Самодельный полуавтомат сварочный своими руками: схема, как правильно использовать
Сварочный полуавтомат может быть самодельным, сделанным из инвертора. Сразу скажем, что смастерить сварочный полуавтомат из инвертора своими руками непросто, но не невозможно. Тому, кто задумал смастерить полуавтомат своими руками из инвертора, следует изучить принцип его работы, посмотреть при необходимости видео или фото, посвященные данной теме, подготовить необходимые комплектующие и оборудование.
Как инвертор переделать в полуавтомат
Для работы понадобится:
- Инверторный аппарат, который может сформировать сварочный ток в 150 А.
- Механизм, подающий для полуавтомата (сварочную проволоку).
- Горелка.
- Шланг, через который идет сварочная проволока.
- Шланг для подачи в зону сварки защитного газа.
- Катушка со сварочной проволокой (потребуются некоторые переделки).
- Электронный блок управления.
Схема сварочного полуавтомата
Особое внимание уделяется переделке подающего устройства, подающего в зону сварки проволоку, которая передвигается по гибкому шлангу. Для получения качественного аккуратного сварного шва скорость подачи проволоки по гибкому шлангу и скорость ее расплавления должны соответствовать.
При сварке полуавтоматом используется проволока разного диаметра и из разных материалов, поэтому должна быть возможность регулирования скорости ее подачи. Этим занимается подающий механизм.
Наиболее распространенные диаметры проволоки в нашем случае: 0,8; 1; 1,2 и 1,6 мм. Перед сваркой проволока наматывается на катушки, являющиеся приставками, закрепляемыми нехитрыми крепежными элементами. Проволока в процессе сварки подается автоматически, благодаря чему значительно сокращается время технологической операции и повышается эффективность.
Главный элемент электронной схемы блока управления — это микроконтроллер, отвечающий за стабилизацию и регулирование сварочного тока. От этого элемента зависят параметры тока и возможность регулирования их.
Переделываем инверторный трансформатор
Полуавтомат сварочный своими руками сделать можно путем переделки трансформатора инвертора. Для приведения характеристик инверторного трансформатора в соответствии с необходимыми, он обматывается медной полосой, обматывающейся термобумагой. Обыкновенный толстый провод для этих целей не используется, потому что он будет сильно нагреваться.
Вторичная обмотка тоже переделывается. Для этого нужно:
- Намотать обмотку из трех слоев жести, из которых каждый изолируется фторопластовой лентой.
- Концы обмоток спаять друг с другом для повышения проводимости токов.
В конструктивной схеме инвертора, используемого для включения в полуавтомат, должен быть предусмотрен вентилятор для охлаждения аппарата.
Настройка
При изготовлении полуавтомата из инвертора предварительно обесточьте оборудование. Для предотвращения перегрева устройства разместите его входной и выходной выпрямители, а также силовые ключи на радиаторах.
По выполнении вышеперечисленных процедур соедините силовую часть с блоком управления и подключите его к электросети. Когда загорится индикатор подключения к сети, подключите к выходам инвертора осциллограф. С помощью осциллографа найдите электрические импульсы в 40−50 кГц. Между формированием импульсов должно проходить 1,5 мкс, и регулируется это изменением величины напряжения, поступающего на вход.
Осциллограмма сварочного тока и напряжения: на обратной полярности — слева, на прямой полярности — справа
Проверьте, чтоб импульсы, которые отражаются на экране осциллографа, были прямоугольными, а фронт их составлял не больше 500 нс. Если проверяемые параметры такие как должны быть, подключите инвертор к электросети.
Ток, который поступает от выхода, должен быть не меньше 120А. Если эта величина меньше, вероятно, что в провода оборудования идет напряжение, не превышающее 100 В. В таком случае оборудование тестируется изменением силы тока (плюс постоянно контролируется напряжение на конденсаторе). Также постоянно контролируется температура внутри устройства.
После тестирования проверьте аппарат под нагрузкой: подключите к сварочным проводам реостат сопротивлением не менее 0,5 Ом. Он должен выдержать ток в 60 А. Сила тока, поступающего на сварочную горелку, контролируется амперметром. Если она не соответствует требуемому значению, величину сопротивления подбирают эмпирически.
Использование
После запуска аппарата индикатор инвертора должен высветить значение силы тока — 120 А. Если значение иное, что-то сделано неверно.
Контроль правильности работы
Чтобы полуавтомат прослужил длительный срок, рекомендуется все время контролировать температурный режим работы инвертора. С целью контроля одновременно нажимаются две кнопки, а после температура самого горячего из радиаторов инвертора выведется на индикатор. Нормальная рабочая температура — не больше 75 ° C .
Если будет больше, кроме информации, которая выводится на индикатор, инвертор будет издавать прерывистый звук, что сразу должно насторожить. При этом (или при замыкании термодатчика) электронная схема автоматически уменьшит рабочий ток до 20А, а звуковой сигнал идти будет, пока оборудование не придет в норму. О неисправности оборудования может говорить и код ошибки (Err), который высвечивается на индикаторе инвертора.
Когда используется полуавтомат сварочный
Схема самодельного сварочного полуавтомата. | Самодельные сварочные аппараты, полуавтоматы, схемы
Представляем вам схему самодельного сварочного аппарата, собранного в домашних условиях и показавшего не плохие результаты.Данная схема работает в ручном режиме сварки и автоматическом (точеном), то есть можно варить точками.
Перебрав много схем сварочных аппаратов мы пришли к выводу, что сварочный полуавтомат должен работать следующим образом:
- при нажатии кнопки управления сначала должен податься углекислый газ, это делается для того, что бы горелка наполнилась газом.
- после задержки 1..3 секунды автоматически включается ток сварки и подача проволоки.
- после отпускания кнопки управления отключается подача проволоки.
- затем через 1…3 сек отключается подача углекислого газа, это нужно для того, что бы расславленный метал не окислился при остывании, и отключается сварочный ток.
В результате такой работы сварочного полуавтомата шов получается качественный.
Исходя из этих требований нами была разработана схема сварочного полуавтомата, представленная на рисунке.
Схема работает следующим образом:1. Ручной режим.Переключатель SB1 в замкнутом состоянии.
При нажатии кнопки управления SA1 срабатывает реле К2, своими контактами К 2.1, К 2.2, К 2.3 включает реле К1 и К3.
Реле К1 контактами К1.1 включает подачу углекислого газа, К1.2 включает цепь питания электродвигателя, К1.3 отключает тормоз двигателя.
В это же время реле К3 своими контактами К3. 1 отключает цепь питания двигателя и К3.2 отключает реле К5, которое отвечает за включение тока сварки, на время заданное резистором R2 (1…3 сек).
На данном этапе подается газ, двигатель подачи проволоки и ток сварки отключены.
Далее.. после разряда конденсатора С2 через цепь резистора R2 отключается реле К3 и своими контактами К3.1 включает двигатель подачи проволоки и контактами К3.2 включает реле К5, которое своими контактами К5.1 включает ток сварки.
В это время идет процесс сварки.
Далее.. При отпускании кнопки управления SA1 реле К2 отключается, своими контактами К 2.1, К 2.2 отключает реле К1.
Реле К1 контактами К1.2 отключает двигатель подачи проволоки, контактами К1.3 включает тормоз двигателя (так как любой двигатель имеет инертность — это необходимо, что бы после окончания сварки сварочная проволока моментально останавливалась), контакты К1.1 размыкают цепь питания конденсатора С3.
На данном сварка прекращена, двигатель подачи проволоки остановлен, ток сварки включен и подача углекислого газа продолжается.
Далее.. после разряда конденсатора С3 через резистор R3 (1…3 сек) отключается реле К4 отвечающее за подачу газа и реле К5 отвечающее за включение тока сварки.
2. Автоматический режим.Переключатель SB1 в разомкнутом состоянии.
При нажатии кнопки управления SA1 все процессы в схеме происходят, так же как и в ручном режиме, только время сварки задается не удержанием кнопки управления SA1, а цепочкой С1R1 (1…10 сек).
Для чего нужен автоматический режим? Представьте, что нужно приварить крыло автомобиля. Если использовать ручной режим, то сварные швы по размеру будут разными и придется долго выравнивать все неровности.
Другое дело это автоматический режим, вам нужно будет настроить время сварки и силу тока, попробовать на какой нибудь опытной детали и можно варить не задумываясь о времени сварки. В этом случае все сварные швы будут одинаковые (точки).
Работает все просто, нажимаете на кнопку управления, держите ее и варите, схема после определенного времени, заданного резистором R1 отключит процесс сварки.
В аппарате можно использовать любые реле на ток коммутации (К1 и К3) — 5..10А, остальные реле (К2, К4, К5) — 400 мА.
Все элементы схемы не критичны, вместо силовых диодов можно использовать любые на ток 200 А, Тиристор управления сварочным током тоже любой на ток 200 А.
Для сглаживания пульсации и уменьшения брызг во время сварки нужно использовать сглаживающий дроссель L1. ( сварочный дроссель ) В качестве магнитопровода сварочного дросселя использован сердечник от лампового телевизора. В зазоры магнитопровода вставлены пластины из текстолита толщиной 2 мм. Способ намотки сварочного дросселя показан на рисунке.
Сварочный трансформатор мощностью 3 кВт намотан на кольцевом магнитопроводе и имеет следующие характеристики:Сначала наматывается первичная обмотка трансформатора, делаются отводы начиная с напряжения 160 в, далее 170 в, 180 в , 190 в, 200 в, 210 в, 220, в, 230 в, 240 в. проводом из меди сечением 5 мм. кв.
Вторичная обмотка наматывается по верх первичной проводом из меди сечением 20 мм. кв. Номинальное напряжение обмотки 20 вольт.
Таким образом мы имеем сварочный трансформатор с жесткой характеристикой (что очень важно для сварочного полуавтомата) и имеем 6 ступеней регулирования сварочного тока в форсированном режиме, 1 ступень нормальной работы трансформатора (220 в. превичная, 20 вольт вторичная) и 2 ступени пассивного режима работы трансформатора.
Ступени регулирования тока вторичной обмотки:
17 в, 19 в, 20 в, 22 в, 23 в, 24 в, 25 в, 27 в, 28 вольт.
Двигатель подачи сварочной проволоки можно использовать любой редуктор стеклоочистителя автомобиля например от ВАЗ 2110.
Важно отметить, при проектировании протяжного механизма нужно учитывать, что максимальная скорость протяжки проволоки должна обеспечиваться на уровне 11 метров в минуту, минимальная 0.7 метра в минуту. Для этого нужно рассчитать диаметр ведущего колеса механизма подачи проволоки.
Клапан газа можно использовать от клапана подачи воды от омывателя заднего стекла автомобиля ВАЗ 2109. Другие типы клапанов автомобилей использовать не рекомендуется, например воздушный от ВАЗ 2105, так как после некоторого времени работы они начинают пропускать (нарушается герметичность клапана).
Данный полуавтомат сварка работает уже 3 года, зарекомендовал себя очень надежным.
Ответы на комментарии:
Топология печатной платы, не хотел выкладывать из за того что ни чего не понятно.. но заставили..
В качестве реле К1, К2, К3 можно использовать реле типа HJQ-22F-3Z с тремя группами контактов.
На фото такое же реле, только с четырьмя группами контактов HJQ-22F-4Z (показываю как выглядит).
Так как сам сварочный полуавтомат был утрачен, то по моей просьбе фото этого сварочного аппарата были любезно предоставлены посетителем сайта Андреем, который повторил эту схему.
Большое спасибо ему за это.
Внешний вид полуавтомата:
Компоновка, вид сверху:
Компоновка, вид сбоку:
Компоновка, вид сбоку, вид подающего механизма:
Протяжный механизм:
Плата управления сварочным полуавтоматом:
Диодный мост, дроссель, трансформатор питания схемы управления:
Автор фото полуавтомата: Андрей.
Фото блока управления и печатная плата присланная посетителем сайта Николаем (комментарий 100)
Печатную плату в формате программы Sprint-layout 5 можно скачать по этой ссылке:
Печатная плата345
Если возникнут вопросы, задавайте их в комментариях.
Автор статьи: Admin Svapka.Ru
Понравилась ли вам статья? Если не трудно, то проголосуйте пожалуйста:Похожие записи
Самодельный сварочный полуавтомат | Сварка своими руками
Сэкономить на приобретении сварочного полуавтомата возможно, если собрать его самостоятельно. При этом можно получить высококачественную сварку для ответственных конструкций, например, автомобиля, которая ни в чем не будет уступать дорогому аппарату, купленному в магазине. Сварочным оборудованием собранным своими руками, доступно выполнение качественной сварки и получение прочных соединений.
Вариант полуавтомата №1 «Собрать с нуля»
Схема приведенная ниже проверена, по ней собраны и успешно работают несколько сварочных аппаратов, которые жужжат бесперебойно уже не один год. Варить можно как с углекислотой, так и без.
Приведенная схема упрощена специально, чтобы со сборкой мог справится даже новичек, не владеющий особыми знаниями.
Силовой трансформатор Tr1 намотан на лабораторный автотрансформатор на 10А. Первичную обмотку транса оставляем без изменений, но выводы для регулировки тока расположены через пятнадцать витков. Вторичная состоит из двух обмоток по тридцать витков
Транс Tr2 подберите какой найдете на 13В, трехамперный.
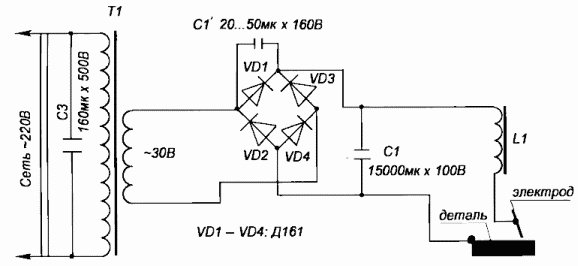
Движок М2 –для подачи элетрода-проволоки можно взять от дворников старого автомобиля.
Движок М1 –вентилятор от системного блока (компа) – система охлаждения .
R4 – регулятор движения проволоки.
Релюшку включения силового трансформатора можно не устанавливать, так же можно обойтись без реле тормозной системы двигателя подачи.
Вариант №2. Берем за основу сварочник ММА.
За основу в самодельном полуавтомате можно взять обыкновенный инвертор постоянного тока для бытовых работ, который стоит не дорого. К примеру, инвертор MINIONE подойдет для этих целей.
Avrora Minione 1600
К минивану нужно собрать выпрямитель, который состоит из мощных диодов, дросселя и мощного, емкостью примерно 50мкФ, конденсатора. Приобрести шлаг, протяжный механизм, который продается отдельно. В качестве тормоза для катушки с присадочным материалом можно взять обычную резинку со старого магнитофона (если еще есть такой в хозяйстве). Он необходим для того, чтобы когда подача останавливается, катушка не продолжала свое вращение самостоятельно.
сварочная проволока 08Г2С
Для питания регулятора подачи проволоки можно использовать схему, которая состоит из автомобильных реле, блока питания на 12В, используемого для потолочного освещения, выпрямителя постоянного тока (блока диодов). Регулятор подключается к электродвигателю, который вращает катушку. Всю конструкцию можно закрепить в металлическом каркасе и варить с удовольствием! Огромный плюс еще и в том, что инвертор, который используется как база для самодельного полуавтомата можно всегда снять и использовать как обычную ММА-сварку.
Сварочный полуавтомат своими руками
Как сделать сварочный полуавтомат своими руками. Рано или поздно, я думаю, все в жизни сталкивались с тем что нужно было что-то подварить, а для этого нужен сварочный аппарат. Многие скажут, зачем его делать — проще купить, но ведь приятнее сделать своими руками!
Всегда хотел иметь собственный сварочный аппарат, и даже думал его купить, но впереди была зима (больше времени), и я решил сделать его сам. Больше нужен был полуавтомат, но и дуговая сварка не помешает, поэтому решил делать 2в1 п-полуавтомат и дуговую от одного трансформатора.
Изготовление
Для дуговой сварки мне пришлось только домотать на трансформаторе нужное количество витков провода, чтобы трансформатор выдавал 45 вольт, и все.
Изготовление магнитопровода
А теперь начнем все по порядку. Сначала я занялся изготовлением магнитопровода, его я сделал из двух магнитопроводов от ЛАТРов.
Один отрезал до нужного размера.
Приспособление для размотки намотки
Оба размотал и с помощью нехитрого приспособления смотал их в один.
Затем магнитопровод я пропитываю эпоксидным клеем для того, чтобы трансформатор не гудел и не было короткого замыкания пластин.
После этого магнитопровод обматываем картоном.
Затем все обмотал изолентой из Х/Б ткани и малярным скотчем.
Подробнее о сборке тороидального магнитопровода смотрите на видео ниже:
youtube.com/embed/MAJ-dKjbrDY?feature=oembed» frameborder=»0″ allow=»accelerometer; autoplay; clipboard-write; encrypted-media; gyroscope; picture-in-picture» allowfullscreen=»»/>
Намотка первичной и вторичной обмоток
Следующий этап — намотка первичной и вторичной обмотки. Я мотал по такой схеме исходя из моего сечения магнитопровода.
(рассчитывается индивидуально для каждого трансформатора).
Первичная обмотка мотается медным проводом сечением от 2 мм2 (у меня он набран из нескольких жил). Для удобства намотки под магнитопровод сделал подставку, которая крепится к столу.
Провод наматываем на челнок — так намного проще мотать.
Каждый слой пропитываю лаком и мотаю сверху Х/Б тканью или изолентой.
Сечение провода на вторичной обмотке 16 мм2.
Подробнее о намотке я рассказал в видео ниже:
О результатах промежуточных испытаний также заснял видеоролик:
youtube.com/embed/QZg7KR7_hCM?feature=oembed» frameborder=»0″ allow=»accelerometer; autoplay; clipboard-write; encrypted-media; gyroscope; picture-in-picture» allowfullscreen=»»/>
Изготовление механизма протяжки
Следующий этап — сделать механизм протяжки. В качестве мотора я использовал двигатель от стеклоочистителя автомобиля ВАЗ 2101.
Подающий ролик купил готовый, но его также можно выточить у токаря.
Для того, чтобы на ось двигателя было меньше нагрузки — поставил два подшипника, которые между собой соединяются и прижим к ролику регулируется винтом.
Сварочный рукав
Рукав длиной 2,5 метра на 160 ампер.
Намотка дросселя
Дальше мотаем дроссель, который является неотъемлемой частью полуавтомата. Он служит для сглаживания импульсов тока, и без него полуавтомат не будет работать полноценно. Он намотан на трансформаторе ТС 250 от телевизора.
Но лучше ТС 270.Намотать нужно столько сколько влезет до заполнения окна тем самым проводом не меньше 20 мм2.Между подковами трансформатора обязательно должен быть немагнитный зазор и он изначально ставится 2 мм (текстолитовая пластина) но лучший результат достигается экспериментальным путем увеличения или уменьшения зазора в результате чего получаем наилучший сварной шов.
Плата управления и схема
Также одной из главных составных полуавтомата является плата управления-делал я ее по такой схеме.
Схема была взята здесь: http://svapka.ru/sampoluavtom/svarochnyj-poluavtomat-svapka-ru-vol-2-0-svapka-ru. htm
Файл печатной платы (проект программы DipTrace), можно скачать с сайта Svapka.ru по ссылке: http://svapka.ru/down/svapka20smd.dip
Плата управления
Есть также альтернативная схема регулировки оборотов двигателя.
Вместо клапана газа использовал клапан омывателя стекол ВАЗ 2108.
Силовые диоды на 200 ампер на радиаторах.
Провод для массы.
Переключатель напряжения первичной обмотки.
Тиристор Т-161-160 ампер.
Изготовление корпуса
Ну и наконец, завершающий этап — изготовление корпуса, компоновка всех элементов и сборка согласна схемы.
Ну и самое главное — как все это работает смотрим в финальном видео.
У кого возникнут вопросы — задавайте, всем отвечу.
Спасибо за внимание!
как собрать своими руками, инструкции, схемы
С опытом многие профессионалы приходят к выводу, что сварочный полуавтомат это намного больше, чем инструмент. Это универсальный помощник в бытовой сварке как на дачном участке, так и при ремонте автомобиля.
Он не ограничивает вас в выборе материала для сварки и пригодится не только мастеру, но и новичку.
Массовое производство полуавтоматов началось всего несколько лет назад. Сварщики старой школы раньше соединяли конструкции огромными трансформаторами.
Но технологический прогресс двигается вперед и позволил создать переносной и легкий полуавтомат. Появившись на рынке, он быстро показал миру свои преимущества и отправил старые модели на покой.
Сегодня им доступны самые разные виды сварки: ручная дуговая сварка покрытыми (штучными) электродами (MMA), дуговая сварка плавящимся металлическим электродом в газовой среде (MAG/MIG), а также ручная дуговая сварка неплавящимся электродом в среде инертного защитного газа (TIG).
Этого удалось достичь потому что внутри аппарата находится обычный инвертор. Из этого следует, что рабочий полуавтомат можно сделать в домашних условиях, взяв за основу инвертор. В концу этой статьи вы получите все необходимые советы и знания для этого.
Содержание статьиПоказать
Как устроен полуавтомат?
Перед началом работы с любой техникой первым делом нужно ознакомиться с его конструкцией.
В каждом полуавтомате находятся два блока: силовой и подающий.
Силовой блок представлен инвертором, который подает ток. Подающий блок — это отдельное устройство, который подключают для подачи проволоки. Моток проволоки закрепляют в подающем блоке, а конец выходит возле сопла горелки.
Но для наших целей он не очень нужен. Подачу проволоки можно делать самостоятельно, однако это замедлит рабочий процесс и будет крайне неудобно.
Мы описали вам главные элементы аппарата, но этого недостаточно. Вам также понадобится заказать специальные детали, нужные для определенного типа инвертора, а также комплектующие (горелка, рукав, сопло и т.д.).
Особенности рабочего процесса
Освоить работу с полуавтоматической сваркой не так сложно, как может показаться. После прочтения этой статьи с ней справиться даже неопытный сварщик.
Начнем с того, как устроена горелка. Горелка состоит из двух механизмов которые одновременно обеспечивают подачу защитного газа и проволоки.
Первую можно регулировать самостоятельно, однако вторая осуществляется в полуавтоматическом режиме (так и появилось соответствующее название). Из-за этого у сварщика задействована в работе только та рука, которая удерживает горелку.
Вернемся к подаче защитного газа в сварочную точку. Смесь газов окружает конец проволоки и верхний слой материала, и в этой среде возникает электроразряд, который плавит заготовку с проволокой.
Размягченный металл перемешивается с проволокой, и после этого можно делать сварочный шов.
Во время сварки вы не сможете обойтись без проволоки. Газ тоже необходим, поскольку он предотвращает попадание в ванну кислорода. Но даже при отсутствии газа вы можете использовать специальной порошковой проволокой.
Самодельный полуавтомат
Есть разные подходы к созданию самодельного сварочного полуавтомата из инвертора, но мы остановимся на самых практичных и интересных.
Следуя этим инструкциям любой новичок с начальными познаниями электротехники сможет сделать это у себя дома.
Метод №1
Сконструировать полуавтоматическое сварочное устройство можно и дома, используя подручный инвертор. Без него обойтись невозможно.
Подойдет инвертор средней мощности для MMA сварки. Важно, чтобы он был в рабочем состоянии и мог выполнять простые операции.
Далее нужно поменять вольт-амперные показатели (ВАХ) для работы в полуавтоматическом режиме. Тут пригодиться ШИМ-контроллер. Отметим, что этот подход самый трудный и справиться смогут только опытные сварщики.
Необходимо сделать дроссель из дневной лампы, и переключить напряжение на обратную связь. В видеоролике, представленном ниже, вы можете узнать все подробности и схемы этого метода.
Метод №2
Этот способ сбора самодельного сварочного полуавтомата очень простой и его может освоить практически каждый человек, который имел дело с инверторной сваркой. Некоторые модели инверторов можно переключать в режим с жестким изменением ВАХ.
Если у вас есть под рукой такой аппарат, то вы с легкостью можете сделать из него полуавтомат. Останется лишь заказать внешний подающий блок.
Важно иметь под рукой соответствующие провода. Нужно лишь подключить подающий блок к инвертору и вы готовы варить. В этом случае подающий блок выступает в роли дополнения. В видеоролике ниже демонстрируются особенности такого способа.
Метод №3
Последний метод сбора самодельного сварочного полуавтомата покажется не таким простым, ведь тут вам пригодятся определенные знания и умения. Как и в предыдущем случае, вам так же понадобится инвертор-донор.
Любым аппаратом обойтись не получится, потому что необходима именно сборка ZX-7 с шунтом на выходе. Отсутствие форсажа дуги и горячего старта будет только на пользу.
Не забывайте про вольт-амперные характеристики, их тоже нужно изменить. Далее настройте нарастание тока. В зависимости от сборки инвертора, дальнейшие шаги могут отличаться в разных источниках.
Рекомендуем вам прочитать больше информации на специальных форумах. В видеоролике ниже вы можете взглянуть на работу самодельного полуавтомата.
Итог
Это вся информация, необходимая вам для того, чтобы из инвертора сделать самодельный сварочный полуавтомат. Этот инструмент пригодится вам в тех случаях, когда под рукой не будет заводской модели.
Переделав его, вы не только сэкономите деньги, но также получите новые умения в электротехнике. Такой полуавтомат не требует тщательного ухода и его можно хранить хоть в подвале, хоть в гараже.
К тому же, починка инструмента не займет у вас много времени и сил, поскольку вы прекрасно понимаете, из каких деталей он состоит.
Важно помнить, что самодельный аппарат не станет вашим идеальным помощником. Не рекомендуется использовать его длительное время.
Во многих нюансах и характеристиках он будет сильно уступать заводским моделям, и вы пойдете на риск, если будете перестраивать его в полевых условиях. Для серьезных сварочных работ будет лучше приобрести инструмент в магазине.
В этой статье мы не смогли осветить все нюансы самостоятельной сборки полуавтомата. Но этой информации вам будет вполне достаточно. Собрать дома его возможно, но процесс этот довольно трудный и не самый выгодный.
Самодельное оборудования практически всегда будет работать хуже заводского. Учитывайте это перед тем, как решитесь на такой шаг. Желаем удачи в работе!
Сварочный полуавтомат своими руками — схема для сборки
Изделие, которое предназначено для процесса сварки называется сварочным полуавтоматом. Аппараты для сварки бывают разных форм и видов, но главное, чтобы этот механизм надежно работал, был качественным, практичным, безопасным и служил долгие годы.
Схемы самодельных сварочных полуавтоматов можно найти в интернете или узнать, получив консультацию специалиста. Данный инструмент пригодится в любом хозяйстве, хранить его можно как дома, так и в гараже или на даче. Для того чтобы сварка полуавтомат своими руками работала, необходимо знать кое-что о принципах работы этого механизма.
Виды сварочных полуавтоматов
Во-первых, нужно отметить, что сварочные аппараты делятся на следующие виды:
- для сварки под слоем флюса;
- для сварки на газах;
- а также для сварки порошковой проволокой.
Бывает такое, что для качественного результата необходимо взаимодействие этих видов аппаратов.
Кроме вышеперечисленных видов, эти изделия делятся и по другим критериям и бывают:
- однокорпусные и двукорпусные;
- стационарные, переносные и передвижные;
- профессиональные, полупрофессиональные и любительские;
- тянущие, толкающие.
Иногда для полноценной и качественной работы необходимо приобрести дополнительное оборудование (например, баллон с углекислым газом).
Основные составляющие сварочного аппарата и принцип сварки
Сварочный полуавтомат своими руками, схема которого не представляет особой сложности, состоит из нескольких основных элементов:
- источник питания;
- устройство с основной функцией – управление сварочным током;
- рукава;
- горелки;
- зажимы.
Источником питания может служить трансформатор, инвертор или выпрямитель. От того, какой источник питания выбран, зависит объем и цена сварочника. Лучшими называют инверторные источники питания.
Электрическая схема сварочного полуавтомата предусматривает, что тип сварки влияет на слаженность работы оборудования в целом.
Принцип работы аппарата заключается в перемещении и регулировке грелки, в контроле и отслеживании сварочного процесса.
Также схемы самодельных сварочных аппаратов предусматривают определенную последовательность работы. На начальном этапе проходит подготовительная продувка системы для дальнейшей подачи газа. Следующим запускается источник питания дуги. Потом подается проволока и начинается движение полуавтомата с определенной скоростью. По окончании процесса, необходимо обеспечить заварку кратера и защиту шва.
Нужно также учесть, что процесс сварки выполняется в специальном помещении с применением сварочного оборудования.
Сварка полуавтомат своими руками предусматривает обязательное соблюдение правил безопасности. Нужно проверить исправность всех механизмов, перепроверить заземлен ли корпус устройства. Во время сварки, нельзя облокачиваться или опираться на аппарат. Если с аппаратом возникли какие-то неполадки, следует немедленно прекратить работу и прибегнуть к помощи специалиста.
Плюсы и минусы сварочного аппарата, и советы по его изготовлению своими руками
Сварочный полуавтомат своими руками, схема которого рассмотрена выше, имеет свои достоинства и недочеты.
К преимуществам можно отнести высокий коэффициент полезного действия, минимальную потерю энергии и расход электротехнического материала. Этот современный механизм характеризуется небольшими габаритами и весом, высоким качеством шва и возможностью работы с любыми сплавами. Его удобно передвигать к месту сварки, и он имеет достаточно высокий уровень безопасности.
Недостатками этого аппарата можно считать его высокую стоимость и плохую работу в условиях отрицательных температур.
Существуют инструкции для изготовления полуавтоматов для сварки своими руками, которые, как правило, предусматривают их применение в мелких бытовых целях. Именно исходя из этого и производятся основные расчеты по его изготовлению. Лучше всего для изготовления этого аппарата ручным способом, использовать трансформаторное железо.
Изучив, что такое электросхема сварочного полуавтомата и основные принципы его действия можно без особого труда сделать сварочный аппарат самостоятельно. Важно не забывать об электробезопасности и правилах, удобнее выполнять работы по изготовлению сварочного полуавтомата в домашних условиях вдвоем. Также нужно помнить, что электрическая схема сварочного полуавтомата предусматривает предварительные расчеты, которые лучше лишний раз перепроверить.
Поделитесь со своими друзьями в соцсетях ссылкой на этот материал (нажмите на иконки):
изготовление из инвертора и трансформатора
Возможности сварочного полуавтомата значительно выше, чем у аппарата, предназначенного для выполнения ручной дуговой сварки. Полуавтоматом можно сваривать значительно более тонкий металл.
Применение специальной сварочной проволоки позволяет работать с цветными металлами, а использование защитного газа обеспечивает сварной шов более высокого качества. Учитывая эти обстоятельства, желание пополнить свою домашнюю мастерскую таким устройством вполне объяснимо.
Общие сведения
Если купить сварочный полуавтомат нет возможности, можно попробовать собрать его своими руками. Сразу нужно сказать, задача эта не из самых лёгких, и собрать самодельный сварочный полуавтомат под силу только тем, кто имеет определённый навык работы с электрическими приборами, уже что-то ремонтировал, и разбирается в схемах. Для тех, кто решился на это, можно порекомендовать несколько возможных вариантов сборки.
До начала планирования работ по созданию сварочного полуавтомата, следует изучить принципы полуавтоматической сварки, а также устройство и работу предназначенного для этого прибора.
Сварочными полуавтоматами называют аппараты, осуществляющие электродуговую сварку постоянным током с использованием в качестве электрода специальной сварочной проволоки в среде защитных газов.
Проволока намотана на вращающейся катушке и автоматически подается к месту сварки, проходя через механизм подачи. Схема сварочного полуавтомата может содержать как инверторный, так и трансформаторный источник тока.
Сварщик своими руками разжигает дугу и выполняет шов, поэтому работа называется полуавтоматической. Аналогом держателя электродов в сварочном полуавтомате служит горелка, имеющая пистолетную рукоятку с клавишей включения подачи проволоки.
Подача проволоки осуществляется по тонкому каналу, проходящему внутри обрезиненного рукава, соединяющего полуавтомат с горелкой. Канал для подачи газа при сварке находится в том же рукаве и заканчивается соплом на конце горелки.
Перед тем как зажечь дугу, включением подачи проволоки нужно добиться её выдвижение за край горелки на 10 – 15 мм.
Затем включается подача газа и начинается процесс сварки. Скорость подачи проволоки и газа регулируется руками, вращением головок, расположенных на лицевой панели сварочного полуавтомата.
Из сварочного трансформатора
Если в Вашем распоряжении есть старый сварочный трансформатор, он может послужить основой для сборки своими руками полуавтоматического аппарата.
Если старый аппарат имеет выпрямитель и успешно варит постоянным током, в этой части больше ничего делать не надо. Если же это просто трансформатор для сварки переменным током, его следует доработать.
Диодный мост
Для того чтобы получить источник постоянного тока сварки, трансформатор необходимо укомплектовать диодным мостом и фильтром. Диодная сборка выпрямляет вторичное напряжение, фильтр сглаживает пульсации, поддерживая стабильное горение дуги.
Выпрямленное напряжение однофазного трансформатора имеет вид синусоиды, нижние полуволны которой отражены симметрично оси абсцисс и перемещены в верхние квадранты системы координат.
По сути, это пульсирующее с частотой 100 герц напряжение, два раза за период достигающее нулевого значения. Использование такого напряжения для сварки в качестве постоянного, приводит к нестабильному горению дуги. Для устранения этого явления требуется фильтр, сглаживающий провалы напряжения.
Фильтр
Фильтр состоит из дросселя, включенного в сварочную цепь последовательно, и конденсатора, включенного параллельно. Такая комбинация индуктивности и ёмкости называется Г – образным фильтром, потому что на схеме, подключенные таким образом элементы образуют букву Г.
Конденсатор для будущего полуавтомата нужен электролитический, полярный, ёмкостью 10000 микрофарад, чем больше, тем лучше. Напряжение конденсатора должно быть не менее 100 вольт, чтобы имелся хороший запас. Можно спаять несколько конденсаторов параллельно, ёмкость при этом суммируется.
Дроссель
Для намотки дросселя своими руками нужно найти старый трансформатор подходящих размеров. Хорошо подходит для этой цели трансформатор питания от старых ламповых цветных телевизоров, мощностью не менее 250 ватт.
Трансформатор имеет две катушки на овальном замкнутом сердечнике, состоящем из двух половинок. Трансформатор разбирается, катушки снимаются, старый провод с них удаляется.
Для намотки подбирается подходящая медная шина плоского сечения. На каждую катушку вместо снятого провода руками наматывается два слоя витков медной шиной. На катушке должно получиться 15 – 20 витков.
После этого, стальной сердечник собирается, катушки ставятся на место, между половинками сердечника вставляется текстолитовая прокладка толщиной 1,5 мм. Катушки соединяются последовательно.
Протяжка
Механизм протяжки проволоки для полуавтомата можно соорудить своими руками, используя небольшие подшипники и электродвигатель от автомобильных дворников.
Но лучше купить в сборе готовый, он продаётся как запчасть к сварочным полуавтоматам. Также придётся купить горелку и рукав, по которому будет подаваться проволока и газ.
Из инвертора для ручной сварки
Если в мастерской имеется сварочный инвертор для ручной сварки, проблему с источником тока для полуавтомата можно считать решённой. На базе аппарата для ручной сварки можно своими руками сделать инверторный полуавтомат.
Для того чтобы не разбирать работоспособный инверторный преобразователь, можно поступить следующим образом. Все дополнительные узлы, необходимые для работы сварочного полуавтомата можно расположить в отдельном корпусе.
Изготовление корпуса
Задача заключается в том, чтобы найти или изготовить подходящий корпус, в котором будет установлена катушка со сварочным проводом, свободно вращающаяся на барабане, механизм протяжки проволоки. На лицевой панели этого корпуса будет располагаться гнездо для подключения рукава с горелкой и регулятор скорости подачи проволоки.
Регулировку тока можно осуществлять на инверторе, плюсовая клемма может соединяться с заготовкой также непосредственно от инвертора.
Минусовой вывод инвертора нужно завести в новый корпус и соединить с клеммой рукава. Сварочная проволока должна быть соединена с этим потенциалом.
Также внутри нового корпуса следует предусмотреть монтаж шланга, соединяющего баллон с защитным газом и рукав горелки. Для осуществления регулируемой подачи газа можно установить клапан от автомобильного стеклоочистителя.
Обеспечение питания протяжки и клапана
Поскольку электродвигатель механизма протяжки проволоки и клапан, перекрывающий газ питаются постоянным напряжением 12 вольт, придётся установить небольшой трансформатор с выпрямителем, обеспечивающий это питание.
Для коммутации двигателя и клапана лучше установить промежуточные автомобильные реле на 12 вольт. Включение протяжки проволоки осуществляется клавишей на горелке, удерживаемой руками, для открытия и закрытия клапана подачи газа, на лицевой панели устанавливается тумблер.
Такая компоновка позволит пользоваться инвертором и для ручной сварки, и как источником тока для сварочного полуавтомата. Затраты на изготовление самодельного полуавтомата невелики, а польза от него будет ощутимая.
Дуговая сварка под флюсом (SAW) — Weld Guru
Дуговая сварка под флюсом (SAW) — это процесс, в котором соединение металлов производится дугой или дугой между неизолированным металлическим электродом или электродами и изделием.
Дуга защищена слоем гранулированного плавкого материала на рабочем месте.
Давление не используется.
Компоненты оборудования для сварки под флюсом, необходимые для сварки под флюсом, показаны на рис. 10-59.
Оборудование состоит из сварочного аппарата или источника питания, механизма подачи проволоки и системы управления, сварочной горелки для автоматической сварки или сварочного пистолета и кабельной сборки для полуавтоматической сварки, бункера для флюса и механизма подачи, обычно системы восстановления флюса, и механизм передвижения для автоматической сварки.
Источник питания для дуговой сварки под флюсом должен быть рассчитан на 100-процентный рабочий цикл, поскольку операции сварки под флюсом являются непрерывными, а продолжительность сварки может превышать 10 минут.
Если используется источник питания с рабочим циклом 60 процентов, его номинальные характеристики должны быть снижены в соответствии с кривой рабочего цикла для 100-процентного режима работы.
При использовании постоянного тока переменного или постоянного тока необходимо использовать систему подачи проволоки с чувствительным к напряжению электродом.
При использовании постоянного напряжения используется более простая система подачи проволоки с фиксированной скоростью.Система CV используется только с постоянным током.
Используются как генераторные, так и трансформаторно-выпрямительные источники питания, но выпрямительные машины более популярны.
Сварочные аппараты для дуговой сварки под флюсом мощностью от 300 до 1500 ампер.
Их можно подключать параллельно для обеспечения дополнительной мощности для сильноточных приложений.
Электропитание постоянного тока используется для полуавтоматических применений, но питание переменного тока используется в основном с машиной или автоматическим методом.
Для систем с несколькими электродами требуются специальные типы цепей, особенно когда используется переменный ток.
Для полуавтоматического применения сварочная горелка и кабельная сборка используются для передачи электрода и тока, а также для обеспечения потока на дуге.
Небольшой бункер для флюса прикреплен к концу кабельной сборки.
Электродная проволока подается через дно этого флюсового бункера через наконечник датчика тока к дуге.
Подача флюса из бункера в зону сварки осуществляется самотеком.
Количество подаваемого флюса зависит от того, насколько высоко расположен пистолет над изделием.
Бункерный пистолет может включать пусковой переключатель для инициирования сварки или может использовать «горячий» электрод, чтобы при прикосновении электрода к изделию подача начиналась автоматически.
Для автоматической сварки горелка присоединяется к двигателю подачи проволоки и включает в себя наконечники датчиков тока для передачи сварочного тока на электродную проволоку.
Бункер флюса обычно прикрепляется к горелке и может иметь клапаны с магнитным приводом, которые могут открываться или закрываться системой управления.
Другое оборудование, которое иногда используется, может включать в себя передвижную тележку, которая может быть простым трактором или сложным движущимся специализированным приспособлением. Блок рекуперации флюса обычно используется для сбора неиспользованного флюса подводной дуги и возврата его в питающий бункер.
Система для дуговой сварки под флюсом может стать довольно сложной из-за включения дополнительных устройств, таких как толкатели для швов, ткацкие станки и рабочие вездеходы.
Схема сварки под флюсом
Рисунок 10-59. Блок-схема оборудования для сварки под флюсом.Преимущества SAW
Основными преимуществами процесса сварки под флюсом или под флюсом являются:
- металлический шов высокого качества.
- чрезвычайно высокая скорость и производительность наплавки
- гладкий, однородный сварной шов без брызг.
- мало или совсем нет дыма.
- нет дуги, поэтому необходимость в защитной одежде минимальна.
- высокий коэффициент использования электродной проволоки.
- Простая автоматизация для высокого оператора.
- в норме, манипулятивные навыки не задействованы.
Основные области применения SAW
Процесс под флюсом широко используется при производстве толстолистовой стали. Сюда входит сварка:
- Профили конструкционные
- Продольный шов трубы большего диаметра
- производство деталей машин для всех видов тяжелой промышленности,
- производство сосудов и резервуаров для давления и хранения использовать
Он широко используется в судостроении для сращивания и изготовления узлов, а также во многих других отраслях промышленности, где используется сталь средней и большой толщины.
Применяется также для наплавочных и наплавочных работ, технического обслуживания и ремонта.
При сварке SAW флюс и проволока разделены. И то и другое влияет на свойства сварного шва, что требует от инженера выбора оптимальной комбинации для каждого проекта.Ограничения процесса
Основным ограничением сварки под флюсом является ограничение положения при сварке. Другое ограничение заключается в том, что он в основном используется только для сварки мягких и низколегированных высокопрочных сталей.
Высокая погонная энергия и цикл медленного охлаждения могут быть проблемой при сварке закаленной и отпущенной стали.При использовании дуговой сварки под флюсом необходимо строго соблюдать ограничение тепловложения для рассматриваемой стали.
Это может потребовать выполнения многопроходных сварных швов, когда однопроходный сварной шов приемлем для низкоуглеродистой стали. В некоторых случаях экономические преимущества могут быть сведены к тому моменту, когда следует рассмотреть дуговую сварку порошковой проволокой или какой-либо другой процесс.
При полуавтоматической сварке под флюсом невозможность видеть дугу и лужу может быть недостатком для достижения корня сварного шва с разделкой кромок и правильного заполнения или калибровки.
Демонстрация процесса сварки пилой.Принципы работы
Процесс
Процесс сварки под флюсом показан на рисунке 10-60. Он использует тепло дуги между непрерывно подаваемым электродом и изделием.
Рисунок 10-60: Схема процесса сварки под флюсом (SAW)Тепло дуги плавит поверхность основного металла и конец электрода. Металл, расплавленный с электрода, переносится через дугу к заготовке, где он становится наплавленным металлом сварного шва.
Экранирование достигается за счет слоя гранулированного флюса, который накладывается непосредственно на область сварного шва. Флюс вблизи дуги плавится и смешивается с расплавленным металлом сварного шва, помогая его очистить и укрепить.
Флюс образует стеклоподобный шлак, который легче по весу, чем наплавленный металл шва, и плавает на поверхности в качестве защитного покрытия.
Сварной шов погружается под этот слой флюса и шлака, отсюда и название сварка под флюсом. Флюс и шлак обычно покрывают дугу, так что ее не видно.
Нерасплавленная часть флюса может быть использована повторно. Электрод вводится в дугу автоматически из катушки. Дуга поддерживается автоматически.
Путешествие может быть ручным или машинным. Дуга возникает при запуске с предохранителем или системой реверсирования или возврата.
Нормальный метод применения и возможности положения
Самым популярным методом нанесения SAW является машинный метод, при котором оператор контролирует сварочную операцию.
Вторым по популярности является автоматический метод, при котором сварка осуществляется нажатием кнопки.Процесс может применяться полуавтоматически; однако этот способ нанесения не слишком популярен.
Этот процесс нельзя применить вручную, потому что сварщик не может контролировать невидимую дугу. Процесс дуговой сварки под флюсом — это сварочный процесс с ограниченными позициями.
Позиции сварки ограничены, потому что большая ванна расплавленного металла и шлака очень текучие и имеют тенденцию вытекать из стыка. Сварку можно легко выполнять как в горизонтальном, так и в горизонтальном положении.
В соответствии со специальными контролируемыми процедурами, можно выполнять сварку в горизонтальном положении, иногда называемом сваркой на 3 часа.
Для этого требуются специальные устройства для удержания флюса, чтобы расплавленный шлак и металл шва не могли уйти. Процесс нельзя использовать в вертикальном или верхнем положении.
Металлы свариваемые и диапазон толщины
Сварка под флюсом применяется для сварки низко- и среднеуглеродистых сталей, низколегированных высокопрочных сталей, закаленных и отпущенных сталей и многих нержавеющих сталей.
Экспериментально он использовался для сварки некоторых медных сплавов, никелевых сплавов и даже урана.
Металл толщиной от 1/16 до 1/2 дюйма (от 1,6 до 12,7 мм) можно сваривать без подготовки кромок. С подготовкой кромок можно выполнять сварные швы за один проход на материале от 1/4 до 1 дюйма (от 6,4 до 25,4 мм).
При использовании многопроходной техники максимальная толщина практически не ограничена. Эта информация обобщена в таблице 10-22. Горизонтальные угловые швы можно выполнять до 3/8 дюйма.(9,5 мм) за один проход и в плоском положении можно выполнять угловые швы размером до 1 дюйма (25 мм).
Совместное проектирование
Хотя в процессе дуговой сварки под флюсом могут использоваться те же детали конструкции соединения, что и в процессе дуговой сварки защищенным металлом, для максимального использования и эффективности дуговой сварки под флюсом предлагаются другие детали соединения. Для сварных швов с канавкой можно использовать конструкцию с квадратными канавками толщиной до 5/8 дюйма (16 мм).
При превышении этой толщины требуются фаски.Используются открытые корни, но необходимы подкладки, так как расплавленный металл будет проходить через стык.
При сварке более толстого металла, если используется достаточно большая поверхность основания, опорный стержень может быть удален. Однако для обеспечения полного проплавления при сварке с одной стороны рекомендуется использовать подкладные стержни. Там, где доступны обе стороны, можно сделать подкладочный сварной шов, который вплавится в исходный сварной шов, чтобы обеспечить полное проплавление.
Сварочная цепь и ток
При сварке под флюсом или под флюсом в качестве сварочной мощности используется постоянный или переменный ток.Постоянный ток используется в большинстве приложений, в которых используется одиночная дуга. Используются как положительный электрод постоянного тока (DCEP), так и отрицательный электрод (DCEN).
Источник постоянного напряжения постоянного тока более популярен для дуговой сварки под флюсом с использованием электродной проволоки диаметром 1/8 дюйма (3,2 мм) и меньшего диаметра.
Система постоянного тока обычно используется для сварки электродной проволокой диаметром 5/3 2 дюйма (4 мм) и большего диаметра. Схема управления мощностью CC более сложна, поскольку она пытается дублировать действия сварщика, чтобы сохранить определенную длину дуги.Система подачи проволоки должна определять напряжение на дуге и подавать электродную проволоку в дугу, чтобы поддерживать это напряжение. При изменении условий подача проволоки должна замедляться или увеличиваться, чтобы поддерживать заданное напряжение на дуге. Это усложняет систему управления. Система не может реагировать мгновенно. Запуск дуги более сложен с системой постоянного тока, так как она требует использования реверсивной системы, чтобы зажигать дугу, отводить и затем поддерживать заданное напряжение дуги.
При сварке SAW на переменном токе всегда используется постоянный ток. Когда системы с несколькими электродными проводами используются как с дугой переменного, так и с постоянным током, используется система постоянного тока. Однако система постоянного напряжения может применяться, когда два провода подводятся к дуге, питаемой от одного источника питания. Сварочный ток для дуговой сварки под флюсом может варьироваться от 50 до 2000 ампер. Чаще всего сварка под флюсом выполняется в диапазоне от 200 до 1200 ампер.
Скорость наплавки и качество сварки
Скорость наплавки при дуговой сварке под флюсом выше, чем при любой другой дуговой сварке.Скорость наплавки отдельных электродов показана на рисунке 10-62. Скорость наплавки при сварке под флюсом определяется как минимум четырьмя факторами: полярность, большой вылет, добавки во флюсе и дополнительные электроды. Скорость осаждения является самой высокой для отрицательного электрода постоянного тока (DCEN). Скорость осаждения для переменного тока находится между DCEP и DCEN. Полярность максимального тепла — отрицательный полюс.
Скорость наплавки при любом сварочном токе можно увеличить, увеличив «вылет».”Это расстояние от точки, где ток вводится в электрод, до дуги. При использовании «длинного вылета» степень проникновения уменьшается. Скорость наплавки может быть увеличена за счет добавок металла во флюс под флюсом. Дополнительные электроды можно использовать для увеличения общей скорости осаждения.
Качество наплавленного металла шва, наплавленного дуговой сваркой под флюсом, высокое. Прочность и пластичность металла сварного шва превышают таковые у низкоуглеродистой стали или низколегированного основного материала, когда используется правильное сочетание электродной проволоки и флюса под флюсом.Когда сварка под флюсом выполняется машиной или автоматически, человеческий фактор, присущий процессам ручной сварки, исключается. Сварной шов будет более однородным и без неровностей. Как правило, размер сварного шва за проход намного больше при дуговой сварке под флюсом, чем при любом другом процессе дуговой сварки. Подвод тепла выше, а скорость охлаждения ниже. По этой причине газам дается больше времени для выхода. Кроме того, поскольку плотность шлака под флюсом ниже плотности металла сварного шва, он будет всплывать в верхнюю часть сварного шва.Однородность и последовательность — преимущества этого процесса при автоматическом применении.
При использовании полуавтоматического метода нанесения может возникнуть несколько проблем. Электродная проволока может искривляться на выходе из сопла сварочной горелки. Эта кривизна может привести к возникновению дуги в месте, не ожидаемом сварщиком. При сварке в достаточно глубоких канавках кривизна может привести к тому, что дуга будет приходиться к одной стороне сварного соединения, а не к основанию. Это приведет к неполному сращиванию корней.Флюс останется у основания сварного шва. Другая проблема, связанная с полуавтоматической сваркой, заключается в том, что сварная канавка полностью заполняется или сохраняется точный размер, поскольку сварной шов скрыт и не может быть замечен во время его выполнения. Для этого нужно сделать дополнительный проход. В некоторых случаях получается слишком много сварного шва. Вариации раскрытия корня влияют на скорость движения. Если скорость движения одинакова, сварной шов может быть недостаточно или переполнен на разных участках. Высокая квалификация оператора решит эту проблему.
Есть еще одна проблема качества, связанная с очень большими наплавками за один проход.Когда эти большие сварные швы затвердевают, все примеси в расплавленном основном металле и в металле сварного шва собираются в последней точке замерзания, которая является центральной линией сварного шва. Если в этом месте будет собрано достаточное количество примесей, может произойти растрескивание по средней линии. Это может произойти при выполнении больших однопроходных плоских угловых швов, если основные металлические пластины расположены под углом 45º от плоскости. Простое решение — избегать размещения деталей под истинным углом 45 °. Его следует изменять примерно на 10º, чтобы корень шва не совпадал с центральной линией углового шва.Другое решение — сделать несколько проходов, а не пытаться сделать большой сварной шов за один проход.
Другая проблема качества связана с твердостью наплавленного металла шва. Чрезмерно твердые отложения сварного шва способствуют растрескиванию сварного шва во время изготовления или во время эксплуатации. Рекомендуется максимальный уровень твердости 225 по Бринеллю. Причиной твердого сварного шва углеродистых и низколегированных сталей является слишком быстрое охлаждение, недостаточная обработка после сварки или чрезмерное поглощение сплава металлом шва.Чрезмерное поглощение сплава связано с выбором электрода со слишком большим количеством сплава, выбором флюса, который вводит слишком много сплава в сварной шов, или использованием слишком высоких сварочных напряжений.
При автоматической и машинной сварке дефекты могут возникать в начале или в конце шва. Лучшее решение — использовать вкладки биения, чтобы запуски и остановки находились на вкладках, а не на продукте.
Графики сварки
Процесс сварки под флюсом, применяемый машиной или полностью автоматически, должен выполняться в соответствии с графиками сварочных работ.Все сварные швы, выполненные с помощью этой процедуры, должны пройти аттестацию и испытания, предполагая, что были выбраны правильный электрод и флюс. Если графики отличаются более чем на 10 процентов, следует провести квалификационные испытания для определения качества сварки.
Сварочные параметры
Параметры сварки для дуговой сварки под флюсом аналогичны другим процессам дуговой сварки, за некоторыми исключениями.
При дуговой сварке под флюсом тип электрода и тип флюса обычно основываются на механических свойствах, требуемых сварным швом.Размер электрода зависит от размера сварного шва и тока, рекомендованного для конкретного соединения. Это также необходимо учитывать при определении количества проходов или валиков для конкретного соединения. Сварные швы с одинаковым размером стыка можно выполнять за несколько или несколько проходов, в зависимости от желаемой металлургии металла шва. За несколько проходов обычно получается более качественный сварной металл. Полярность устанавливается изначально и зависит от того, требуется ли максимальное проникновение или максимальная скорость наплавки.
Основные переменные, влияющие на сварку, включают подвод тепла и включают сварочный ток, напряжение дуги и скорость перемещения.Сварочный ток — это самое главное. Для однопроходных сварных швов сила тока должна быть достаточной для желаемого проплавления без прожога. Чем выше сила тока, тем глубже проникновение. При многопроходной работе ток должен быть подходящим для получения сварного шва того размера, который ожидается при каждом проходе. Сварочный ток следует выбирать в зависимости от размера электрода. Чем выше сварочный ток, тем выше скорость плавления (скорость наплавки).
Напряжение дуги изменяется в более узких пределах, чем сварочный ток.Это влияет на ширину и форму борта. Более высокое напряжение приведет к тому, что борт будет шире и ровнее. Следует избегать чрезмерно высокого напряжения дуги, так как это может вызвать растрескивание. Это связано с тем, что чрезмерное количество флюса расплавляется, и избыточные раскислители могут быть перенесены в наплавленный слой, снижая его пластичность. Более высокое напряжение дуги также увеличивает количество потребляемого магнитного потока. Низкое напряжение дуги создает более жесткую дугу, которая улучшает проплавление, особенно в нижней части глубоких канавок.Если напряжение слишком низкое, получится очень узкий валик. У него будет высокий венец, и удалить шлак будет сложно.
Скорость движения влияет как на ширину борта, так и на глубину проникновения. Более высокие скорости движения позволяют получить более узкие валики с меньшим проникновением. Это может быть преимуществом при сварке листового металла, когда требуются небольшие валики и минимальное проплавление. Однако при слишком высоких скоростях возникает тенденция к образованию поднутрений и пористости, поскольку сварной шов быстрее застывает. Если скорость движения слишком низкая, электрод слишком долго остается в сварочной ванне.Это создает плохую форму валика и может вызвать чрезмерное разбрызгивание и вспышку через слой флюса.
Вторичные переменные включают угол электрода к изделию, угол самой работы, толщину слоя флюса и расстояние между наконечником датчика тока и дугой. Этот последний фактор, называемый «вылетом» электрода, оказывает значительное влияние на сварной шов. Обычно расстояние между контактным наконечником и деталью составляет от 1 до 1-1 / 2 дюйма (от 25 до 38 мм). Если вылет увеличивается сверх этого значения, это вызовет предварительный нагрев электродной проволоки, что значительно увеличит скорость наплавки.По мере увеличения вылета уменьшается проникновение в основной металл. Этому фактору необходимо уделить серьезное внимание, потому что в некоторых ситуациях требуется проникновение.
Также необходимо учитывать глубину слоя флюса. Если он слишком тонкий, то в потоке или вспышке дуги будет слишком много дуги. Это также может вызвать пористость. Если глубина флюса слишком велика, сварной шов может быть узким и выпуклым. Слишком большое количество мелких частиц во флюсе может вызвать точечную коррозию на поверхности, поскольку газы, образующиеся в сварном шве, могут не выйти.Иногда их называют следами клюва на поверхности борта.
Советы по использованию процесса
Одно из основных применений дуговой сварки под флюсом — это круговые сварные швы, когда детали вращаются под неподвижной головкой. Эти сварные швы могут быть выполнены по внутреннему или внешнему диаметру. При дуговой сварке под флюсом образуется большая сварочная лужа и расплавленный шлак, который имеет тенденцию течь. Это означает, что на наружных диаметрах электрод должен располагаться впереди крайней вершины или положения на 12 часов, чтобы металл сварного шва начал затвердевать до того, как начнется наклон вниз.Это становится еще большей проблемой, когда диаметр свариваемой детали становится меньше. Неправильное положение электрода увеличивает вероятность улавливания шлака или плохой поверхности сварного шва. Также следует изменить угол наклона электрода и направить его в направлении движения вращающейся части. Когда сварка выполняется по внутренней окружности, электрод следует наклонить так, чтобы он находился впереди центра нижней части или в положении «6 часов».
Иногда свариваемая деталь имеет уклон вниз или вверх, чтобы обеспечить различные типы контуров сварных швов.Если работа идет под уклоном, борт будет иметь меньшую глубину проникновения и будет шире. Если сварной шов идет вверх с уклоном, валик будет иметь более глубокий провар и будет уже. Это основано на том, что все остальные факторы остаются неизменными.
Сварочный шов будет отличаться в зависимости от угла наклона электрода по отношению к работе, когда работа выровнена. Это угол перемещения, который может быть углом сопротивления или толкания. Он оказывает определенное влияние на контур валика и проплавление металла шва.
Односторонняя сварка с полным проваром корня может быть получена дуговой сваркой под флюсом.Если сварное соединение спроектировано с плотным отверстием в корне и довольно большой поверхностью корня, следует использовать высокий ток и положительный электрод. Если соединение спроектировано с корневым отверстием и минимальной поверхностью основания, необходимо использовать опорный стержень, поскольку нет ничего, что могло бы поддерживать расплавленный металл сварного шва. Расплавленный флюс очень жидкий и будет проходить через узкие отверстия. Если это произойдет, металл шва последует за ним, и сварной шов прожигет соединение. Опорные стержни необходимы всякий раз, когда есть отверстие в корне и минимальная поверхность корня.
Медные опорные стержни используются при сварке тонкой стали. Без подкладных стержней сварной шов будет иметь тенденцию плавиться, и металл шва будет выпадать из стыка. Опорная планка удерживает металл сварного шва на месте, пока он не затвердеет. Медные опорные стержни могут охлаждаться водой, чтобы избежать возможности плавления и захвата меди в металле сварного шва. Для более толстых материалов основа может быть флюсом под флюсом или другим специализированным типом флюса.
Варианты процесса SAW
Существует множество разновидностей процесса, которые дают дополнительные возможности для сварки под флюсом.Некоторые из наиболее популярных вариантов:
- Двухпроводные системы — один источник питания.
- Двухпроводные системы — отдельный источник питания.
- Трехпроводные системы — отдельный источник питания.
- Ленточный электрод для наплавки.
- Добавки порошка железа во флюс.
- Сварка с длинным вылетом.
- Электрически «холодная» присадочная проволока.
Многопроволочные системы
Многопроволочные системы обладают преимуществами, поскольку скорость наплавки и скорость перемещения могут быть улучшены за счет использования большего количества электродов.На рис. 10-68 показаны два метода использования двух электродов: один с одним источником питания, а другой — с двумя источниками питания. При использовании одного источника питания одни и те же приводные ролики используются для подачи обоих электродов в сварной шов. При использовании двух источников питания необходимо использовать отдельные механизмы подачи проволоки для обеспечения электрической изоляции между двумя электродами. С двумя электродами и раздельным питанием можно использовать разные полярности на двух электродах или использовать переменный ток на одном и постоянный ток на другом.Электроды можно размещать рядом. Это называется поперечным положением электрода. Их также можно разместить один перед другим в положении тандемного электрода.
Двухпроводной тандемный
Двухпроводной тандемный электрод с индивидуальными источниками питания используется там, где требуется очень глубокое проникновение. Ведущий электрод положительный, а задний электрод отрицательный. Первый электрод создает копающее действие, а второй электрод заполняет сварной шов.Когда две дуги постоянного тока находятся в непосредственной близости, существует тенденция к взаимному влиянию дуги между ними. В некоторых случаях второй электрод подключается к переменному току, чтобы избежать взаимодействия дуги.
Трехпроводная тандемная система
Трехпроводная тандемная система обычно использует питание переменного тока на всех трех электродах, подключенных к трехфазным системам питания. Эти системы используются для изготовления высокоскоростных продольных швов труб большого диаметра и сборных балок. Чрезвычайно высокие токи могут использоваться при соответственно высоких скоростях движения и производительности наплавки.
Система сварки лент
Система сварки полос используется для наплавки низкоуглеродистой и легированной стали, как правило, нержавеющей сталью. Получается широкий валик с равномерным минимальным проплавлением. Этот вариант процесса показан на рисунке 10-69. Он используется для покрытия внутренней части сосудов, чтобы обеспечить коррозионную стойкость нержавеющей стали, используя при этом прочность и экономичность низколегированных сталей для толщины стенок. Требуется устройство подачи ленточных электродов, и обычно используется специальный флюс.Когда ширина полосы превышает 2 дюйма (51 мм), используется устройство колебания магнитной дуги для обеспечения равномерного прожигания полосы и равномерного проплавления.
Другие опции
Другой способ увеличения скорости наплавки при дуговой сварке под флюсом — добавление компонентов на основе железа в соединение под флюсом. Железо в этом материале расплавится под действием тепла дуги и станет частью наплавленного металла шва. Это увеличивает скорость наплавки без ухудшения свойств металла сварного шва.Добавки для металлов также можно использовать для специальных наплавок. Этот вариант может использоваться с однопроводной или многопроволочной установкой.
Другой вариант — использование электрически «холодной» присадочной проволоки, подаваемой в зону дуги. «Холодный» присадочный пруток может быть сплошным или порошковым для добавления специальных сплавов к металлу сварного шва. Регулируя добавление подходящего материала, можно улучшить свойства наплавленного металла шва. Можно использовать порошковую проволоку для электрода или для одного из нескольких электродов, чтобы ввести специальные сплавы в наплавленный металл шва.Каждый из этих вариантов требует специальной инженерии, чтобы гарантировать, что правильный материал добавлен для обеспечения желаемых свойств отложения.
Типичные области применения
Процесс дуговой сварки под флюсом широко используется при производстве большинства тяжелых стальных изделий. К ним относятся сосуды высокого давления, котлы, резервуары, ядерные реакторы, химические сосуды и т. Д. Другое применение — изготовление ферм и балок. Применяется для приваривания фланцев к стенке. Промышленность тяжелого оборудования является основным потребителем дуговой сварки под флюсом.
Используемые материалы
При сварке под флюсом используются два материала: сварочный флюс и плавящаяся электродная проволока.
Флюс для дуговой сварки под флюсом защищает дугу и расплавленный металл шва от вредного воздействия атмосферного кислорода и азота. Флюс содержит раскислители и поглотители, которые помогают удалять загрязнения из расплавленного металла шва. Флюс также обеспечивает введение сплавов в металл сварного шва. Когда этот расплавленный флюс охлаждается до стекловидного шлака, он образует покрытие, защищающее поверхность сварного шва.Нерасплавленная часть флюса не меняет своей формы и не влияет на ее свойства, поэтому ее можно восстанавливать и использовать повторно. Флюс, который плавится и образует шлаковое покрытие, необходимо удалить со сварного шва. Это легко сделать после того, как сварной шов остынет. Во многих случаях шлак действительно отслаивается, не требуя особых усилий для удаления. При сварке с разделкой кромок затвердевший шлак может быть удален с помощью отбойного молотка сварщика.
Флюсы предназначены для конкретных применений и для определенных типов наплавок.Флюсы под флюсом имеют разный размер частиц. Многие флюсы не имеют маркировки по размеру частиц, потому что размер разработан и произведен для предполагаемого применения.
Нет спецификации для флюсов под флюсом, используемых в Северной Америке. Однако метод классификации флюсов основан на наплавленном металле сварного шва, полученном с помощью различных комбинаций электродов и запатентованных флюсов для дуговой сварки под флюсом. Это соответствует стандарту Американского общества сварки. Электроды из углеродистой стали и флюсы для дуговой сварки под флюсом.Таким образом, можно назначить флюсы для использования с различными электродами для обеспечения желаемого анализа наплавленного металла шва.
Ссылки для SAW
Процесс дуговой сварки под флюсом
Зависимость постоянного тока от постоянного напряжения на выходе
У меня дома есть небольшой сварщик MIG. Я хочу использовать его для сварки штангой, но мне сказали, что я не могу. Почему это? В работе у нас есть несколько разных типов сварочных аппаратов. Почему некоторые из них могут использоваться только для сварки штучной сваркой, а некоторые — только для сварки проволокой, а другие аппараты могут использоваться и для того, и для другого? Я слышал термины CC и CV, но что они означают и почему они важны? Наконец, у нашей компании есть несколько переносных механизмов подачи проволоки с переключателем «CV / CC» внутри них.Значит ли это, что их можно использовать с любым сварочным аппаратом?
Это очень хорошие вопросы, и я уверен, что их задавали многие сварщики. С точки зрения конструкции и управления дугой существует два принципиально разных типа источников сварочного тока. К ним относятся источники питания, вырабатывающие на выходе постоянный ток (CC), и источники питания, которые производят постоянное выходное напряжение (CV). Многопроцессорные источники питания — это те, которые содержат дополнительные схемы и компоненты, которые позволяют им выдавать как CC, так и CV выход в зависимости от выбранного режима.
Обратите внимание, что сварочная дуга является динамической, в которой ток (A) и напряжение (V) постоянно меняются. Источник питания отслеживает дугу и вносит изменения в миллисекунды, чтобы поддерживать стабильное состояние дуги. Термин «постоянный» относителен. Источник питания CC будет поддерживать ток на относительно постоянном уровне, несмотря на довольно большие изменения напряжения, в то время как источник питания CV будет поддерживать напряжение на относительно постоянном уровне, независимо от довольно больших изменений тока. Рисунок 1 содержит графики типичных выходных кривых источников питания постоянного и постоянного тока. Обратите внимание, что в различных рабочих точках кривой выхода на каждом графике наблюдается относительно небольшое изменение одной переменной и довольно большие изменения другой переменной («Δ» (дельта) = разница).
Рисунок 1: Выходные кривые для источников питания постоянного и постоянного тока |
Также следует отметить, что в этой статье обсуждаются только обычные типы источников сварочного тока.При импульсной сварке с использованием многих новых источников питания с технологией управления формой волны вы действительно не можете рассматривать выход как строго CC или CV. Скорее, источники питания отслеживают и изменяют напряжение и ток с чрезвычайно высокой скоростью (намного быстрее, чем источники питания с традиционной технологией), чтобы обеспечить очень стабильные условия дуговой сварки.
Прежде чем обсуждать вопрос о CC и CV, мы должны сначала понять эффекты как тока, так и напряжения при дуговой сварке.Ток влияет на скорость плавления или скорость расхода электрода, будь то стержневой электрод или проволочный электрод. Чем выше уровень тока, тем быстрее плавится электрод или тем выше скорость плавления, измеряемая в фунтах в час (фунт / час) или килограммах в час (кг / час). Чем ниже ток, тем ниже становится скорость плавления электрода. Напряжение регулирует длину сварочной дуги, а также ширину и объем дугового конуса. По мере увеличения напряжения длина дуги становится больше (и конус дуги шире), а по мере ее уменьшения длина дуги становится короче (и конус дуги уже). На рисунке 2 показано влияние напряжения на дугу.
Рисунок 2: Влияние напряжения дуги |
Теперь тип используемого сварочного процесса и связанный с ним уровень автоматизации определяют, какой тип сварочной мощности является наиболее стабильным и, следовательно, предпочтительным. Процессы дуговой сварки защищенного металла (SMAW) (также известные как MMAW или Stick) и газо-вольфрамовая дуговая сварка (GTAW) (также известные как TIG) обычно считаются ручными процессами.Это означает, что вы управляете всеми параметрами сварки вручную. Вы держите электрододержатель или горелку TIG в руке и вручную управляете углом перемещения, рабочим углом, скоростью перемещения, длиной дуги и скоростью подачи электрода в соединение. В процессах SMAW и GTAW (т. Е. Ручных процессах) CC является предпочтительным типом выхода от источника питания.
И наоборот, процесс газовой дуговой сварки (GMAW) (он же MIG) и процесс дуговой сварки порошковой проволокой (FCAW) (он же флюсовый сердечник) обычно считаются полуавтоматическими процессами.Это означает, что вы по-прежнему держите сварочный пистолет в руке и вручную контролируете угол перемещения, рабочий угол, скорость перемещения и расстояние между контактным наконечником и рабочим расстоянием (CTWD). Однако скорость подачи электрода в соединение (известная как скорость подачи проволоки (WFS)) автоматически регулируется устройством подачи проволоки с постоянной скоростью. Для процессов GMAW и FCAW (то есть полуавтоматических процессов) предпочтительным выходом является CV.
Таблица 1 содержит сводную информацию о рекомендуемых типах вывода по процессу сварки.
Таблица 1: Рекомендуемый тип выхода источника питания для процесса дуговой сварки |
Чтобы использовать более простую конструкцию и снизить затраты на закупку, источники сварочного тока обычно предназначены для использования только с одним или двумя типами сварочных процессов. Таким образом, базовая машина для стержневой сварки будет иметь мощность только CC, поскольку она предназначена только для сварки стержнем.Аппарат TIG также будет иметь выход только CC, так как он предназначен только для сварки TIG и электродной сварки. И наоборот, базовая машина MIG будет иметь только выходное напряжение CV, поскольку она предназначена только для сварки MIG и сердечника под флюсом. Что касается вашего первого вопроса: «Почему я не могу выполнять сварку при помощи сварочного шва на моем аппарате MIG», ответ заключается в том, что ваш аппарат MIG имеет только выходное напряжение CV, что не предназначено или не рекомендуется для сварки сваркой при помощи сварочного шва. И наоборот, вы, как правило, не можете выполнять сварку MIG на ручном станке с выходом CC, потому что это неправильный тип мощности для сварки MIG.Как упоминалось ранее, существуют источники питания для многопроцессорной сварки, которые могут обеспечивать выход как CC, так и CV. Однако они, как правило, более сложные, имеют более высокую производительность, предназначены для промышленного применения и не имеют цены в базовом ценовом диапазоне сварочных аппаратов начального уровня. На рис. 3 показаны примеры типичных сварочных аппаратов CC, CV и многопроцессорных сварочных аппаратов.
Рисунок 3: Пример источников сварочного тока по типу выхода |
Вы можете создать сварочную дугу с помощью любого из сварочных процессов на выходе типа CC или CV (если вы можете настроить сварочное оборудование для этого).Однако, когда вы используете предпочтительный тип выхода для каждого соответствующего процесса, условия дуги очень стабильны. Однако, когда вы используете неправильный тип вывода для каждого соответствующего процесса, условия дуги могут быть очень нестабильными. В большинстве случаев они настолько нестабильны, что поддерживать дугу невозможно.
Теперь давайте обсудим, почему эти последние утверждения верны. С помощью двух ручных процессов, SMAW и GTAW, вы контролируете все переменные вручную (вот почему они являются двумя процессами, требующими наибольшего количества навыков оператора).Вам необходимо, чтобы электрод плавился с постоянной скоростью, чтобы вы могли подавать его в соединение с постоянной скоростью. Для этого сварочная мощность должна поддерживать постоянный ток (т. Е. CC), чтобы результирующая скорость плавления была постоянной. Напряжение — менее контролируемая переменная. При ручных процессах очень трудно постоянно поддерживать одну и ту же длину дуги, потому что вы также постоянно вводите электрод в соединение. Напряжение меняется в результате изменения длины дуги.С выходом CC ток — это ваша предварительная установка, регулирующая переменная и напряжение просто измеряются (обычно как среднее значение) во время сварки.
Если вы попытаетесь выполнить сварку методом SMAW, например, используя выходное напряжение CV, ток и итоговая скорость плавления будут слишком сильно отличаться. Когда вы двигались вдоль стыка (пытаясь согласоваться со всеми другими параметрами сварки), электрод плавился бы быстрее, затем с меньшей скоростью, затем с большей скоростью и т. Д. вы вставили электрод в стык.Это невыполнимое условие, поэтому выход CV нежелателен.
Когда вы переключаетесь на полуавтоматический процесс, такой как GMAW или FCAW, что-то меняется. Хотя вы все еще управляете многими параметрами сварки вручную, электрод подается в соединение с постоянной скоростью (в зависимости от конкретной WFS, установленной на механизме подачи проволоки). Теперь вы хотите, чтобы длина дуги была одинаковой. Для этого сварочная мощность должна поддерживать напряжение на постоянном уровне (т.е.е., CV), так что результирующая длина дуги согласована. Ток — менее контролирующая переменная. Он пропорционален WFS или является его результатом. По мере увеличения WFS увеличивается и ток, и наоборот. С выходом CV напряжение и WFS являются вашими предустановками, а управляющие переменные и ток просто измеряются во время сварки.
Если вы попытаетесь выполнить сварку с использованием процессов GMAW или FCAW, используя выход CC, напряжение и результирующая длина дуги будут слишком сильно отличаться. При уменьшении напряжения длина дуги становилась очень короткой, и электрод входил в пластину.Затем по мере увеличения напряжения длина дуги станет очень большой, и электрод сгорит обратно к контактному наконечнику. Электрод будет постоянно вонзаться в пластину, затем гореть обратно к кончику, затем врезаться в пластину и т. Д. Это невыполнимое условие, что делает выход CC нежелательным.
В качестве примечания, также принято полностью автоматизировать процессы сварки GTAW, GMAW и FCAW. В случае полной автоматизации все переменные контролируются машиной и удерживаются под постоянным углом, расстоянием или скоростью.Следовательно, меньше изменений в условиях дуги. Однако предпочтительным типом вывода для автоматизированной GTAW по-прежнему является CC, а для автоматизированных GMAW и FCAW — по-прежнему CV. Пятый распространенный процесс дуговой сварки, сварка под флюсом (SAW) (также известный как поддуговая сварка), также обычно является автоматизированным процессом. Для SAW обычно используется выход CC или CV. Определяющими факторами, определяющими, какой тип вывода является наилучший, обычно являются диаметр электрода, скорость перемещения и размер сварочной ванны. Для полуавтоматической резки SAW предпочтительным типом вывода является CV.
Ваш последний вопрос касался переносных механизмов подачи проволоки (см. Пример на , рис. 4 ). Это оборудование, которое позволяет вам идти вразрез с основными правилами, описанными в этой статье… в некоторой степени. Они предназначены в первую очередь для сварки в полевых условиях и обладают тремя уникальными особенностями по сравнению с традиционными механизмами подачи проволоки в заводских условиях. Во-первых, провод заключен в жесткий пластиковый футляр для лучшей защиты и долговечности в полевых условиях. Во-вторых, им не нужен кабель управления для питания приводного двигателя, а скорее используется провод измерения напряжения от механизма подачи проволоки.Таким образом, подключение выполняется просто, для этого достаточно использовать имеющийся сварочный кабель источника питания (и добавить газовый шланг). В-третьих, они действительно могут работать с источником питания CC, но с ОГРАНИЧЕННЫМ успехом. У них есть тумблер «CC / CV», с помощью которого вы выбираете тип выхода от источника питания.
Когда эти портативные механизмы подачи проволоки впервые появились, теория заключалась в том, что их можно было использовать с большой существующей базой источников питания CC, уже используемых в полевых условиях (в основном, сварочных аппаратов с приводом от двигателя), и, таким образом, теперь дают производителям GMAW и FCAW (т.е. проволочная сварка) возможность. Вместо того, чтобы покупать новый источник питания постоянного тока, им нужно было только получить механизм подачи проволоки. Чтобы компенсировать колебания напряжения, которые вы получаете на выходе CC, эти механизмы подачи проволоки имеют дополнительную схему, которая замедляет реакцию скорости подачи проволоки на изменения напряжения, чтобы помочь стабилизировать дугу (обратите внимание, что на CC скорость подачи проволоки равна больше не является постоянным, а, скорее, постоянно увеличивается и уменьшается в попытке сохранить ток на постоянном выходе).
Рисунок 4: Пример переносного устройства подачи проволоки |
Реальность сварки проволокой с выходом CC состоит в том, что она довольно хорошо работает с одними приложениями и плохо работает с другими. Относительно хорошая стабильность дуги достигается при использовании процесса наплавки флюсом в среде защитного газа (FCAW-G) и процесса GMAW при использовании струйной дуги или импульсной струйной дуги в режиме переноса металла. Тем не менее, стабильность дуги все еще очень неустойчива и неприемлема для самозащитной порошковой проволоки (FCAW-S) и процесса GMAW в режиме передачи металла при коротком замыкании.Хотя напряжение изменяется в зависимости от выхода CC, процессы, которые обычно работают при более высоких напряжениях (например, 24 В или более), такие как FCAW-G и струйная дуга или импульсная дуга MIG со струйным распылением, менее чувствительны к изменениям напряжения, возникающим при выходе CC. Поэтому стабильность дуги очень хорошая. В то время как такие процессы, как короткое замыкание MIG и FCAW-S, которые обычно работают при более низких настройках напряжения (например, 22 В или меньше), более чувствительны к колебаниям напряжения. Поэтому стабильность дуги намного хуже и обычно считается неприемлемой.Другой фактор, связанный с использованием электродов FCAW-S на выходе CC, заключается в том, что чрезмерное напряжение дуги и, как следствие, большая длина дуги, по сути, могут привести к чрезмерному попаданию дуги в атмосферу. Это потенциально может привести к пористости сварного шва и / или резкому снижению ударной вязкости металла шва при низких температурах.
В заключение, выход CV ВСЕГДА рекомендуется для сварки проволокой. Поэтому при использовании этих переносных механизмов подачи проволоки с источником питания с выходом CV используйте его вместо выхода CC.Наконец, хотя выход CC может быть приемлемым для общего назначения FCAW-G, а также для струйной дуги и импульсной сварки MIG со струйной дугой, он не рекомендуется для работы с качеством кода.
Ручная сварка — обзор
3.2 «Производственные дефекты»
Ручная сварка — это метод, требующий значительных навыков и сноровки. При ручной дуговой сварке металлическим электродом (MMA) (рис. 3.2) дуга зажигается между плавящимся электродом и свариваемой деталью. Электродный стержень плавится на кончике дуги, и капли металла падают в сварочную ванну.Таким образом, по мере сварки сварочный электрод становится короче. Сварщик должен поддерживать постоянную длину дуги между заготовкой и концом электрода по мере того, как электрод перемещается по стыку, при этом компенсируя скорость выгорания электрода. При работе с электродом необходима твердая рука, и необходимо надлежащее обучение сварщиков, чтобы добиться удовлетворительных результатов ручной сварки. Дефекты неплавления могут возникать при ручной сварке, особенно в корне шва, где доступ наиболее ограничен и металл шва затвердевает быстрее всего, но неплавление может также возникать между проходами сварного шва (рис.3). Мастерство сварщика влияет на форму, смешение и рябь на поверхности сварного шва, а также на наличие брызг вокруг сварного шва. На поверхности сварочного металла могут оставаться куски сварочного шлака даже после очистки проволочной щеткой между проходами сварного шва, и они могут затем застрять в виде шлаковых включений в стыке, когда более поздние проходы сварного шва накладываются поверх .
Рисунок 3.2. Ручная металлическая дуговая сварка стальной панели.
(© TWI)Рисунок 3.3.Отсутствие дефектов плавления и пористости при многопроходном стыковом шве GMAW углеродисто-марганцевой стали.
(© TWI)Есть несколько причин пористости сварных швов, и это особая проблема для алюминиевых сварных швов. В сталях пористость может быть вызвана недостаточной защитой сварного шва инертным газом, позволяющей атмосферным газам или влаге попадать в сварочную ванну. В алюминиевых сплавах пористость вызвана захваченным водородом, который полностью нерастворим в твердом состоянии; поэтому любая смазка или влага в стыке вызывает пористость.
Эти типы дефектов, которые, как правило, являются результатом плохой квалификации сварщика, обычно известны как дефекты «изготовления». Возможно, что дефекты не могут повлиять на структурную целостность готового сварного шва, но обычно существует ограничение на количество разрешенных дефектов изготовления, поскольку они могут указывать на то, что сварщик не имеет достаточных навыков или опыта в этой конкретной области. сварочный процесс. Когда имеется чрезмерная пористость или отсутствие плавления, несущее поперечное сечение сварного шва может быть значительно уменьшено.Чрезмерный выступ в заглушке сварного шва или чрезмерное проплавление корневого прохода может привести к высокой концентрации напряжений на носке сварного шва. Некоторые дефекты неплавления могут быть достаточно острыми, чтобы вызвать хрупкое разрушение чувствительных сталей, поэтому эти дефекты изготовления нельзя сбрасывать со счетов как незначительные. Пределы допустимого размера дефектов, известные как уровни качества сварных швов, указаны в таких стандартах, как BS EN ISO 5817. В качестве альтернативы их значимость можно оценить с помощью оценки пригодности к эксплуатации, как описано в главе 11.
Механизированные сварочные процессы, основанные на газовой дуговой сварке (сварка GMAW, MIG или MAG), снижают необходимый уровень квалификации сварщика. Электронные элементы управления при сварке MAG самостоятельно регулируют длину сварочной дуги, когда горелка перемещается ближе или дальше от заготовки в руке сварщика. Следовательно, размер полученного сварного шва намного более постоянен, а скорость осаждения расходной проволоки является постоянной, поскольку она постоянно подается из устройства подачи проволоки. Механизированные сварочные швы позволяют достичь более высоких скоростей сварки и, следовательно, в значительной степени заменили сварку стержневым электродом в большинстве видов промышленной ручной сварки сегодня (Рисунок 3.4).
Рисунок 3.4. Механизированная сварка кольцевого шва газопровода с использованием дуговой сварки металлическим газом и системы «жучок на ленте» для обеспечения стабильной сварки.
(© TWI)Для полностью автоматизированных сварочных процессов не требуется ручной сварщик для их выполнения, вместо этого оператор управляет машиной или роботом, который выполняет сварку. Наиболее распространенным примером является сварка под флюсом (SAW), но лазерная сварка, сварка трением с перемешиванием и электронно-лучевая сварка также являются автоматизированными сварочными процессами.Автоматическая сварка полностью исключает квалификацию сварщика как фактор качества сварки и позволяет выполнять непрерывную сварку в течение нескольких часов. Даже в этом случае механизированные и автоматизированные сварочные процессы не могут всегда гарантировать бездефектность сварных швов.
% PDF-1.4 % 340 0 obj> эндобдж xref 340 90 0000000016 00000 н. 0000002826 00000 н. 0000002096 00000 н. 0000002914 00000 н. 0000003252 00000 н. 0000003569 00000 н. 0000003602 00000 н. 0000004125 00000 н. 0000004653 00000 п. 0000005228 00000 н. 0000005289 00000 п. 0000005359 00000 п. 0000005435 00000 н. 0000005490 00000 н. 0000005993 00000 н. 0000006062 00000 н. 0000009766 00000 н. 0000010136 00000 п. 0000012945 00000 п. 0000013242 00000 п. 0000020063 00000 н. 0000020675 00000 п. 0000021367 00000 п. 0000021880 00000 п. 0000021950 00000 п. 0000022591 00000 п. 0000029405 00000 п. 0000029830 00000 н. 0000030406 00000 п. 0000031060 00000 п. 0000031113 00000 п. 0000031291 00000 п. 0000031675 00000 п. 0000031719 00000 п. 0000032348 00000 п. 0000032791 00000 п. 0000032866 00000 п. 0000033261 00000 п. 0000033648 00000 п. 0000033793 00000 п. 0000033923 00000 п. 0000034029 00000 п. 0000042784 00000 н. 0000042965 00000 п. 0000043354 00000 п. 0000043534 00000 п. 0000043941 00000 п. 0000044207 00000 п. 0000044598 00000 п. 0000044724 00000 п. 0000045087 00000 п. 0000046973 00000 п. 0000047217 00000 п. 0000047444 00000 п. 0000047841 00000 п. 0000096187 00000 п. 0000096272 00000 н. 0000096334 00000 п. 0000096413 00000 п. 0000096458 00000 п. 0000097066 00000 п. 0000097085 00000 п. 0000097108 00000 п. 0000097131 00000 п. 0000097153 00000 п. 0000097176 00000 п. 0000097199 00000 п. 0000097237 00000 п. 0000097260 00000 п. 0000097335 00000 п. 0000097410 00000 п. 0000097485 00000 п. 0000097559 00000 п. 0000097593 00000 п. 0000097616 00000 п. 0000097650 00000 п. 0000097673 00000 п. 0000097707 00000 п. 0000097730 00000 п. 0000097764 00000 н. 0000097787 00000 п. 0000097813 00000 п. 0000097839 00000 п. 0000097865 00000 п. 0000097946 00000 п. 0000098050 00000 п. 0000098099 00000 п. 0000098131 00000 п. 0000098157 00000 п. 0000002655 00000 н. трейлер ] >> startxref 0 %% EOF 342 0 obj> поток xb«g`4f`c`h Ȁ
Что такое газовая дуговая сварка металла? (Сварка MIG / Сварка MAG)
Сварка в среде инертного газа (MIG) и сварка в среде активного газа (MAG) — это процессы газовой дуговой сварки (GMAW), в которых используется тепло, создаваемое электрической дугой постоянного тока между плавящимся металлическим электродом и заготовкой, которые плавятся вместе, чтобы создать сварочную ванну, которая предохранители, чтобы сформировать соединение.
Сварка MIG и MAG известна в США как газовая дуговая сварка (GMAW).
Это часть серии часто задаваемых вопросов TWI.
MIG / MAG аналогичен MMA в том, что тепло для сварки создается за счет образования дуги между плавящимся металлическим электродом и заготовкой; электрод плавится, образуя сварной валик. Основное отличие состоит в том, что металлический электрод представляет собой проволоку небольшого диаметра, подаваемую через контактный наконечник от катушки подачи проволоки, а защитный газ подается через сварочную горелку.Поскольку проволока подается непрерывно, ручной процесс иногда называют полуавтоматической сваркой. При сварке MIG и MAG используются газовые баллоны для подачи защитного газа и совместимые присадочные материалы. Например, для сварки алюминия следует использовать алюминиевую проволоку, тогда как для сварки стали методом MIG потребуется подходящая стальная присадочная проволока.
В чем разница между MIG и MAG?
Сварка MIG (металл в инертном газе) — это процесс сварки, при котором между плавящимся проволочным электродом и заготовкой образуется электрическая дуга.В этом процессе в качестве защитного газа используются инертные газы или газовые смеси. Аргон и гелий обычно используются для сварки MIG цветных металлов, таких как алюминий.
Сварка MAG (Metal Active Gas) — это процесс дуговой сварки, при котором между плавящимся проволочным электродом и соединяемым материалом создается электрическая дуга. При сварке MAG используются активные защитные газы, в первую очередь для сварки сталей. Эти защитные газы представляют собой смеси двуокиси углерода, аргона и кислорода.
Примеры этих активных газов включают CO 2 , Ar + от 2 до 5% O 2 , Ar + от 5 до 25% CO 2 и Ar + 10% CO 2 + 5% O 2 .
Единственное различие между MIG и MAG — это тип используемого защитного газа.
Состав защитного газа важен, поскольку он оказывает значительное влияние на стабильность дуги, перенос металла и степень разбрызгивания. Защитный газ также влияет на поведение сварочной ванны, особенно на проплавление и механические свойства сварного соединения.
Режим переноса металла
Способ или режим, в котором металл переходит от присадочной проволоки в сварочную ванну, в значительной степени определяет рабочие характеристики процесса.Существует три основных режима переноса металла:
- Короткое замыкание (перенос погружением)
- Распылительная передача
- Импульсная передача
Короткое замыкание и импульсный перенос металла используются для работы с низким током, тогда как перенос распылением используется только при высоких сварочных токах. При коротком замыкании или переносе «погружением» расплавленный металл, образующийся на кончике проволоки, переносится путем погружения проволоки в сварочную ванну. Это достигается установкой низкого напряжения.Чтобы минимизировать разбрызгивание, необходимо соблюдать осторожность при настройке напряжения и индуктивности в зависимости от скорости подачи проволоки. Индуктивность используется для управления скачком тока, возникающим при погружении проволоки в сварочную ванну.
Для переноса распылением необходимо гораздо более высокое напряжение, чтобы проволока не соприкасалась, то есть не замыкалась, со сварочной ванной. Расплавленный металл на кончике проволоки переходит в сварочную ванну в виде брызг мелких капель (меньше диаметра проволоки).Однако существует минимальный уровень или порог тока, ниже которого капли не будут принудительно выбрасываться через дугу. Если попытаться использовать технику открытой дуги намного ниже порогового уровня тока, слабые силы дуги будут недостаточными для предотвращения образования больших капель на кончике проволоки. Эти капли беспорядочно перемещаются по дуге под действием нормальной силы тяжести. Импульсный режим был разработан как средство стабилизации разомкнутой дуги при низких уровнях тока, то есть ниже порогового уровня, во избежание короткого замыкания и разбрызгивания.Перенос металла методом распыления достигается применением импульсов тока, каждый из которых имеет силу, достаточную для отделения капли.
Обычная сварка MIG / MAG выполняется с использованием источника постоянного напряжения, который обеспечивает стабильную «саморегулирующуюся» дугу. Для импульсной сварки используется источник постоянного напряжения или постоянного тока с обратной связью по напряжению.
Каковы преимущества и недостатки сварки MIG?
СваркаMIG позволяет быстро выполнять сварные швы высокого качества, а из-за отсутствия флюса нет шансов, что шлак попадет в металл шва.Защитный газ защищает дугу, что означает небольшую потерю легирующих элементов и незначительное разбрызгивание сварочного шва. Сварку MIG можно выполнять несколькими способами, включая полуавтоматический и полностью автоматический, и это универсальный процесс, который можно использовать для соединения различных металлов и сплавов.
Недостатки сварки MIG заключаются в том, что ее нельзя выполнять в вертикальном или верхнем положении из-за высокой температуры и текучести сварочной ванны. Кроме того, оборудование, используемое сварщиком MIG, может быть сложным.
Каковы преимущества и недостатки сварки MAG?
Поскольку зона сварки защищена защитным газом, сварка MAG не вызывает окисления. Это быстрый процесс сварки, что означает меньшее тепловое воздействие на окружающий материал. Сварку MAG можно выполнять во всех положениях, что делает ее одним из наиболее широко используемых сварочных процессов.
К недостаткам можно отнести опыт, необходимый для правильного выполнения этого процесса. Сварку MAG нельзя проводить на открытом воздухе, так как сварочный газ необходимо защищать от ветра, а всю ржавчину необходимо удалить с детали до начала сварки.Дуговая сварка порошковой проволокой больше подходит для наружных работ или подводных сварочных швов, которые также можно лучше выполнять с помощью дуговой сварки металлическим электродом в защитных оболочках или дуговой сварки вольфрамовым электродом. Как и во всех электродуговых процессах, необходимо использовать надлежащие PPI и, в частности, средства защиты глаз.
Опыт в области сварки MIG и MAG
TWI имеет значительный опыт в разработке и аттестации процедур сварки MIG / MAG для различных областей применения в промышленности.
СхемаБармалея на 160 ампер.Сварочный инверторный аппарат своими руками. Как я сделал сварочный аппарат своими руками
Сварочный инвертор своими руками собрали сотни мастеров. Как показывает практика, ничего сверхсложного в этом процессе нет. Если у вас есть опыт и желание, вы можете приобрести необходимые запчасти и потратить некоторое время на работу.
Для изготовления устройства необходимо запастись всеми необходимыми деталями и аксессуарами.
Сварочный аппарат трансформаторного типа был настолько громоздким и проблематичным в эксплуатации, что заменившие его тиристорные инверторы быстро приобрели всеобщую популярность.
Дальнейшее развитие технологий изготовления полупроводниковых компонентов позволило создать мощные полевые транзисторы. С их появлением инверторы стали еще легче и компактнее. Улучшенные условия регулирования и стабилизации сварочного тока позволяют легко работать даже новичкам.
Выбор конструкции инвертора
В качестве кейса можно использовать старый компьютерный блок.
Компоновка самодельного сварочного инвертора неоригинальна и похожа на большинство других конструкций.Большинство деталей можно заменить аналогами. Необходимо определиться с габаритами устройства и приступить к изготовлению корпуса при наличии всех основных элементов.
Можно использовать стандартные радиаторы (от старых компьютерных блоков питания или других устройств). Если у вас есть алюминиевая шина толщиной 2-4 мм и шириной более 30 мм, вы можете сделать их самостоятельно. Можно использовать любой вентилятор от старых устройств.
Все габаритные детали должны располагаться на ровной поверхности, возможности подключения смотреть согласно принципиальной схеме.
Затем определите место установки вентилятора, чтобы горячий воздух от одних частей не нагревал другие. В сложной ситуации можно использовать два вентилятора, работающих на выхлопе. Стоимость кулеров невысока, вес также невелик, а надежность всего устройства значительно возрастет.
Самыми крупными и тяжелыми частями являются трансформатор и дроссель для сглаживания пульсаций. Желательно располагать их по центру или симметрично по краям, чтобы их вес не тянул устройство в сторону.Крайне неудобно работать с устройством, носимым на плече и постоянно скользящим вбок во время сварки.
Если все части расположены удовлетворительно, нижняя часть устройства должна быть определена по размеру и вырезана из имеющегося материала. Материал должен быть токонепроводящим, обычно используют гетинакс, стекловолокно. При отсутствии этих материалов можно использовать древесину, обработанную антипиренами и для защиты от влаги. Последний вариант в чем-то имеет свои преимущества.Для крепления деталей можно использовать винты, а не резьбовые соединения. Это несколько упростит и удешевит производственный процесс.
Электросхема инвертора
Все инверторы имеют аналогичную структурную схему:
- входной диодный мост, преобразующий переменное напряжение сети в постоянное;
- преобразователь постоянного тока в переменный высокочастотный;
- устройство для понижения высокочастотного напряжения до рабочего;
- Преобразователь постоянного напряжения с фильтром сглаживания пульсаций.
Схема, выбранная для домашнего изготовления, устроена по классической методике. Сердце схемы — наклонный мост, обеспечивающий наилучшие характеристики при максимальной простоте и стоимости. Цепь питания управляется контроллером TL494. Функции управления и регулирования сварочного тока выполняет микроконтроллер PIC16F628. Также через него реализована защита устройства от перегрева. В зависимости от максимального тока и используемых деталей возможны несколько версий прошивки устройства с разным максимально допустимым сварочным током.
Блок питания логических элементов схемы и низковольтной аппаратуры построен на базе ШИМ-контроллера TNY264.
Принципиальная схема, несмотря на большое количество элементов, довольно проста в изготовлении. Вся система управления сделана на нескольких платах:
- плата элемента питания, два варианта; Выпрямитель
- ;
- две платы управления.
На плате силовых элементов расположены выпрямительные диоды со схемами защиты, силовые транзисторы, трансформатор, измерительное сопротивление.Требуемый вариант платы нужно выбирать в соответствии с имеющимися компонентами для сварочного инвертора.
Для инверторного устройства требуется плата управления мощностью.
На плате выпрямителя расположены мостовые элементы, сглаживающие конденсаторы, реле плавного пуска, сопротивления, компенсирующие изменение параметров от температуры (термисторы).
Платы управления питанием содержат следующие цепи:
- ШИМ-контроллер с элементами развязки оптопары; Цифровой индикатор
- с кнопками управления;
- элементов питания;
- микроконтроллер.
Перед сборкой плат дорожки для установки силовых элементов необходимо армировать медным проводом сечением 2,5-4 мм. Для лужения дорожек желательно использовать тугоплавкий припой.
Трансформатор и дроссель для инвертора
При изготовлении сердечника для трансформатора сварочного инвертора можно использовать линейные трансформаторы от старых телевизоров. Потребуется шесть трансформаторов типа ТВС110ПЦ15.У. Снимите зажимную скобу с трансформаторов (открутите две гайки M3 и снимите скобу).Обмотку можно разрезать с обеих сторон ножовкой по металлу или болгаркой, соблюдая необходимые меры предосторожности. Если после снятия обмотки сердечник не распадается на две части, нужно зажать его в тисках и разделить легким ударом. Поверхности деталей необходимо очистить от эпоксидной смолы. После подготовки магнитопроводов нужно сделать каркас. Оптимальным материалом для каркаса будет стекловолокно толщиной 1-2 мм, но можно использовать гетинакс или картон. Технические характеристики магнитопровода в сборе:
Трансформаторы можно позаимствовать у старого телевизора.
- средняя длина магнитной линии kp = 182 мм;
- размеры окна S 0 = 6,2 см 2;
- сечение магнитопровода S м = 11,7 см 2;
- коэрцитивная сила H c = 12 А / м;
- остаточная магнитная индукция B g = 0,1 Тл;
- магнитная индукция B s = 0,45 Тл (если H = 800 А / м), B m = 0,33 Тл (если H = 100 А / м и t = 60 ° C).
Сечение и количество витков обмоток следует рассчитывать исходя из максимально допустимого рабочего тока устройства.
Обмотки следует располагать по всей ширине окна, чтобы уменьшить потери на накладных расходах.
В качестве материала обмоток для устранения скин-эффекта можно использовать медную фольгу или лицевую проволоку нужного сечения. Изоляционным материалом между слоями и обмотками может быть вощеная бумага, лакированное полотно, ФУМ-лента.
Если необходимо контролировать сварочный ток, можно изготовить трансформатор тока. Для его изготовления вам потребуются два кольца типа К30х18х7.Им нужно намотать в лаковой изоляции 85 витков медной проволоки сечением 0,2-0,5 мм. Кольцо надевается на любой из выходных проводов устройства.
Использование инвертора в трехфазной сети
Иногда при перегрузке сети не хватает мощности для нормальной работы инвертора. По возможности однофазный инвертор можно преобразовать в трехфазный.
При подключении к однофазной сети (вилка вставлена в розетку) пускатель К1 включается.Одна пара его контактов соединяет провода, идущие от вилки к штатному выключателю (вкл / выкл) инвертора. Другая пара соединит отрезанные дорожки печатной платы от автоматического выключателя со стационарным выпрямителем.
Пускатель К1 должен иметь контакты с максимально допустимым током не менее 25 А.
Для подачи напряжения от трехфазного выпрямителя используется пускатель К2. Максимально допустимый ток его контактов должен быть не менее 10А. Для подключения к трехфазной сети желательно использовать розетку 3p + N + E (три фазных провода, нейтраль и земля).Устройство может быть встроено в инвертор или изготовлено как отдельный блок. Изготовление отдельной единицы оптимально при работе на одном месте. При частых движениях переносить два устройства неудобно.
Заключение по теме
Сделать сварочный инвертор своими руками не так уж и сложно. При недостатке опыта всегда можно проконсультироваться со специалистами.
В результате вы можете получить отличное устройство с дополнительными функциями, недоступными в коммерческих инверторах.
Ремонт поделки не создаст особых проблем, а пользоваться инструментом в работе будет приятно.
Сегодня широко используемым сварочным аппаратом является сварочный инвертор. Его преимущества — функциональность и производительность. Сварочный мини-аппарат своими руками можно сделать без особых денег (потратившись только на расходные материалы), если иметь представление о том, как устроена и работает электроника. Хорошие инверторы сегодня дороги, а дешевые инверторы могут расстраивать из-за низкого качества сварки.Перед тем как самому построить такой инструмент, необходимо внимательно изучить схему.
Все компоненты устройства должны быть установлены на основании. Для его изготовления подойдет пластина гетинакс толщиной ½ см. Вырежьте в центре пластины круглое отверстие для вентилятора, которое нужно будет защитить решеткой. Между проводами должно быть воздушное пространство.
На переднюю часть базы нужно вывести светодиоды, резистор и ручки тумблера, кабельные зажимы. Весь этот механизм должен быть снабжен сверху «кожухом», для изготовления которого подойдет винилпласт или текстолит (толщиной не менее 4 мм).На электрододержателе устанавливается кнопка, которая вместе с подключенным кабелем должна быть хорошо изолирована.
Сам процесс сборки не такой уж и сложный. Самым важным этапом является настройка сварочного инвертора. Иногда для этого требуется помощь мастера.
- Инвертор необходим для начала. Подключите источник питания 15В к ШИМ , одновременно подключив к источнику питания один конвектор, чтобы снизить тепловую мощность устройства и сделать его работу тише.
- Чтобы замкнуть резистор, нужно подключить реле … Подключается, когда заряд конденсаторов закончился. Такая процедура значительно снижает колебания напряжения при подключении инвертора к сети 220 В. Если резистор не используется при прямом подключении, может произойти взрыв.
- Затем проверьте, как срабатывают реле. замыкает резистор через несколько секунд после подключения тока к плате ШИМ. Провести диагностику самой платы на наличие прямоугольных импульсов после срабатывания реле.
- Затем подается питание 15В на мост для проверки его исправности и правильности установки. Сила тока не должна превышать 100 мА. Установите ход на холостой ход.
- Проверить правильность установки фаз трансформатора … Для этого можно использовать двухлучевой осциллограф. Подключите питание к мосту от конденсаторов через лампу 220В 200Вт, перед этим установите частоту ШИМ на 55кГц, подключите осциллограф, посмотрите форму сигнала, убедитесь, что напряжение не поднимается больше 330 В.
- Постепенно увеличивайте ток инвертор с резистором. Обязательно слушайте прибор и наблюдайте за показаниями осциллографа. Нижний ключ не должен подниматься выше 500 В.Стандартный показатель — 340В. При наличии шума IGBT может выйти из строя.
- Начать сварку через 10 секунд … Проверить радиаторы, если холодные, продлить сварку до 20 секунд. Затем вы можете увеличить время сварки до 1 минуты или более.
После использования нескольких электродов трансформатор нагревается. Через 2 минуты вентилятор остынет, и вы снова сможете начать работу.
Для того, чтобы определить частоту устройства, нужно постепенно снижать частоту ШИМ, пока не появится небольшой поворот на нижней клавише IGBT. Зафиксируем этот показатель, разделим на два, к полученной сумме прибавим значение частоты перенасыщения. Итоговой суммой будет рабочая частота колебаний трансформатора.
Мост должен потреблять ток около 150 мА. Свет от лампочки не должен быть ярким, очень яркий свет может указывать на поломку обмотки или ошибки в конструкции моста.
Трансформатор не должен создавать шумовых эффектов. Если они есть, то стоит проверить полярность. Тестовое питание может быть подключено к мосту через какой-нибудь бытовой прибор. Можно использовать чайник мощностью 2200 Вт.
Проводники от ШИМ должны быть короткими, скрученными и удалены от источников помех.
Сборка самодельного сварочного инвертора своими руками на видео
Сделать инвертор своими руками реально даже при отсутствии глубоких знаний в области электротехники и электроники.Для этого нужно просто разобрать принцип работы такого устройства, строго придерживаться готовой схемы. Если начать делать самодельный сварочный аппарат, который по техническим характеристикам практически не будет уступать заводскому аналогу, можно очень хорошо сэкономить.
В том, что сварочный агрегат своими руками заработает качественно, можно не сомневаться. Устройство, собранное по простейшей схеме, позволит готовить с электродами 3,0-5,0 мм, при длине дуги 1 см.
- Ненужным компьютерным блоком может быть монтажный корпус.
- Комплектация сварочного инвертора своими руками неоригинальна, напоминает большинство других самодельных конструкций. Многие элементы можно заменить аналогами. Если у вас есть основные конструктивные детали, вы можете рассчитать оптимальные параметры корпуса и приступить к его изготовлению.
- Подойдут готовые радиаторы от старых устройств, например, блоков питания ПК. Но сделать их можно самостоятельно, если под рукой будет алюминиевая рейка, толщина которой от 2 до 4 мм, а ширина более 3 см.Вы можете использовать вентилятор от любого старого устройства.
- Все крупные детали рекомендуется изначально разложить на плоскости, чтобы можно было четко определить возможности подключения по схеме.
- Далее нужно определиться с местом для вентилятора. Он не должен гнать поток горячего воздуха от одного элемента устройства к другому. Если в этой ситуации возникнут трудности, то можно использовать одновременно несколько вентиляторов, которые будут работать на вытяжке. Цена кулеров, их вес незначительны, но надежность агрегата в целом значительно возрастет.
- Основными конструктивными элементами самодельного сварочного полуавтомата, крупными и тяжелыми, являются дроссель и трансформатор. Рекомендуется размещать их по краям (симметрично друг другу) или по центру. То есть их масса не должна тянуть машину в сторону. Например, довольно неудобно работать с установкой, подвешенной на ремне через плечо сварщика, когда она будет постоянно скользить в одном направлении.
- После того, как все детали от сварочного инвертора будут расставлены на свои места, необходимо определить параметры днища агрегата, вырезанного из имеющегося материала, который должен быть непроводящим. Чаще всего для этих целей используют стеклопластик, гетинакс. Если этого материала нет в наличии, то подойдет обычная древесина, предварительно обработанная влагостойкими противопожарными растворами. Крайний вариант даже имеет некоторые преимущества.
- Компонентами крепежа обычно являются винты, что упрощает и удешевляет сборку изделия.
Самодельная сварка: материалы для изготовления, основные характеристики
Собрав сварочный полуавтоматический инвертор по стандартной простой электрической схеме, вы станете обладателем эффективной установки со следующими эксплуатационными характеристиками:
- напряжение — 220В;
- входной ток — 32А, выходной — 250А.
Схема сварочного оборудования с аналогичными техническими показателями включает следующие детали:
- силовой агрегат;
- силовой агрегат;
- драйверы ключа питания.
Перед сборкой самодельного сварочного аппарата рекомендуется подготовить все комплектующие по схеме, инструмент для сборки. Для такого самодельного изделия вам потребуется:
- набор отверток;
- ножовка по металлу;
- проволока, ленты медные;
- паяльник для соединения частей электронных схем;
- тонкий листовой металл:
- деталей крепежных резьбовых;
- компонентов для формирования электронных схем;
- текстолит;
- термобумага;
- слюда;
- стеклопластик.
Для домашнего использования часто делают инверторы, которые работают от стандартной электросети (220 В). Если есть необходимость, то можно также собрать устройство, которое будет работать от трехфазной сети (380В). Инверторы этого типа имеют свои преимущества, одно из которых — довольно высокий КПД, в отличие от однофазных изделий.
Обмотка трансформатора
Для намотки трансформатора понадобится медная полоса: толщина — 0,3 мм, ширина — 40 мм. Медная проволока подходит для сильного нагрева.Термослой может быть выполнен из бумаги, используемой для кассовых аппаратов или копировального аппарата. Но второй вариант хуже, бумага недостаточно прочная, может порваться.
Лак — лучший из имеющихся изоляционных материалов; желательно использовать минимальный слой. В целях электробезопасности устройство можно разместить в обмотке печатной платы. Напряжение зависит от качества изоляции между обмотками. Длины полосок бумаги должно хватить, чтобы полностью покрыть периметр намотки, и еще должен быть запас не менее 2 см.
Запрещается использовать толстую проволоку, так как работа инверторного сварочного аппарата основана на токах высокой частоты. Если взять такой провод, то его жила при эксплуатации использоваться не будет. В результате трансформатор может перегреться.
Во избежание этого эффекта рекомендуется брать проводник минимальной толщины и большей площади. Поверхность такого типа не перегревается, это эффективный проводник.
При выполнении вторичной обмотки рекомендуется использовать 3 медные полоски, разделенные фторопластовой пластиной.И снова из бумажной кассовой ленты делают термослой. Недостатком этой бумаги является то, что она темнеет после нагрева, но остается прочной.
Вместо медной ленты также можно использовать провод ПЭВ — диаметром не более 0,7 мм. Такой провод имеет большое количество жил — это его главное преимущество. Но этот вариант обмотки намного хуже медного, провода такого типа имеют значительные воздушные зазоры, из-за чего плохо подходят.
При использовании СЭВ конструкция полуавтомата от инвертора имеет четыре обмотки (СЭВ диаметром 0.3 мм):
- первичная обмотка — 100 витков;
- 1-я вторичная обмотка — 15 витков;
- 2-я вторичная обмотка — 15 витков;
- 3-я вторичная обмотка — 20 витков.
Для трансформатора и всей конструкции необходим охлаждающий вентилятор. Для этих целей отлично подойдет кулер системного блока (220В, 0,15А).
Охлаждение
Силовые элементы самодельной схемы сварочного инвертора, сделанной своими руками, значительно нагреваются.Это может привести к быстрым поломкам. Чтобы они не перегревались, помимо радиаторов охлаждения для блоков нужно дополнительно установить вентиляторы.
Если у вас есть вентилятор большой мощности, вы можете только это сделать. В этом случае поток холодного воздуха необходимо направить на силовой трансформатор. При использовании маломощных вентиляторов, например, от старых ПК, их потребуется около шести, три из которых будут охлаждать трансформатор.
Также во избежание перегрева сварочного аппарата своими руками рекомендуется на самом горячем радиаторе установить датчик температуры, который при достижении максимально допустимой температуры сигнализирует об автоматическом отключении.
Для эффективной работы системы вентиляции необходимо правильно установить воздухозаборники в корпусе сварочного агрегата, решетки которых не должны перекрываться.
Настройка
Самодельный сварочный инвертор прост в сборке и не требует значительных капитальных вложений. Но без привлечения специалиста настроить его проблематично. Как сделать и настроить самодельный инвертор самостоятельно?
Инструкции
- Сначала необходимо подать напряжение на плату сварочного агрегата.Блок издаст характерный писк. Сетевое напряжение также должно подаваться на охлаждающий вентилятор, что предотвратит перегрев деталей, и агрегат будет работать более стабильно.
- Когда силовые конденсаторы получили достаточный заряд, необходимо замкнуть токоограничивающий резистор (проверяется работа реле, на резисторе должно быть нулевое напряжение).
Важно — при подключении сварки без токоограничивающего резистора возможен взрыв!
- Использование резистора данного типа значительно снижает броски тока при сварке, подключенной к сети 220 В.
- Наш инструмент вырабатывает ток более 100 А. Этот параметр зависит от конкретной используемой схемы, и вы можете рассчитать его с помощью осциллографа.
- Проверка режима сварки на самодельном блоке управления плазменной резкой. Для этого нужно подключить к выходу усилителя оптопары вольтметр. Для маломощных устройств среднее пиковое напряжение должно быть около 15 В.
- Далее необходимо проверить выходной мост на правильность сборки. Для этого от подходящего блока питания на вход блока подается напряжение 16В.Бездействующий блок потребляет ток около 100 мА, что следует учитывать при проведении контрольных измерений.
- Работу вашего самодельного инвертора можно сравнить с работой промышленного. На обеих обмотках осциллограф измеряет соответствие импульсов друг другу.
- Далее нужно проверить работу. Необходимо изменить напряжение с 16В на 220В, подключив инвертор напрямую к электросети. С помощью осциллографа, подключенного к выходным транзисторам, наблюдаем форму волны, ее соответствие испытаниям при минимальном напряжении.
Инвертор для сварки — довольно востребованный агрегат в любой сфере деятельности: на производстве, дома. А благодаря использованию встроенного регулятора, выпрямителя тока сварочный аппарат инверторного типа позволит добиться наиболее эффективных результатов сварки по сравнению с результатами аналогичных работ на стандартных сварочных аппаратах, на которых установлены трансформаторы из электротехнической стали.
Заключение
Собрать самодельный не представляет особой сложности.Если для этого недостаточно опыта, то всегда можно обратиться к специалистам за дополнительной консультацией. Но в результате можно собрать агрегат с дополнительными функциями, которых лишены заводские аналоги, и существенно сэкономить деньги.
Инверторные сварочные аппаратышироко используются в строительной отрасли благодаря своей высокой производительности и небольшому весу. Однако не каждый может позволить себе такой инструмент. Единственный выход — сделать сварочный инвертор своими руками.Схем подобных устройств в Интернете существует множество. Многие из них сложные и дорогие, но есть и бюджетные модели.
Общие сведения о сварочном инверторе
Традиционные сварочные аппараты имеют довольно низкую цену, простую ремонтопригодность, однако очень существенным недостатком является не только их вес, но и их зависимость от напряжения. Вход электронного счетчика ограничен мощностью от 4 до 5 кВт. Для сварки толстого металла аппарат потребляет значительную мощность и часто становится невозможным выполнение работы.На смену им пришли инверторные сварочные аппараты.
Назначение и особенности функционирования
Применяется для сварки в домашних условиях, а также на предприятиях, около обеспечивает стабильное горение и поддержание сварочной дуги с использованием тока высокой частоты (кроме 50 Гц).
Сварочный инвертор — это обычный импульсный источник питания, работа которого основана на следующих принципах:
- Входное напряжение (питание от сети инвертора переменного тока 220 В переменного тока) преобразуется в постоянное.
- Постоянный ток преобразуется в высокочастотный переменный ток.
- Идет процесс преобразования напряжения за счет его уменьшения.
- Выпрямление и преобразование тока для частотно-безопасной сварки.
Благодаря этим моментам уменьшаются вес и габариты аппарата. Чтобы собрать инверторную сварку своими руками, необходимо знать принцип работы этого аппарата.
Принцип работы оборудования
В предыдущих моделях основным элементом был огромный мощный силовой трансформатор, позволяющий получать во вторичной обмотке мощные токи, необходимые для сварки.Для получения такого тока необходимо использовать проволоку большого диаметра, что сказывается на весе сварочного аппарата.
С изобретением импульсного блока питания оказалось проще решить проблему с массой и габаритами, потому что габариты и вес самого трансформатора уменьшаются в несколько десятков и сотен раз. Например, если увеличить частоту в 6 раз, можно уменьшить размер трансформатора но в 3 раза.Это приводит к значительной экономии материала.
Благодаря мощным ключевым транзисторам, используемым в схеме инвертора, переключение происходит с частотой от 50 до 80 кГц. Эти транзисторы работают только при постоянном напряжении.
Как известно из курса физики, для получения постоянного напряжения используется простейший полупроводниковый прибор — диод. Диод пропускает ток в одном направлении, отсекая отрицательные синусоидальные напряжения. Но использование одного диода приводит к большим потерям, поэтому используется группа, состоящая из мощных диодов, которая называется диодным мостом.
На выходе диодного моста получается постоянное пульсирующее напряжение. Конденсаторный фильтр используется для получения нормального постоянного напряжения. После этих преобразований на выходе фильтра появляется постоянное напряжение выше 220 В.
Блок, состоящий из выпрямительного моста и фильтрующих элементов, называется блоком питания (БП).
Блок питания служит источником питания для схемы инвертора. Транзисторы подключены к понижающему трансформатору, который является импульсным и работает на частотах в диапазоне от 50 до 90 кГц.По мощности такой трансформатор примерно такой же, как у его огромного собрата — сварочного силового трансформатора.
Модернизация такого аппарата становится легче, потому что благодаря его габаритам и весу появляются дополнительные возможности повышения устойчивости сварочного аппарата.
Существует огромное количество самодельных сварочных инверторов, схемы которых разнообразны по функционалу и способам установки. Разберем подробно каждую из самодельных моделей.
Изготовление резонансного инвертора
В качестве основы нужно использовать компьютерный блок питания форм-фактора AT, от которого потребуются кулер и радиаторы. Детали берутся из элементарной базы мониторов и телевизоров, в противном случае, если их нет, покупаются на рынке. Все комплектующие невысокие.
Тогда нужно определиться с параметрами инверторной сварки своими руками. Также возможно использование следующих характеристик:
Схема оборудования
Основная часть — задающий генератор собрана на микросхеме SG3524, которая используется во всех источниках бесперебойного питания.Инвертор имеет низкое энергопотребление около 2,5 кВт, что позволяет использовать его в квартире.
Трансформатор должен быть в сборе и сердечниками типа Е42, который используется в старых ламповых мониторах. Для изготовления понадобится около 5 штук таких трансформаторов.
Для дросселя следует использовать другой трансформатор. Остальные элементы индуктивности собраны из сердечника 2000HM. Диоды и транзисторы необходимо устанавливать на радиаторы с КТП-8 или другой термопастой.Напряжение холостого хода составляет примерно 36 В при длине дуги от 4 до 5 мм, что позволяет работать с ней начинающим строителям. Выходные кабели должны быть обернуты ферритовыми трубками или ферритовыми кольцами от источника питания.
Конструктивной особенностью схемы является возникновение максимального тока в обмотке I при резонансе.
Схема 1 — Схема сварочного резонансного инвертора
Благодаря небольшому весу и габаритам появляется возможность модернизировать устройство.
Предотвращение прилипания электрода
В данном случае используется транзистор IRF510, который является полевым. Кроме того, он также обеспечивает плавный пуск и прерывание входа на микросхеме SG3524:
- При высоких температурах срабатывает датчик температуры.
- Отключение тумблером.
- Блокировка при коротком замыкании (коротком замыкании).
Простой сварочный аппарат
Данная модель рассчитана на напряжение 220 В и ток 32А, после преобразования его значение достигнет 280А.Этого значения вполне хватит для прочного шва на расстоянии до 1,5 сантиметра.
Схема и аксессуары
Главный элемент — трансформер, сделать его достаточно сложно, но вполне реально.
Основные данные:
- Состоит из ферритового сердечника (7 × 7 или 8 × 8).
- Первичная обмотка примерно на 100 витков и ее диаметр составляет 0,3 мм.
- Вторичные обмотки — 3 штуки: 15 витков и диаметр проволоки 1 мм; 15 витков — 0.2 мм; 20 витков — 0,35 мм.
- Материалы для трансформатора: медные провода соответствующего диаметра, стекловолокно, текстолит, электротехническая сталь (для железной руды), хлопчатобумажный материал.
Для четкого понимания принципа работы необходимо внимательно изучить схему основных агрегатов.
Рисунок 1 — Блок-схема инверторного сварочного аппарата
Пояснение к схеме:
Блок питания и силовая часть
Блок, состоящий из трансформатора, выпрямителя и фильтра (или системы фильтров), выполнен отдельно от силовой части.
Схема 2 — Принципиальная схема блока питания
Проводники (длиной не более 15 см) для управления затворами транзисторов необходимо припаять ближе к последним, причем проводники соединены попарно между собой, их сечение не играет роли.
Основа блока питания — понижающий трансформатор с сердечником Ø20 × 208 2000 нм, а II обмотка намотана в несколько слоев провода, изоляция которого не повреждена.Намотать вторичную обмотку необходимо следующим образом, изолируя слои: 3 слоя, затем прокладка из фторопласта, затем снова 3 слоя и снова прокладка из фторопласта. Делается это для увеличения сопротивления перегрузке … Затем на II обмотку ставим конденсатор не менее 1000 В.
Для обеспечения циркуляции воздуха между слоями обмоток необходимо на ферритовом сердечнике собрать трансформатор тока, подключенный к плюсу, а его сердечник обернуть термобумагой (кассовой лентой).Присоедините выпрямительные диоды к радиатору.
Схема 3 — Силовая часть инвертора
Инверторный блок и охлаждение
Основным назначением инверторного блока является процесс преобразования постоянного тока в переменный ток высокой частоты. Для этого используются мощные транзисторы, хотя в некоторых случаях можно заменить более мощный на 2 и более транзистора средней мощности.
Неплохое охлаждение — важный элемент всего устройства. Для этого следует использовать кулеры от компьютерной техники, но не следует ограничиваться одним, потому что необходимо обеспечить достаточное охлаждение силовой цепи, радиаторы которой служат для отвода тепла, но это тепло необходимо отводить.Для полной защиты необходимо установить датчик температуры (устанавливается на ТЭН), из-за которого будет отключаться питание от сети.
Пайка, регулировка и проверка работоспособности
Пайка является ключевым моментом, потому что при правильном расположении деталей от этого зависят размер всего изделия и возможность оптимального охлаждения. Диоды и транзисторы установлены противоположно друг другу. Входная цепь рассчитана с запасом около 300 В.
Для настройки функции необходимо подключить широтно-импульсный модулятор к напряжению 15 В для питания кулера. Реле включается вместе с резистором R11 и должно выдавать 150 мА.
После проделанных манипуляций необходимо перейти непосредственно к проверке работоспособности устройства:
Если эта схема показалась очень сложной, то рассмотрим схему очень простого устройства.
Самый простой инверторный сварочный аппарат
Модель данного агрегата очень простая и бюджетная.Его легко собрать благодаря простой принципиальной схеме.
Весь процесс сборки можно разделить на этапы, кроме того, необходимо собрать все детали, материалы:
Схема 4 — Схема простейшего сварочного инвертора своими руками
После сборки устройство должно быть настроено и диагностировано при первом запуске для выявления ошибок в работе.
Настройка инвертора:
Таким образом, можно собрать инвертор для сварки своими руками.Необязательно использовать сложные схемы, ведь радиолюбители нашли лучшее решение в бюджетном варианте. Причем уровень сложности схем варьируется от довольно сложных до простых. Чтобы собрать сварочный инвертор своими руками, необязательно покупать дорогие детали, но можно использовать подручные средства.
Инверторная сварка быстро вошла в рабочее пространство мобильных бригад и индивидуальных дежурных работ. Наличие такого сварочного аппарата также пригодится каждому хозяину в гараже или частном доме.Компактные размеры устройства, небольшой вес и высокие показатели качества шва выгодно выделяют его на фоне больших трансформаторов. К сожалению, магазинная цена не позволяет каждому стать владельцем данной техники. Но для тех, кто умеет работать своими руками, выход есть — это самодельный сварочный инвертор. Какие инструменты и материалы вам понадобятся для его создания? Как собрать основные узлы? Что входит в обслуживание и ремонт самодельного устройства?
Принимая решение создать аппарат из удобных деталей, доступный по цене и пригодный для сварки в домашних условиях или на небольших заказах, вы должны осознавать реальность результата.Сварочный инверторный аппарат своими руками существенно уступает по внешнему виду магазинным аналогам. Для солидного частного предпринимателя, специализирующегося на установке отопления, установке заборов, металлических дверей и других услугах, такой агрегат не будет смотреться авторитетно.
А вот простой сварочный инвертор своими руками отлично подойдет для личных нужд в частном доме, или работы в гараже. Такое устройство сможет потреблять 220В из сети, преобразовывать их в 30В, а силу тока увеличивать до 200А.Этого вполне достаточно для работы с электродами диаметром 3 и 4 мм. Качество шва будет лучше, чем у громоздкого трансформатора, так как переменный ток преобразуется в постоянный, а затем обратно в переменный, но с высокой частотой.
Такие инверторы подходят для сварки забора, ворот, собственного отопления, дверей. С ним удобно носить и даже готовить, повесив на плече. Если новичок усердно потренируется, посмотрит видео и попробует на практике наложить швы, то станет возможно сваривать тонкие листы стали.В дальнейшем можно усовершенствовать схемы сварочных инверторов, добавив к ним механизм подачи проволоки, барабанное крепление и газовые клапаны своими руками, чтобы сделать полуавтомат. Возможна также переделка под аргонную сварку.
Необходимые детали и инструменты
Чтобы создать инверторный сварочный аппарат своими руками, не обойтись без похода в магазин или рынок. Собрать его бесплатно из вещей в гараже совершенно невозможно. Но общая стоимость будет в три раза дешевле, чем покупка готовой продукции.В сварочных аппаратах и их создании используются:
- набор отверток;
- плоскогубцы;
- паяльник для изготовления электрощита;
- сверло, для отверстий под выключатели и вентиляцию;
- ножовка;
- лист металла под кузов;
- болтов и шурупов;
- устройств и кнопок на панели;
- конденсаторов, транзисторов и диодов;
- медная шина для намотки;
- проводов для подключения всех узлов;
- элементов для сердечника;
- изоляционная бумага и изолента;
- кабели силовые и рабочие.
Прежде чем приступить к созданию сварочного инвертора своими руками, схема которого уже должна быть распечатана на бумаге, стоит посмотреть несколько видеороликов от специалистов о пошаговой сборке. Это поможет вам четко увидеть, с чем вам придется столкнуться, и сравнить результат. Далее приводится пошаговая инструкция, как сделать сварочный инвертор своими руками. Допускаются некоторые отклонения и вариации, в зависимости от того, какая мощность устройству нужна на выходе, и какие материалы есть под рукой.
Трансформатор
Электрический компонент инвертора начинается с трансформатора. Он отвечает за понижение напряжения до безопасного для жизни рабочего уровня и повышение тока до значения, способного расплавить металл. В первую очередь нужно выбрать материал для сердцевины. Это могут быть стандартные заводские плиты или самодельный каркас из листового металла. Видео в сети помогает увидеть главный принцип этой конструкции, независимо от используемых опций.
Сварочные трансформаторы лучше наматывать из медной шины, так как оптимальные характеристики — достаточная ширина и малое сечение. Такие параметры позволят использовать все физические ресурсы материала. Но если такой шины нет, то можно использовать провод другого сечения. Все это влияет на степень нагрева изделия при эксплуатации.
Трансформатор намотан вручную и состоит из двух частей: первичной и вторичной обмоток. Для инвертора своими руками подойдет:
- Феррит 7 x 7.Первичная обмотка создается из провода ПЭВ 0,3 мм, который намотан ровно, виток за витком, 100 витков.
- Следующий слой — изоляционная бумага. Подойдет лента от кассы или стеклопластик. Первый сильно темнеет при нагревании, но сохраняет свои свойства.
- Вторичная обмотка применена в несколько уровней. Первый — ПЭВ 1,0 мм за 15 оборотов. Поскольку витков мало, их следует равномерно распределить по всей ширине. Они покрыты лаком и слоем бумаги.
- Второй уровень состоит из ПЭВ 0,2 мм в 15 витков, за которым следует изоляция, аналогичная предыдущим слоям.
- Финальный уровень состоит из ПЭВ 0,35 за 20 ходов. Вы также можете изолировать слои с помощью ленты второго слоя.
Рама
Когда основной элемент инвертора будет создан своими руками, можно приступать к изготовлению корпуса. Можно ориентироваться на ширину трансформера, чтобы он беспрепятственно поместился внутри. Из его размеров стоит рассчитать еще 70% необходимого места для остальных деталей.Защитный кожух может быть собран из стального листа толщиной 0,5 — 1,0 мм. Углы можно приварить, прикрутить болтами, а стороны можно сделать сплошными на гибочном станке (что потребует дополнительных затрат). Для переноски инвертора вам потребуется ручка или зажим для ремня.
При создании корпуса стоит предусмотреть легкий демонтаж и доступ к основным элементам в случае ремонта. На лицевой стороне необходимо проделать отверстия под:
- выключатели тока;
- кнопка включения;
- светодиодов, сигнализирующих о включении;
- разъемы для кабелей.
Инверторы для заводской сварки имеют порошковое покрытие. В домашнем производстве подойдет обычная краска. Традиционные цвета сварочных аппаратов — красный, оранжевый и синий.
Охлаждение
В корпусе необходимо просверлить отверстия для вентиляции. Желательно, чтобы они находились на противоположных сторонах друг напротив друга. Вентилятор тоже нужен. Это может быть кулер от старого компьютера. Его необходимо устанавливать, работая на вытяжку горячего воздуха. Приток холода осуществляется через отверстия.Установите кулер как можно ближе к трансформатору — самому горячему элементу устройства.
Преобразование тока
В схему сварочного инвертора обязательно входит диодный мост. Он отвечает за изменение напряжения на постоянное. Пайка диодов осуществляется по схеме «косой мост». Эти элементы также подвержены нагреву, поэтому их следует устанавливать на радиаторы, имеющиеся в старых системных блоках. Чтобы найти их, вы можете обратиться в мастерские по ремонту компьютеров.
Два радиатора размещены по краям диодного моста. Между ними и диодами необходимо установить прокладки из термопласта или другого изолятора. Выводы направлены на контактные провода транзисторов, которые отвечают за возврат тока в переменный, но с повышенной частотой. Соединяемые вместе провода должны быть длиной 150 мм. Трансформатор и диодный мост рекомендуется разделять внутренней перегородкой.
В схеме инвертора требуются конденсаторы, при последовательном включении. Они отвечают за уменьшение резонанса трансформатора и минимизацию потерь в транзисторах. Последние быстро открываются и медленно закрываются. В этом случае появляются потери тока, которые компенсируют конденсаторы.
Сборка и комплектация
После создания всех компонентов устройства можно переходить к сборке. К основанию прикреплены трансформатор, диодный мост и электронная схема управления.Все провода подключены. На внешней панели закреплены:
- переключатели резисторные;
- кнопка включения;
- световых индикаторов;
- ШИМ-контроллер;
- разъемы для кабелей.
Держатель и зажим для массы лучше покупать готовые, потому что они безопаснее и удобнее. Но возможно изготовление держателя самостоятельно, из стальной проволоки диаметром 6 мм. Когда все детали установлены и подключены, можно приступать к проверке устройства.Измеряется начальное напряжение. При 15В он не должен читать больше 100А. Диодный мост проверяется с помощью осциллографа. После этого временная пригодность к работе проверяется путем наблюдения за отоплением радиаторов отопления.
самостоятельный ремонт
Правильное обслуживание инвертора необходимо для долгой и безотказной работы. Для этого каждые два месяца после снятия кожуха следует производить очистку от пыли. Если устройство перестало работать, вы можете произвести ремонт самостоятельно, посмотрев видео в сети об основных поломках и способах их устранения.
Что проверяется в первую очередь:
- Входное напряжение. Если он отсутствует или недостаточен по размеру, то устройство работать не будет.
- Автоматические выключатели. При скачке сгорают защитные элементы или срабатывает автоматическое отключение.
- Датчик температуры. В случае повреждения блокирует работу последующих узлов.
- Контактные клеммы и соединения под пайку. Размыкание цепи останавливает прохождение тока и рабочие процессы.
Изучив схемы обычных инверторов, и закупив необходимые детали, а также посмотрев обучающие видеоролики, вы сможете собрать качественный сварочный аппарат, который будет очень кстати хорошему хозяину.
Оборудование для контактной сварки: Maine Welding Company
Оборудование для контактной сварки используется в группе сварочных процессов, в которых соединение металлов происходит за счет тепла, полученного в результате сопротивления работы электрическому току, в цепи которого работа является частью, и путем приложения давления. Три фактора, участвующие в сварке сопротивлением, — это количество тока, проходящего через изделие, давление, которое электроды передают изделию, и время, в течение которого ток протекает через изделие.Тепло генерируется при прохождении электрического тока через ток сопротивления, при этом максимальное количество тепла выделяется на соединяемых поверхностях. Давление требуется на протяжении всего цикла сварки, чтобы обеспечить непрерывную электрическую цепь во время работы. Величина используемого тока и период времени связаны с подводимой теплотой, необходимой для преодоления тепловых потерь и повышения температуры металла до температуры сварки. Выбор оборудования для контактной сварки обычно определяется конструкцией стыка, конструкционными материалами, требованиями к качеству, графиками производства и экономическими соображениями.Стандартные аппараты для контактной сварки способны сваривать различные сплавы и компоненты различных размеров. Существует семь основных процессов контактной сварки: контактная контактная сварка, контактная точечная сварка, контактная контактная сварка оплавлением, контактная сварка с высадкой, контактная сварка швом, контактная ударная сварка и контактная высокочастотная сварка.
Основные элементы машин для контактной сварки
Аппарат контактной сварки состоит из трех основных элементов:
- Электрическая цепь со сварочным трансформатором и регулятором тока и вторичная цепь, включая электроды, которые проводят сварочный ток к изделию.
- Механическая система, состоящая из рамы машины и связанных с ней механизмов для удержания работы и приложения сварочного усилия.
- Контрольное оборудование (устройства измерения времени) для определения времени и продолжительности текущего потока. Это оборудование также может контролировать величину тока, а также последовательность и время других частей сварочного цикла.
Электрические операции. Контактные швы выполняются на полуавтоматических или механизированных станках. В полуавтомате сварщик перемещает изделие между электродами и нажимает переключатель, чтобы начать сварку; программист сварки завершает последовательность.В механизированной установке детали автоматически загружаются в машину, затем свариваются и выгружаются без помощи сварщика. Машины для контактной сварки подразделяются на две основные группы в зависимости от их электрического режима: прямая энергия и накопленная энергия. Машины обеих групп могут быть рассчитаны на работу как от однофазной, так и от трехфазной сети.
Точечная сварка
Существует несколько типов аппаратов для точечной сварки, включая коромысло, прессы, переносные и несколько типов.Типичный аппарат для точечной сварки с основными элементами управления для ручного управления показан на рисунке 5-39. В этих машинах электродные губки выдвинуты таким образом, чтобы можно было выполнить сварку на значительном расстоянии от края основного металлического листа. Электроды состоят из медного сплава и собраны таким образом, чтобы в процессе сварки к металлу можно было приложить значительную силу или сжатие.
Тип коромысла. Эти машины по существу состоят из цилиндрического плеча или удлинителя плеча, который передает электродную силу и, в большинстве случаев, сварочный ток.Их легко адаптировать для точечной сварки большинства свариваемых металлов. Путь перемещения верхнего электрода представляет собой дугу вокруг оси плеча. Электроды необходимо располагать так, чтобы оба находились в плоскости осей рупора. Из-за радиального движения верхнего электрода эти аппараты не рекомендуются для выпуклой сварки.
Тип пресса. В аппарате этого типа подвижная сварочная головка движется по прямой линии в направляющих подшипниках или траекториях. Машины прессового типа классифицируются в зависимости от их использования и способа приложения силы.Они могут быть предназначены для точечной сварки, сварки выступами или того и другого. Усилие можно прикладывать с помощью пневматических или гидравлических цилиндров или вручную с помощью небольших стендов.
Переносной тип. Типичный переносной аппарат для точечной сварки состоит из четырех основных блоков: переносного сварочного пистолета или инструмента; сварочный трансформатор и, в некоторых случаях, выпрямитель; электрический контактор и таймер последовательности; и блок кабеля и шланга для передачи энергии и охлаждающей воды между трансформатором и сварочной горелкой. Типичный переносной сварочный пистолет состоит из рамы, пневматического или гидравлического исполнительного цилиндра, рукояток и пускового переключателя.Конструкция пистолета адаптирована к потребностям свариваемого узла.
- Тип многоточечной сварки. Это машины специального назначения, предназначенные для сварки определенной сборки. В них используется ряд трансформаторов. Сила прикладывается непосредственно к электроду через держатель с помощью воздушного или гидравлического цилиндра. Для большинства применений нижний электрод изготовлен из куска твердого медного сплава с одной или несколькими вставками из электродного сплава, которые контактируют с свариваемой деталью. Выравнивающие пистолеты часто используются там, где стандартные электроды необходимы с обеих сторон сварного шва для достижения хорошего теплового баланса, или когда вариации в деталях не позволяют обеспечить постоянный контакт с большим твердым нижним электродом.В конструкциях используется та же основная сварочная горелка, но она установлена на специальной C-образной раме, аналогичной той, что используется для переносной горелки для точечной сварки. Вся сборка может перемещаться при приложении силы электрода к месту сварки.
- При точечной сварке алюминия можно использовать обычные аппараты для точечной сварки, используемые для сварки листового металла. Однако наилучшие результаты достигаются только в том случае, если в эти машины будут внесены определенные усовершенствования. Эти функции включают следующее:
- Способность выдерживать большой ток в течение короткого времени сварки.
- Точный электронный контроль силы тока и продолжительности применения.
- Быстрое отслеживание силы электродов за счет использования антифрикционных подшипников и легких низкоинерционных головок.
- Высокая структурная жесткость рычагов, держателей и плит сварочного аппарата для минимизации прогиба под действием высоких электродных сил, используемых для алюминия, и для уменьшения магнитных отклонений, цикла переменной или двойной силы, позволяющего ковку сварного шва.
- Регулировка крутизны для постепенного увеличения и уменьшения сварочного тока.
- Ток последующего нагрева для более медленного охлаждения сварного шва.
- Хорошее охлаждение электродов класса I для предотвращения захвата или прилипания наконечника. Холодное охлаждение часто бывает полезным.
Проекционная сварка. Матрицы или электроды для выступающей сварки имеют плоские поверхности с большей площадью контакта, чем электроды для точечной сварки. Эффективность этого вида сварки зависит от однородности выступов или выпуклостей на основном металле, с которым контактируют электроды (рис.5-40). Аппарат контактной сварки прессового типа обычно используется для выпуклой сварки. Используются плоские электроды или специальные электроды.
Сварка швов. Аппарат для шовной сварки в принципе аналогичен аппарату для точечной сварки, за исключением того, что используются электроды в форме колеса, а не наконечники электродов, используемые при точечной сварке. Для шовной сварки используются несколько типов машин, которые зависят от требований к обслуживанию. В некоторых машинах работа удерживается в фиксированном положении, и над ней пропускается электрод колесного типа.Переносные аппараты для сварки швов используют этот принцип. В машине для шовной сварки подвижного приспособления электрод неподвижен, а изделие перемещается. Органы управления аппаратом для сварки швов должны обеспечивать последовательное включение и выключение сварочного тока и контроль вращения колеса. Компоненты стандартной машины для сварки швов включают в себя основную раму, в которой размещены сварочный трансформатор и переключатель ответвлений; сварочная головка, состоящая из пневмоцилиндра, плунжера и механизма крепления и привода верхнего электрода; механизм крепления и привода нижнего электрода, если он используется; соединения вторичной цепи; электронное управление и контактор; и колесные электроды.
Сварка оплавлением и оплавлением. Аппараты для сварки оплавлением и осаждением аналогичны по конструкции. Основное различие заключается в движении подвижной плиты во время сварки и механизмах, используемых для передачи движения. Сварка оплавлением методом оплавления обычно предпочтительнее для стыковки компонентов равного поперечного сечения. Сварка с осадкой обычно используется для сварки проволоки, прутка или стержня небольшого поперечного сечения, а также для непрерывного соединения шва в трубе или насосно-компрессорной трубе. Машины для сварки оплавлением обычно имеют гораздо большую мощность, чем машины для сварки с осадкой.Однако оба эти процесса могут выполняться на одном и том же типе машины. Соединяемые металлы служат электродами.
Стандартный аппарат для сварки оплавлением состоит из основной рамы, неподвижной плиты, подвижной плиты, зажимных механизмов и приспособлений, трансформатора, переключателя ответвлений, электрических элементов управления, а также механизма оплавления и осадки. На плитах установлены электроды, которые удерживают детали и проводят к ним сварочный ток.
Сварочные аппаратысостоят из основной рамы, в которой размещены трансформатор и переключатель ответвлений, электроды для удержания деталей и проведения сварочного тока, а также средства для разрушения соединения.Первичный контактор используется для управления сварочным током.
Ударная сварка. В этом процессе для соединения металлов используется тепло дуги, возникающей в результате быстрого разряда электрической энергии. Давление прикладывают постепенно во время или сразу после электрического разряда. Этот процесс аналогичен сварке оплавлением и осаждением. При ударной сварке используются два типа сварочных аппаратов: магнитные и конденсаторные. Установка обычно состоит из модифицированного пресса для контактной сварки со специально разработанным преобразователем, элементами управления и инструментами.
Высокочастотная сварка. Этот процесс соединяет металлы с теплом, выделяемым из-за сопротивления деталей высокочастотному переменному току в диапазоне от 10 000 до 500 000 герц, и быстрое приложение осаждающей силы после завершения нагрева. Процесс полностью автоматизирован и использует оборудование, разработанное специально для этого процесса.
.