные процессы обеспечивают множество преимуществ для производительности, включая меньшее разбрызгивание, меньшее тепловложение и более высокую скорость движения. Импульсный процесс может обеспечить на 10% более высокую скорость движения при том же тепловложении по сравнению с прямым GMAW. Кроме того, некоторые усовершенствованные импульсные процессы, такие как технология Accu-Pulse ™ от Miller Electric Mfg. LLC, предлагают на 28% более широкое рабочее окно. Это упрощает использование процесса, поэтому сварщики с любым уровнем подготовки могут создавать высококачественные сварные швы, даже если техника или параметры различаются.
Замена присадочного металла или защитного газа также может помочь повысить производительность труда. Имейте в виду, что для замены газа и присадочного металла также может потребоваться повторное одобрение WPS.
Многие производители используют сплошную проволоку для GMAW, но порошковая проволока и проволока с металлическим сердечником могут дать преимущества в определенных областях применения. Правильный раствор присадочного металла зависит от используемого процесса, свариваемого материала и защитного газа. Например, порошковая проволока может обеспечить значительное повышение производительности благодаря очень высокой скорости перемещения, но ее трудно использовать при импульсной сварке.
Различные защитные газы также могут лучше подходить для определенных применений и процессов. 100% углекислый газ широко используется в производстве, поскольку он доступен по цене и обеспечивает легкую сварку операторам с меньшим опытом. Однако это приводит к гораздо большему разбрызгиванию, чем смешанный газ, что требует больше времени для шлифовки после сварки. Смешанный газ, такой как 90% аргона / 10% CO 2 , может обеспечить более высокую скорость перемещения и обеспечить лучший сварной шов, поэтому меньше времени тратится на очистку после сварки.
Совет № 3: Проверьте параметры
Обеспечение правильного выбора параметров во время сварки имеет решающее значение для получения хороших сварных швов, не требующих длительной доработки. Слишком высокая или медленная скорость движения, слишком высокая или холодная подводимая энергия и неправильный вылет проволоки — это параметры, за которыми следует следить.
Слишком низкая скорость перемещения приводит к увеличению тепловложения в зоне сварного шва, что может вызвать коробление. Поддержание адекватной скорости движения помогает контролировать нагрев. Но слишком быстрое (и слишком холодное) движение может слишком быстро влить слишком много присадочного металла в сварной шов, что приведет к разбрызгиванию или отсутствию проплавления, что потребует доработки.Другая причина повышенного разбрызгивания — слишком большой вылет проволоки.
Когда целью является сокращение времени горения дуги, худшее, что может сделать сварщик, — это сделать плохой сварной шов, требующий доработки. Время, необходимое для вырезания плохого сварного шва и его замены новым, может утроить затраченное время — или даже больше.
Совет № 4: Сократите время поиска и устранения неисправностей
Время, затрачиваемое на устранение неполадок, таких как проблемы с подачей проволоки, сокращает время зажигания дуги, поэтому для обеспечения оптимальной производительности важно поддерживать горелку GMAW в надлежащем состоянии.
Если футеровка горелки или контактный наконечник слишком изношены или натяжение приводного ролика неправильно отрегулировано, эти проблемы будут способствовать проблемам с подачей проволоки, что может привести к увеличению разбрызгивания и плохому качеству сварки. Проблемы с качеством сварки также часто возникают из-за изношенных сварочных кабелей или плохого соединения кабелей.
Перед каждой сменой — и после внесения любых изменений в процесс сварки — дважды проверяйте все соединения расходных деталей в системе подачи проволоки, чтобы убедиться, что все установлено и правильно затянуто.Также обратите внимание на признаки износа или повреждений. Это помогает сократить время, затрачиваемое на устранение неполадок, поэтому сварщик может проводить больше времени под капотом.
Совет № 5: Положитесь на технологии
Поскольку отрасль борется с нехваткой квалифицированных сварщиков, а многие компании ищут способы повышения производительности, технологии могут помочь. Когда источник сварочного тока обеспечивает большую простоту использования и улучшенное управление дугой, сварщикам с любым уровнем подготовки становится проще производить высококачественные сварные швы и уменьшать количество ошибок, а, следовательно, сокращать время горения дуги.
- Синергетическое управление: Дополнительные источники сварочного тока предназначены для автоматического внесения изменений в соответствии с настройками оператора. Когда оператор изменяет скорость подачи проволоки, машина регулирует напряжение в соответствии с требованиями, обеспечивая использование оптимальных параметров.
- Упрощенная установка: Некоторые новые сварочные системы предлагают «простую кнопку» для настройки машины, поэтому сварщики могут быстрее проникнуть под капот. Это может быть особенно полезно для менее опытных сварщиков.При использовании этой технологии оператору нужно только ввести толщину материала, а источник питания автоматически установит другие параметры соответствующим образом. Это экономит время и помогает снизить вероятность разбрызгивания и деформации, которые увеличивают очистку после сварки и могут потребовать доработки.
- Блокировки и ограничения: Источники сварочного тока, которые включают эту функцию, позволяют заблокировать определенные параметры в пределах установленного диапазона. Например, если блокировка установлена на 28–32 вольт, оператор не может выходить за пределы этого окна.Когда производитель обучает новых сварщиков, эта технология помогает удерживать их в пределах диапазона параметров для конкретной работы. Некоторые системы также могут отправлять предупреждения, чтобы менеджеры или руководители знали, когда сварщик работает за пределами заданных параметров.
- Мониторинг данных сварных швов: Цифровой мониторинг сварных швов доступен для большего количества источников питания, чем когда-либо, что позволяет производителям любого размера отслеживать важные показатели производительности. Доступные решения варьируются от базовых систем, которые проверяют параметры сварки и сообщают о производительности, до более продвинутого программного обеспечения для мониторинга, которое обнаруживает ошибки сварки, отслеживает детали и обеспечивает обратную связь в режиме реального времени для сварщиков.Отслеживание и понимание этих данных — ключевая часть улучшения времени дуги и производительности. Эти подробные данные также могут помочь производителям обучить новых сварщиков и ускорить их освоение.
Сварка старых времен | JLC Онлайн
В 1942 году компания Holmes Burton выпустила серию профессиональных фильмов «Работа вашей жизни», призванную познакомить студентов с различными профессиями и профессиями (видео ниже). Что классно в сериале, так это то, что он проливает свет на аспекты сделок, которые могли быть потеряны для истории, потому что никто не думал, что эту информацию стоит сохранять.
Эти фильмы не показывали студентам уже более 50 лет и сами могли быть потеряны для истории. И они были бы, если бы не стараниями архивариуса Рика Прелингера, который собирал эти и другие «эфемерные» (рекламные, образовательные, индустриальные и любительские) фильмы. Его коллекция стала известна как Архив Прелингера и теперь является частью Интернет-архива.
Как говорит один из обозревателей The Welding Operator:
В центре фильма — главный метод сварки современности — газовая кислородно-ацетиленовая сварка.Хотя сегодня это считается в значительной степени устаревшим для производственных работ, это хорошая съемка основ любого метода сварки. Фильм переходит к точечной сварке, затем приклеиванию, а затем к описанию различных применений этих методов. Интересна газовая сварка стального планера.
Зная о существовании сварки MIG и TIG на момент создания фильма, рецензент справедливо предполагает, что эти технологии, вероятно, были слишком передовыми, чтобы их можно было включить в обзор. Первоначально разработанная для сварки цветных металлов, дуговая сварка металлическим электродом в газе (такая как MIG и TIG) не получила широкого распространения в течение следующих 10–20 лет — после того, как эти методы были адаптированы для сварки стали.
Если вы интересуетесь сваркой, то вот подборка совершенно разных историй о сварке из Tools of the Trade: Thermite Welding Railroad Tracks
DeWalt Cordless Stick и TIG Welder
Cool Work Wheels: White Motor Company COE
Five Freaky Welding Videos
Традиционная сварка по сравнению с лазерной сваркой
Лазерная и традиционная сварка все еще конкурируют с
Вы можете подумать, что лазерная сварка быстро захватит сферу применения благодаря гораздо более высокой скорости обработки и более высокому качеству.Но традиционная сварка сохраняется. И в зависимости от того, кого вы спросите и какие приложения вы рассматриваете, он может никогда не исчезнуть. Итак, каковы плюсы и минусы каждого метода, которые продолжают приводить к смешанному рынку?
Линия Fusion Line от Trumpf оснащена лазером с проволокой для придания большей массы сварному шву, перекрывая зазоры шириной до 1 мм.Традиционные методы сварки остаются популярными. Вообще говоря, в промышленности используются три типа традиционной сварки: MIG (металлический инертный газ), TIG (вольфрамовый инертный газ) и точечная сварка.При контактной точечной сварке два электрода прижимают детали, которые необходимо соединить между собой, через это пятно пропускается большой ток, а электрическое сопротивление материала детали генерирует тепло, которое сваривает детали вместе. Это быстрый метод, и, по словам Эрика Миллера, менеджера по развитию лазерной группы Miller Electric Mfg LLC в Эпплтоне, штат Висконсин, это основной метод, используемый в автомобилестроении, особенно для кузовов. Но, добавил он, самый большой рынок для лазерной сварки — это замена точечной контактной сварки.И наоборот, Миллер не видел «какой-либо лавины» в использовании лазеров, заменяющих TIG или MIG. И даже в группе автоматизации компании около 90 процентов проектов выполняются в MIG.
Big на MIG
Чем объясняется непреходящая популярность MIG? «Расходный материал — это проволока с непрерывной подачей», — сказал Миллер. «Таким образом, он добавляет материал и усиливает сварной шов, что делает его идеальным для углового шва [в котором детали перпендикулярны]». Аутогенный лазер объединяет два основных материала вместе.По словам Миллера, лазер может выполнять угловой шов, но точность деталей и всего остального должна быть на порядок выше.
«При сварке MIG на угловом соединении допуск составляет не менее плюс-минус половина диаметра проволоки, а в целом даже больше», — сказал он. Точно так же технологическое окно MIG для других типов сварных швов намного больше, чем у лазера. Другими словами, детали не должны быть такими точными, а приспособления не должны обеспечивать почти идеальную посадку, как в случае с аутогенным лазером.
Темная область под сварным швом слева показывает глубокое проплавление и полное сплавление хорошего сварного шва MIG. На изображении справа показан лазерный сварной шов с полным сплавлением, но с очень неглубоким проплавлением, что уменьшает смешивание наполнителя и основы. СваркуMIG также проще автоматизировать. По словам Миллера, единственными факторами, которые вам нужно контролировать, являются скорость движения, напряжение, сила тока, угол резака и рабочий угол, и «если вы сделаете пять из десяти вещей правильно, вы все равно получите хороший сварной шов». Для автоматизации лазерной сварки требуется робот с превосходной точностью траектории и повторяемостью, а в процессе сварки нужно контролировать больше факторов.В этом отношении TIG аналогичен.
Нельзя сказать, что автоматизировать сварку MIG настолько просто, что это может сделать каждый. По-прежнему требуется эксперт для программирования и диагностики проблем. Эд Хансен, директор по глобальному управлению продуктами и гибкой автоматизации ESAB Welding & Cutting Products, Дентон, Техас, сказал, что это еще один плюс для MIG.
«После многих лет эмпирических и научных данных традиционная сварка стала хорошо изученной. Мы знаем, что нужно для того, чтобы получить предсказуемый результат, обеспечивающий соединение, требуемое для конструкции.И даже несмотря на то, что мы говорим о нехватке квалифицированной рабочей силы, что является реальной проблемой для отрасли, все еще существует большой пул опытных сварщиков, техников и инженеров, которые все знакомы с управлением этими традиционными процессами ». Для большинства продуктов это простое и недорогое решение, обеспечивающее приемлемые результаты.
Темная область под сварным швом слева показывает глубокое проплавление и полное сплавление хорошего сварного шва MIG. На изображении справа показан лазерный сварной шов с полным сплавлением, но с очень неглубоким проплавлением, что уменьшает смешивание наполнителя и основы.Дело в том, что первоначальная стоимость системы MIG или TIG меньше, чем стоимость лазерной системы. Однако стоимость лазеров снижается и будет продолжать снижаться. «Стоимость лазера составляет от трети до половины стоимости системы лазерной сварки, — сказал Хансен, — а стоимость в зависимости от возможностей сварки снижается на 10-15 процентов в год».
Миллер также отметил, что «лазерная технологическая головка дороже, чем традиционные головки, волокно доставки дороже, и защита лазерной ячейки также дороже.«Например, лазерная ячейка должна быть« светонепроницаемой »со стенками толщиной 4 дюйма (101,6 мм), чтобы выдерживать прямое попадание в течение 10 минут без прожига. (Лазер не будет в фокусе более 4 дюймов [101,6 мм]. ] на большую глубину.) Системы TIG и MIG могут быть экранированы недорогим листовым металлом, который оставляет зазоры.
С другой стороны, если учесть разницу в производительности и стоимости каждой детали, как мы увидим, часто выигрывает лазер. Это особенно верно для TIG, который является очень медленным процессом, требующим высокой квалификации, что делает его дорогостоящим в использовании.По этой причине Миллер сказал, что TIG в основном ограничивается производством промышленного пищевого оборудования и бытовой техники, а также некоторыми прецизионными компонентами. «Люди выбирают TIG для пищевого оборудования, потому что сварной шов не имеет пористой поверхности — он очень гладкий», — сказал он. Но если эти детали необходимо производить в больших объемах, рентабельность инвестиций в лазерную систему «взорвет двери» TIG, поэтому, естественно, в таких случаях она берет верх.
Масуд Харуни, менеджер по продукции по лазерной сварке Trumpf Inc., Хоффман Эстейтс, Иллинойс, сказал, что даже TIG не может обеспечить полностью удовлетворительную поверхность для пищевой промышленности и других приложений, где внешний вид имеет решающее значение.«Это не так плохо, как MIG, но поверхность TIG определенно требует шлифовки после обработки, в которой нет необходимости при использовании лазера», — сказал Харуни. «Кроме того, скорость лазерной сварки видимых швов в два-три раза выше, чем у TIG. Если вы видите хороший радиус на холодильнике или аналогичной детали, значит, он был отшлифован или сварен лазером ».
Последний голос за традиционную сварку: за исключением нескольких специализированных случаев, лазерная сварка должна быть автоматизирована из соображений безопасности. И это оставляет много работы сварщикам, как объяснил Хансен.«Робот не может взбираться на леса или залезать в трюм корабля. Мы можем мечтать о таких супер-роботах, но с практической точки зрения в ближайшем будущем их здесь не будет ».
Тенденции принятия лазерных решений
По мнению Миллера, производство в США обычно консервативно, и «если нет проблемы, которую нужно решить, будет выбрано самое дешевое, самое надежное и проверенное решение. Таким образом, люди начинают смотреть в сторону лазера только тогда, когда сварка MIG не работает или сварка TIG идет слишком медленно.”
Объемная сварка TIG либо уже переехала за границу, либо была заменена лазером, так где же лазер может бросить вызов MIG?
Одной из основных проблем является повреждение — металлургическое или конструктивное — потенциально вызванное относительно длительной и широко распространенной теплопередачей MIG в деталь с последующим длительным циклом охлаждения. И наоборот, лазер передает тепловую энергию очень маленьким лучом, плавя только локализованную область. Общее количество подводимого тепла намного меньше, чем при сварке MIG, и деталь остывает очень быстро, что сводит к минимуму деформацию и металлургические эффекты.
Харуни предложил полезную аналогию: «Представьте себе бутылку воды на песчаном пляже в сравнении с иглой. Если вы положите на бутылку пятифунтовую гирю, она не пробьет песок. Но если вы нанесете на иглу всего несколько унций, это произойдет. Думайте о весе, которое вы прикладываете, как о нагреве, о бутылке как о MIG, а об игле как о лазере ».
Хансен изESAB сказал, что лазер снижает тепловложение примерно на 85 процентов по сравнению с MIG, и «остаточное напряжение в сварном шве прямо пропорционально тепловложению.Чем больше тепла вы поместите в него, тем больше остаточного напряжения вы создадите. А это означает коробление, деформацию, усадку и все эти вещи, которые вызывают кошмар, когда вы берете эту деталь и делаете из нее сборку или вставляете ее в конструкцию или транспортное средство ».
Чем больше деталь, тем больше мелких индивидуальных остаточных напряжений становятся макро-прогибами, которые очень дорого исправить и которые позже трудно исправить, добавил он. И это главное соображение для клиентов, которые пытаются «облегчить» свои продукты.Более того, по его словам, «некоторые сплавы расслаиваются или изменяют свойства при нагревании, или структура зерен растет нежелательным образом. У многих из этих материалов зернистая структура и микроструктура отличаются, если сварной шов расплавить, а затем охладить ».
С расположенным на расстоянии источником тепла и высококонцентрированной областью расплава внизу лазерная сварка кажется волшебством, как показано здесь в системе Miller Electric.Миллер из Miller Electric отметил, что последнее поколение высокопрочных сталей «приобретает большую прочность благодаря сложным процессам термообработки.Когда вы расплавляете и затвердеваете при низкой скорости охлаждения (как при сварке MIG), все эти сильные стороны исчезают. Лазер может помочь сохранить исходную прочность материала ».
В другом примере Миллер сказал, что сварка титана методом MIG затруднена из-за «проблемы с плавающим катодом». Дуга нестабильна. Так что лазер — идеальный выбор ». Проблема с алюминием серии 6000 — образование горячих трещин. «Горячее растрескивание — это функция силицида магния, мигрирующего к границе зерен. Поэтому, если вы можете нагреть материал, расплавить его и охладить до того, как силицид магния переместится, тогда вы сможете создать сварной шов без трещин », — сказал он.«Лазер может сделать это, используя новейшие методы сканирования, при которых мы перемещаем луч вперед и назад с помощью зеркала».
Превосходная пропускная способностьLaser
С точки зрения Миллера, большинство применений лазера связано с трудносвариваемыми материалами. С точки зрения Харуни, лазер настолько быстрее, что даже проекты из листового металла переходят на лазер. Насколько быстрее? Харуни из Trumpf сказал, что сварка MIG обычно происходит со скоростью 20-30 дюймов (508-762 мм) в минуту — максимум 40 дюймов (1016 мм) в минуту.Лазер, по словам Харуни, может сваривать со скоростью почти 200 дюймов (508 см) в минуту, поэтому сам процесс соединения уже намного быстрее. Второе преимущество — сокращение постобработки. Харуни заметил, что если внешний вид сварного шва ухудшится. Важно то, что после сварки MIG вам потребуется длительный цикл шлифовки, в котором нет необходимости после лазерной сварки.
«Вот почему, — добавил он, — обычно случается, что деталь, изготовленная с помощью сварки MIG по цене 25 долларов, будет стоить всего 15 долларов за лазерную сварку, даже с учетом более высоких первоначальных вложений в лазерную сварку.Например, Харуни рассказал о недавнем проекте, в котором Трампф сократил время цикла сварки большой двери с десяти часов до 35 минут. Другой заказчик столкнулся с трудностями при сварке MIG алюминиевого электрического корпуса. Пузыри были частой проблемой, и общее время цикла составляло четыре часа. Харуни сказал, что Trumpf сократил это время до 18 минут с помощью лазерной сварки.
Хансен добавил, что способность лазера глубоко проникать в материал многократно увеличивает его преимущество перед традиционной сваркой. Поскольку лазер не только в три-десять раз быстрее, чем MIG (и даже быстрее по сравнению с TIG), он может сваривать относительно толстые швы, которые потребуют нескольких проходов с помощью MIG или TIG.
«Традиционные методы также требуют очистки и шлифования между проходами, что еще больше увеличивает общее время цикла», — пояснил Хансен. «Лазер может выполнять однопроходную сварку примерно на полдюйма по сравнению с примерно пятью проходами для сварки MIG, в зависимости от используемого процессора. Более полдюйма для лазерной сварки потребовалось бы заранее вырезать или отшлифовать скос до края, но это гораздо меньший скос, чем все скосы стыка, необходимые для сварки MIG ».
Таким образом, для материала толщиной в полдюйма лазерная сварка будет в 15-50 раз быстрее, чем MIG, только по скорости сварки — и даже быстрее, если учесть дополнительную постобработку, необходимую для MIG.
Сравнение методов: несварное соединение внизу, сварка MAG чуть выше, сварка Trumpf Fusion Line (которая сочетает в себе проволоку и лазер) выше, и вверху автогенная лазерная сварка после перепроектирования соединения для этого процесса.Конечно, при такой высокой производительности вам потребуется много сварочных работ, чтобы обеспечить питание лазерной системы и максимизировать рентабельность инвестиций. По словам Хансена, «обычно лазер может производить от трех до пяти систем дуговой сварки, например, при сварке листов. Чтобы запитать пять систем дополнительной дуги, потребуется много работы.”
Новые технологии в сочетании со старыми
Поскольку для автогенной лазерной сварки требуется плотная посадка между соединяемыми деталями, во многих случаях лучше всего изменить расположение стыков, чтобы представить лазеру перекрывающиеся поверхности (чтобы использовать его прокалывающую способность). Все больше производителей готовы вкладывать средства в более совершенные процессы и инструменты для разведки и добычи, чтобы воспользоваться преимуществами более высокой производительности лазера.
Но для тех, кто сопротивляется таким изменениям или в ситуациях, когда промежутки неизбежны, существуют гибридные системы, сочетающие в себе технологию лазера и подачи проволоки, а также другие новые разработки, расширяющие область применения лазера.Одна простая концепция (упомянутая ранее в связи с решением проблемы горячего растрескивания) — это раскачивание лазерного пятна. Миллер сказал, что это старая концепция, которая в последнее время стала намного более экономичной. Он предложил пример перемещения пятна диаметром 1,2 мм вперед и назад по площади 3 мм с высокой скоростью, эффективно захватывая большую площадь и при этом обеспечивая хороший сварной шов.
Хансен сказал, что гибридные системы сочетают в себе процесс MIG и лазерный луч. «Мы действительно используем лазер для проникновения.Обычно, если вы хотите повлиять на проплавление сварного шва MIG, вам необходимо увеличить силу тока. Используя лазер для проплавления, мы можем уменьшить силу тока на MIG и использовать сварной шов наименьшего диаметра, который позволяет наша конструкция для инженерных целей. Таким образом, лазер позволяет нам оптимизировать MIG ». Также существует синергия между процессами благодаря стабилизации дуги лазерным лучом. «Мы можем путешествовать по дуге намного быстрее, чем если бы у нас не было лазерного луча. Вот почему мы можем так быстро реализовать гибридный процесс », — сказал он.
Комплект больших шестиосных лазерных порталов ESAB для сварки пассажирских вагонов. Линия Fusion LineTrumpf, которую Харуни описал как «технологический лазер с добавлением проволоки для увеличения массы зазоров», может перекрывать зазоры шириной до 1 мм.
Со своей стороны, ЭСАБ разработал адаптивную технологию сварки, которая определяет состояние деталей и изменяет параметры процесса в соответствии с ними. В системе используется камера, которая «рисует лазерную полосу на детали, а затем смотрит на нее под углом параллакса, чтобы увидеть форму сустава, примерно на 20-40 мм впереди процесса», — сказал Хансен.Лазерная когерентная визуализация используется для измерения замочной скважины, прорезаемой лазером в металле. «Мы можем измерить глубину проникновения и форму замочной скважины и использовать эту информацию либо в качестве меры качества, либо в замкнутом контуре для управления процессом», — сказал он.
Система автоматически регулирует проникновение лазера, мощность лазера, параметры газовой металлической дуги, скорость подачи проволоки, напряжение, поток газа и скорость перемещения по мере того, как сварочная головка обрабатывает деталь. Гол, которым руководил У.Требования S. Navy заключаются в том, чтобы обеспечить преимущества лазерной сварки с низким тепловложением для «деталей, приготовленных традиционным способом» (то есть деталей, которые не были обработаны с жесткими допусками для стандартной лазерной сварки). Хансен сообщил, что это расширяет технологическое окно для гибридной сварки в пять раз по сравнению с тем, что было бы возможно при установившемся контроле.
Лазерная сварка остается относительно новой для многих пользователей, и Харуни подчеркнул приверженность Trumpf обучению и поддержке с самого начала, а также преимущества автономного программирования их систем после установки.
Trumpf также предлагает TeachLine, новую сенсорную систему на основе камеры, которая определяет местоположение свариваемого шва. «Заказчики не хотят прерывать производство, чтобы запрограммировать новую деталь или вносить изменения в свое программирование, поэтому они могут использовать это автономное программирование и загрузить деталь, запрограммировать ее и доставить в ячейку. С TeachLine им не нужно настраивать его. TeachLine увидит деталь и откорректирует созданную вами программу в автономном режиме. Комбинация автономного программирования и TeachLine помогает нашим клиентам быстро вносить изменения в производство.”
ESAB также внедряет новый пакет «цифровых решений», который объединяет огромное количество информации, охватывающей весь процесс сварки, включая присадочный материал, основной материал и газ, чтобы упростить использование систем. Как сказал Хансен: «Сложную систему легко создать. Очень сложно сделать сложную систему простой. И вот к чему мы идем с нашими цифровыми решениями. Мы используем наши знания о процессе, чтобы принимать разумные решения по управлению процессом, чтобы оператору не нужно было быть таким же опытным или знающим, как в прошлом.”
ЭСАБ также работает над тем, чтобы сделать свое оборудование способным оценивать качество производимого сварного шва и, в идеале, предотвратить возникновение дефектов или разрывов.
Наконец, традиционная сварка также претерпела улучшения, такие как усовершенствованные формы волны и концепция ActiveWire Miller Electric, которая непрерывно подает проволоку MIG вперед и назад, чтобы уменьшить разбрызгивание и тепловложение. Такой подход расширяет возможности автоматизации сварки MIG и делает MIG жизнеспособным решением даже для сварки некоторых сверхтонких материалов.
(PDF) Влияние времени сварки и сварочных токов на сварной шов и свойства растяжения тонкого алюминия A1100 при микро- контактной точечной сварке
VOL. 11, № 2, ЯНВАРЬ 2016 ISSN 1819-6608
ARPN Журнал инженерных и прикладных наук
© 2006-2016 Asian Research Publishing Network (ARPN). Все права защищены.
www.arpnjournals.com
1050
ВЛИЯНИЕ ВРЕМЕНИ СВАРКИ И СВАРОЧНЫХ ТОКОВ НА
СВАРОЧНЫЙ НАГНЕТ И СВОЙСТВА НА РАСТЯЖЕНИЕ ТОНКОГО АЛЮМИНИЯ
A1100 WASK5000 WINDOWS
A11OROZOK A11OROZOK 9D2000 MUROZOK 9D2000 от
1Механический факультет инженерного факультета Университета Индонезии, Депок, Индонезия
2Металлургический факультет и инженерный факультет Университета Индонезии, Депок, Индонезия
Электронная почта: ario @ eng.ui.ac.id
РЕФЕРАТ
В этой статье процесс контактной точечной сварки был применен к тонкому алюминию A1100, используемому для
, при исследовании процесса микросоединения. Параметры точечной сварки сопротивлением, такие как форма электрода, материал электрода, напряжение
и сила электрода, оставались постоянными. В этом эксперименте используются различное время сварки и сварочный ток, чтобы
определить оптимальные параметры сварки для максимальной прочности соединения.В данной работе исследуются характеристики сопротивления
, сваренного точечной сваркой тонкого листа алюминия A1100 толщиной 0,4 мм. Материал был вырезан по стандарту ANSI / AWS
размером. Производительность измеряется испытанием на сдвиг при растяжении и испытанием микроструктуры. Испытание на растяжение проводилось в технологическом центре полимеров
BPPT (исследовательский центр Индонезии). Толщина образца 0,4 мм. Он имеет
, теплопроводность 222 Вт / м-К, температура плавления 643-657.2 ° C, солидус 643 ° C и ликвидус 657,2 ° C. Влияние сварочного тока и времени сварки
обеспечит лучшие характеристики, такие как сварка самородком и свойства при растяжении. Время сварки
и сварочный ток дают квадрат размера зоны самородка или отверстия в образце. Исходя из результатов, максимальная нагрузка
образца 272N может быть достигнута с параметрами сварки: время выдержки 10 секунд, время цикла 1 и сварочный ток
2 кА.Этот результат сварки имеет размер ядра 292,1 мм2 и размер трещины 107,85 мм2. Этот эксперимент
показывает оптимальные параметры сварки, которые можно использовать при микросоединении (тонкая пластина).
Ключевые слова: влияние времени сварки и сварочных токов, зона расплава, точечная микрокомпонентная сварка, алюминий А1100.
ВВЕДЕНИЕ
Сварка — важная технология соединения материалов
, которая использовалась в крупном производстве
отраслей [1, 2].Тенденция создания более сложных и сложных микросистем
требует миниатюрности, высокой точности
и высокого качества [3]. Для соединения тонких листов толщиной менее
1 мм используется микросварка [4]. Эта последняя проблема является основной проблемой
в области контактной точечной сварки [5]. Сообщается, что контактная точечная сварка
является сегодня промышленным стандартом, а
— ведущим процессом соединения в автомобильных сборках. Арио.
с.B. et al. В [6] были изучены зажимные приспособления и методы соединения, оптимальные параметры
и их влияние на качество
сварных швов, качество поверхности и стабильность результатов сварки.
Влияние сварки током на микроструктуры было
очень незначительным, в то время как размер слитка сильно зависел от сварочного тока
[7]. Величины радиальных остаточных напряжений
во внутренней и внешней областях сварочного стержня
будут расти с увеличением времени сварки и тока
, при небольшом уменьшении в краевых областях
сварочного стержня [9] .Для анализа остаточных напряжений использовался основной материал (BM), зона плавления
(FZ) и зона термического влияния (HAZ) сварного соединения пятна сопротивления
.
Зона расплава (сварочный шар) и область преобразования тепла
являются ЗТВ при контактной точечной сварке.
ЗТВ контактной точечной сварки изучали
авторов, влияние сварочного тока на диаметр и несущую способность самородка
оценивали с помощью
, наблюдая за диаметром самородка и выполняя испытание на сдвиг при растяжении —
.Отожженный Gal с двойной фазой 780 МПа и стальной лист с борсодержащим покрытием Al-
(22MnB5) были использованы Hong-
Seok Choi и др. [10] в качестве материала объекта. Daniel, K. и др.
[2] изучали влияние сварочных токов на размер сварных швов
диаметром, несущую способность и энергию разрушения
сварных материалов, в этом исследовании использовалась аустенитная нержавеющая сталь AISI 316L
в качестве материал объекта. M. H.
Razmpoosh и др. [11] изучали эволюцию микроструктуры
и механические свойства, которые наблюдались в зоне плавления
, ЗТВ, усадочных полостях.В их исследованиях используется сталь Fe-31Mn-3Al-
3Si TWIP. A. S. Baskoro и
и др. [12] изучали время сварки и сварочный ток до размера сварных швов
и испытание на сдвиг при растяжении. Материалом в этом исследовании
является холоднокатаный стальной лист.
Исследования контактной точечной сварки
были проведены исследователями именно в отношении влияния сварочного
времени и сварочного тока на сварочный стержень и механические свойства
с различными материалами и размерами.
Тенденция к продукту ведет к более сложной и изощренной микросистеме
, соединение для создания продуктов micro
необходимо в отраслях. Для соединения тонких листов
толщиной менее 1 мм используется микросварка [4]. Проблема
в этом случае заключается в влиянии времени сварки и тока
на сварочный стержень (зона расплава) и свойства при растяжении
тонкого алюминия A1100 при микро-
точечной сварке сопротивлением.Подвод тепла является важным фактором в процессе сварки
, и некоторые параметры влияют на ввод тепла
в методе точечной сварки сопротивлением, некоторые параметры
— это сварочный ток (I), сопротивление (R) и время сварки
. (t) [12] уравнение, показанное в уравнении 1.
Точечная контактная сварка осуществлялась сваркой
Уравнения и расчеты, относящиеся к контактной сварке
Это некоторые из основных расчетов, с которыми вам следует ознакомиться, если вы покупаете оборудование или изучаете процесс контактной сварки.
Расчет времени
Сварочные циклы
Первые аппараты для контактной сварки были привязаны к промышленной частоте источника питания машины. По этой причине вы по-прежнему будете видеть Weld Cycles довольно часто в документации по контактной сварке. В Северной Америке частота сети составляет 60 Гц. Во многих других частях света рабочая частота составляет 50 Гц.
Карта мира, показывающая частоту электросети общего пользования с разбивкой по странам. Не все окрашенные области имеют доступ к электросети.В Японии используются как 50 Гц, так и 60 Гц.
Однофазные машины переменного тока все еще подсчитывают количество циклов сетевой частоты, чтобы контролировать время сварки. Инверторы (иногда называемые среднечастотными сварочными аппаратами постоянного тока [MFDC]) часто имеют частоту 1000 Гц, что упрощает расчет времени.
Время сварки (в миллисекундах) = количество циклов сварки / частота электросети
В Северной Америке при 60 Гц:
Время сварки (в миллисекундах) = количество циклов / 60
пример
15 циклов времени сварки
Время сварки (в миллисекундах) = 15/60 = 0.250 секунд (или 250 миллисекунд [мс])
В Англии и Европе, Китае и большинстве других мест в мире с частотой 50 Гц:
Время сварки (в миллисекундах) = количество циклов / 50
пример
15 циклов времени сварки
Время сварки (в миллисекундах) = 15 / 50 = 0,300 секунды (или 300 миллисекунд [мс])
Рабочий цикл
Рабочий циклиспользуется для математического снижения сварочного трансформатора. Сварщики сопротивлением очень редко работают при 100% рабочем цикле (что приравнивается к постоянному включению, как лампочка).Часто они включаются только на непродолжительное время. Если бы все аппараты для контактной сварки были рассчитаны на 100% -ный рабочий цикл, все они были бы огромными и очень дорогими. Таким образом, рабочий цикл можно использовать, чтобы сделать оборудование более подходящим для повседневной «нормальной» работы.
Следует проявлять осторожность при покупке сварщика, так как расчет рабочего цикла может быть изменен, чтобы заставить оборудование звучать более мощно, чем другое оборудование. См. Диаграммы ниже в разделе «КВА в зависимости от рабочего цикла». «50 кВА» — это не всегда сравнение яблок с яблоками.
В Северной Америке обычно принято оценивать сварочные трансформаторы на уровне 50%. На некотором импортном оборудовании вы увидите рейтинг рабочего цикла 20%. Можно найти трансформаторы с рейтингом от 4%. (Трансформатор с номиналом 0% означает, что вы никогда не сможете его использовать.)
Рабочий цикл = (время сварки) / (прошедшее время)
Истекшее время часто рассчитывается с использованием 2 секунд, но также может быть рассчитано за одну минуту
пример (1 минута)
в среднем 4 сварных шва в минуту при времени сварки 15 циклов (250 мс) в Северной Америке
Рабочий цикл = (4 сварных шва X 0.250 с) / 60 с = 0,01667 = 1,67% рабочего цикла
пример (2 секунды)
в среднем 1 сварка за 2 секунды при времени сварки 15 циклов (250 мс) в Северной Америке
Рабочий цикл = (1 сварка X 0,250 с) / 2 секунды = 0,125 = рабочий цикл 12,5%
Трансформатор кВА
Расчет однофазного тока в кВА
S (кВА) = I (A) x V (RMS) / 1000
S (кВА) = полная мощность в кВА
I (A) = ток в амперах
В (RMS) = действующее напряжение
пример
I (A) = 153 A
V (RMS) = 460 V
S (kVA) = 70 kVA
Расчет трех (3) фазных ампер на кВА
S (кВА) = sqrt (3) x I (A) x V (RMS) / 1000
S (кВА) = полная мощность в кВА
I (A) = ток в амперах
В (RMS) = действующее напряжение
пример
I (A) = 153 A
V (RMS) = 460 V
S (kVA) = 122 kVA
кВА в зависимости от рабочего цикла
Px = Pmax X sqrt (Dc)
Px = кВА (нагрузка x%)
Pmax = кВА (нагрузка 100%)
Dc = рабочий цикл (пример: 30% = 0.30)
пример
Dc = 0,5
Pmax = 100 кВА
Px = 70,7 кВА
пример
Dc = 0,5
Px = 100 кВА
Pmax = 141,4 кВА
Передаточное число
Коэффициентвитков — это просто отношение входного напряжения / силы тока к выходному напряжению / силе тока.
Мощность трансформатора должна быть примерно такой же, как на входе, так и на выходе. Следовательно:
Power (in) = Power (out)
and
Power (Watts) = Volts X Amps
Volts (in) X Amps (in) = Volts (out) X Amps (out)
Volts (in) / Amps (выход) = Вольт (выход) / Ампер (вход)
Школа подготовки сварщиков | Классы сварки
1) UTI является образовательным учреждением и не может гарантировать работу или заработную плату.
2) Для получения информации о результатах программы и другой информации посетите сайт www.uti.edu/disclosures.
5) Программы UTI готовят выпускников к карьере в различных отраслях промышленности с использованием предоставленного обучения, в первую очередь, для специалистов по автомобилям, дизельным двигателям, ремонту после столкновений, мотоциклетным и морским техникам. Некоторые выпускники UTI устраиваются на работу в рамках своей области обучения на должности, отличные от в качестве технического специалиста, например: специалист по запчастям, специалист по обслуживанию, изготовитель, лакокрасочный отдел и владелец / оператор магазина.
10) Финансовая помощь, стипендии и гранты доступны тем, кто соответствует требованиям.Награды различаются в зависимости от конкретных условий, критериев и состояния.
26) Расчетная годовая средняя заработная плата сварщиков, резчиков, паяльщиков и брейзеров в Профессиональной занятости и заработной плате Бюро статистики труда США, май 2020 г. UTI является образовательным учреждением и не может гарантировать трудоустройство или заработную плату. Достижения выпускников UTI могут быть разными. Индивидуальные обстоятельства и заработная плата зависят от личных качеств и экономических факторов. Опыт работы, отраслевые сертификаты, местонахождение работодателя и его программы компенсации влияют на заработную плату.Заработная плата начального уровня может быть ниже. Программы UTI готовят выпускников к карьере в отраслях промышленности с использованием предоставленного обучения, в первую очередь в качестве техников-сварщиков. Некоторые выпускники UTI устраиваются на работу в рамках своей области обучения на должности, отличные от технических, например, сертифицированный инспектор или специалист по контролю качества. Информация о заработной плате в штате Массачусетс: средний годовой диапазон заработной платы начального уровня для лиц, занятых сварщиками, резчиками, паяльщиками и брейзерами в Содружестве Массачусетса (51-4121), составляет от 34 399 до 48 009 долларов США (Massachusetts Labor and Workforce Development, May Данные за 2019 г., просмотренные 2 июня 2021 г., https: // lmi.dua.eol.mass.gov/lmi/OccupationalEmploymentAndWageSpecificOccupations#). Информация о зарплате в Северной Каролине: по оценке Министерства труда США почасовая оплата в среднем 50% для квалифицированных сварщиков в Северной Каролине, опубликованная в мае 2021 года, составляет 20,28 доллара США. Бюро статистики труда не публикует данные о заработной плате начального уровня. Однако 25-й и 10-й процентили почасовой оплаты труда в Северной Каролине составляют 16,97 и 14,24 доллара соответственно. (Бюро статистики труда Министерства труда, занятости и заработной платы США, май 2020 г.)Сварщики, резаки, паяльщики и паяльщики, просмотр на 2 июня 2021 г.)
42) Для сварщиков, резчиков, паяльщиков и паяльщиков Бюро статистики труда США прогнозирует в среднем 43 400 вакансий в год в период с 2019 по 2029 год. вакансии включают вакансии, связанные с чистыми изменениями занятости и чистыми замещениями. См. Таблицу 1.10. Временные увольнения и вакансии, прогнозируемые на 2019–29 годы, Бюро статистики труда США, www.bls.gov, дата просмотра 3 июня 2021 г. UTI является образовательным учреждением и не может гарантировать работу или заработную плату.
50) Бюро статистики труда США прогнозирует, что общая занятость сварщиков, резчиков, паяльщиков и брейзеров в стране к 2029 году составит 452 500 человек.