Сырье для биогаза | Биогаз в России. Биогазовые установки. Компания Биокомплекс
Сырье для биогазовых установок
Поскольку технологии в настоящее время стремительно шагнули вперед, сырьем для получения биогаза могут стать самые различные отходы органического происхождения. Показатели выхода биогаза из различных видов органического сырья приведены ниже.
Таблица 1. Выход биогаза из органического сырья
Категория сырья | Выход биогаза (м3) из 1 тонны базового сырья |
Коровий навоз | 39-51 |
Навоз КРС, перемешанный с соломой | 70 |
Свиной навоз | 51-87 |
Овечий навоз | 70 |
Птичий помет | 46-93 |
Жировая ткань | 1290 |
Отходы с мясобойни | 240-510 |
ТБО | 180-200 |
Фекалии и сточные воды | 70 |
Послеспиртовая барда | 45-95 |
Биологические отходы производства сахара | 115 |
Силос | 210-410 |
Картофельная ботва | 280-490 |
Свекольный жом | 29-41 |
Свекольная ботва | 75-200 |
Овощные отходы | 330-500 |
Зерно | 390-490 |
Трава | 290-490 |
Глицерин | 390-595 |
Пивная дробина | 39-59 |
Отходы, полученные в процессе уборки ржи | 165 |
Лен и конопля | 360 |
Овсяная солома | 310 |
Клевер | 430-490 |
Молочная сыворотка | 50 |
Кукурузный силос | 250 |
Мука, хлеб | 539 |
Рыбные отходы | 300 |
Навоз КРС
Во всем мире к числу наиболее популярных относят биогазовые установки, предусматривающие использование в качестве базового сырья коровьего навоза. Содержание одной головы КРС позволяет обеспечить в год 6,6–35 т жидкого навоза. Этот объем сырья может быть переработан в 257–1785 м3 биогаза. По параметру теплоты сгорания указанные показатели соответствуют: 193–1339 кубометрам природного газа, 157–1089 кг бензина, 185–1285 кг мазута, 380–2642 кг дров.
Одним из ключевых преимуществ использования коровьего навоза в целях выработки биогаза является наличие в ЖКТ крупного рогатого скота колоний бактерий, вырабатывающих метан. Это означает, что отсутствует необходимость дополнительного внесения микроорганизмов в субстрат, а следовательно, потребность в дополнительных инвестициях. Вместе с тем однородная структура навоза делает возможным применение данного типа сырья в устройствах непрерывного цикла. Производство биогаза будет еще более эффективным при добавлении в ферментируемую биомассу мочи КРС.
Навоз свиней и овец
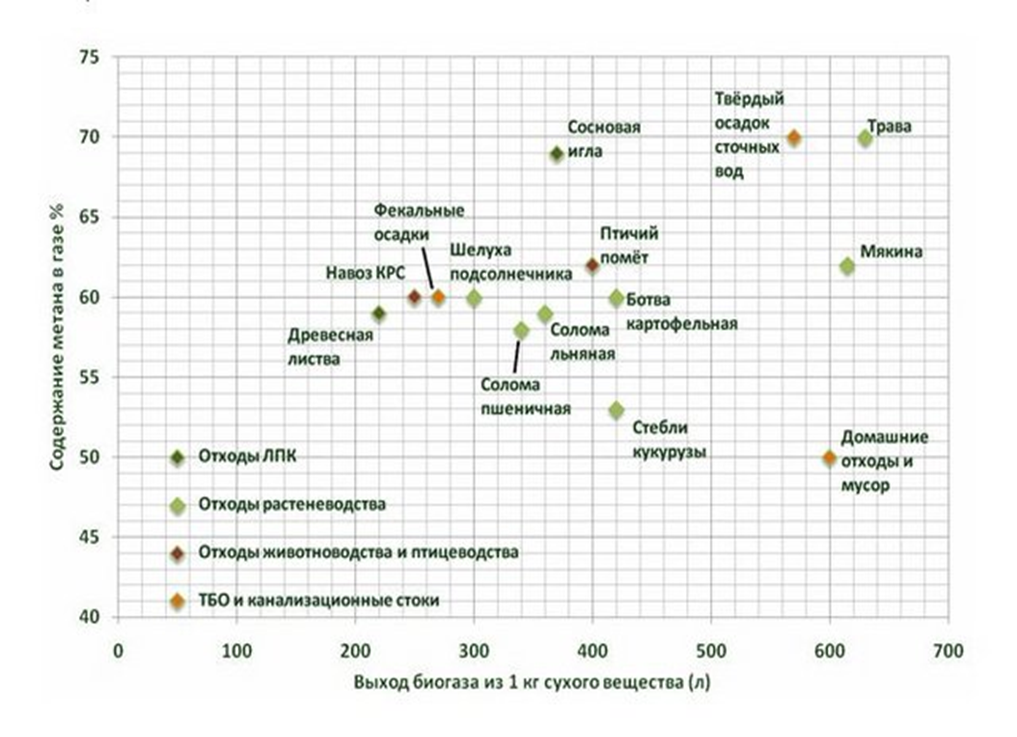
Птичий помет
В целях эффективного применения птичьего помета для получения биогаза рекомендуется оснащать птичьи клетки насестами, поскольку это позволит обеспечить сбор помета в больших объемах. Для получения значительных объемов биогаза следует перемешивать птичий помет с коровьей навозной жижей, что исключит излишнее выделение аммиака из субстрата. Особенностью применения птичьего помета при производстве биогаза является необходимость введения 2-стадийной технологии с использованием реактора гидролиза. Это требуется в целях осуществления контроля над уровнем кислотности, в противном случае бактерии в субстрате могут погибнуть.
Фекалии
Для эффективной переработки фекалий требуется минимизировать объем воды, приходящийся на один санитарный прибор: единовременно он не может превышать 1 л.
С помощью научных исследований последних лет удалось установить, что в биогаз, в случае использования для его производства фекалий, наряду с ключевыми элементами (в частности, метаном) переходит множество опасных соединений, способствующих загрязнению окружающей среды. Например, во время метанового брожения подобного сырья при высоких температурных режимах на станциях биоочистки стоков практически во всех пробах газовой фазы обнаружено около 90 µg/м
Энергетические растительные культуры
Подавляющее большинство зеленых растений обеспечивает исключительно высокий выход биогаза. Множество европейских биогазовых установок функционируют на кукурузном силосе. Это вполне оправданно, поскольку кукурузный силос, полученный с 1 га, позволяет выработать 7800–9100 м3 биогаза, что соответствует: 5850–6825 м3 природного газа, 4758–5551 кг бензина, 5616–6552 кг мазута, 11544–13468 кг дров.
Около 290–490 м3 биогаза дает тонна различных трав, при этом особенно высоким выходом отличается клевер: 430–490м
Следует отметить, что в случае целенаправленного выращивания энергетических культур для производства биогаза существует необходимость инвестирования денежных средств в их посев и уборку. Этим подобные культуры существенно отличаются от иных источников сырья для биореакторов.
«Свалочный газ»
Из тонны сухих ТБО может быть получено до 200 м3 биогаза, свыше 50% объема которого составляет метан. По активности выбросов метана «свалочные полигоны» намного превосходят любые другие источники. Использование ТБО в производстве биогаза не только позволит получить существенный экономический эффект, но и сократит поступление загрязняющих соединений в атмосферу.
Качественные характеристики сырья для получения биогаза
Показатели, характеризующие выход биогаза и концентрацию в нем метана, зависят в том числе от влажности базового сырья. Рекомендуется поддерживать ее на уровне 91% в летний период и 86% в зимний.
Осуществить получение максимальных объемов биогаза из ферментируемых масс можно, обеспечив достаточно высокую активность микроорганизмов. Реализовать эту задачу можно лишь при необходимой вязкости субстрата. Процессы метанового брожения замедляются, если в сырье присутствуют сухие, крупные и твердые элементы. Кроме того, при наличии таких элементов наблюдается образование корки, приводящей к расслоению субстрата и прекращению выхода биогаза. Чтобы исключить подобные явления, перед загрузкой сырьевой массы в биореакторы ее измельчают и осторожно перемешивают.
Оптимальными значениями pH сырья являются параметры, находящиеся в диапазоне 6,6–8,5. Практическая реализация увеличения рН до необходимого уровня обеспечивается посредством дозированного введения в субстрат состава, изготовленного из измельченного мрамора.
В целях обеспечения максимального выхода биогаза большинство различных типов сырья допускается смешивать с другими видами посредством кавитационной переработки субстрата. При этом достигаются оптимальные соотношения углекислого газа и азота: в обрабатываемой биомассе они должны обеспечиваться в пропорции 16 к 10.
Таким образом, при выборе сырья для биогазовых установок имеет смысл уделить его качественным характеристикам самое пристальное внимание.
Содержание метана в биогазе — AgroBiogas
Содержание энергии в биогазе связано непосредственно с содержанием в нем метана. Чем больше метана содержится в биогазе, тем выше его калорийность. При этом, разные виды органического сырья имеют не одинаковое содержание метана, что объясняется, как характеристиками того или иного субстрата, так и используемыми техническими и технологическими решениями на биогазовой станции.
Ориентировочные показатели выхода биогаза из биомассы
Производство биогаза в биогазовых установках имеет много переменных, влияющих на выход биогаза и потенциальное производство энергии из биомассы.
В основном, выход биогаза зависит от состава и соотношения субстратов для биогазового производства. Важным является содержание питательных веществ в субстратах, в частности углеводов, жиров и белков, которые преобразуются микроорганизмами в метантенках биогазовой станции, преимущественно в метан, углекислый газ, воду и кислород.
С другой стороны, важными показателями являются содержание сухого вещества (СВ) и содержание органического сухого вещества (оСВ) в субстрате. Простыми словами: СВ — это свежая масса субстрата без содержания воды, а оСВ — сухое вещество без содержания сырой золы. СВ и оСВ субстратов являются важными факторами влияния на выход биогаза и метана, содержащегося в нем.
Ориентировочные значения содержания энергии и метана в различных субстратах
Приблизительное содержание метана в биогазе находится в пределах 50 — 75%. Содержание метана зависит от ряда факторов, среди которых: собственно тип и вид субстрата для биогазового производства, содержание питательных веществ в субстрате, техническое и технологическое решение биогазовой станции и др.
Энергия, которую можно выработать из биомассы измеряется в стандартных кубических метрах (Нм³) и соответствует примерно 10 киловатт-часам (кВт * ч). В зависимости от содержания метана, отличается и калорийность биогаза и составляет от 5 до 7,5 кВт * ч.
Кроме типа и вида сбраживаемого сырья на выход биогаза влияют такие параметры, как время пребывания субстрата в ферментере, температура сбраживания и подход к эксплуатации биогазовой станции.
Следует отметить, что значения содержания сухого вещества и органического сухого вещества — не постоянные показатели и могут меняться из года в год в зависимости от качества почвы, на которой выращиваются культуры, от погодных условий и т.д., соответственно имеют значительное влияние на выход биогаза.
Ориентировочные показатели выхода биогаза из тонны свежей массы (м³ / т СМ) и содержания метана в процентах некоторых наиболее распространенных в биогазовом производстве субстратов приведены на следующем графике (по данным FNR).
На данном графике представлены только некоторые субстраты для биогазового производства. Биогаз производится практически из любых субстратов органического/биологического происхождения, объединенных в четыре основные группы, а именно:
— биогаз из отходов животноводства (навоз твердый, навоз жидкий, помет)
— биогаз из отходов и остатков растениеводства/агропромышленного комплекса
— биогаз из возобновляемых энергетических культур (кукуруза, сильфий, суданская трава, сорго и т. д.)
— биогаз из компостированных остатков ухода за ландшафтом (листья, газонная трава и т.д.)
В начало
Для того, чтобы определить целесообразность и возможность внедрения технологии метанового брожения того или иного вида органических отходов того или иного предприятия, необходимо знать о биогазовых установках следующее:
Объем биореактора
На территории нашей страны из-за, преимущественно, суровых климатических условий, к сожалению, мы вынуждены признать тот факт, что биогазовые установки с реактором менее 50м3 эффективно работать не будут, т.к. процесс
Назначение биогазовой установки
Основным и единственным назначением биогазовой установки является переработка органических отходов, а точнее, их обеззараживание! Выработка энергии — это лишь приятный бонус, делающий этот процесс менее затратным, а в некоторых случаях, при чрезвычайно больших объемах переработки, способный даже обеспечить некоторые энергетические нужды предприятия. Поэтому эффект лучше считать, исходя из стоимости переработки отходов, и прибыли от реализации удобрений, либо от повышения урожайности собственных полей.
Объем переработки отходов
Максимальный целесообразный суточный объем переработки субстрата (отходы + вода) в БГУ составляет около 20% от физического объема (т.е. объема, который можно загрузить в реактор). Субстрата получается, как правило, в два раза больше, чем отходов, например, фермы крупного рогатого скота. Например, если объем суточного выхода составляет 1 тонну навоза КРС, субстрата получится около 2 тонн и тогда объем реактора биогазовой установки должен быть не меньше 10 м3. Чем меньше влажность исходного сырья, тем больше получится из него субстрата, т.к. влажность, необходимая для эффективного анаэробного процесса очистки от 90-92%.
Материал реактора биогазовой установки
Мы прошли этапы тестирования реакторов из металла и бетона. Мы эксплуатировали в лабораторных условиях реакторы с расположением теплообменника внутри емкости сбраживания. Наши исследования дают серьезные основания сомневаться в возможности использования этих материалов с точки зрения коррозионной стойкости, стойкости к биологическому и химическому разложению (время разложения металлического реактора около 5 лет). Остаются реакторы из нержавеющей стали, но помимо их дороговизны, они обладают еще одним весьма весомым недостатком для эксплуатации в суровых климатических условиях — это существенная способность передавать тепло, столь ценное в сорокоградусные морозы. Стеклопластик, кроме основных проблем, решает вопрос удержания биомассы из-за пористой структуры стенки. Его стоимость вполне оправдана его долговечностью, которая серьезно превышает срок окупаемости.
Сбраживаемые органические отходы
Биогазовая установка способна сбраживать 27 различных видов органических отходов (потенциал приведен в таблице ниже).
Выход биогаза из органического сырья
Категория сырья | Выход биогаза (м3) из 1 тонны базового сырья |
Коровий навоз | 39-51 |
Навоз КРС, перемешанный с соломой | 70 |
Свиной навоз | 51-87 |
Овечий навоз | 70 |
Птичий помет | 46-93 |
Жировая ткань | 1290 |
Отходы с мясобойни | 240-510 |
ТБО | 180-200 |
Фекалии и сточные воды | 70 |
Послеспиртовая барда | 45-95 |
Биологические отходы производства сахара | 115 |
Силос | 210-410 |
Картофельная ботва | 280-490 |
Свекольный жом | 29-41 |
Свекольная ботва | 75-200 |
Овощные отходы | 330-500 |
Зерно | 390-490 |
Трава | 290-490 |
Глицерин | 390-595 |
Пивная дробина | 39-59 |
Отходы, полученные в процессе уборки ржи | 165 |
Лен и конопля | 360 |
Овсяная солома | 310 |
Клевер | 430-490 |
Молочная сыворотка | 50 |
Кукурузный силос | 250 |
Мука, хлеб | 539 |
Рыбные отходы | 300 |
Приведенные в таблице отходы имеют свои особенности при анаэробной биологичской очистке:
Навоз КРС
Во всем мире к числу наиболее популярных относят биогазовые установки, предусматривающие использование в качестве базового сырья коровьего навоза. Содержание одной головы крупного рогатого скота позволяет обеспечить в год 6,6–35 т жидкого навоза. Этот объем сырья может быть переработан в 257–1785 м3биогаза. По параметру теплоты сгорания указанные показатели соответствуют: 193–1339 м3 природного газа, 157–1089 кг бензина, 185–1285 кг мазута, 380–2642 кг дров. Одним из ключевых преимуществ использования коровьего навоза в целях выработки биогаза является наличие в желудочно кишечном тракте крупного рогатого скота колоний бактерий, вырабатывающих метан. Это означает, что отсутствует необходимость дополнительного внесения микроорганизмов в субстрат, а следовательно, потребность в дополнительных инвестициях. Вместе с тем однородная структура навоза делает возможным применение данного типа сырья в устройствах непрерывного цикла. Производство биогаза будет еще более эффективным при добавлении в ферментируемую биомассу мочи КРС.
Навоз свиней и овец
В отличие от КРС, животные этих групп содержатся в помещениях без бетонных полов, поэтому процессы производства биогаза здесь несколько осложняются. Использование навоза свиней и овец в устройствах непрерывного цикла невозможно, допускается лишь его дозированная загрузка. Вместе с сырьевой массой данного типа в биореакторы нередко попадают растительные отходы, что может существенно увеличить период ее обработки.
Птичий помет
В целях эффективного применения птичьего помета для получения биогаза рекомендуется оснащать птичьи клетки насестами, поскольку это позволит обеспечить сбор помета в больших объемах. Для получения значительных объемов биогаза следует перемешивать птичий помет с коровьей навозной жижей, что исключит излишнее выделение аммиака из субстрата. Особенностью применения птичьего помета при производстве биогаза является необходимость введения 2-стадийной технологии с использованием реактора гидролиза. Это требуется в целях осуществления контроля над уровнем кислотности, в противном случае бактерии в субстрате могут погибнуть.
Фекалии
Для эффективной переработки фекалий требуется минимизировать объем воды, приходящийся на один санитарный прибор: единовременно он не может превышать 1 л.
С помощью научных исследований последних лет удалось установить, что в биогаз, в случае использования для его производства фекалий, наряду с ключевыми элементами (в частности, метаном) переходит множество опасных соединений, способствующих загрязнению окружающей среды. Например, во время метанового брожения подобного сырья при высоких температурных режимах на станциях биоочистки стоков практически во всех пробах газовой фазы обнаружено около 90 мг/м3 мышьяка, 80 мг/м3 сурьмы, по 10 мг/м3 ртути, 500 мг/м3 теллура, 900 мг/м3 олова, 700 мг/м3 свинца. Упомянутые элементы представлены тетра- и диметилированными соединениями, свойственными процессам автолиза. Выявленные показатели серьезно превышают ПДК указанных элементов, что свидетельствует о необходимости более обстоятельного подхода к проблеме переработки фекалий в биогаз.
Энергетические растительные культуры
Подавляющее большинство зеленых растений обеспечивает исключительно высокий выход биогаза. Множество европейских биогазовых установок функционируют на кукурузном силосе. Это вполне оправданно, поскольку кукурузный силос, полученный с 1 га, позволяет выработать 7800–9100 м3биогаза, что соответствует: 5850–6825 м3 природного газа, 4758–5551 кг бензина, 5616–6552 кг мазута, 11544–13468 кг дров.
Около 290–490 м3биогаза дает тонна различных трав, при этом особенно высоким выходом отличается клевер: 430–490м3. Тонна качественного сырья картофельной ботвы также способна обеспечить до 490 м3, тонна свекольной ботвы – от 75 до 200 м3, тонна отходов, полученных в процессе уборки ржи, — 165 м3, тонна льна и конопли – 360 м3, тонна овсяной соломы — 310 м3 .
Следует отметить, что в случае целенаправленного выращивания энергетических культур для производства биогаза существует необходимость инвестирования денежных средств в их посев и уборку. Этим подобные культуры существенно отличаются от иных источников сырья для биореакторов. Необходимости в удобрении подобных культур нет. Что касается отходов овощеводства и производства зерновых культур, то их переработка в биогаз имеет исключительно высокую экономическую эффективность.
«Свалочный газ»
Из тонны сухих ТБО может быть получено до 200 м3биогаза, свыше 50% объема которого составляет метан. По активности выбросов метана «свалочные полигоны» намного превосходят любые другие источники. Использование ТБО в производстве биогаза не только позволит получить существенный экономический эффект, но и сократит поступление загрязняющих соединений в атмосферу.
Белгород. Биогаз и биогазовые станции.
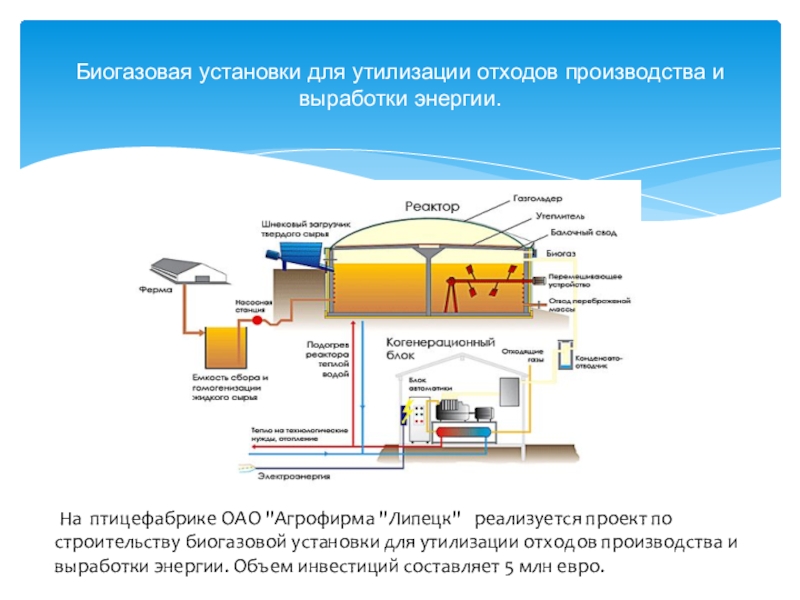
В Белгородской области сконцентрировано большое количество предприятий животноводства и птицеводства, одновременно регион является одним из флагманов российского сельского хозяйства.
В результате деятельности таких предприятий образуется значительное количество органических отходов, необходимость утилизации которых является одной из приоритетных задач по обеспечению экологической безопасности атмосферы и земельных угодий.
За последнее десятилетие в мире получили развитие технологии, позволяющие утилизировать органические отходы, и при этом децентрализовано получать в большом количестве энергию из биоотходов путем переработки их в биогаз с использованием соответствующих технологических решений – биогазовых установок.
Биогаз – газ, получаемый в ходе брожения биомассы (органических отходов) посредством воздействия различных видов бактерий.
Различные виды микроорганизмов метаболизируют углерод из органических субстратов в безкислородных условиях (анаэробно). Этот процесс, называемый гниением или безкислородным брожением, следует за цепью питания. В процессе брожения из биоотходов вырабатывается биогаз. Этот газ может использоваться как обычный природный газ для технологических целей, обогрева, выработки электроэнергии. Его можно накапливать, перекачивать, использовать для заправки автомобиля или продавать соседям.
Биогаз состоит из метана (55-85%) и углекислого газа (15-45%). Плохо растворим в воде, его теплота сгорания составляет от 21 до 27,2 МДж/м³. При переработке 1 т свежих отходов крупного рогатого скота и свиней (при влажности 85%) можно получить от 45 до 60 м³ биогаза, 1 т куриного помета (при влажности 75%) – до 100 м³ биогаза. По теплоте сгорания 1 м³ биогаза эквивалентен: 0,8 м³ природного газа, 0,7 кг мазута, 0,6 кг бензина, 1,5 кг дров (в абсолютно сухом состоянии), 3 кг навозных брикетов.
Для работы электрогенераторов биогаз используется без какой либо очистки. Для заправки автомобилей устанавливается дополнительная система очистки. После такой системы очистки полученный газ — полный аналог природного газа (90% метана (CH4) и 10% углекислого газа (CO2)). Вторым продуктом очистки биогаза является CO2. Этот газ тоже идет в прибыль. Его можно использовать как сухой лед, для газировки или в технических целях.
Биогазовая станция (Биогазовая установка) – это комплекс оборудования по переработке органических отходов с производством удобрений и биогаза, который используется в энергоустановках для выработки электроэнергии и тепла. Работу станции можно разделить на два технологических процесса:
• Анаэробное метановое брожение отходов для получения биогаза.
• Сжигание биогаза в энергетической установке для получения электрической энергии и тепла.
Анаэробное метановое брожение отходов — это разложение биомассы до простейших составляющих с получением метана, двуокиси углерода и воды под воздействием трёх видов бактерий. В цепочке питания последующие бактерии питаются продуктами жизнедеятельности предыдущих. Первый вид — бактерии гидролизные, второй — кислотообразующие, третий — метанообразующие. В производстве биогаза участвуют не только бактерии класса метаногенов, а все три вида.
Этапы процесса брожения биомассы
Для производства биогаза пригодно большинство отходов пищевой промышленности и сельского хозяйства, а также специально выращенные энергетические растения. Биогазовые установки могут работать как на моно-сырье, так и на смеси.
Органические отходы, пригодные для производства биогаза:
• навоз
• птичий помёт
• зерновая и меласная послеспиртовая барда
• пивная дробина
• свекольный жом
• фекальные осадки
• отходы рыбного и забойного цеха (кровь, жир, кишки, каныга)
• трава
• бытовые отходы
• отходы молокозаводов — соленая и сладкая молочная сыворотка
• отходы производства биодизеля — технический глицерин от производства биодизеля из рапса
• отходы от производства соков — жом фруктовый, ягодный, овощной
• виноградная выжимка
• водоросли
• отходы производства крахмала и патоки — мезга и сироп
• отходы переработки картофеля
• производства чипсов — очистки, шкурки, гнилые клубни, кофейная пульпа
Тип сырья |
Выход газа, |
Навоз коровий |
38-52 |
Навоз свиной |
52-88 |
Помет птичий |
47-94 |
Отходы бойни |
250-500 |
Жир |
1300 |
Барда послеспиртовая |
50-100 |
Зерно |
400-500 |
Силос, ботва, трава, водоросли |
200-400 |
Молочная сыворотка |
50-80 |
Свекольный и фруктовый жом |
40-70 |
Глицерин технический |
400-600 |
Дробина пивная |
130-150 |
Таблица. Объемы получаемого биогаза из различных видов исходного сырья
Белгородская область, по состоянию на 2012 год занимает лидирующее место по производству мяса в России:
— Поголовье свиней в сельскохозяйственных организациях оставляет 3305,1 тыс. голов (доля в общероссийском производстве свинины составляет 16,7%);
— Поголовье кур в сельскохозяйственных организациях 46,3 млн. голов (доля в общероссийском производстве мяса птицы составляет 14,9%).
— В сельскохозяйственных организациях и хозяйствах населения Белгородской области более 233 тысяч голов крупного рогатого скота.
Всего в регионе работает более 1000 комплексов по производству мяса птицы и свинины, они производят примерно 15 млн. тонн отходов в год.
Из суммарных отходов птицеводческих и животноводческих предприятий Белгородской области можно в сутки производить свыше 500 тысяч кубометров биогаза.
Масса органических отходов предприятий животноводства
и птицеводства Белгородской области, прогноз до 2015 г., тыс. тонн
(данные – Региональный центр биотехнологий)
Энергетический потенциал |
Всего |
Отходы свиноводства |
Отходы КРС |
Отходы птицеводства |
Отходы сахарного производства |
ТБО и отходы очистных сооружений |
Отходы перерабаты-вающих пред-приятий |
Мощность, МВт |
223,2 |
76,5 |
45,8 |
38,6 |
26,8 |
26,5 |
9,2 |
Электроэнергия, млн. кВт*ч/год |
1766 |
605 |
363 |
306 |
212 |
207 |
73 |
Тепловая энергия, тыс. Гкал/год |
1693 |
580 |
348 |
294 |
203 |
198 |
70 |
Производство удобрений, тыс. тонн/год |
7362 |
2524 |
1511 |
1273 |
885 |
864 |
305 |
Сокращение парниковых выбросов, млн. тонн/год |
1324 |
454 |
272 |
230 |
160 |
155 |
54 |
Энергетический потенциал
объектов биоэнергетики Белгородской области
(данные – Региональный центр биотехнологий)
Также, в результате деятельности сахарных заводов в Белгородской области ежегодно образуется порядка 1,6 млн. тонн побочного продукта производства – жома, который является хорошим органическим сырьем для выработки биогаза и, учитывая его низкую стоимость, позволяет сэкономить на сырье.
При переработке имеющихся в области отходов животноводства, птицеводства, жома свеклосахарного производства, энергетический потенциал региона составит 500 мегаватт, что полностью сможет обеспечить всю сельскую часть области электроэнергией и теплом.
Биомасса (отходы или зеленая масса) периодически подаются с помощью насосной станции или загрузчика в реактор. Реактор представляет собой подогреваемый и утепленный резервуар, оборудованный мешалками. В реакторе живут бактерии, питающиеся биомассой. Продуктом жизнедеятельности бактерий является биогаз. Для поддержания жизни бактерий требуется подача корма, подогрев до 35-38 °С и периодическое перемешивание.
На выходе установки получают два продукта: биогаз и биоудобрения (компостированный и жидкий субстрат).
Образующийся биогаз скапливается в хранилище (газгольдере), затем проходит систему очистки и подается к потребителям (котел или электрогенератор). Реактор работает без доступа воздуха, герметичен и неопасен.
Из газгольдера идет непрерывная подача биогаза в газовый или дизель-газовый теплоэлектрогенератор. Здесь уже производится тепло и электричество. 1м3 газа дает 2кВт*ч электрической и 2кВт*ч тепловой энергии. Крупные биогазовые установки имеют аварийные факельные установки на тот случай, если двигатель/двигатели не работают и биогаз надо сжечь. Газовая система может включать в себя вентилятор, конденсатоотводчик, десульфулизатор и т.п.
Возникающее при производстве электрического тока тепло, подаётся через систему водяного охлаждения или же через систему охлаждения отработанных газов в обогревательную систему. Образующееся избыточное тепло может быть отведено через аварийный охладитель и, при необходимости, использовано в других системах.
Для сбраживания некоторых видов сырья в чистом виде требуется особая двухстадийная технология. Например, птичий помет, спиртовая барда не перерабатываются в биогаз в обычном реакторе. Для переработки такого сырья необходим дополнительно реактор гидролиза. Такой реактор позволяет контролировать уровень кислотности, таким образом бактерии не погибают из-за повышения содержания кислот или щелочей. Возможна переработка этих же субстратов по одностадийной технологии, но при коферментации (смешивании) с другими видами сырья, например, с навозом или силосом.
Переброженная масса – это биоудобрения, готовые к использованию. Жидкие биоудобрения отделяются от твердых с помощью сепаратора и сохраняются в емкости для хранения биоудобрения.
Переработка отходов на биогазовой установке позволяет одновременно получить:
1. газ
2. электричество
3. тепло
4. топливо для автомобилей
5. биоудобрения
Несмотря на отсутствие в РФ «зеленого тарифа» на электроэнергию, произведенную из биомассы, российский рынок биогаза может активно развиваться за счет проектов, направленных на утилизацию разного рода аграрных отходов.
В качестве дополнительного фактора повышенного интереса европейских компаний к российскому рынку биогаза — растущая конкуренция в данном сегменте в странах ЕС.
В Европе биогазовые компании уже начали «толкать» друг друга «локтями», аграрный рынок практически не растет, соответственно спрос на биогазовые проекты снижается. Единственным выходом для европейских компаний является поиск и освоение новых рынков. В данном случае российский рынок может стать для них Клондайком.
Общий потенциал рынка биогаза, а также электро- и теплогенерации на базе биогазовых комплексов, использующих отходы аграрной промышленности, составляет в Российской Федерации более $18,4 млрд. При этом производство биогаза может достичь 14,7 млрд кубометров в год, что является эквивалентом 10 млрд кубометров природного газа.
В России в 2013 году принято постановление правительства «О механизме стимулирования использования возобновляемых источников энергии на оптовом рынке электрической энергии и мощности», направленное на стимулирование использования возобновляемых источников энергии и компенсацию тарифов по такой энергии с целью повышения ее конкурентоспособности. Эта система в будущем может стимулировать развитие сетевой генерации, продажи произведенной из биогаза электроэнергии на оптовом и розничном рынке.
Инвестиционные аспекты использования биогазовых технологий:
Экономические
Существенные экономические выгоды получают все заинтересованные участники сельскохозяйственного и энергетического рынков:
• Инвесторы – срок окупаемости таких проектов составляет порядка 3-5 лет.
• Фермеры, предприятия АПК – снижение экологических платежей, собственная генерация электроэнергии и тепла, высококачественные удобрения.
• Государство – снижение нагрузки на региональный и муниципальный бюджеты, увеличение налоговой базы за счет развития сельскохозяйственных предприятий.
• Российская энергетика – оптимизация энергетического баланса, высвобождение дополнительных объемов природного газа для экспорта на европейские рынки, где цены выше, снижение нагрузки на сети и генерирующие мощности, снижение затрат на развитие и ремонт сетевого хозяйства.
Биогазовые технологии позволяют наиболее рационально и эффективно конвертировать энергию химических связей органических отходов в энергию газообразного топлива (биогаз) собственного производства с получением высокоэффективных органических удобрений. Произведенный биогаз может быть направлен в энергетические установки для выработки электроэнергии и тепла. Поэтому потребность в закупке электроэнергии, тепла, органических удобрений у сторонних производителей отпадает.
Энергетические
Биогаз с высокой эффективностью используется для получения собственной тепловой и электрической энергии. Если весь биогаз будет перерабатываться на когенерационных установках, это полностью обеспечить сельские районы доступом к газу и тепловой мощности. Излишки энергии, а также побочная товарная продукция могут быть реализованы на свободном рынке.
Экологические
Биогазовая станция решает проблему утилизации органических отходов и очистки сточных вод, содержание органических веществ в отходах снижается в 10 раз, также напрямую (за счет переработки) и косвенно (за счет замещения углеводородов в энергобалансе) сокращают выбросы в атмосферу парниковых газов – метана (СН4) и углекислого газа (СО2).
Географические
Биогазовые станции могут быть размещены в любом регионе, где есть достаточное количество органического сырья вне зависимости от наличия объектов традиционной энергетики, инженерных и транспортных сетей.
Инфраструктурные
При наличии сырья, строительство биогазовой станции является отличной альтернативой строительства объектов традиционной энергетики (газопроводов, котельных, электросетей, трансформаторов) и других объектов инфраструктуры (хранилищ отходов, подъездных путей и т.д.). В случае автономной работы отсутствуют затраты на подключение к энергосетям.
Социальные
Биогазовая установка предоставляет возможность обеспечения теплом и электроэнергией объектов социальной инфраструктуры, расположенных поблизости (жилых домов, школ, больниц, детсадов, домов отдыха и т.д.). Развитие биогазовой энергетики также решает проблемы занятости в сельских районах и повышает реальные доходы населения. Кроме этого, внедрение биогазовых технологий способствует развитию энергетической инфраструктуры села, что положительно сказывается на уровне жизни сельского населения.
Инвестиционные проекты в сфере биогазовой индустрии в Белгородской областиВ Белгородской области создана законодательная база развития малой энергетики. В соответствии в Постановлением Правительства Белгородской области №427-пп от 29.10.2012г. утверждена долгосрочная целевая программа «Развитие возобновляемых источников энергии на 2013-2015 годы и на период до 2020 года». Согласно целевым показателям в области планируется введение 223,3 МВт мощностей альтернативной энергетики, в основном за счёт биогазовых станций.
Предусматривается переработка биологических отходов животноводства и птицеводства для производства биогаза и биотоплива.
Для решения этих задач планируется скоординировать работу всех сельскохозяйственных предприятий в нескольких направлениях. В первую очередь, это строительство сети биогазовых установок для переработки органических отходов с влажностью более 50%.
В числе предлагаемых инвестиционных проектов – строительство биогазовых установок на работающих в области свинокомплексах, очистных сооружениях птицефабрик. Компании, которые производят электроэнергию с использованием биотехнологий, будут включены в реестр энергоснабжающих организаций области.
В перспективе, в области намечается обеспечить рациональный, экономически обоснованный рост использования различных видов возобновляемых источников энергии для производства электрической и тепловой энергии, а также расширить использование альтернативных видов топлива для транспорта и энергетики.
Карта – схема
потенциального размещения площадок для биогазовых комплексов
(данные – Региональный центр биотехнологий)
По состоянию на 2013 год Белгородская область газифицирована на 99,8%. Это самый высокий показатель газификации среди российских регионов.
Карта газоснабжения Белгородской области
(источник — ООО «Газпром межрегионгаз Белгород»)
Производственные модели для инвестиционных проектов малой энергетики в Белгородской областиСпециалистами ОАО «Корпорация «Развитие» Белгородской области представлены наиболее выгодные для инвестирования схемы технологических процессов получения альтернативного топлива. В качестве сырья предполагается использование различных органических и бытовых отходов, в том числе побочных продуктов сельскохозяйственных предприятий области.
Использование биогаза в качестве газомоторного топлива
Биогаз представляет собой горючую газовую смесь, состоящую из 50-70% метана (Ch5), которая образуется из органических субстанций в результате анаэробного микробиологического процесса.
Одним из самых наиболее перспективных направлений использования биогаза является его применение в качестве газомоторного топлива.
В качестве сырья для производства биогаза можно использовать любые органические отходы, отходы пищевого производства, животноводства, сельскохозяйственной отрасли, деревоперерабатывающей промышленности, осадки хозяйственно-бытовых сточных вод и прочее сырье, подлежащее ферментации и дальнейшей обработке.
Произведенный биогаз необходимо дополнительно обогатить метаном. Затем полученный биометан можно транспортировать на стационарные или мобильные заправочные станции.
Схема процесса получения биогаза,
используемого в качестве моторного топлива
ПАГЗ — Передвижной автогазозаправщик
АГНКС — Автомобильная газонаполнительная компрессорная станция
Производство RDF-топлива
Одним из наиболее эффективных способов переработки твердых бытовых отходов (ТБО) является производство RDF-топлива (Refuse Derived Fuel (анг.) – топливо, производимое из отходов).
RDF представляет собой топливо, производимое путем измельчения, преобразования и обезвоживания ТБО. RDF состоит в основном из горючих компонентов ТБО, таких как пластик и биоразлагаемые отходы.
Для производства RDF твердые бытовые отходы предварительно поступают на мусоросортировочные комплексы. Полученные в ходе сортировки органические отходы сначала компостируются, а затем направляются на рекультивацию полигонов. На захоронение идет не более 30% отходов.
Получение энергии из RDF является одним из самых экономичных источников энергии. RDF широко используется в цементной промышленности и других отраслях в качестве замены ископаемого топлива и снижает зависимость от него.
Схема процесса вывоза и утилизации мусора с получением RDF-топлива
Модель автономной системы энергосбережения за счет источников малой энергетики на примере одного из районов Белгородской области
Специалистами ООО «Дирекция инвестиционного развития» ОАО «Корпорация «Развитие» на примере одного из районов Белгородской области была сформирована модель автономной системы энергосбережения за счет источников малой энергетики.
В ходе анализа энергобаланса Шебекинского района были рассмотрены объем и структура потребителей рынка энергопотребления. Шебекинский район был разделен на энергосегменты: Шебекино, Муром, Маслова Пристань, Ржевка, Большетроицкое. Общее количество точек поставок по Шебекинскому району составляет 46 664 ед. При этом пиковые мощности равны 59 МВт, а объем потребления — 330 692 МВт*ч. Также по данным филиала ОАО «МРСК-Центра» — «Белгородэнерго» спрогнозирован рост объема потребления на уровне 1,5% (до 335 604 МВт*ч).
Предлагаемая географическая модель строительства объектов генерации Шебекинского района Белгородской области 2013-2018
В ходе анализа ресурсной базы для выработки электроэнергии за счет альтернативных источников рассмотрены отходы животноводства (птицекомплексы, свинокомплексы и фермы КРС), а также сахарных заводов (жом), водоканалов и отходы ТБО на территории Шебекинского района.
Сравнение показателей энергопотребления Шебекинского района Белгородской области в 2012 и 2018 (прогноз) годах
в разрезе структуры объектов генерации
Данные о ВИЭ были разнесены по энергосегментам с проработкой вопроса о типе генерации и мощностях установок. Произведено сравнение объема потребляемой электроэнергии в энергосегменте и энергопотенциале с учетом растительного сырья (на территории конкретного энергосегмента).
Биогазовая установка. Инвестиционная стоимостьВ инвестиционную стоимость биогазовой станции входят следующие основные составляющие:
• Стоимость конструкторской, проектно-сметной и рабочей документации на установку;
• Стоимость и доставка оборудования;
• Стоимость строительно-монтажных работ;
• Стоимость пусконаладочных работ;
• Прочее (разрешения, согласования, обучение персонала, подключения к энергосетям и др.)
Основными инвестиционными затратами при создании биогазовой станции являются затраты на приобретение оборудования и составляют до 60% от общей стоимости проекта. Основными элементами биогазовой станции (БГС) являются:
• Загрузчики твердого (жидкого) сырья
• Ферменторы (метантенки, реакторы)
• Мешалки
• Газгольдеры
• Система смешивания воды и отопления
• Газовая система
• Насосная станция
• Сепараторы
• Приборы контроля
• КИПиА
• Система безопасности
• Когенерационный блок.
Самыми дорогими элементами являются ферменторы из железобетона или стали со специальным покрытием и когенерационный блок (до 70% от общей стоимости оборудования). Стоимость ферментеров зависит от их типа, объема и количества. Стоимость когенерационного блока – от установленной мощности.
Для того чтобы отследить правильные зависимости (объем перерабатываемых отходов и электрическая мощность) между ключевыми элементами установки необходимо обратить более пристальное внимание к самим отходам. Каждый отход характеризуется своими физико-химическими показателями:
• Влажностью
• Содержанием сухого вещества
• Содержанием органического сухого вещества
• Содержанием белков
• Содержанием углеводов
• Содержанием жиров
• рН.
Именно от этих показателей зависит время его сбраживания, количество получаемого биогаза и его состав. Приведем сравнительную таблицу выхода биогаза и его качество (содержание метана) с тонны сырья:
Субстрат |
СВ |
оСВ |
N |
P2O5 |
K2O |
Выход биогаза |
Содержание метана |
Выход метана |
[%] |
[%СВ] |
[%СВ] |
[нм3/т субстрата] |
[% об объема Биогаза] |
[нм3/т оСВ] |
|||
Навозная жижа КРС |
10 |
80 |
3,5 |
1,7 |
6,3 |
25 |
56 |
210 |
Свиные стоки |
6 |
80 |
3,6 |
2,5 |
2,4 |
28 |
61 |
250 |
Навоз КРС |
25 |
80 |
4 |
3,2 |
8,8 |
80 |
55 |
250 |
Птичий помет |
40 |
75 |
18,4 |
14,3 |
13,5 |
140 |
64 |
280 |
Кукурузный силос |
33 |
95 |
2,8 |
1,8 |
4,3 |
200 |
53 |
340 |
Травяной силос |
35 |
90 |
4 |
2,2 |
8,9 |
180 |
54 |
310 |
Свекловичный жом |
24 |
95 |
н.д. |
н.д. |
н.д. |
68 |
72 |
218 |
Чистый жир |
100 |
98 |
н.д. |
н.д. |
н.д. |
1300 |
87 |
1154 |
Из таблицы видно, что для одинакового количества подаваемого субстрата количество и качество получаемого биогаза отличаются в разы и, поскольку, только метан поставляет энергию из биогаза, целесообразно, данные о производстве газа выражать в м3 метана на тонну органического сухого вещества (оСВ), это намного точнее и красноречивее нежели данные в м3 биогаза в м3 свежего субстрата.
При этом количество получаемой электроэнергии зависит от объема и качества биогаза.
Для производства 1 МВтч электроэнергии потребуется либо почти 18 тонн навозной жижи КРС, либо 220 кг чистого жира. Поэтому объем ферментеров для переработки данных видов субстратов будет различаться в десятки раз, что влечет за собой отличие и в их стоимости на аналогичный порядок при одинаковой стоимости когенерационного блока.
Биогазовая паровая котельная .Реализованный проект
В репортаже Екатерины Столповской,
Специалиста по связям со СМИ ОАО «Корпорация «Развитие»
В конце апреля на базе крупнейшего агрохолдинга «Приосколье» была запущена экспериментальная, единственная в Европе паровая котельная, работающая на подстилочно-помётной массе. Оборудование изготовлено и смонтировано российским заводом ООО «Союз» (г. Ковров). Новейшая разработка предприятия позволяет получать при сжигании отходов птицеводства пар, который может быть использован для их технологических нужд, получения электроэнергии и тепла. Кроме того, решается вопрос экологии – помёт больше не нужно складировать на полигонах.
По поручению губернатора Белгородской области специалисты ОАО «Корпорация «Развитие» ознакомились с совместным опытом работы компании «Приосколье» и завода «Союз». Была поставлена задача не только всесторонне изучить новый для России метод утилизации отходов птицефабрик, его рентабельность и эффективность, но и сформировать предложение о возможности его широкого применения в регионе.
— Посетив птицефабрику «Приосколье» и увидев в работе паровой котёл, мы получили ответы на интересующие нас вопросы, — рассказал Андрей Урванов, руководитель направления «Альтернативная энергетика» ОАО Корпорация «Развитие». – Как нам пояснили, проект этот адресный, и пригоден только для тех птицефабрик, где используется напольное содержание птицы. Для более детального обсуждения предложений разработчиков, мы недавно побывали на заводе, где нам представили еще ряд не менее перспективных идей по использованию оборудования для сжигания куриного помета. Так пар при определённом давлении и температуре можно направить на паровую турбину и получить на выходе электричество и тепло. Был также озвучен весьма интересный способ утилизации клеточного помёта, малопригодного для биогазовых станций из-за необходимости нейтрализации азота. Его можно перерабатывать в экологически адаптированное органическое удобрение, обеззараженное от микроорганизмов с помощью тепла, при сохранении полезных органических веществ.
Именно поэтому проект интересен и перспективен для нашего региона – белгородские птицефабрики, производящие в год свыше 700 тысяч тонн мяса птицы, могут полностью перейти на замкнутый цикл, без вреда для себя и окружающей среды. Также агрохолдинги смогут существенно снизить свои расходы на электроэнергию и отопление. А значит, в итоге, и себестоимость продукции. Срок его окупаемости – до трёх лет.
Сейчас анализируются все экономические показатели, запланированы дополнительные исследования в Белгородской сельскохозяйственной академии им. В. Я. Горина. В дальнейшем полученные результаты будут представлены на рассмотрение в Правительство области, и в случае получения одобрения со стороны руководства региона, проект будет рекомендован всем птицеводческим компаниям Белгородской области, а Корпорация займется привлечением инвестиций для его реализации.
Александр Лукьянов,
ведущий аналитик ОАО «Корпорация «Развитие»
Сырьё для получения биогаза
Главная→Биогазовые станции→Сырьё для получения биогаза
Получение биогаза на станциях, которые строит наша корпорация, делает возможным переработка органических отходов от птицефабрик, свиноферм, ферм, специализирующихся на крупнорогатом скоте и других предприятий, в ходе работы которых выбрасывается большое количество органических отходов. В последние годы интерес бизнеса, науки и общественности к экологичным способам утилизации отходов возрос, равно как и интерес к альтернативным источникам энергии, обусловленный ростом цен на традиционные. Остановимся чуть подробнее на сырье, из которого можно изготавливать газ, пригодный для использования в бытовых и промышленных целях. Наша корпорация предлагает оборудование для осуществления этой возможности.
Принято считать, что изготавливается биогаз из навоза, хотя на практике видов сырья, пригодного для выработки биогаза, намного больше. Это может быть навоз (как плотный, так и жидкий), отходы производства пищевой промышленности, пищевые и кормовые остатки, барда, выжимки, биомусор из коммунальных служб и прочие органические отходы. Помимо отходов для производства биогаза могут быть использованы энергетические растения, которые могут быть выращены специально для этих целей. Это кукуруза, зерно, подсолнечник, различные травы, а так же свёкла, силос и так далее.
Некоторые цифры: одна тонна навоза крупного рогатого скота даёт 30-50 м3 биогаза, 60% которого составляет метан, тонна различных видов растений на выходе даст 150-500 м3 биогаза с 70% содержанием метана, а тонна жира после переработки — это 1300 м3 биогаза, 87% которого составляет метан.
Проще говоря, за сутки мы можем получить от одной коровы — 2,5 м3 биогаза, от быка на откорме — 1,6 м3, свиньи — 0,3 м3 и от птицы — 0,02 м3 биогаза.
Важно отметить, что установка по производству биогаза устроена таким образом, что за её пределы не проникнет ни характерное для перерабатываемых отходов зловоние, ни токсичные вещества, которые в других условиях загрязняют атмосферу и приводят к болезням. Получение биогаза из органических отходов – это не только собственный газовый источник. Переработка органических отходов в газ и удобрения с помощью наших биогазовых установок — это в первую очередь экологичный способ избавиться от опасного мусора и извлечь из него не вред, а пользу.
Биогаз — обзор | Темы ScienceDirect
2.55.7 Утилизация биогаза
Биогаз — отличное топливо для большого числа применений [2, 4]. Существует три основных способа использования биогаза, такие как производство тепла и потока, производство / когенерация электроэнергии и использование в качестве автомобильного топлива.
Во всем мире биогаз в основном используется в системах комбинированного производства тепла и электроэнергии (ТЭЦ), в то время как различные страны ЕС инициировали программы по использованию растущего количества биогаза в транспортном секторе, что особенно привлекательно из-за постоянного роста стоимости ископаемое топливо [4, 5].
Обычные газовые горелки можно легко настроить на биогаз, изменив соотношение воздуха и газа. Сжигание биогаза — это устоявшаяся и заслуживающая доверия технология с низкими требованиями к качеству биогаза. Давление обычно должно быть от 10 до 25 мбар. Рекомендуется снизить уровень H 2 S ниже 1000 ppm, чтобы поддерживать точку росы на уровне примерно 150 ° C.
Биогаз также является отличным топливом для ТЭЦ. В основном двигатели внутреннего сгорания используются в когенерационных установках либо в качестве двигателей с искровым зажиганием, либо в качестве двухтопливных.Двухтопливные двигатели, например, с впрыском дизельного топлива (> 10%), хотя и гораздо менее экономичны, очень популярны в меньших масштабах с хорошей энергоэффективностью (до 40%). Они имеют высокие выбросы, если не используется обработка дымовых газов, но позволяют легко запускать, используя только дизельное топливо (при запуске производства биогаза). Двигатели с искровым зажиганием могут быть стехиометрическими двигателями или двигателями с обедненной смесью, последние являются общими для больших размеров и имеют более высокий КПД.
Считается, что топливные элементы станут малой электростанцией будущего, обладающей потенциалом для достижения очень высокого КПД (> 65%) и низкого уровня выбросов.Особый интерес к биогазу вызывают горячие топливные элементы (> 800 ° C), где CO 2 не ингибирует электрохимический процесс, а скорее служит теплоносителем.
Транспортные средства, работающие на газе, могут использовать биогаз в качестве топлива при условии, что он повышен до качества природного газа, и становится возможным его применение на тех же транспортных средствах, которые используют природный газ. Заметно увеличивается количество общественного транспорта, работающего на газе, такого как автобусы и мусоровозы. Большинство газовых индивидуальных автомобилей — это переоборудованные автомобили, которые были оснащены бензобаком в багажном отделении и системой подачи газа в дополнение к обычной бензиновой топливной системе.Специальные газовые автомобили работают с большей эффективностью. Газ хранится под давлением 200–250 бар в резервуарах под давлением из стали или алюминиевых композитных материалов. Транспортные средства, работающие на газе, имеют важные преимущества перед автомобилями, оснащенными дизельными или бензиновыми двигателями, поскольку выбросы CO 2 сокращаются более чем на 95%. Также значительно сокращаются выбросы твердых частиц и сажи. Во всем мире насчитывается более 3 миллионов транспортных средств, работающих на природном газе, и около 10 000 автомобилей и автобусов, работающих на биогазе, что свидетельствует о том, что конфигурация транспортных средств не является проблемой для использования биогаза в качестве автомобильного топлива.Однако требования к качеству газа очень строгие, поэтому неочищенный биогаз из варочного котла необходимо модернизировать.
Наконец, возможна закачка биогаза в газовую сеть, и различные страны ЕС установили стандарты (например, фиксированные пределы для серы, кислорода, твердых частиц и точки росы) для закачки улучшенного биогаза в сеть, чтобы избежать его загрязнения. Методы модернизации должны позволять очищенному биогазу соответствовать этим стандартам качества [4].
Стратегии увеличения производства биогаза за счет анаэробного сбраживания лесного материала — обзор :: BioResources
Мацакас, Л., Rova, U., and Christakopoulos, P. «Стратегии увеличения производства биогаза за счет анаэробного сбраживания лесного материала — обзор», BioRes. 11 (2), 5482-5499.Abstract
Включение биотоплива в существующие виды топлива — очень важная мера для замедления разрушения окружающей среды и противодействия неизбежной нехватке ископаемого топлива. Биогаз — очень интересный вариант для использования как для производства электроэнергии, так и для тепла, а также в качестве топлива для транспортных средств.Положительные топливные характеристики биогаза и высокий выход биогаза, полученного из традиционного сырья (, например, , навоз), привели к эксплуатации нескольких коммерческих установок по всему миру. С другой стороны, существует повышенный спрос на производство биогаза, которое для удовлетворения потребности должно включать в себя возобновляемые ресурсы. Лесные материалы являются интересным кандидатом, и в исследовательских и промышленных кругах растет интерес к их использованию в качестве сырья для анаэробного сбраживания при производстве биогаза.В этой обзорной статье мы стремимся дать читателю представление о самых последних процессах преобразования различных источников лесного сырья в биогаз.
Скачать PDF
Полная статья
Стратегии увеличения производства биогаза за счет анаэробного сбраживания лесных материалов — обзор
Леонидас Мацакас, Ульрика Рова и Пол Христакопулос *
Включение биотоплива в существующие виды топлива — очень важная мера для замедления разрушения окружающей среды и противодействия неизбежной нехватке ископаемого топлива.Биогаз — очень интересный вариант для использования как для производства электроэнергии, так и для тепла, а также в качестве топлива для транспортных средств. Положительные топливные характеристики биогаза и высокий выход биогаза, полученного из традиционного сырья (, например, , навоз), привели к эксплуатации нескольких коммерческих установок по всему миру. С другой стороны, существует повышенный спрос на производство биогаза, которое для удовлетворения потребности должно включать в себя возобновляемые ресурсы. Лесные материалы являются интересным кандидатом, и в исследовательских и промышленных кругах растет интерес к их использованию в качестве сырья для анаэробного сбраживания при производстве биогаза.В этой обзорной статье мы стремимся дать читателю представление о самых последних процессах преобразования различных источников лесного сырья в биогаз.
Ключевые слова: биогаз; Метан; Анаэробное пищеварение; Лесные материалы; Предварительная обработка
Контактная информация: Разработка биохимических процессов, Отдел химической инженерии, Департамент инженерии гражданского строительства, окружающей среды и природных ресурсов, Технологический университет Лулео, Лулео, SE-97187, Швеция; * Автор, ответственный за переписку: пол[email protected]
ВВЕДЕНИЕ
Быстрый рост индустриализации, наблюдавшийся в прошлом веке, вместе с увеличением населения, привел к увеличению потребности в энергии (Matsakas et al. 2014a; Sarris et al. 2014). В настоящее время основным источником энергии являются ископаемые ресурсы (например, нефть) (Matsakas et al. 2014b). Использование ископаемого топлива в качестве источника энергии не только неустойчиво, но также приводит к экологическим проблемам, таким как выброс парниковых газов (ПГ) и других потенциально вредных соединений (Bonturi et al. 2015). Более того, использование ископаемых ресурсов привело к зависимости подавляющего большинства стран от импорта топлива, что может привести к отсутствию энергетической безопасности. Чтобы решить эти проблемы, необходимо использовать новые возобновляемые источники энергии. Эти формы биотоплива предпочтительно производить с использованием технологий, основанных на местном сырье, что приводит к энергетической безопасности и созданию новых рабочих мест, , то есть , что позволяет перейти к экономике, основанной на биологических источниках. Наиболее распространенными видами биотоплива, которые в настоящее время используются, являются жидкое топливо этанол и биодизель, а также газообразное топливо метан.При их производстве очень важно, чтобы используемое сырье не являлось также источниками пищи и не конкурировало с землей, используемой для производства продуктов питания. Использование пищевых ресурсов для производства биотоплива уже подвергалось серьезной критике (Nitsos et al. 2015), так как в прошлом это приводило к росту цен на них.
В основном биогаз используется в качестве автомобильного топлива и для производства электроэнергии (Jeihanipour et al. 2013). Для производства электроэнергии биогаз сжигается в специальном оборудовании, называемом ТЭЦ (комбинированное производство тепла и электроэнергии).С другой стороны, для использования в качестве топлива для транспортных средств биогаз должен быть улучшен путем удаления диоксида углерода (CO 2 ) и других газов (, например, , , сероводорода (H 2 S)), а затем увеличение концентрации метана (CH 4 ), что приводит к увеличению энергоемкости биогаза. Для увеличения содержания метана используются различные методы, такие как химическая адсорбция, активированный уголь, очистка и биологическое окисление (Abatzoglou and Boivin, 2008).Производство биогаза, по данным Европейской ассоциации производителей биомассы (www.eubia.org), в 25 странах ЕС в 2012 г. достигло 12 090 тыс. (1811 тыс. Тнэ) и Италия (1178 тыс. Тнэ). По данным Статистического управления Швеции (scb.se), Швеция уже создала рынок автомобилей на основе биометана с в общей сложности 40 095 автомобилей с гибким топливом на газе / газе в 2014 году; и среди них 8 150 автомобилей, работающих на метановом газе.
Биогаз, как будет обсуждено позже, производится путем анаэробного сбраживания органических материалов. Процесс анаэробного сбраживания положительно влияет на окружающую среду, так как предотвращает выброс органических отходов на свалки. Размещение органических материалов на свалках может привести к неконтролируемому выбросу газов в окружающую среду. Эти газы включают метан, который, как считается, представляет в 20-23 раза более высокий потенциал парниковых газов по сравнению с двуокисью углерода (Browne and Murphy 2013; Zheng et al. 2014). Кроме того, свалки также образуют фильтрат, который приводит к загрязнению подземных вод. Наконец, еще одна положительная характеристика анаэробного пищеварения — образование дигестата. Дигестат — это остающаяся твердая фракция после переваривания, она богата азотом, калием и фосфором и обладает особыми реологическими характеристиками; эти свойства делают его очень эффективным биоудобрением (Liu et al. 2009; Adu-Gyamfi et al. 2012; Kafle et al. 2014).
Биогаз в качестве топлива
Одним из привлекательных преимуществ использования биогаза в качестве автомобильного топлива является то, что он не требует значительных изменений транспортного средства. Технология преобразования бензинового транспортного средства для работы на метане уже проверена, а модификация двигателя с искровым зажиганием проста и может быть выполнена путем добавления второй топливной системы (Aslam et al. 2006). Стоимость этого преобразования варьируется в зависимости от размера и типа транспортного средства, типа двигателя, размера метанобака, затрат на рабочую силу и страны, в которой будет проводиться модификация.Использование биогаза в качестве топлива способствует сокращению выбросов парниковых газов и загрязнения воздуха, поскольку он имеет незначительные выбросы пыли и частиц, практически не выделяет парниковых газов и снижает выбросы соединений серы, окиси углерода, оксидов азота и углеводородов (шведский Газовая ассоциация 2011). Несмотря на очень положительные характеристики биогаза в качестве топлива и тот факт, что более важно использовать произведенный биогаз для автомобильного топлива, а не для производства электроэнергии (поскольку существует широкая доступность «зеленых» альтернатив, таких как энергия ветра и солнца) , только относительно небольшое количество биогаза направляется в транспортный сектор (Naik et al. 2010). С точки зрения ресурсоэффективности считается, что биогаз имеет лучшее соотношение выходной энергии и входящей энергии, чем этанол (Jeihanipour et al. 2013), достигая коэффициента до 28 (Zheng et al. 2014).
Производство и использование любой формы возобновляемой энергии для использования в качестве автомобильного топлива всегда должно конкурировать с ценами на ископаемое топливо ( например, нефть). Примерно с середины 2014 года цены на ископаемое топливо значительно снизились по сравнению с предыдущими годами, и это усилило давление на альтернативные возобновляемые источники энергии.Хотя экономическая ценность топлива является важным фактором, необходимо серьезно рассмотреть другие вопросы. Использование возобновляемых видов топлива очень важно с экологической точки зрения, поскольку оно приводит к снижению выбросов парниковых газов и других загрязнителей воздуха. Более того, использование возобновляемых источников для производства энергии приводит к ее неограниченному запасу, тогда как использование ископаемого топлива столкнется с дефицитом в будущем. Еще одно преимущество производства возобновляемого топлива — это возможность использовать «местное» сырье (например, лесные материалы в Швеции), что будет способствовать развитию местной экономики, а также уменьшит зависимость страны от импорта топлива.
Процесс производства биогаза
Метан — газообразный энергоноситель, который образуется в результате анаэробного разложения органических материалов. Анаэробное сбраживание — это сложный процесс, который включает разложение различных органических молекул (, например, , углеводы, белки и жиры) до метана на разных этапах (Matsakas et al. 2014c). Эти шаги включают начальное разложение сложных молекул (, например, , полисахариды) до простых ( e.грамм. , мономерные сахара) с последующим преобразованием этих простых молекул в различные летучие жирные кислоты (ЛЖК) на стадии ацидогенеза (рис. 1). На следующем этапе (ацетогенез) ЛЖК, которые длиннее, чем уксусная кислота, превращаются в уксусную кислоту, CO 2, и H 2 , а на последнем этапе расщепления ЛЖК превращаются в CH 4 . и CO 2 метаногенами (Adu-Gyamfi et al. 2012). Первый этап производства ЛЖК — более быстрый процесс, чем метаногенез.Если весь процесс становится несбалансированным, может происходить накопление ЛЖК, что приводит к подкислению и последующему ингибированию метаногенеза (Griffin et al. 1998).
Рис. 1. Этапы биологического разложения органических материалов до биогаза
Производство биогаза обычно происходит в психрофильных (<25 ° C), мезофильных (от 25 до 35 ° C) или термофильных условиях (от 45 до 60 ° C) (Liu et al. 2009; Zhou et al. 2012). Как правило, термофильный процесс считается более полезным, поскольку он приводит к более высокой метаногенной активности и, следовательно, к более быстрому процессу, а также предотвращает микробное загрязнение (Lesteur et al. 2010; Xia et al. 2013). Основными материалами, которые используются для анаэробного сбраживания, являются навоз, пищевые отходы и отходы бойни. Анаэробное разложение этих материалов очень эффективно, и уже достигнуты высокие урожаи (Hill and Bolte 2000; Nielsen et al. 2004; Банки и др. 2011; Palatsi et al. 2011; Nagao et al. 2012). Растущий спрос на биогаз привел к необходимости включения новых ресурсов для анаэробного сбраживания. Лигноцеллюлозная биомасса может служить новым возобновляемым материалом во время анаэробного сбраживания.
ЛИГНОЦЕЛЛЮЛОЗНАЯ БИОМАССА
Лигноцеллюлозная биомасса — это богатое возобновляемое сырье, которое можно использовать для производства биотоплива (Xia et al. 2013). Было подсчитано, что годовое производство биомассы может достигать 150 миллиардов тонн органического вещества (из них 100 миллиардов тонн относятся к наземной биомассе и 50 миллиардов тонн водной биомассы) (Naik et al. 2010). Продуктивность образования биомассы (оцененная в сухой беззольной биомассе) составляет от 7,5 до 15 т / га / год (Datta et al. 2011). Источниками дешевой лигноцеллюлозы могут быть лесные остатки, сельскохозяйственные остатки и даже твердые отходы промышленного и бытового секторов (McKendry 2002; Tomás-Pejó et al. 2008 г.). Помимо этого, считается, что биомасса играет очень важную роль в сокращении выбросов CO 2 в атмосфере, поскольку она одновременно действует как резервуар CO 2 , а также заменяет использование ископаемого топлива (Ciubota-Rosie et al. 2008 г.). Подсчитано, что замена всего 5% жидкого ископаемого топлива жидким топливом на основе биомассы может снизить выбросы CO 2 на 0,4 Гт / год (Sridhar and Hill 2011).
Лигноцеллюлоза — это общий термин, используемый для описания основных компонентов, содержащихся в стенках растительных клеток.В основном он состоит из целлюлозы, гемицеллюлозы, лигнина, экстрактивных веществ и неорганических материалов (Taherzadeh and Karimi 2008). Состав основных компонентов (целлюлоза, гемицеллюлоза и лигнин) варьируется в зависимости от источника лигноцеллюлозы, при этом средний состав целлюлозы составляет от 35% до 50%, гемицеллюлозы от 20% до 35% и лигнина от 5% до 30%. (Линд и др. 2002). Целлюлоза представляет собой линейный кристаллический гомополимер β-1,4-D-глюкозы с высокой степенью полимеризации (Taherzadeh and Karimi 2008; Zheng et al. 2014). Из-за природы связей, образующихся между различными цепями, целлюлоза имеет очень стабильную структуру, которую трудно разложить. Различные части целлюлозы имеют разную степень полимеризации и классифицируются как кристаллические или аморфные (Sun et al. 2008). Гемицеллюлоза, с другой стороны, представляет собой гетерополимер, состоящий из пентоз (ксилоза и арабиноза) и гексоз (глюкоза, манноза, рамноза и галактоза) вместе с уроновыми кислотами (глюкуроновая кислота, галактуроновая кислота и метилглюкуроновая кислота) (Zheng и другие. 2014). Гемицеллюлозу легче гидролизовать, чем целлюлозу, и она имеет более низкую степень полимеризации (Saha 2003). Роль гемицеллюлозы заключается в защите целлюлозы от ферментативной деградации. Наконец, лигнин представляет собой сложный гетерополимер, состоящий из фенилпропановых звеньев (таких как синапиловый спирт, p -кумариловый спирт и конифериловый спирт) (Nigam and Singh 2011; Stamatelou et al. 2012). Лигнин отвечает за целостность и структурную жесткость, а также за предотвращение набухания лигноцеллюлоз (Taherzadeh and Karimi 2008; Zheng et al. 2014).
В деревообрабатывающей промышленности (целлюлозно-бумажная промышленность, лесопилки, и т. Д. ) ежегодно производится большое количество остаточной древесной биомассы (Garcìa-Pérez et al. 2007), которая может служить сырьем для анаэробного сбраживания растения. Древесина классифицируется как древесина хвойных и лиственных пород в зависимости от их структуры. Хвойная древесина (характерными представителями которой являются ель и сосна) имеют приблизительный состав от 43% до 45% целлюлозы, от 20% до 23% гемицеллюлозы и 28% лигнина, причем гемицеллюлоза в основном состоит из маннозы (Galbe and Zacchi 2002).С другой стороны, гемицеллюлоза, присутствующая в древесине лиственных пород (, например, , береза и ива), составляет примерно 25% от сухой массы и в основном состоит из ксилозы (Lawford and Rousseau 1991). Хвойные и лиственные породы также демонстрируют различия в структуре лигнина. В частности, лигнин древесины хвойных пород состоит в основном из гваяцильных звеньев, тогда как лигнин лигнина в основном представляет собой смесь гваяцильных и сирингильных звеньев (Taherzadeh and Karimi, 2008).
Необходимость предварительной обработки
Сложная структура лигноцеллюлозы делает ее очень стабильным соединением, которое очень трудно гидролизовать.Как правило, на степень гидролиза целлюлозы влияют разные факторы, включая кристалличность, степень полимеризации, уровни присутствующих гемицеллюлозы и лигнина, степень ацетилирования гемицеллюлозы и количество доступной площади поверхности (Kim and Holtzapple 2006 ; Parawira 2012). Эти факторы отрицательно влияют на степень разложения целлюлозы и гемицеллюлозы, что приводит к очень низким уровням продукта при использовании необработанных лигноцеллюлозных материалов.Чтобы преодолеть эти барьеры, перед любой микробной конверсией необходимо использовать какой-то процесс предварительной обработки (Demirbas 2008; Matsakas and Christakopoulos 2015). Для того чтобы предварительная обработка считалась эффективной, она должна приводить к получению более легко гидролизуемой целлюлозы, низким уровням разложения сахаров и образованию соединений-ингибиторов ―, а также процесс должен иметь низкие эксплуатационные расходы и низкое воздействие на окружающую среду. Хотя обычно предварительная обработка увеличивает стоимость процесса, она абсолютно необходима для достижения высоких выходов метана, и это недавно было показано Кабиром et al. (2015), что производство биогаза из предварительно обработанной органо-солью лесной биомассы может быть финансово жизнеспособным.
В литературе доступно большое количество способов предварительной обработки, которые подразделяются на физические, физико-химические, химические и биологические (Mosier et al. 2005; Matsakas and Christakopoulos 2013; Xiros et al. 2013). Эффективность предварительной обработки сильно зависит от источника используемой лигноцеллюлозной биомассы, и по этой причине не существует универсального решения, которое можно было бы применить для каждой биомассы.
ПРОГРАММНОЕ ОБЕСПЕЧЕНИЕ
Ель
Ель (, например, , Picea abies ) — важный образец древесины хвойных пород. Необработанная ель не очень эффективна для использования в анаэробном сбраживании, так как полученный выход метана был всего лишь 30 мл CH 4 / г ТС (летучие твердые вещества) (Mirahmadi et al. 2010; Mohsenzadeh et al. 2012 ), тогда как самый высокий полученный выход составил только 85 мл CH 4 / г ТС (Gao et al. 2013).
Предварительная гидротермальная обработка диоксидом серы (SO 2 ) оказалась очень эффективной для обработки ели; выход метана 276 мл CH 4 / г VS (Таблица 1) был достигнут, когда ель обрабатывали SO 2 при 212 ° C в течение 4-8 мин, с pH от 1,6 до 1,8 в конце предварительная обработка (Matsakas et al. 2015).
Таблица 1. Различные источники материалов из мягкой древесины и выход биогаза, полученного при анаэробном сбраживании
Для достижения такого высокого выхода была необходима ферментативная детоксикация с помощью лакказы (15 Ед / г за 12 ч до переваривания) и добавление целлюлолитических ферментов (30 FPU / г) одновременно с перевариванием.С другой стороны, при предварительной обработке ели в более мягких условиях (200 ° C в течение 4-8 мин и pH после предварительной обработки от 1,8 до 2,0) выход метана был немного ниже, достигая 259 мл CH 4 / г VS. Для достижения этого выхода было необходимо добавление 30 FPU / г целлюлолитических ферментов, тогда как в детоксикации не было необходимости. В другом исследовании, когда предварительная обработка паром использовалась при 220 ° C в течение 5 минут с добавлением 2,4% SO 2 , полученный выход биогаза достиг 304 мл / г VS (Janzon et al. 2014). Это трудно сравнивать с другими исследованиями, где результаты приведены в мл CH 4 / г ТС, поскольку содержание метана в биогазе может варьироваться. Согласно этим авторам, содержание метана в биогазе колеблется от 50% до 80%, что подразумевает выход метана между 152 мл CH 4 / г VS и 243 мл CH 4 / г VS приблизительно.
Помимо предварительной термической обработки с использованием неорганических кислот, другие исследователи оценивали использование щелочи в процессе предварительной обработки.Например, Mirahmadi et al. (2010) предварительно обработали ель 7% NaOH в течение 2 ч при 5 ° C. Эти условия предварительной обработки были не такими эффективными, как с кислотой, так как выход метана из предварительно обработанной щелочью ели достигал только 50 мл CH 4 / г ТС. В другом исследовании та же исследовательская группа добавила в NaOH 12% тиомочевину и обработала ель при -15 ° C в течение 16 часов. Добавление тиомочевины положительно сказалось на выходе метана, который достиг 210 мл CH 4 / г ТС (Mohsenzadeh et al. 2012).
Наконец, в некоторых других исследованиях была оценена другая стратегия, согласно которой предварительная обработка включала использование ионных жидкостей. Например, Тегаммар и др. (2012) оценили влияние измельчения еловой щепы на выход метана, как необработанного, так и предварительно обработанного ионной жидкостью N-метилморфолин-N-оксид (NMMO) при 130 ° C в течение 15 часов. Они обнаружили, что измельчение стружки было необходимо как для обработанных, так и для необработанных материалов, тогда как использование предварительной обработки ионной жидкостью улучшило производство метана из стружки с 11 до 125 мл CH 4 / г VS и из измельченной стружки из 66. до 245 мл CH 4 / г VS.С другой стороны, более низкий выход метана был получен Gao et al. (2013) с использованием [C 4 мкм] Cl / ДМСО (1-N-бутил-3-метилимидазолий хлорид / диметилсульфоксид) для обработки ели при 120 ° C в течение 2 часов. Наибольший обнаруженный ими выход метана составил 141 мл / г ТР, что почти вдвое меньше, чем при использовании NMMO. Однако не всегда легко сравнивать выходы различных исследований, поскольку на выход метана могут влиять несколько факторов, таких как источник посевного материала и протокол, используемый для определения выхода метана.
Сосна
Сосна также является важным представителем хвойных пород древесины, и ее можно встретить в большинстве стран северного полушария. Когда сосна используется для анаэробного сбраживания необработанной, выход метана обычно невелик. Браун et al. (2012) оценил необработанную сосну как сырье для жидкого и твердого анаэробного сбраживания. Переваривание жидкости было более эффективным, но выход метана составил только 54 мл CH 4 / г ТС (Таблица 1).Соответствующий выход для твердофазного разложения составлял 17 мл CH 4 / г VS.
Гидротермальная предварительная обработка (от 210 до 215 ° C в течение 5 минут) с использованием SO 2 в качестве катализатора оказалась эффективной для предварительной обработки сосны, что дало 180 мл CH 4 / г VS (Matsakas et al. 2015 ). Для достижения этого выхода была необходима детоксикация с помощью лакказы (10 Ед / г) и добавление целлюлолитических ферментов (15 FPU / г).
Щелочная предварительная обработка была использована Салехианом и Карими (2012) для предварительной обработки различных частей сосны (хвои (листья), веток, шишек и коры).Предварительная обработка проводилась 8% NaOH либо в течение 60 минут при 0 ° C, либо в течение 10 минут при 100 ° C. Использование предварительной щелочной обработки улучшило выход метана во всех частях дерева, за исключением игл ―, где выход метана фактически снизился по сравнению с необработанным материалом. Наивысший выход метана был получен при использовании необработанных игл (213 мл CH 4 / г VS) с последующей обработкой коры (при более высокой температуре), что дало 107 мл CH 4 / г VS. Ветви и конусы дали 98 и 75 мл CH 4 / г ТС после предварительной обработки при более низкой температуре.Наконец, предварительная щелочная обработка (8% NaOH) при 100 ° C в течение 10 мин привела к выходу метана 178 мл CH 4 / г ТС (Салехиан и др. 2013).
Ионные жидкости также использовались для предварительной обработки сосны. Более конкретно, Shafiei et al. (2014) оценили предварительную обработку 85% -ным NMMO при 120 ° C в течение 30 минут. Использование этого процесса предварительной обработки привело к повышению выхода метана из сосновой щепы с 21 мл / г VS до приблизительно 143 мл / г VS, тогда как выход метана из соснового порошка улучшился с 66 мл CH 4 / г VS до примерно 224 мл CH 4 / г VS.
Наконец, предварительная обработка органических растворов была использована в качестве процесса предварительной обработки Mirmohamadsadeghi et al. (2014). Предварительная обработка проводилась 75% этанолом с добавлением 1% серной кислоты и проводилась при 150 ° C в течение 30 минут. Выход метана, полученный при твердофазном разложении, составил 71 мл CH 4 / г углеводов (что равно 54 мл CH 4 / г VS).
кедр
Кедр японский ( Cryptomeria japonica ) — эндемичный вид Японии.Возьмите et al. (2006) использовал японский кедр в своей работе для оценки влияния различных процессов предварительной обработки на выход метана (очистка, обработка паром, биологическая обработка с базидиомицетами и паровой взрыв). При переваривании необработанного материала метана не наблюдалось; тогда как только предварительная обработка в рафинере дала только 8 мл метана (было неясно, было ли это в миллилитрах общего произведенного метана или выходом метана). Когда предварительная обработка рафинера была повторена 10 раз, количество метана увеличилось до 26 мл.Предварительная обработка, когда проводилась только обработкой паром (170 ° C в течение 30 мин), давала 28 мл метана, тогда как при сочетании обработки паром с рафинированием количество полученного метана увеличивалось до 45 мл. Взрыв пара был превосходным, в результате чего образовалось до 180 мл метана, когда обработка проводилась при 258 ° C в течение 5 минут. Наконец, из различных базидиомицетов, использованных в этой работе, наиболее эффективным оказался Cyathus stercoreus AW 03-72, а полученный метан достиг 43 мл (таблица 1).
Предварительная биологическая обработка кедровой щепы была также оценена Amirta et al. (2006) с использованием грибов белой гнили. Более конкретно, они использовали три штамма Ceriporiopsis subvermispora и Pleurocybella porrigens с присутствием или отсутствием пшеничных отрубей в течение 4-8 недель. Штамм C. subvermispora был более эффективным для предварительной обработки кедра, при этом максимальный выход метана был получен при использовании штамма C. subvermispora ATCC в течение восьми недель в присутствии пшеничных отрубей. В этих условиях выход метана достигал приблизительно 25% от максимального теоретического выхода, исходя из содержания холоцеллюлозы в исходной древесной стружке (данные по выходу в мл CH 4 / г VS отсутствуют).
Смеси хвойных пород
Смеси ели и сосны довольно часто встречаются в литературе, так как эти две породы хвойных пород не часто разделяются в лесной промышленности. Наиболее распространенной предварительной обработкой смесей древесины хвойных пород в литературе является использование ионных жидкостей. Например, Kabir et al. (2013) оценил использование смеси ели, сосны, коры, и т. Д. для производства метана. На первом этапе оценивали влияние размера материалов (2, 4 и 8 мм).Хотя выход метана из необработанных материалов был низким, было обнаружено, что размер материала играет очень важную роль: частицы размером 8 мм дают 0 мл CH 4 / г VS, а частицы размером 2 мм дают 70 мл CH 4 / г VS. На следующем этапе оценивали эффект предварительной обработки ионными жидкостями с использованием 75-85% NMMO при 120 ° C в течение 3-15 часов. Наилучшие результаты были получены, когда материал был обработан 85% -ным NMMO в течение 15 часов, что дало 170 мл CH 4 / г VS (Таблица 1).Наконец, авторы оценили ингибирующий эффект NMMO на анаэробное пищеварение и продемонстрировали, что даже 0,0016% NMMO может привести к снижению выхода метана на 34%. Это очень интересное наблюдение, которое подтверждает важность удаления NMMO из предварительно обработанных материалов перед разложением.
В другом исследовании Kabir et al. (2014) предварительно обработал смесь древесины хвойных пород 85% -ным NMMO при 90 ° C в течение 30 часов и получил выход метана 150 мл CH 4 / г VS.Они также оценили возможность повторного использования NMMO для снижения стоимости процесса. Хотя они обнаружили, что это возможно, когда в качестве сырья использовали ячменную солому; повторное использование NMMO для предварительной обработки лесных остатков привело к снижению выхода метана. Пытаясь найти причину этого эффекта, они измерили кристалличность предварительно обработанного материала (как со свежим, так и с переработанным NMMO). Было обнаружено, что при повторном использовании NMMO кристалличность была выше, чем при использовании свежего NMMO, и, следовательно, был сделан вывод, что NMMO теряет способность растворять при повторном использовании.Наконец, другая комбинация температуры и времени выдержки (120 ° C в течение 3 часов) была оценена Aslanzadeh et al. (2014) при использовании 85% НММО. Они получили 109 мл CH 4 / г VS, что было выше, чем выход из необработанного материала (42 мл CH 4 / г VS). В том же исследовании полунепрерывная система была также оценена для смеси ели и сосны, как необработанной, так и предварительно обработанной. В обоих материалах время гидравлического удерживания (HRT) составляло 20 дней, а максимальная скорость органической нагрузки (OLR) составляла 4.4 г ВС / л / сут. Ежедневная производительность для необработанного материала составляла 53 мл CH 4 / г VS / день, а для предварительно обработанного материала — 92 мл CH 4 / г VS / день.
Наконец, смесь ели, сосны, коры, и т. Д. также была оценена как сырье для анаэробного сбраживания Kabir et al. (2015), используя предварительную обработку органосольвом. Необработанные материалы дали только 50 мл CH 4 / г VS, тогда как материалы, предварительно обработанные при 190 ° C в течение 1 часа, улучшили выход до диапазона от 230 до 340 мл CH 4 / г VS.Среди различных используемых растворителей (50% об. Этанола или метанола) и катализаторов (серная кислота, уксусная кислота или без катализатора) двумя оптимальными комбинациями были этанол с 1% серной кислоты и метанол с 1%. с серной кислотой. Обе комбинации привели к 340 мл CH 4 / г VS. На основании этих двух методов предварительной обработки авторы после проведения технико-экономического анализа процесса пришли к выводу, что использование метанола более рентабельно с финансовой точки зрения.
ТРУБА
Береза
Береза ( эл.грамм. Betula pendula и B. pubescens ) — это древесина лиственных пород, произрастающая во всем мире и очень распространенная в северной части Европы (Goshadrou et al. 2013; Vivekanand et al. 2013). Выход метана из необработанной березы, как правило, выше, чем из других необработанных древесных материалов, и может достигать 250 мл CH 4 / г ТС (Mirahmadi et al. 2010), хотя и гораздо более низкие значения ( например, , 18 мл CH 4 / г VS) также были продемонстрированы в литературе (Matsakas et al. 2015).
Были изучены различные методы предварительной обработки с целью повышения выхода метана. Vivekanand et al. (2013) оценили влияние различных рабочих условий парового взрыва на усвояемость березы. Максимальный выход метана, который они получили, составил 369 мл CH 4 / г ТР из березы, предварительно обработанной при 220 ° C в течение 10 мин (таблица 2). Более того, они обнаружили, что существует корреляция между высвобождением глюкозы в результате ферментативной обработки и выходом метана, полученным при анаэробном сбраживании.С другой стороны, гидротермальная предварительная обработка с использованием SO 2 в качестве катализатора, как было обнаружено нами, привела к несколько более низкому выходу метана, составляющему 305 мл CH 4 / г ТС (Matsakas et al. 2015). Для получения этого выхода добавляли целлюлолитические ферменты в концентрации, соответствующей 15 FPU / г.
Помимо термической обработки, также оценивалась предварительная щелочная обработка при более низких температурах. Предварительная щелочная обработка оказалась более эффективной, как Mirahmadi et al. (2010) достиг более высокого выхода метана (460 мл CH 4 / г VS) при обработке березы 7% -ным раствором NaOH в течение 2 часов при 100 ° C. С другой стороны, когда NaOH был дополнен 5,5% -ной тиомочевиной и обработан при -15 ° C в течение 16 часов, выход метана снизился до 360 мл CH 4 / г VS (Mohsenzadeh et al. 2012 ).
Наконец, другая исследовательская группа также попыталась оценить предварительную обработку ионной жидкости с использованием NMMO (Goshadrou et al. 2013). Предварительная обработка NMMO при 130 ° C в течение 3 часов привела к увеличению образования метана с 158 мл CH 4 / г ТС до 232 мл СН 4 / г ТС.
Ива
Ива( Salix spp.) Также является важным родом, который встречается в нескольких странах по всему миру. Turick et al. (1991) оценил различные виды ивы без использования какой-либо предварительной обработки, кроме уменьшения размера. Максимальный выход метана, который они продемонстрировали, достигал 310 мл CH 4 / г ТС при использовании S. eriocephala или S. exigua (Таблица 2).
Horn et al. (2011) использовали в своей работе вид Salix viminalis . Они оценили различные комбинации температуры и времени выдержки во время предварительной обработки паровым взрывом, изменяя температуру от 170 до 230 ° C, тогда как время выдержки было установлено на 5, 10 или 15 минут. Производство метана через 57 дней было более или менее одинаковым для диапазона комбинаций температуры и времени выдержки, с максимальным полученным выходом около 240 мл CH 4 / г ТС. Более того, авторы обнаружили корреляцию между выходом метана (и биогаза) и высвобождением сахара после ферментативного осахаривания предварительно обработанных материалов.В результате такой хорошей корреляции они предположили, что это может служить быстрым скринингом усвояемости лигноцеллюлозных материалов. В другом исследовании Estevez et al. (2012) оценили различные рабочие условия предварительной обработки паровым взрывом для Salix , где наибольшее количество метана было получено с комбинациями 230 ° C в течение 5 минут (241 мл CH 4 / г VS), 230 ° C для 10 мин (234 мл CH 4 / г VS) и 210 ° C в течение 10 мин (230 мл CH 4 / г VS).На следующем этапе своей работы они также оценили совместное переваривание предварительно обработанного Salix с коровьим навозом при различных соотношениях, что привело к различным отношениям углерода к азоту (C: N). Для этих экспериментов они решили использовать условия предварительной обработки 210 ° C в течение 10 минут, поскольку улучшение выхода метана, наблюдаемое в более жестких условиях предварительной обработки, не было статистически значимым. Из различных смесей, которые были оценены, самые высокие выходы метана были получены для 30% Salix (228 мл CH 4 / г VS) и 40% Salix (224 мл CH 4 / г VS) в пересчете на от общего VS, что эквивалентно соотношению C: N, равному 35 и 39, соответственно.
Таблица 2. Различные источники лесного сырья лиственных пород и урожай, полученный при анаэробном сбраживании
Наконец, выдержка в водном растворе аммиака была исследована Jurado et al. (2013) для предварительной обработки ивы перед перевариванием. Необработанная ива привела к получению 80 мл CH 4 / г VS, тогда как при предварительной обработке 32% -ным раствором аммиака при 25 ° C в течение трех дней выход метана увеличился до 155 мл CH 4 / г VS.
Эвкалипт
Эвкалипт — это род деревьев, преобладающий в австралийских лесах. Помимо Австралии, эвкалипт можно найти во многих других странах, таких как Бразилия. Накамура и Мтуи (2003) использовали древесную щепу из Eucalyptus globulus и оценили следующие процессы предварительной обработки: экстракция горячей водой (125 ° C в течение 20 минут), экстракция в присутствии 1% NaOH (125 ° C в течение 20 минут). , и паровой взрыв (25 атм в течение 3 мин). Необработанная эвкалиптовая стружка давала очень низкое образование метана — всего 48 мл (что эквивалентно 14 мл CH 4 / г TS (общее твердое вещество), если принять во внимание количество сухих стружек, которое использовали авторы).Экстракция горячей водой была более эффективной, в результате было получено 421 мл метана (что эквивалентно 124 мл CH 4 / г TS), тогда как при добавлении 1% NaOH выход метана увеличился до 456 мл (134 мл CH 4 / г TS). Наконец, наибольшее образование метана наблюдалось при использовании парового взрыва, и оно достигло 660 мл (194 мл CH 4 / г TS) (Таблица 2).
Тополь
Различные виды тополей были оценены Turick et al. (1991) без предварительной обработки, за исключением измельчения. Наибольший выход метана был получен у гибрида Populus nigra x Populus maximowiczii и достиг 290 мл CH 4 / г ТС (Таблица 2). Более низкий выход метана из необработанного тополя был получен Yao et al. (2013), достигая значения 127 мл CH 4 / г VS. С другой стороны, те же авторы оценили использование предварительной щелочной обработки с различными дозами NaOH при температуре окружающей среды в течение 4 дней.Влажность составляла примерно 88%. Помимо различных концентраций NaOH, они исследовали эффект увеличения концентрации твердого вещества в варочных котлах (с 35 до 80 г / л). Наивысший выход метана 272 мLCH 4 / г VS был получен при использовании 5% NaOH с начальным содержанием твердого вещества 35 г / л. Авторы наблюдали снижение урожайности с увеличением содержания субстрата от 50 до 80 г / л. Наконец, они упомянули, что снижение выхода метана на 80 г / л могло быть вызвано сочетанием подкисления и высоких уровней ионов натрия.
Прочие лиственные породы
Mirmohamadsadeghi et al. (2014) исследовали возможность использования вязов в качестве сырья для производства биогаза. Выход метана из необработанного материала был низким, достигая только 54 мл CH 4 / г углеводов (что эквивалентно приблизительно 42 мл CH 4 / г VS). При использовании обработки органосольв (75% этанол, 180 ° C в течение 1 ч) выход метана улучшился до 94 мл CH 4 / г углеводов (что эквивалентно приблизительно 75 мл CH 4 / г VS).Хотя урожайность улучшилась, она все еще оставалась довольно низкой.
Йошида и др. (2010) использовал бук японский ( Fagus crenata ) в качестве сырья для анаэробного сбраживания. Они применили двухэтапную предварительную обработку. На первом этапе проводилась экстракция Сокслета смесью 1: 2 об / об этанол: бензол в течение 12 часов. На втором этапе обработка сверхкритической воды оценивалась при 380 ° C, где давление составляло 30 или 100 МПа, а время сопротивления составляло 7, 60 или 240 с.Согласно их выводам, давление 30 МПа было более эффективным, чем 100 МПа для всех использованных времен выдержки. Наибольшее образование метана наблюдалось, когда обработка проходила в течение 240 с при 30 МПа (15,8 мл метана, что соответствует 117% от максимального расчетного выхода). Данных о выходе метана на грамм VS или TS не было.
Turick et al. (1991) оценивали различные породы древесины твердых пород без какой-либо предварительной обработки, за исключением измельчения.Во время их работы необработанный платан ( Platanus occidentalis ) дал выход метана 320 мЛКГ 4 / г ТШ, тогда как урожай черной акации ( Robinia pseudoacacia ) и сладкой жевательной резинки ( Liquidambar styraciflua ) составил 240 мл CH. 4 / г VS и 210 мл CH 4 / г VS соответственно. Наконец, Brown et al. (2012) также оценила необработанную древесину лиственных пород, точнее, клен, как сырье для жидкого и твердого анаэробного сбраживания.Жидкое анаэробное сбраживание было более эффективным с выходом метана 57 мл CH 4 / г VS, тогда как выход от твердотельного анаэробного разложения составлял 47 мл CH 4 / г VS.
ВЫВОДЫ
Использование лесных материалов в качестве сырья для анаэробного сбраживания в последние годы вызвало большой исследовательский интерес. Лесные материалы, как правило, труднее переваривать по сравнению с другими остатками (, например, сельскохозяйственных остатков) и требуют более жестких процессов предварительной обработки.В литературе были рассмотрены различные методы предварительной обработки, такие как паровой взрыв, гидротермальный и щелочной. Было обнаружено, что их эффективность сильно зависит от источника используемого сырья. Хотя очень трудно сделать вывод, какой метод предварительной обработки является более подходящим (поскольку также трудно сравнивать результаты различных работ), существует тенденция, указывающая на то, что термическая обработка диоксидом серы и органосольвом является наиболее подходящей для предварительной обработки древесины хвойных пород.С другой стороны, для древесины твердых пород тенденция заключается в том, что предварительная щелочная обработка, как правило, более эффективна, после чего следует гидротермальный и паровой взрыв. Кроме того, было показано, что применение ферментов, хотя обычно не используется, также может иметь положительное влияние на выход метана. В будущем необходимо провести дальнейшие исследования в области применения ферментов, чтобы повысить выход метана. В качестве общего вывода показано, что лесные материалы могут эффективно использоваться для анаэробного сбраживания в лабораторных условиях.Конечно, необходимо провести дополнительную работу, чтобы еще больше повысить эффективность этого преобразования.
БЛАГОДАРНОСТИ
Мы благодарим Bio4Energy, среду стратегических исследований, назначенную правительством Швеции, за поддержку этой работы. Леонидас Мацакас также благодарит Фонды Кемпе за финансовую поддержку.
ССЫЛКИ
Abatzoglou, N., and Boivin, S. (2008). «Обзор процессов очистки биогаза», Биотопливо.Биопрод. Биор. 3 (1), 42-71. DOI: 10.1002 / bbb.117
Аду-Гьямфи, Н., Рао Равелла, С., и Хоббс, П. Дж. (2012). «Оптимизация анаэробного разложения путем выбора иммобилизующей поверхности для увеличения производства метана», Bioresour. Technol. 120, 248-255. DOI: 10.1016 / j.biortech.2012.06.042
Амирта, Р., Танабе, Т., Ватанабе, Т., Хонда, Ю., Кувахара, М., и Ватанабе, Т. (2006). «Метановая ферментация древесины японского кедра, предварительно обработанной грибком белой гнили, Ceriporiopsis subvermispora », J.Biotechnol. 123 (1), 71-77. DOI: 10.1016 / j.jbiotec.2005.10.004
Аслам М., Масьюки Х., Калам М., Абдесселам Х., Махлия Т. и Амалина М. (2006). «Экспериментальное исследование КПГ в качестве альтернативного топлива для модернизированного бензинового автомобиля», Топливо 85 (5-6), 717-724. DOI: 10.1016 / j.fuel.2005.09.004.
Асланзаде, С., Берг, А., Тахерзаде, М. Дж., И Хорват И. С. (2014). «Производство биогаза из предварительно обработанных лесных остатков N -метилморфолин- N -оксид (NMMO)», заявка Appl.Biochem. Biotechnol. 172 (6), 2998-3008. DOI: 10.1007 / s12010-014-0747-z
Бэнкс, К. Дж., Чесшир, М., Хевен, С., и Арнольд, Р. (2011). «Анаэробное сбраживание домашних пищевых отходов с разделением по источникам: оценка эффективности по балансу массы и энергии», Биоресурсы. Technol. 102 (2), 612-620. DOI: 10.1016 / j.biortech.2010.08.005
Бонтури, Н., Мацакас, Л., Нильссон, Р., Христакопулос, П., Миранда, Э.А., Берглунд, К.А., и Рова, У. (2015). «Одноклеточные дрожжи, продуцирующие масло Lipomyces starkeyi и Rhodosporidium toruloides : Выбор стратегии экстракции и прогноз свойств биодизеля», Energy 8 (6), 5040-5052.DOI: 10.3390 / en8065040
Браун Д., Ши Дж. И Ли Ю. (2012). «Сравнение твердофазного и жидкого анаэробного сбраживания лигноцеллюлозного сырья для производства биогаза», Биоресурсы. Technol. 124, 379-386. DOI: 10.1016 / j.biortech.2012.08.051
Браун, Дж. Д., и Мерфи, Дж. Д. (2013). «Оценка ресурсов, связанных с биометаном из пищевых отходов», Appl. Energ. 104, 170-177. DOI: 10.1016 / j.apenergy.2012.11.017
Чубота-Рози, К., Гаврилеску М. и Маковяну М. (2008). «Биомасса — важный возобновляемый источник энергии в Румынии», Environ. Англ. Manag. J. 7 (5), 559-568.
Датта Р., Махер М. А., Джонс К. и Бринкер Р. В. (2011). «Этанол — основное возобновляемое жидкое топливо», J. Chem. Technol. Biotechnol. 86 (4), 473-480. DOI: 10.1002 / jctb.2580
Демирбас А., (2008). «Продукты из лигноцеллюлозных материалов в результате процессов разложения», Energ. Кислый. А 30 (1), 27-37.DOI: 10.1080 / 00
0600626705
Эстевес М. М., Линьордет Р. и Моркен Дж. (2012). «Эффекты парового взрыва и совместного разложения при производстве метана из Salix с помощью мезофильных периодических анализов», Bioresour. Technol. 104, 749-756. DOI: 10.1016 / j.biortech.2011.11.017
Гальбе М. и Закки Г. (2002). «Обзор производства этанола из древесины хвойных пород», Прил. Microbiol. Biotechnol. 59 (6), 618-628. DOI: 10.1007 / s00253-002-1058-9
Гао, Дж., Чен, Л., Юань, К., Хуан, Х., Янь, З. (2013). «Предварительная обработка ионной жидкости для улучшения анаэробного переваривания лигноцеллюлозной биомассы», Bioresour. Technol. 150, 352-358. DOI: 10.1016 / j.biortech.2013.10.026
Гарсия-Перес, М., Чаала, А., Пакдел, Х., Кречмер, Д., и Рой, К. (2007). «Вакуумный пиролиз биомассы древесины хвойных и твердых пород: сравнение выхода продукта и свойств бионефти», J. Anal. Прил. Пирол. 78 (1), 104-116. DOI: 10.1016 / j.jaap.2006.05.003
Гошадроу А., Карими К. и Тахерзаде М. Дж. (2013). «Производство этанола и биогаза из березы с помощью предварительной обработки NMMO», Биомасса Биоэнерг. 49, 95-101. DOI: 10.1016 / j.biombioe.2012.12.013
Гриффин М. Э., МакМахон К. Д., Маки Р. И. и Раскин Л. (1998). «Динамика метаногенного населения во время пуска анаэробных варочных котлов, обрабатывающих твердые биологические твердые бытовые отходы», Biotechnol. Биоэнерг. 57 (3), 342-355. DOI: 10.1002 / (SICI) 1097-0290 (19980205) 57: 3 <342 :: AID-BIT11> 3.0.CO; 2-я
Хилл, Д. Т., и Болт, Дж. П. (2000). «Производство метана из жидких свиноводческих отходов с низкой концентрацией твердых веществ с использованием традиционной анаэробной ферментации», Биоресурсы. Technol. 74 (3), 241-247. DOI: 10.1016 / S0960-8524 (00) 00008-0
Хорн, С. Дж., Эстевес, М. М., Нильсен Х. К., Линьордет, Р., и Эйсинк, В. Г. Х. (2011). «Производство биогаза и осахаривание Salix , предварительно обработанного при различных условиях парового взрыва», Биоресурсы. Technol. 102 (17), 7932-7936. DOI: 10.1016 / j.biortech.2011.06.042
Янзон, Р., Шютт, Ф., Ольденбург, С., Фишер, Э., Кёрнер, И., и Сааке, Б. (2014). «Предварительная обработка остатков елового леса паром: оптимальные условия для производства биогаза и ферментативного гидролиза», Carbohyd. Polym. 100, 202-210. DOI: 10.1016 / j.carbpol.2013.04.093
Джейханипур А., Асланзаде С., Раджендран К., Баласубраманян Г. и Тахерзаде М. Дж. (2013). «Высокопроизводительное производство биогаза из текстильных отходов с использованием двухстадийного процесса», — Renew.Energ. 52, 128–135. DOI: 10.1016 / j.renene.2012.10.042
Хурадо, Э., Гавала, Х. Н., Скиадас, И. В. (2013). «Повышение выхода метана из пшеничной соломы, мискантуса и ивы с помощью замачивания водным аммиаком», Environ. Technol. 34 (13-14), 2069-2075. DOI: 10.1080 / 095
.2013.826701Кабир М. М., дель Пилар Кастильо М., Тахерзаде М. Дж. И Хорват И. С. (2013). «Влияние предварительной обработки N -метилморфолин- N -оксидом (NMMO) на анаэробное переваривание лесных остатков», BioResources 8 (4), 5409-5423.DOI: 10.15376 / biores.8.4.5409-5423
Кабир М. М., Никлассон К., Тахерзаде М. Дж. И Хорват И. С. (2014). «Производство биогаза из лигноцеллюлоз с помощью предварительной обработки N -метилморфолин- N -оксид (NMMO): эффекты восстановления и повторного использования NMMO», Bioresour. Technol. 161, 446-450. DOI: 10.1016 / j.biortech.2014.03.107
Кабир М. М., Раджендран К., Тахерзаде М. Дж. И Хорват И. С. (2015). «Экспериментальная и экономическая оценка биоконверсии лесных остатков в биогаз с использованием предварительной обработки органических растворов», Биоресурсы.Technol. 178, 201-208. DOI: 10.1016 / j.biortech.2014.07.064
Кафле, Г. К., Бхаттарай, С., Ким, С. Х., и Чен, Л. (2014). «Влияние корма для микробов на анаэробное переваривание отходов китайской капусты в мезофильных и термофильных условиях: биогазовый потенциал и кинетическое исследование», J. Environ. Управлять. 133, 293-301. DOI: 10.1016 / j.jenvman.2013.12.006
Ким, С., Хольцаппл, М. Т. (2006). «Влияние структурных особенностей на ферментативную перевариваемость кукурузной соломы», Биоресурсы.Technol. 97 (4), 583-591. DOI: 10.1016 / j.biortech.2005.03.040
Лоуфорд, Х. Г., и Руссо, Дж. Д. (1991). «Топливный этанол из гидролизата гемицеллюлозы твердых пород древесины с помощью генной инженерии Escherichia coli B, несущей гены из Zymomonas mobilis », Biotechnol. Lett. 13 (3), 191–196.
Лестер, М., Беллон-Морель, В., Гонсалес, К., Латриль, Э., Роджер, Дж. М., Джанква, Г., и Стейер, Дж. П. (2010). «Альтернативные методы определения анаэробной биоразлагаемости: обзор», Process Biochem. 45 (4), 431-440. DOI: 10.1016 / j.procbio.2009.11.018
Лю Г., Чжан Р., Эль-Машад Х. М. и Донг Р. (2009). «Влияние соотношения корма и инокулята на выход биогаза из пищевых продуктов и зеленых отходов», Биоресурсы. Technol. 100 (21), 5103-5108. DOI: 10.1016 / j.biortech.2009.03.081
Мацакас, Л., и Христакопулос, П. (2013). «Ферментация сжиженного гидротермально предварительно обработанного жмыха сладкого сорго в этанол с высоким содержанием твердых веществ», Bioresour. Technol. 127, 202-208.DOI: 10.1016 / j.biortech.2012.09.107
Мацакас, Л., и Христакопулос, П. (2015). «Производство этанола из ферментативно обработанных высушенных пищевых отходов с использованием ферментов, производимых на месте», Sustainability 7 (2), 1446-1458. DOI: 10.3390 / su7021446
Мацакас, Л., Стериоти, А. А., Рова, У., и Кристакопулос, П. (2014a). «Использование сушеного сладкого сорго для эффективного производства липидов дрожжами Lipomyces starkeyi CBS 1807», Ind. Crop. Prod. 62, 367-372.DOI: 10.1016 / j.indcrop.2014.09.011
Мацакас, Л., Топакас, Э., и Христакопулос, П. (2014b). «Новые тенденции в микробном производстве 3-гидроксипропионовой кислоты», Curr. Biochem. Англ. 1 (2), 141-154. DOI: 10.2174 / 22127116140415200133
Мацакас, Л., Рова, У., и Христакопулос, П. (2014c). «Оценка сушеных стеблей сладкого сорго как сырья для производства метана», BioMed Res. Int. 2014, 731731. DOI: 10.1155 / 2014/731731
Мацакас, Л., Рова, У., Кристакопулос, П. (2015). «Последовательная параметрическая оптимизация производства метана из различных источников лесного сырья», Frontiers Microbiol . 6, 1163. DOI: 10.3389 / fmicb.2015.01163
Маккендри, П. (2002). «Производство энергии из биомассы (часть 1): Обзор биомассы», Биоресурсы. Technol. 83 (1), 37-46. DOI: 10.1016 / S0960-8524 (01) 00118-3
Мирахмади К., Кабир М. М., Джейханипур А., Карими К. и Тахерзаде М. Дж. (2010).«Предварительная щелочная обработка ели и березы для улучшения производства биоэтанола и биогаза», BioResources 5 (2), 928-938. DOI: 10.15376 / biores.5.2.928-938
Мирмохамадсадеги С., Карими К., Замани А., Амири Х. и Хорват И. С. (2014). «Повышенное производство биогаза в твердом состоянии из лигноцеллюлозной биомассы путем предварительной обработки органических растворов», BioMed Res. Int. 2014, 350414. DOI: 10.1155 / 2014/350414
Мохсензаде А., Джейханипур А., Карими К. и Тахерзаде М.J. (2012). «Предварительная щелочная обработка ели хвойных пород и березы лиственных пород с помощью NaOH / тиомочевины, NaOH / мочевины, NaOH / мочевины / тиомочевины и NaOH / PEG для улучшения производства этанола и биогаза», J. Chem. Technol. Biotechnol. 87 (8), 1209-1214. DOI: 10.1002 / jctb.3695
Мозье, Н., Вайман, К., Дейл, Б., Эландер, Р., Ли, Ю. Ю., Хольцаппл, М., и Ладиш, М. (2005). «Особенности перспективных технологий предварительной обработки лигноцеллюлозной биомассы», Биоресурсы. Technol. 96 (6), 673-686.DOI: 10.1016 / j.biortech.2004.06.025
Нагао Н., Таджима Н., Кавай М., Нива К., Куросава Н., Мацуяма Т., Юсофф Ф. М. и Тода Т. (2012). «Максимальная скорость загрузки органических веществ для одностадийного влажного анаэробного сбраживания пищевых отходов», Bioresour. Technol. 118, 210-218. DOI: 10.1016 / j.biortech.2012.05.045
Наик, С. Н., Гоуд, В. В., Рут, П. К., и Далай, А. К. (2010). «Производство биотоплива первого и второго поколения: всесторонний обзор», Renew.Sust. Energy Rev. 14 (2), 578-597. DOI: 10.1016 / j.rser.2009.10.003
Накамура Ю. и Мтуи Г. (2003). «Анаэробная ферментация древесной биомассы, обработанной различными методами», Biotechnol. Bioproc. Англ. 8 (3), 179-182. DOI: 10.1007 / BF02935893
Нильсен, Х. Б., Младеновска, З., Вестерманн, П., и Аринг, Б. К. (2004). «Сравнение двухэтапного термофильного (68 o C / 55 o C) анаэробного сбраживания с одностадийным термофильным (55 o C) сбраживанием навоза крупного рогатого скота», Biotechnol.Bioeng. 86 (3), 291-300. DOI: 10.1002 / bit.20037
Нигам П. С., Сингх А. (2011). «Производство жидкого биотоплива из возобновляемых источников», Прог. Energ. Гребень. Sci. 37 (1), 52-68. DOI: 10.1016 / j.pecs.2010.01.003
Ницос, К., Мацакас, Л., Триантафиллидис, К., Рова, У., и Христакопулос, П. (2015). «Оценка средиземноморских сельскохозяйственных остатков как потенциального сырья для производства биогаза посредством анаэробной ферментации», BioMed Res.Int. 2015, 171635. DOI: 10.1155 / 2015/171635
Палаци, Дж., Виньяс, М., Гивернау, М., Фернандес, Б., и Флотатс, X. (2011). Анаэробное сбраживание отходов бойни: «Основные ограничения процесса и взаимодействия микробного сообщества», Биоресурсы. Technol. 102 (3), 2219-2227. DOI: 10.1016 / j.biortech.2010.09.121
Parawira, W. (2012). «Ферментные исследования и применение в биотехнологической интенсификации производства биогаза», Crit. Rev. Biotechnol. 32 (2), 172-186.DOI: 10.3109 / 07388551.2011.595384
Саха, Б. С. (2003). «Биоконверсия гемицеллюлозы», J. Ind. Microbiol. Biotechnol. 30 (5), 279-291.
Салехиан П., Карими К. (2012). «Предварительная щелочная обработка для улучшения производства биогаза и этанола из различных частей отходов сосны», Ind. Eng. Chem. Res. 52 (2), 972-978. DOI: 10.1021 / ie302805c
Салехиан П., Карими К., Зилуэй Х. и Джейханипур А. (2013). «Улучшение производства биогаза из древесины сосны путем предварительной обработки щелочью», Топливо 106, 484-489.DOI: 10.1016 / j.fuel.2012.12.092
Саррис Д., Мацакас Л., Аггелис Г., Кутинас А. А. и Папаниколау С. (2014). «Аэрированный по сравнению с без аэрации конверсии мелассы и сточных вод оливковых заводов, смешанных в биоэтанол с помощью Saccharomyces cerevisiae в неасептических условиях», Ind. Crop. Prod. 56, 83-93. DOI: 10.1016 / j.indcrop.2014.02.040
Шафие, М., Карими, К., Зилуэй, Х., и Тахерзаде, М. Дж. (2014). «Повышенное производство этанола и биогаза из соснового леса путем предварительной обработки NMMO и подробного анализа биомассы», BioMed Res.Int. 2014, 469378. DOI: 10.1155 / 2014/469378
Шридхар Н. и Хилл Д. (2011). Утилизация углекислого газа. Электрохимическая конверсия CO 2 — Возможности и проблемы , Det Norske Veritas, (http://www.dnv.com/binaries/dnv-position_paper_co2_utilization_tcm4-445820.pdf).
Стамателу К., Антонопулу Г., Нтайкоу И. и Либератос Г. (2012). «Влияние предварительной физической, химической и биологической обработки биомассы на ее анаэробную усвояемость и производство биогаза», в: Производство биогаза: методы предварительной обработки при анаэробном сбраживании , A.Мудху (ред.), John Wiley & Sons Inc., Хобокен, Нью-Джерси, стр. 55-90. DOI: 10.1002 / 9781118404089.ch4
Сунь Ю., Линь Л., Дэн Х., Цзячжэ Л., Бэйхай Х., Сунь Р. и Оуян П. (2008). «Структурные изменения бамбуковой целлюлозы в муравьиной кислоте», BioResources, 3 (2), 297-315. DOI: 10.15376 / biores.3.2.297-315
Шведская газовая ассоциация (2011 г.). Биогаз в Швеции .
Тахерзаде, М. Дж., И Карими, К. (2008). «Предварительная обработка лигноцеллюлозных отходов для улучшения производства этанола и биогаза: обзор», Int.J. Mol. Sci. 9 (9), 1621–1651. DOI: 10.3390 / ijms21
Такэ, Х., Андо, Ю., Накамура, Ю., Кобаяши, Ф., Куримото, Ю., и Кувахара, М. (2006). «Производство метана из стружки японского кедра, предварительно обработанной различными методами делигнификации», Biochem. Англ. J. 28 (1), 30-35. DOI: 10.1016 / j.bej.2005.08.036
Тегаммар А., Карими К., Хорват И. С. и Тахерзаде М. Дж. (2012). «Повышенное производство биогаза из рисовой соломы, соломы тритикале и ели хвойных пород с помощью предварительной обработки NMMO», Biomass Bioenerg. 36, 116-120. DOI: 10.1016 / j.biombioe.2011.10.019
Томас-Пейо, Э., Олива, Дж. М., Баллестерос, М., и Олссон, Л. (2008). «Сравнение процессов SHF и SSF из взорванной паром пшеничной соломы для производства этанола путем ферментации ксилозы и устойчивой ферментации глюкозы штаммов Saccharomyces cerevisiae », Biotechnol. Bioeng. 100 (6), 1122-1131. DOI: 10.1002 / bit.21849
Турик, К. Э., Пек, М. В., Чиновет, Д. П., Джергер, Д. Э. и Уайт, Э. Х. (1991).«Метановая ферментация древесной биомассы», Биоресурсы. Technol. 37 (2), 141-147. DOI: 10.1016 / 0960-8524 (91) -U
Вивекананд В., Олсен Э. Ф. и Эйсинк В. Г. Х. (2013). «Влияние различных условий парового взрыва на метановый потенциал и ферментативное осахаривание березы», Биоресурсы. Technol. 127, 343-349. DOI: 10.1016 / j.biortech.2012.09.118
Ся, Ю., Фанг, Х. Х. П., и Чжан, Т. (2013). «Недавние исследования термофильной анаэробной биоконверсии лигноцеллюлозной биомассы», RSC Adv. 2013 (3), 15528-15542. DOI: 10.1039 / C3RA40866C
Ксирос, К., Топакас, Э., и Христакопулос, П. (2013). «Гидролиз и ферментация для производства целлюлозного этанола», Энерг. Environ. 2 (6), 633-654. DOI: 10.1002 / wene.49
Яо, Ю., Хе, М., Рен, Ю., Ма, Л., Ло, Ю., Шэн, Х., Сян, Ю., Чжан, Х., Ли, К., и Ан, Л. . (2013). «Анаэробное сбраживание остатков переработки тополя для производства метана после щелочной обработки», Биоресурсы. Технол .134, 347-352. DOI: 10.1016 / j.biortech.2012.12.160
Йошида К., Мияфудзи Х. и Сака С. (2010). «Производство метана из органических кислот, полученных сверхкритической обработкой воды из японского бука», J. Wood Sci. 56 (2), 160–165. DOI: 10.1007 / s10086-009-1074-9
Zheng, Y., Zhao, J., Xu, F., and Li, Y. (2014). «Предварительная обработка лигноцеллюлозной биомассы для увеличения производства биогаза», Prog. Energ. Гореть. 42, 35-53. DOI: 10.1016 / j.pecs.2014.01.001
Чжоу, Д., Ли, Дж., Ван, К., и Лю, Ю. (2012). «Анаэробная ферментация коровьего навоза — влияние концентрации твердого вещества и температуры на качество биогаза», Adv. Мат. Res. 608-609, 419-427. DOI: 10.4028 / www.scientific.net / AMR.608-609.419
http://www.eubia.org/index.php/about-biomass/anaerobic-digestion. Последний доступ 15 декабря 2015 г.
http://www.scb.se/en_/Finding-statistics/search/?query=Personbilar+i+trafik+efter+drivmedel,+%C3%A5rsvis+2005-2014&tab=scb#. Последний доступ 22 февраля 2016 г.
Статья подана: 21 декабря 2015 г .; Рецензирование завершено: 12 февраля 2016 г .; Доработанная версия получена и принята: 25 февраля 2016 г .; Опубликовано: 7 марта 2016 г.
DOI: 10.15376 / biores.11.2.Matsakas
Аварийный анализ биогазовых систем на основе различного сырья
Загрязнение окружающей среды и энергетический кризис ограничивают развитие Китая, и использование возобновляемых источников энергии является эффективной стратегией для уменьшения ущерба. Биогазовая инженерия быстро разработала атрибуты для решения экологических проблем и создания возобновляемого источника энергии — биогаза.В этой статье материалы двух различных биогазовых установок были проанализированы методом аварийной обработки. Один из них — это биогазовый проект, деградированный материал которого — фекалии (система BPF), а другой — тот, где деградированный материал — кукурузная солома (система BPC). В результате эколого-экономическая стоимость БПФ и БКК составляет 28 300 долларов США в год и 8 100 долларов США в год соответственно. Принимая во внимание валюту, окружающую среду и человеческие ресурсы, оба биогазовых проекта обладают способностью удалять отходы и имеют потенциал для развития. Доля производства биогаза намного больше, чем производство удобрений; Таким образом, в будущем следует сделать упор на использование удобрений.Для сравнения, BPF лучше, чем BPC, с точки зрения эколого-экономических преимуществ, преимуществ для окружающей среды и устойчивости. Причина в сложности сезонного сбора и деградации кукурузной соломы. Таким образом, предлагается комбинировать БКК с другим сырьем.
1. Введение
Китай — крупнейшая развивающаяся страна мира с населением более 1,3 миллиарда человек. С развитием экономики и индустриализации проблемы чрезмерного энергопотребления существенно влияют на будущее Китая.Поиск новых источников энергии для замены ископаемого топлива является актуальной задачей для Китая [1–5]. Анаэробное сбраживание — одна из наиболее подходящих технологий для решения этих проблем. В Китае имеются большие ресурсы биомассы, особенно солома сельскохозяйственных культур, остатки леса, навоз домашнего скота и птицы, а также различные виды городских и промышленных органических отходов и сточных вод [2]. Такое достаточное количество материалов способствует развитию биогаза, особенно крупных и средних биогазовых проектов.
В 2003 году была реализована «агроэкологическая» программа, которая создала благоприятные условия для развития биогазовых проектов.Согласно статистике (приведенной на Рисунке 1), выход биогаза в 2009 году в 1,75 раза больше, чем в 2003 году. Кроме того, развитие биогазовых проектов также положительно влияет на смежные отрасли, такие как обрабатывающее производство, строительные материалы и строительное машиностроение. Все они достигли хороших экономических, социальных и других комплексных преимуществ [6].
С увеличением количества биогазовых проектов, биогазовые экологические системы привлекают все больше и больше внимания.Биогазовая экологическая система представляет собой комплекс, состоящий из сельского хозяйства, окружающей среды, энергетики, общества и других соответствующих секторов. Цели биогазовой экологической системы — производство энергоносителя из возобновляемых ресурсов и достижение множества экологических выгод. Были предприняты некоторые исследования биогазовых экологических систем, но в основном основное внимание уделялось технической оценке, экономической выгоде и потокам энергии [7–13]. Методы исследования экологической системы биогаза включают учет эксергии, энергетический анализ, оценку жизненного цикла и аварийный анализ, которые были разработаны за последние 30 лет.Emergy выбран в этой статье, потому что это особенно подходящий инструмент для оценки системы сельскохозяйственного производства. Emergy фокусируется на сложной экосистеме на стыке естественных и человеческих систем, которая включает в себя многие предметные области, не только системы экологии, экосистемной экологии, энергетики, науки о ресурсах, наук об окружающей среде, систематики, наук о Земле и других естественных наук, но и также относящиеся к экономике, социологии, прогнозированию и другим гуманитарным наукам [14, 15].Метод Emergy объединяет все меры, и все показатели входов в процессе формирования преобразуются в солнечную эмерджету (sej) и солнечную трансформацию (sej / J). Таким образом, можно рассчитать как экологические ценности, так и экономические ценности, что упрощает процесс оценки.
Все исследования, упомянутые ранее, сосредоточены на одном типе биогазовой установки, и материалы, используемые в качестве входных, не дифференцируются. Однако с развитием биогазовой технологии появилось несколько видов биогазовых материалов.В настоящее время основными материалами для анаэробной ферментации являются солома и фекалии, и их процесс и параметры ферментации (температура, концентрация, коэффициент дефлегмации, режим перемешивания и т. Д.) Сильно различаются. Таким образом, анализ системы биогазового проекта может быть исчерпывающим и правильным только с учетом различных характеристик материалов. В этом документе для сравнения выбраны два репрезентативных биогазовых проекта, и для анализа их характеристик используется аварийный режим. Целью данного исследования является оценка эколого-экономической выгоды, пользы для окружающей среды и возможности устойчивого развития двух различных видов сырья (кукурузная солома и фекалии) в системе производства биогаза и создание теоретической основы для обобщения экологического производства биогаза. система.Все расчеты должны быть максимально прозрачными, чтобы результаты можно было использовать для будущих анализов.
2. Материалы и методы
2.1. Учебная площадка
Два биогазовых проекта, изучаемые в этой статье, различаются по разложенным материалам; один — кукурузная солома, а другой — фекалии. Все данные получены по результатам исследования сайта за весь год.
2.1.1. Система BPF
Биогазовый проект, где разложившимся материалом являются фекалии (BPF), расположен на западе деревни Хэгэчжуанг района Чаоян в Пекине.Общий объем инвестиций в биогазовую установку составляет 2 600 000 юаней, площадь которой составляет 2930 м 2 . БНФ начал работу в октябре 2010 года, перерабатывая фекалии из трех деревень: Найдонг, Хегечжуан и Найси. Этот биогазовый проект решил проблему загрязнения фекалиями и улучшил качество жизни в деревне.
Технология БПФ — реактор непрерывного действия с мешалкой (CSTR), а материал бака — эмалированная прессованная сталь. Емкость БПФ составляет 400 м³, он имеет интегрированный резервуар для хранения сжиженного газа, в том числе объем хранения жидкости 224 м³ и объем хранения газа 200 м³.Биогазовый проект может переваривать 10-20 т твердого навоза и 25 т бытовых сточных вод в день, а выход биогаза составляет 650 м³ / сут. При обычном управлении концентрация ферментации поддерживается на уровне 6-10% за счет обратного флегма биогазовой суспензии. Солнечная система — одна из важнейших частей всей биогазовой установки, потому что она может повышать температуру питательных материалов до 5 ° C зимой. Кроме того, часть биогаза на выходе нагревается для поддержания температуры ферментации. Весной и осенью будет отапливаться 250 м³ биогаза, а мощность составит 400 м³.Летом из-за высокой температуры нагревать биогазовый бак не нужно; Таким образом, весь биогаз в объеме 650 м³ будет экспортирован. Зимой отапливается 350 м³ биогаза и 300 м³ биогаза идет на экспорт. Кроме того, зимой будет поставляться 113 кг угля в сутки, этого хватит на 4 месяца; Итак, количество угля составляет 13,6 т / год.
2.1.2. Система BPC
Другой биогазовый проект, где деградированный материал представляет собой BPC, расположен в деревне Дунъяочжуан страны Цин в провинции Хэбэй, где хорошо развита растениеводческая промышленность.Из-за этого существует ряд видов стеблей соломы из отходов сельскохозяйственных культур, а окружающая среда была загрязнена из-за складирования и преднамеренного сжигания соломы. В 1999 году был построен первый подземный биогазовый резервуар CSTR объемом 1000 м³. Однако в тот период технология была незрелой; Итак, биогазовый резервуар не может быть введен в эксплуатацию. После этого в 2005 году был успешно построен биогазовый резервуар кирпично-бетонной конструкции объемом 400 м³, который стал первым в Китае. Однако из-за ограничений строительных материалов и технологий этот биогазовый проект сейчас не работает.Благодаря обобщению опыта строительных работ и совершенствованию технологий в 2006 году был построен новый резервуар для биогаза объемом 400 м³. После отладки и эксплуатации он был официально введен в эксплуатацию в 2007 году и стал образцом для биогазового проекта в Китае.
Технология BPC — реактор с восходящим потоком твердых частиц (USR), а материал резервуара — сварная стальная пластина. Общий объем БПК составляет 400 м³ с производительностью обработки 900 кг кукурузной соломы в сутки. Чтобы поддерживать концентрацию корма, нужно добавлять 2 ~ 3 т воды в день.Температура ферментации составляет 44 ~ 55 ° C, а производительность по биогазу составляет 480 м³ / сут. Для всей биогазовой системы требуется 200 м³ биогаза в сутки зимой и 120 м³ / сутки весной и осенью. Чистый объем биогаза составляет 280 м3 / сут зимой и 360 м3 / сут весной и осенью. Поскольку нет необходимости его нагревать, чистый выход биогаза летом составляет 470 м³ / сутки. Так же, как и БПФ, для нагрева биогазового резервуара используется 150 кг / сутки угля, который длится около 4 месяцев, а количество угля составляет 18 т / год.
2.2. Экстренный учет
Необработанные входные и выходные данные двух биогазовых систем регистрируются за весь 2011 год. Подробности аварийного учета можно найти в работах Одума [16]. Процесс аварийного учета состоит из двух этапов. Первый — определить границы системы, а затем составить таблицу непредвиденных оценок. Следующим шагом является суммирование всех дополнительных вкладов от независимых входов и оценки биогазовых систем, как показано в установленной системе индикаторов аварийных ситуаций.
Срочная система показана на рисунке 2. Входные ресурсы разделены на три части: бесплатные местные возобновляемые ресурсы (RR), включающие сырье (фекалии / кукурузная солома), солнечная энергия и подземный полив, приобретенные возобновляемые ресурсы (RP) включают человеческий труд и приобретенные невозобновляемые ресурсы (NP), включая строительные материалы, уголь и электроэнергию. Все продукты, включая биогаз и остатки биогаза, являются выходом системы (Y). В процессе подсчета все экономические ценности конвертируются в солнечную эмерджету (sej).А затем солнечная эмерджентность превращается в эмерджентно-денежную стоимость (Em $) через эмерджентно-денежное соотношение. В данной статье эмерджентно-денежная стоимость (Em $) представляет не только макроэкономическую ценность эмерджентного потока, но и эколого-экономическую ценность, которая оценивает экоэффективность, воздействие на окружающую среду и устойчивость системы.
2.3. Индекс оценки чрезвычайных ситуаций
Для анализа этих двух типов биогазовых систем с точки зрения эколого-экономической выгоды, экологической выгоды и способности устойчивого развития в данной статье используются десять оценочных индексов.
2.3.1. Коэффициент непредвиденных закупок (PER)
Это соотношение затрат, возникающих при возникновении обратной связи, социальной экономики и общего объема затрат, возникающих при возникновении ситуации. Это зависит от степени зависимости системы от внешних ресурсов.
2.3.2. Естественная чрезвычайная ситуация / чрезвычайная ситуация с закупками
Это соотношение представляет собой исходящую от природных ресурсов, деленную на входную возникающую обратную связь социальной экономики, которая показывает состояние промышленной конкурентоспособности.
2.3.3. Коэффициент непредвиденных инвестиций (EIR)
Это соотношение затрат на возникновение обратной связи социальной экономики и затрат на появление природных ресурсов, которое показывает стоимость системы.
2.3.4. Коэффициент рентабельности для чрезвычайных ситуаций (EYR)
Это соотношение общего объема производства и затрат, возникающих при обратной связи социальной экономики, которое представляет ситуацию в системе производства.
2.3.5. Коэффициент аварийной самообеспеченности (ESR)
ESR показывает способность системы к самообслуживанию. Это выход из природы, деленный на общий выход системы.
2.3.6. Коэффициент обработки отходов (% W)
Это отношение количества отходов (для проекта по производству биогаза, это означает сырье, такое как кукурузная солома и фекалии) к общему объему выбросов системы.Это значение показывает способность обработки отходов всей системы.
2.3.7. Коэффициент экологической нагрузки (ELR)
Это важный показатель окружающей среды, [который означает давление на окружающую среду со стороны системы.] Он равен отношению общей невозобновляемой аварийной энергии, деленной на возобновляемую аварийную энергию.
2.3.8. Коэффициент отдачи обратной связи (FYR)
Этот коэффициент означает возникновение системной обратной связи (для биогазовой системы это часть биогаза, которая нагревается), деленное на возникновение экономической обратной связи, что показывает способность системы к самоорганизации.
2.3.9. Коэффициент использования возобновляемых источников энергии (% R)
Это соотношение возобновляемых источников энергии и исходных ресурсов системы, что означает возобновляемую собственность системы.
2.3.10. Коэффициент устойчивости аварийной ситуации (ESR)
Этот оценочный индекс показывает состояние устойчивости системы, которое равно EYR, деленному на ELR.
3. Результаты и обсуждение
3.1. Экстренный учет
Как показано в Таблице 1, общий аварийный ввод системы BPC составляет sej / год, из которых RR, RP и NP составляют 62%, 3% и 35%, соответственно (показано на Рисунке 3). .Выходной выход биогазовой системы состоит из остатков биогаза и биогаза, а остатки биогаза состоят из трех частей: азотных удобрений, фосфорных удобрений и калийных удобрений. Как показано на Рисунке 4, биогаз является наиболее важным производством, выход которого составляет сейдж / год и составляет 99% от общего выхода выброса. Доля остатков биогаза составляет всего 1%.
| |||||||||||||||||||||||||||||||||||||||||||||||||||||||||||||||||||||||||||||||||||||||||||||||||||||||||||||||||||||||||||||||||||||||||||||||||||||||||||||||||||||||||||||||||||||||||||||||||||||||||||||||||||||||||||||||||||||||||||||||||||||||||||||||||||||||||||||||||||||||||||||||||||||||||||||||||||||||
a Местными невозобновляемыми ресурсами можно пренебречь. b Объекты были разделены на срок службы 20 лет. |
Исходя из данных в таблице 2, общий аварийный ввод системы BPF составляет sej / год, из которых RR, RP и NP составляют 88%, 1% и 11%, соответственно. (Рисунок 5). Что касается RR, твердый навоз и моча (включая смывные сточные воды) составляют 46,50% и 53,50% соответственно. Как и в системе BPC, выходная мощность биогазовой системы также состоит из остатков биогаза и биогаза.Как показано на Рисунке 6, биогаз является наиболее важным производством, выход которого составляет сейдж / год и составляет 75% от общего выхода выброса. Оставшаяся часть остатков биогаза делится на три части: азотные удобрения (3%), фосфорные удобрения (17%) и калийные удобрения (5%).
| ||||||||||||||||||||||||||||||||||||||||||||||||||||||||||||||||||||||||||||||||||||||||||||||||||||||||||||||||||||||||||||||||||||||||||||||||||||||||||||||||||||||||||||||||||||||||||||||||||||||||||||||||||||||||||||||||||||||||||||||||||||||||||||||||||||||||||||||||||||||||||||||||||||||||||||
a Местными невозобновляемыми ресурсами можно пренебречь. b Объекты были разделены на срок службы 20 лет. |
По сравнению с системой BPC, входная выходная мощность системы BPF на 4,38 × 10 17 sej / год больше, чем BPC, потому что RR составляет большую часть системы BPF. В противном случае, по выходу системы БКК, выход биогаза составляет 99%, а биогазового навоза — 1%; По выходу системы БПФ выход биогаза составляет 75%, биогазового навоза — 25%. Причина — различие в характере материалов для разложения, строительном масштабе и технологии разложения.Для системы BPC самая большая цель — производство биогаза; Итак, мы называем этот вид биогазового проекта энергоэкологическим. С другой стороны, система BPF реализует задачу по эффективному обращению с навозом и сточными водами, которая тяготеет к энергоэкологическому типу.
3.2. Эколого-экономический анализ
Биогазовый проект — это одна из схем экологической системы замкнутого сельского хозяйства, имеющая отношение к сельскохозяйственным отходам, и эколого-экономические выгоды могут быть измерены с помощью чрезвычайной денежной стоимости, которая представляет собой особую форму чрезвычайной денежной стоимости, отраженную в экономический рынок.
В таблице 3 общие инвестиционные фонды БПФ и БКК составляют 15 700 долларов США в год и 21 500 долларов США в год соответственно. Ресурсы БНФ (фекалии) покупать не нужно; Итак, инвестиционные фонды системы БПФ включают РП и НП, а фонды системы БКК — РР, РП и НП. Таким образом, система БНФ может ослабить давление правительства и быть достойной широкого продвижения. Напротив, ресурсы BPC (кукурузная солома) необходимо покупать из-за их широкого применения, например, в качестве топлива для нагрева воды и брикетирования топлива для формования.Кроме того, перед анаэробным сбраживанием солому необходимо измельчить. И дополнительные добавки, такие как протеиновый порошок, необходимы в процессе анаэробного пищеварения. Таким образом, RP и NP системы BPC выше, чем у BPF. Кроме того, система БПФ имеет систему солнечного отопления, которая снижает количество угля и электроэнергии; Таким образом, вся потребляемая энергия меньше, чем BPC.
|
Выходы систем BPF и BPC составляют 44 000 долларов США в год и 29 600 долларов США в год соответственно. Основная причина заключается в большом разрыве экономической ценности отходов биогаза, что вызывает различия между технологиями двух биогазовых проектов. Эколого-экономическая ценность систем БПФ и БКК составляет 28 300 долл. США в год и 8 100 долл. США в год соответственно. Поскольку оба материала являются возобновляемыми природными ресурсами, два биогазовых проекта имеют высокую эколого-экономическую ценность и значительные экологические преимущества.Большая часть биогаза из проекта может удовлетворить потребности в энергии; биогазовый навоз можно использовать в качестве органического удобрения для сельскохозяйственных культур, овощей и фруктов. Таким образом, все они улучшают экологическую ценность.
3.3. Анализ индексов оценки чрезвычайных ситуаций
Все индексы оценки чрезвычайных ситуаций классифицируются по эколого-экономической выгоде, экологической выгоде и способности к устойчивому развитию (показано в таблице 4).
|
3.3.1. Эколого-экономическая выгода
PER, естественная аварийная / закупочная аварийная ситуация, EIR и ESR системы BPF в 0,32, 4,49, 0,22 и 1,42 раза больше, чем у системы BPC, соответственно. Это указывает на то, что система БПФ меньше зависит от возобновляемых ресурсов и имеет большую конкурентоспособность, а также более высокую эффективность использования природных ресурсов и самодостаточность, чем системы БКК. Это связано с тем, что материал BPC, кукурузная солома, необходимо закупить, а материал BPF, фекалии, не нуждается в финансовой поддержке.
Что касается чистого вклада в экономику, то, хотя обратная связь, возникающая у двух систем, кажется одинаковой, EYR системы BPF примерно в 1,57 раза больше, чем у систем BPC, потому что система BPF имеет гораздо больший выход, Это означает, что система БПФ отличается низкой стоимостью, хорошей производственной эффективностью, высокой эффективностью использования в чрезвычайных ситуациях и конкурентоспособностью.
По всем предыдущим показателям система БПФ имеет более высокий эколого-экономический эффект, чем система БКК.
3.3.2. Экологические преимущества
% W системы BPF примерно в 1,43 раза больше, чем у систем BPC. Сырьем системы БПФ являются навоз, птица и моча. И общий объем ферментации составляет 624 м 3 , который состоит из реактора первичной ферментации (400 м 3 ) и реактора вторичной ферментации (224 м 3 ). С другой стороны, сырьем для системы БПК является только солома с объемом ферментации 480 м 3 . Объемы обработки отходов системы BPF и системы BPC, преобразованные в ценность солнечной энергии, составляют sej / год и sej / год, что означает, что система BPF имеет более высокую эффективность разложения.
ELR — важный показатель, отражающий степень влияния системы на окружающую среду. ELR для систем BPF и BPC равны 0,13 и 0,53, что меньше 1. Результаты показывают, что две системы оказывают небольшое влияние на окружающую среду. Однако, благодаря более высокому коэффициенту выхода возобновляемых источников энергии и большему количеству обрабатываемых отходов, система БПФ имеет гораздо более высокие экологические преимущества.
3.3.3. Анализ способности устойчивого развития
Чтобы проанализировать способность устойчивого развития, необходимо рассмотреть три части: FYR,% R и ESI.
Первый индекс — FYR. FYR — это отношение аварийной обратной связи системы (для биогазовой системы это часть нагреваемого биогаза), деленное на возникновение экономической обратной связи. Возникновение экономической обратной связи для BPF и BPC составляет sej / год и sej / год, в то время как возникновение самоотдачи — sej / год и sej / год. Предыдущие результаты являются результатом количества энергии, используемой для нагрева реактора первичной ферментации на 400 м³ и реакторов вторичной ферментации на 224 м³. FYR BPF в 1,96 раза больше, чем BPC, что означает, что способность к самоорганизации BPF намного лучше, чем у BPC.
Другой индекс -% R, который указывает на возобновляемый характер биогазовой системы. Возобновляемые источники энергии и новая энергия, посвященная BPF, — это больше, чем система BPC. При этом% R БПФ в 1,36 раза больше, чем у системы БКК. Результаты показывают, что способность системы возобновляемого характера BPF лучше.
Последний индекс, ESI, устанавливает взаимосвязь между окружающей средой и возникающими явлениями. Совершенная биогазовая система имеет не только высокую производительность, но и далеко идущее влияние.ESI BPF в 6,61 раза больше, чем система BPC, что показывает, что система BPF имеет большие возможности для устойчивого развития.
4. Заключение
Крупные и средние биогазовые проекты, в которых используются кукурузная солома и фекалии, имеют высокую эколого-экономическую выгоду. В этом исследовании эколого-экономическая ценность систем БПФ и БКК составляет 28 300 долл. США в год и 8 100 долл. США в год соответственно. В соответствии с денежными, экологическими и человеческими факторами производства, оба типа биогазовых проектов обладают большим потенциалом развития.
Что касается всех вводимых ресурсов, возобновляемые природные ресурсы составляют наибольший процент, что означает, что обе системы обладают хорошей способностью обрабатывать сельскохозяйственные отходы (фекалии и солома сельскохозяйственных культур). В системе BPC количество выходящего биогаза намного больше, чем остатков биогаза. В связи с быстрым развитием биогазовых проектов вторичная переработка отходов и сточных вод стала актуальной темой, а комплексная утилизация остатков биогаза стала первоочередной задачей. Следовательно, необходимо усовершенствовать технологию, чтобы эффективно использовать остатки биогаза.
С точки зрения анализа точки возникновения, система BPF превосходит систему BPC в аспектах эколого-экономической выгоды, экологической выгоды и способности к устойчивому развитию. Этот результат связан с проблемами сезонного сбора и деградации кукурузной соломы. Что касается этой ситуации, система BPC может быть рассмотрена, если анаэробное сбраживание сочетается с другим сырьем, таким как птичий и домашний навоз, моча и бытовой мусор.
Приложения
A.
Примечания к таблице 1: (1) Подземная вода Количество: 2500 кг / день Стандартное значение энергии: 4 кДж / кг Энергия: 2500 кг / день × 4 × 10 3 Дж / кг × 365 дней / год = 3,65 × 10 9 Дж / год (2) Кукурузная солома Количество: 900 кг / день Стандартная энергетическая ценность: 14355,72 кДж / кг Энергия: 900 кг / день × 14355,72 × 10 3 Дж / кг × 365 дней / год = 4,72 × 10 12 Дж / год (3) Человеческие рабочие дни: 4 × 365 дней в год = 1460 дней в год Стандартная энергетическая ценность: 12600 кДж / день Энергия: 1460 дней в год × 12600 кДж / день = 1,84 × 10 10 Дж / год (4) Количество стальных листов: 3.5 × 10 7 г / 20 лет = 1,75 × 10 6 г / год (5) Оборудование, полиэтиленовые трубы Количество: (
0/20 лет) RMB / 8,27 = 5,44 × 10
3 (2000 долларов США) (6) Стоимость строительных работ Количество: (100000/20 лет) RMB / 8,27 = 6,05 × 10 2 (2000 долларов США) (7) Стоимость обслуживания Количество: 5000 RMB / 8,27 = 6,05 × 10 2 (2000 долларов США) $) (8) Количество угля: 18000 кг / год Стандартная энергетическая ценность: 26777,6 кДж / кг Энергия: 18000 кг / год × 26777,6 кДж / кг = 4,82 × 10 11 Дж / год (9) Количество электроэнергии: 30000 кВт · ч / год. Нормативная энергетическая ценность: 3598.24 кДж / кВт · ч Энергия: 30000 кВт · ч / год × 3598,24 кДж / кВт · ч = 1,08 × 10 11 Дж / год (10) Белковый порошок Количество: (182,5 кг / год × 4,2 юаней / кг) / 8,27 = 9,27 × 10 1 (2000 долларов США) (11) Биогаз (с подогревом) Количество: 39600 м 3 / год Стандартная энергетическая ценность: 20920 кДж / м 3 Энергия: 39600 м 3 / год × 20920 кДж / м 3 = 8,28 × 10 11 Дж / год Количество: 76500 м 3 / год Стандартное значение энергии: 20920 кДж / м 3 Энергия: 76500 м 3 / год × 20920 кДж / м 3 = 1.60 × 10 12 Дж / год (12) Биогаз (выход) Количество: 133200 м 3 / год Стандартная энергетическая ценность: 20920 кДж / м 3 Энергия: 133200 м 3 / год × 20920 кДж / м 3 = 2,79 × 10 12 Дж / год Число: 157500 м 3 / год Стандартная энергетическая ценность: 20920 кДж / м 3 Энергия: 157500 м 3 / год × 20920 кДж / м 3 = 3,29 × 10 12 Дж / год (13) Количество азотных удобрений: 6,58 × 10 5 г / год (14) Количество фосфатных удобрений: 3.29 × 10 5 г / год (15) Калийные удобрения Количество: 4,94 × 10 5 г / годB.
Примечания к таблице 2: (1) Солнечная энергия Стандартное значение энергии: 4,1868 × 10 3 Дж / кг · k Энергия: 50 м 3 / d × 10 3 кг / м 3 × 120 d / год × 4,1868 × 10 3 Дж / (кг · k) × 5 k = 1,26 × 10 11 Дж / год (2) Количество твердых удобрений: 4,015 × 10 6 кг / год Всего твердого: 18% Стандартная энергетическая ценность: 13500 кДж / кг Энергия: 4.015 × 10 6 кг / год × 18% × 13500 кДж / кг = 9,76 × 10 12 Дж / год (3) Моча (включая промывные сточные воды) Количество: 12410 м 3 / год Стандартное значение энергии: 6,43 × 10 6 Дж / м 3 Энергия: 12410 м 3 / год × 6,43 × 10 6 Дж / м 3 = 7,98 × 10 10 Дж / год (4) Рабочие дни человека: 3 × 365 дней в год = 1095 дней в год Стандартная энергетическая ценность: 12600 кДж / день Энергия: 1095 дней в год × 12600 кДж / кг = 1,38 × 10 10 Дж / год (5) Стоимость строительных работ Число: (734000 / 30 лет) RMB / 8.27 = 2,96 × 10 3 (2000 долларов США) (6) Оборудование, полиэтиленовые трубы Номер: (1289000/30 лет) RMB / 8,27 = 5,20 × 10 3 (2000 долларов США) (7) Номер вспомогательной работы: (176000/30 лет) RMB / 8,27 = 7,10 × 10 2 (2000 долларов США) (8) Стоимость обслуживания Количество: 5000 RMB / 8,27 = 6,05 × 10 2 (2000 долларов США) (9) Количество угля: 13600 кг / год Стандартная энергетическая ценность: 26777,6 кДж / кг Энергия: 13600 кг / год × 26777,6 кДж / кг = 3,64 × 10 11 Дж / год (10) Количество электроэнергии: 20221 кВт · ч Стандартная энергетическая ценность: 3598.24 кДж / кВт · ч / год Энергия: 20221 кВт · ч / год × 3598,24 кДж / кВт · ч = 7,28 × 10 10 Дж / год (11) Биогаз (с подогревом) Количество: 76500 м 3 / год Стандартная энергетическая ценность: 20920 кДж / м 3 Энергия: 76500 м 3 / год × 20920 кДж / м 3 = 1,60 × 10 12 Дж / год (12) Биогаз (выход) Число: 157500 м 3 / год Стандартная энергетическая ценность: 20920 кДж / м 3 Энергия: 157500 м 3 / год × 20920 кДж / м 3 = 3,29 × 10 12 Дж / год (13) Азотные удобрения Количество: 8.63 × 10 3 кг / год (14) Количество фосфорных удобрений: 1,02 × 10 4 кг / год (15) Количество калийных удобрений: 1,73 × 10 4 кг / год.
Благодарность
Исследования поддерживаются Национальной программой исследований и разработок в области ключевых технологий Китая (№№ 2008BADC4B03 и 2009BAC64B08).
Производство биогаза на заднем дворе из навоза: процесс и использование
Эта статья написана Акинтайо Афолаби, студентом Университета Небраски в Линкольне, в рамках курса по управлению использованием навоза в области инженерии биологических систем.Он был рассмотрен экспертами, чтобы обеспечить точность представленных вопросов. Статья отражает понимание студентом предмета, изучаемого на данном этапе его карьеры. Рик Кёльш, преподаватель факультета.
В этой статье описывается процесс производства и преимущества использования биогаза из навоза для мелких животноводческих хозяйств, особенно в развивающихся странах. Помимо санитарных преимуществ правильного обращения с навозом, в этой статье освещаются и другие преимущества, которые могут быть получены от навоза как источника энергии.Таким образом, поощряя этих фермеров хранить навоз со своих животноводческих ферм для использования, тем самым превращая отходы в ценные ресурсы.
Навоз — это отходы, которые образуются в больших количествах и различаются в зависимости от размера фермы, вида животных и питательных веществ в корме, который скармливают животным. Эти отходы при неправильном обращении представляют серьезную угрозу для окружающей среды. Это связано с тем, что отходы животноводства содержат азот и фосфор в количествах, вредных для здоровья человека и водных животных, если эти питательные вещества попадают в водоемы.Чтобы избежать экологического риска, государственные учреждения в развитых странах регулируют хранение, обработку, переработку, управление и внесение навоза в землю. На сегодняшний день в развивающихся странах такие правила применяются редко. Таким образом, отходы животноводства разбросаны повсюду в сообществах, где разводятся животные, с постоянной причиной экологической опасности и социальных неудобств.
Потребность в биогазе
Из-за других ограничений навоз нельзя вносить в поле сразу после его производства.Традиционно навоз хранят до тех пор, пока не появится возможность его внесения в землю. В промежутке между производством и внесением в поле навоз может использоваться для выработки энергии в метантенках. Тип варочного котла, используемого на фермах, обычно определяется применяемой практикой обращения с навозом и типом навоза, который подается в варочный котел. Жидкий навоз и жидкий навоз крупного рогатого скота и свиней можно использовать в качестве сырья для производства биогаза в метантенках. Восстановление биогаза из отходов животноводства может стать ключом к раскрытию финансовых и экологических выгод от использования навоза, образующегося в результате животноводства, и органических отходов в секторах пищевой промышленности.Это также помогает снизить выбросы парниковых газов от метана (Agstar, 2011). Биогаз образуется в результате деятельности бактерий, которые расщепляют биоразлагаемые компоненты навоза в отсутствие кислорода в герметичной камере. Этот процесс называется анаэробным пищеварением.
Анаэробное сбраживание — это микробная ферментация субстрата в отсутствие кислорода. Это приводит к смеси газов, содержащей метан, диоксид углерода и другие газы, такие как азот и серу, в качестве примесей.Сырье, подаваемое в варочный котел, представляет собой органические материалы с высоким содержанием влаги. Примерами таких органических материалов являются отходы животноводства (навоз), пищевые отходы, остатки после уборки сада или сада. Газовая смесь, произведенная в биореакторе, называется биогазом и может использоваться в качестве топлива. Биогаз содержит от 55 до 65% метана, от 30 до 35% углекислого газа и других газов. Пропорции газов зависят от сырья и других параметров процесса, таких как гидравлическое время пребывания (HRT) и температура.Энергетическая ценность биогаза составляет около 60% (в зависимости от содержания метана) по сравнению с природным газом (Noorolahi et al, 2014) и может быть легко адаптирована для использования для замены природного газа.
Образование биогаза в варочном котле
Процесс образования биогаза из подаваемого сырья можно разбить на четыре этапа. На трех последних стадиях присутствуют различные виды бактерий, которые расщепляют продукцию предшествующей стадии на вещества, необходимые для окончательного образования биогаза из органических материалов, подаваемых в варочный котел.Шаги следующие:
- Гидролиз: это добавление воды к органическому сырью. Это вызывает расщепление углеводов на сахар и глюкозу и превращение белков в аминокислоты. Это преобразование обычно является самым медленным из четырех шагов (Vogeli et al., 2014).
- Второй этап — это действие бактерий, которые воздействуют на кислоты с первого этапа, чтобы подготовить их к следующему этапу процесса преобразования.
- На этом этапе задействованы другие виды бактерий, которые воздействуют на вещества, образованные на предыдущем этапе, чтобы преобразовать их в формы, готовые для заключительного этапа анаэробного процесса
- На этом последнем этапе образующие метан бактерии превращают продукты предыдущих этапов в биогаз, содержащий в основном метан и диоксид углерода.Этот конечный продукт необходимо собрать и сохранить для использования в качестве энергии.
Факторами, влияющими на производимый биогаз, являются температура окружающей среды, pH, сырье, участвующие бактерии и HRT. Варочный котел должен быть герметичным, чтобы избежать утечки биогаза. Варочные котлы также должны быть анаэробными или бескислородными. Температуры, при которых бактерии воздействуют на субстраты для их преобразования в биогаз, подразделяются на психрофильные (41-59 F), мезофильные (95-100 F) и термофильные (118-140 F).Были проведены исследования в трех диапазонах температур, чтобы определить наилучшую температуру в различных случаях и с различным сырьем. По сути, температура определяет виды бактерий, которые будут участвовать в производстве биогаза. Различные виды бактерий процветают в разных диапазонах температур. Более высокие температуры быстрее превращают навоз в биогаз. Оптимальный pH для стабильного анаэробного сбраживания и высокого выхода биогаза находится в диапазоне от 6,5 до 7,5 (Vogeli et al., 2014).
Типы варочных котлов
Рисунок 1: Биогазовая установка с фиксированным куполом (Вигели и др., 2014)Существует много типов варочных котлов в зависимости от строительных материалов и применяемой технологии. Красный кирпич, синтетические мембраны и металлические листы — вот некоторые из материалов, из которых можно построить варочные котлы. Первоначальные затраты и затраты на техническое обслуживание варочных котлов зависят от используемых материалов, размера и применяемой технологии. Кирпичи и цемент приемлемы, но дороги, а сталь быстро корродирует в присутствии газов, содержащих сероводород.Некоторые из популярных типов варочных котлов подразделяются на биогазовые установки с фиксированным куполом и плавучим газгольдером. Биогазовая установка с фиксированным куполом не имеет движущихся частей (Рисунок 1). Он имеет смесительный бак и входной канал, через который сырье попадает в установку. Преобразование отходов в биогаз происходит в основной камере варочного котла. Газовая смесь собирается через газовый трубопровод, расположенный в верхней части камеры для разложения. Остаток процесса выпускается через выпускной патрубок и резервуар для перелива, в то время как газ собирается из шланга в верхней части варочного котла.
Рисунок 2: Биогазовая установка с плавающим куполом (Vigeli et al, 2014)Биогазовая установка с плавающим куполом (Рисунок 2) имеет плавающий «баллон» в верхней части варочного котла, который можно использовать для хранения биогаза в периоды повышенного спроса. и контролировать объем добытого газа. Подвижный компонент типа плавающего газгольдера делает его более дорогим в строительстве и обслуживании по сравнению с фиксированным куполом. Тем не менее, он имеет то преимущество, что операторы могут в любой момент оценить количество уже накопленного биогаза.
Преимущества биогазовых установок
Биогазовые установки обладают многочисленными преимуществами и преимуществами, которые отражаются в улучшении экономики фермы и обеспечивают рациональное использование ресурсов и окружающей среды. Биогаз, производимый на ферме, может дополнять текущую энергию, необходимую ферме. Если на ферме вырабатывается большое количество биогаза, его можно продать соседям для дополнительного дохода ферме. Кроме того, производство биогаза снижает зависимость от ископаемого топлива, которое не является возобновляемым, и смягчает сопутствующее глобальное потепление, постоянно вызываемое сжиганием ископаемого топлива.Другими словами, биогаз производит чистое топливо, которое помогает контролировать загрязнение воздуха в результате сжигания ископаемого топлива.
Еще одно преимущество производства биогаза из навоза состоит в том, что оно снижает загрязнение воды за счет первоначального разложения навоза в варочном котле перед внесением навоза в поле. Анаэробное сбраживание отходов животноводства дает значительные экологические преимущества. К ним относятся снижение биологической потребности в кислороде, наличие патогенов человека, сероводорода и компонентов навоза, связанных с запахом (Ciborowski, 2001).В результате биологического процесса, происходящего в варочном котле, его остаток имеет менее неприятный запах, но сохраняет важные питательные вещества в навозе. Этот остаток можно вносить в землю, как и на другой навоз. При нанесении на землю соблюдайте все меры предосторожности и правила по защите окружающей среды.
Каталожный номер:
Agstar (2011). Возврат стоимости из отходов. Основы системы анаэробного реактора. Объединенное государственное агентство по охране окружающей среды
Noorolllahi Y, Kheirrroutz M, Asl H.е, Youdefi H и Hajinezhad A. (2014). Потенциал производства биогаза из навоза в Иране. Обзоры возобновляемых и устойчивых источников энергии.
Вигели И., Лори К.Р., Галлардо А., Динер С. и Зурбругг К. (2014). Анаэробное переваривание Biowatse в развивающихся странах. Швейцарский институт водных наук и технологий.
Циборовски П. (2001). Анаэробное сбраживание навоза для контроля загрязнения и производства энергии. Оценка осуществимости.
Границы | Последовательная параметрическая оптимизация добычи метана из различных источников лесного сырья
Введение
Наша экономика и производство сильно зависят от использования ископаемого топлива, что приводит ко многим осложнениям, таким как экологические проблемы и отсутствие безопасности в отношении энергоснабжения.Использование ископаемого топлива приводит к выбросу огромного количества углекислого газа в атмосферу, что усугубляет глобальное потепление. Более того, помимо двуокиси углерода, в атмосферу выбрасываются другие загрязнители, такие как окись углерода, углеводороды, твердые частицы и т. Д., Что отрицательно сказывается на здоровье населения. Одной из важных проблем, с которыми сталкиваются многие страны мира, является отсутствие энергетической безопасности, поскольку большинству стран необходимо импортировать ископаемое топливо. Чтобы свести к минимуму негативные последствия использования неустойчивых источников энергии, исследователи сосредотачиваются на разработке возобновляемых видов топлива, которые можно производить за счет использования внутренних источников.Наиболее распространенными источниками биотоплива до сих пор были этанол, биодизель и биогаз.
Биогаз, газообразное биотопливо, состоит в основном из диоксида углерода (CO 2 ) и метана (CH 4 ), но также присутствуют другие второстепенные газы (такие как сероводород и водород) и влага. Соотношение между двумя основными газами влияет на энергосодержание биогаза, которое, по оценкам, составляет от 18 630 кДж / м 3 до 26081 кДж / м 3 (Romano et al., 2009), тогда как природный газ имеет энергосодержание примерно 37000 кДж / м 3 (Martin et al., 2013). Основное применение биогаза — это производство электроэнергии путем сжигания в оборудовании ТЭЦ (комбинированное производство тепла и электроэнергии) или в качестве топлива для транспортных средств (Jeihanipour et al., 2013). Чтобы биогаз можно было использовать в качестве автомобильного топлива, необходимо повысить энергоемкость биогаза за счет увеличения концентрации метана. По этой причине углекислый газ и другие газы следует удалять с помощью таких процессов, как криогенное разделение, химическая абсорбция, мембранное разделение, адсорбция при переменном давлении и адсорбция при колебании температуры (Kapdi et al., 2005; Молино и др., 2013). Наконец, улучшенный биогаз сжижается или сжимается. До недавнего времени только небольшие объемы биогаза направлялись в транспортный сектор (Naik et al., 2010), хотя было бы более важно использовать биогаз в качестве топлива, а не для производства электроэнергии (из-за большого количества альтернатив) .
Одно из преимуществ использования биогаза в качестве топлива заключается в том, что его можно использовать непосредственно в транспортных средствах, требуя всего лишь нескольких модификаций, таких как установка специального топливного бака.Использование метана в качестве автомобильного топлива способствует снижению выбросов парниковых газов (ПГ), поскольку практически не выделяет никаких парниковых газов. Более того, выброс других газов, таких как оксид углерода, углеводороды, соединения серы и оксиды азота, незначителен (Swedish Gas Association, 2011). Тем не менее, производство биогаза считается более эффективным с точки зрения ресурсоэффективности с соотношением выхода и входа, достигающим значений 28 (Jeihanipour et al., 2013; Zheng et al., 2014). Для сравнения, такое же соотношение для биоэтанола рассчитано равным 3,7 для бразильской модели (где сахарный тростник является сырьем) и только 1,1 для модели США (где используется кукуруза; De Oliveira et al., 2005).
Производство биогаза происходит путем анаэробного сбраживания, которое представляет собой сложный многоступенчатый биохимический процесс. Каждый этап этого процесса катализируется отдельной группой микроорганизмов, где все они работают вместе как «сообщество», превращая органические молекулы в биогаз (Li et al., 2011; Parawira, 2012). Анаэробное сбраживание состоит из стадии гидролиза, стадии ацидогенеза, стадии ацетогенеза и стадии метаногенеза. На первом этапе сложные молекулы, такие как полисахариды, гидролизуются до более простых молекул, которые на втором этапе превращаются в летучие жирные кислоты (ЛЖК) и спирты. ЛЖК, более длинные, чем уксусная кислота, превращаются в ацетат, CO 2 и h3 за счет ацетогенов, тогда как на последней стадии ЛЖК превращаются в CH 4 и CO 2 метаногенами (Mshandete et al., 2005; Аду-Гьямфи и др., 2012). Из-за того, что скорость производства ЛЖК выше, чем скорость потребления ЛЖК, если процесс не сбалансирован, существует риск накопления ЛЖК, что приведет к снижению pH и последующему ингибированию метаногенеза. Анаэробное сбраживание обычно выполняется в мезофильных условиях (25–35 ° C) или термофильных условиях (45–60 ° C), при этом термофильное сбраживание имеет некоторые положительные характеристики, такие как более высокая метаногенная активность, более быстрый процесс и меньше проблем с загрязнением (Lesteur et al. al., 2010; Xia et al., 2013). В конце анаэробного сбраживания произведенный дигестат можно использовать в качестве биоудобрения, поскольку он богат азотом, фосфором и калием, что также имеет своеобразную реологию (Adu-Gyamfi et al., 2012; Kafle et al. , 2014).
В настоящее время наиболее часто используемыми материалами для производства биогаза являются навоз, пищевые отходы и городские сточные воды. Использование этого сырья оказалось очень полезным, поскольку уже были достигнуты высокие урожаи, что привело к строительству и эксплуатации коммерческих единиц.С другой стороны, растущая потребность в биогазе приводит к острой необходимости включения нового возобновляемого сырья в производственную линию биогаза. Лигноцеллюлозная биомасса является отличным кандидатом для использования в качестве сырья и в последние годы вызвала большой интерес исследователей. Его можно получить из различных источников, таких как сельскохозяйственные и лесные остатки. Лесное хозяйство — очень важная часть шведской экономики, и общий объем древостоя в Швеции составляет приблизительно 3 000 миллионов м3 3 с ежегодным увеличением запасов на 40 миллионов м3 3 (www.svenskttra.se), что является результатом очень хорошего ведения лесного хозяйства. Основными породами деревьев в Швеции являются ель обыкновенная ( Picea abies ), сосна обыкновенная ( Pinus sylvestris ) и береза ( Betula pendula и B. pubescens ), что составляет 41, 40 и 18%. от общего объема древостоя.
Лигноцеллюлозные материалы имеют низкую перевариваемость, поэтому выход метана низкий, что делает необходимым этап предварительной обработки перед перевариванием. Были оценены различные виды предварительной обработки для повышения выхода метана из лесной биомассы, такие как паровой взрыв (Nakamura and Mtui, 2003; Horn et al., 2011), ионных жидкостей (Тегаммар и др., 2012; Кабир и др., 2014), органосольв (Кабир и др., 2015) и сверхкритической воды (Йошида и др., 2010). С другой стороны, предварительная обработка может привести к разложению сахаров и образованию ингибирующих соединений, которые могут препятствовать анаэробному пищеварению. Чтобы снизить уровень ингибиторов, можно использовать процесс детоксикации. Во время ферментации этанола уже были оценены различные методы детоксикации, такие как обработка восстанавливающими агентами (Alriksson et al., 2011; Xiros and Olsson, 2014), с лакказой (Moreno et al., 2013) или с растворами линейного полиэтиленимина (Cannela et al., 2014), но мало что известно о влиянии детоксикации на анаэробное пищеварение. Наконец, несмотря на то, что микроорганизмы, присутствующие в иле, способны использовать нерастворимые углеводы, наша группа ранее показала, что добавление гидролитических ферментов может увеличить выход метана (Matsakas et al., 2014).
По этой причине целью данной работы была оценка возможности использования основных древесных пород в Швеции в качестве сырья для анаэробного сбраживания.Кроме того, было исследовано влияние предварительной гидротермальной обработки, детоксикации суспензии и ферментативного гидролиза на выход метана.
Материалы и методы
Сырье и ферменты
Необработанные лесные остатки предоставлены SLU (Умео, Швеция). Общее количество твердых веществ (TS) и летучих твердых веществ (VS) материалов было следующим (мас. / Мас.): Ель, 90,81% TS и 90,49% VS; сосна, 91,45% TS и 91,26% VS; береза, 92,07% ТС и 91,86% ВС. Термофильный анаэробный отстой, использованный во время этой работы, был собран на биогазовой установке в Бодене, Швеция, где отстой сточных вод и пищевые отходы перевариваются совместно.
Целлюлолитические ферменты, использованные в этой работе, представляли собой коммерческие растворы ферментов Celluclast ® 1,5 л и Novozym ® 188 (Novozymes A / S, Багсверд, Дания) в соотношении 5: 1 об. / Об. Активность смеси составила 83 единицы фильтровальной бумаги (FPU) / мл. Ферментативную детоксикацию проводили с использованием лакказы гриба Pycnoporus cinnabarinus , любезно предоставленной Beldem (Бельгия), с заявленной активностью 13 МЕ / мл.
Предварительная обработка остатков леса
Гидротермальная предварительная очистка проводилась на заводе SEKAB в Эрншельдсвике (Швеция) в непрерывном режиме. Диоксид серы использовался в качестве катализатора во время предварительной обработки в концентрации 1 кг на 40 кг биомассы (Soudham et al., 2011). Различные источники биомассы были предварительно обработаны при различных комбинациях времени выдержки и температуры (Таблица 1), и pH после предварительной обработки варьировался в зависимости от степени тяжести процесса (Таблица 1).Полученные суспензии имели различное содержание твердых веществ, которое в отношении TS и VS было следующим (мас. / Мас.): Предварительно обработанная ель, 25,81% TS и 25,55% VS; мягкая предварительно обработанная ель, 23,48% TS и 23,28% VS; сосна, 19,51% TS и 19,38% VS; береза, 21,69% ТС и 21,60% ВС.
ТАБЛИЦА 1. Условия предварительной обработки материалов, использованных во время этой работы.
Ферментативное осахаривание предварительно обработанных суспензий
Чтобы оценить влияние предварительной обработки на ферментативную перевариваемость суспензий, была проведена серия экспериментов по ферментативному осахариванию.В эти эксперименты были включены как необработанные, так и обработанные материалы. Когда использовались предварительно обработанные материалы, чтобы облегчить обращение, небольшие количества суспензий перед экспериментами сушили при 70 ° C. Ферментативный гидролиз проводили при содержании твердого вещества 3% мас. / Об. В термомиксере Эппендорфа при 50 ° C в течение 24 часов. PH раствора доводили до 5, используя 100 мМ цитрат-фосфатный буфер. К смеси добавляли азид натрия в концентрации 0,01% мас. / Об., Чтобы предотвратить микробное загрязнение.Образцы через 0 и 24 часа инкубации центрифугировали, а супернатанты анализировали на наличие растворимых сахаров.
Детоксикация суспензий
В ходе этой работы были оценены два различных процесса детоксикации: химический и ферментативный. Химическая детоксикация заключалась в обработке дитионитом натрия. Концентрация дитионита натрия была установлена на уровне 10 мМ или 1 мМ, и обработка проводилась одновременно с анаэробным перевариванием. После добавления соли измеряли pH ила, чтобы убедиться, что это не повлияло на него.
Обработку лакказой проводили перед перевариванием в течение 12 ч при 50 ° C в аэробных условиях. Суспензии разбавляли дистиллированной водой, чтобы получить конечную концентрацию твердых веществ 10% мас. / Об., И использованная ферментная нагрузка составляла 10 МЕ / г VS. Наконец, pH суспензии был увеличен до 5,5 путем добавления соответствующих количеств NaOH.
Ферментативная обработка суспензий целлюлолитическими ферментами
Для ферментативной обработки суспензий использовали два различных процесса, а именно обработку вместе с перевариванием и предварительное осахаривание.Во время одновременной обработки целлюлолитические ферменты добавляли к илу в начале переваривания. С другой стороны, когда была включена стадия предварительного осахаривания, суспензии разбавляли до концентрации твердого вещества 10% мас. / Об. И осахаривание происходило при 50 ° C в течение 12 часов. PH также поддерживали на уровне 5,5 добавлением NaOH. В обеих конфигурациях применяли две загрузки фермента (15 FPU / г VS и 30 FPU / г VS), чтобы оценить влияние активности фермента на выход метана.Наконец, стоит упомянуть, что когда обработка лакказой применялась к конкретной суспензии, тогда обе ферментативные обработки выполнялись одновременно (в случае предварительного осахаривания).
Тесты биохимического метанового потенциала (BMP)
Для оценки перевариваемости субстратов использовали тесты BMP. Более конкретно, тесты BMP были выполнены с использованием системы AMPTS II (Bioprocess Control AB, Лунд, Швеция). Система состоит из трех частей: колбы для разложения, блока фиксации CO 2 и блока расходомера.Колбы для разложения представляют собой стеклянные бутыли емкостью 500 мл; они были заполнены 400 г ила и субстратом. Блок фиксации СО2 состоит из стеклянных бутылок емкостью 100 мл; они были заполнены примерно 80 мл 3 М NaOH для «улавливания» всех других газов, кроме метана. Тимолфталеин был добавлен в качестве индикатора pH, чтобы проверить, что раствор оставался активным. Наконец, блок расходомера состоит из набора ячеек расходомера, в которых производится подсчет метана. Значения объема метана соотносятся с нормализованным объемом.
В каждую серию экспериментов также были включены два контрольных образца. Первый содержал отстой, чтобы рассчитать метан, произведенный органической нагрузкой, оставшейся в отстое, а второй контроль содержал фермент (целлюлазы или лакказа, отдельно или вместе), который использовался для подсчета количества метана, образующегося при переваривании ферментов. Значения метана как в осадке, так и в ферментах вычитали из общего количества метана, чтобы рассчитать выход метана только из субстрата.Наконец, был также включен положительный контроль, когда в качестве сырья использовалась целлюлоза avicel, чтобы оценить качество ила.
Переваривание проводили в двух экземплярах, и отношение I / S (отношение инокулята к твердому веществу) было установлено равным 2 в пересчете на VS. Переваривание проводили при 55 ° C, и в каждую колбу добавляли минеральный и солевой раствор, состав которых описан в другом месте (Antonopoulou and Lyberatos, 2013). Перед перевариванием колбы промывали барботажем примерно на 1 час.5 мин с азотом для удаления кислорода.
Аналитические методы
TS и зольность определяли гравиметрически после сушки в течение 24 ч при 105 ° C и обжига в течение 2 ч при 550 ° C соответственно. Чтобы определить содержание VS, зольность была вычтена из содержания TS. Общее количество восстанавливающих сахаров во время экспериментов по ферментативному гидролизу определяли в соответствии с методом DNS (Miller, 1959). Ферментативная активность смеси Celluclast ® 1.5L и Novozym ® 188 определяли стандартным методом активности фильтровальной бумаги (Ghose, 1987). Сахара из структурного анализа углеводов, а также ингибиторы определяли с использованием аппарата ВЭЖХ, оборудованного детектором Series 200 RI (показатель преломления) (PerkinElmer). Более конкретно, во время анализа сахара использовали Aminex HPX-87P с ультрачистой водой в качестве подвижной фазы. Скорость потока была установлена на 6 мл / мин, и колонка поддерживалась при 85 ° C. Для ингибиторов использовали колонку Aminex HPX-87H с 5 мМ H 2 SO 4 в качестве подвижной фазы.Скорость потока была установлена на уровне 0,6 мл / мин, и колонка поддерживалась при 65 ° C.
Результаты
Выходы метана из необработанных материалов
На начальном этапе работы оценивалась возможность использования необработанной ели, сосны и березы в качестве сырья для анаэробного сбраживания. Наибольший урожай был получен с березы, и он достиг всего 17,5 ± 1,9 мл CH 4 / г ТС, тогда как урожай, полученный от ели и сосны, был еще ниже (рис. 1). В попытке улучшить выход метана мы изучили эффект добавления целлюлолитических ферментов.Как описано ранее, анаэробный ил способен гидролизовать нерастворимые углеводы, такие как целлюлоза. С другой стороны, добавление внешних ферментов может облегчить этот процесс и улучшить выход метана. Применяли две различные загрузки фермента, а именно 15 FPU / г и 30 FPU / г. Присутствие ферментов улучшило выход метана из всех материалов, причем самый высокий выход (40 ± 3 мл CH 4 / г VS) был получен при использовании 30 FPU / г для березы (рис. 1). С другой стороны, добавление фермента немного улучшило урожай ели.Несмотря на то, что выходы были улучшены по сравнению с перевариванием без добавления ферментов, выходы были низкими, чтобы их можно было рассматривать как эффективное анаэробное сбраживание.
РИСУНОК 1. Выход метана из необработанных материалов без добавления ферментов (первый столбец) и с добавлением 15 FPU / г фермента (второй столбец) и 30 FPU / г фермента (третий столбец).
Влияние предварительной гидротермальной обработки на усвояемость остатков и выход метана
На этом этапе работ на заводе SEKAB (Örnsköldsvik, Швеция) была использована предварительная гидротермальная обработка с SO 2 в качестве катализатора.Материалы обрабатывали при различных комбинациях температуры и времени выдержки, что приводило к разному pH после предварительной обработки (таблица 1). Обработанные материалы собирали в виде суспензии с общим содержанием твердого вещества от 19,5 до 25,8% мас. / Об., А состав жидкости (в ингибиторах) и твердых фракций представлен в таблице 2.
ТАБЛИЦА 2. Структурный анализ и анализ ингибитора твердой и жидкой фракций соответственно.
На первом этапе была исследована усвояемость предварительно обработанных материалов.По этой причине суспензии, полученные после предварительной обработки, переваривали при низкой концентрации твердых веществ с использованием ферментной нагрузки 10 FPU / г твердых веществ. Предварительная обработка улучшила высвобождение редуцирующих сахаров до 6,7 раз по сравнению с необработанными материалами (рис. 2). Наибольшее улучшение наблюдалось для березы, тогда как для ели интенсивная предварительная обработка лишь незначительно улучшила осахаривание по сравнению с мягкой предварительной обработкой.
РИСУНОК 2. Высвобождение TRS из необработанных материалов (темно-серый) и предварительно обработанных материалов (светло-серый) через 24 часа ферментативного расщепления с ферментной нагрузкой 10 FPU / г и содержанием твердых веществ 3% мас. / Мас. Для предварительно обработанной ели первый и второй столбцы представляют мягкие и тяжелые условия обработки, соответственно.
На следующем этапе также оценивали влияние предварительной обработки на анаэробный ил. Как видно на Рисунке 3, выход метана был значительно улучшен для всех типов лесных материалов по сравнению с выходом метана без предварительной обработки. Наибольший выход метана был получен для березы, достигнув 254,1 ± 3 мл Ch5 / г ТС, что примерно в 14,5 раз превышало выход, полученный из необработанной березы.С другой стороны, самый низкий урожай наблюдался у ели, подвергнутой умеренной предварительной обработке, и достигал лишь 95,4 ± 2,5 мл Ch5 / г VS. При использовании материалов из мягкой древесины выход метана линейно увеличивался по мере увеличения SF (рис. 4).
РИСУНОК 3. Выход метана из предварительно обработанных гидротермально материалов.
РИСУНОК 4. Корреляция между выходом метана и SF при предварительной обработке.
Влияние детоксикации суспензий на выход метана
В ходе этой работы мы изучили влияние ферментативного и химического подходов (основанных на использовании лакказы и дитионата натрия соответственно) на детоксикацию образовавшихся ингибиторов.Ферментативная обработка проводилась за 12 часов до анаэробного расщепления, чтобы фермент действовал в присутствии кислорода. Ферментную нагрузку устанавливали на уровне 10 Ед / г VS. С другой стороны, химическая обработка происходила одновременно с пищеварением.
При использовании 10 мМ дитионита натрия концентрация, которая ранее была признана оптимальной для детоксикации гидролизатов ели для производства этанола (Alriksson et al., 2011), он подавлял анаэробное расщепление (данные не показаны), и это ингибирующий эффект все еще наблюдался до некоторой степени, даже когда концентрация была снижена до 1 мМ (рис. 5).Эти результаты показывают, что, несмотря на то, что дитионит натрия можно использовать для детоксикации гидролизатов при ферментации этанола, он не подходит для использования при анаэробном сбраживании. С другой стороны, когда лакказа использовалась для детоксикации, она оказалась более эффективной для лесного сырья, прошедшего предварительную обработку в более жестких условиях, и повысила выход метана из ели и сосны на 14,3 и 9,8% соответственно (рис. ).
РИСУНОК 5. Выходы метана из недетоксифицированного материала (первый столбец), материала, детоксифицированного дитионитом натрия (второй столбец), и материала, детоксифицированного с помощью лакказы (третий столбец).
Влияние обработки целлюлазой на выход метана
Были исследованы две различные конфигурации процесса: гидролиз одновременно с анаэробным перевариванием и отдельный этап осахаривания перед перевариванием. В обеих конфигурациях использовали две загрузки фермента (15 и 30 FPU / г VS). Добавление ферментов улучшило выход метана в обеих конфигурациях процесса с обеими ферментными нагрузками (рис. 6). Хотя оба процесса были полезными, обработка перед осахариванием дала более высокий выход метана, чем одновременная обработка для всех материалов, кроме березы.Из всех материалов сосна показала наименьшую степень улучшения при включении ферментов. С другой стороны, наибольшее улучшение наблюдалось у ели (как слабой, так и сильно обработанной). Самый высокий выход метана был получен из березы, когда ферментативная обработка проводилась одновременно с вывариванием, используя ферментную нагрузку 15 FPU / г VS. Этот выход достиг 304,8 ± 6,35 мLCH 4 / г VS, тогда как увеличение ферментативной нагрузки не привело к дальнейшему улучшению выхода метана.
РИСУНОК 6. Влияние ферментативной обработки на выход метана, когда она имела место до (A) и вместе с (B) на переваривание. Первый столбец представляет собой контроль без добавления фермента, а второй и третий столбцы представляют собой добавление фермента при нагрузке 15 FPU / г и 30 FPU / г, соответственно.
Обсуждение
В ходе этой работы различные источники лесной биомассы были оценены как сырье для анаэробного сбраживания. Первоначально оценивалась способность переваривать лесной материал без какой-либо обработки.Несмотря на то, что был продемонстрирован высокий выход метана из необработанных сельскохозяйственных остатков (Bauer et al., 2009; Lei et al., 2010), лесные остатки считаются более «жестким» сырьем, и по этой причине урожайность, полученная из необработанных материалов часто бывает очень мало (Nakamura and Mtui, 2003; Yoshida et al., 2010). Аналогичные (низкие) результаты по выходу метана были также получены во время этой работы при использовании необработанных материалов, достигая максимального значения 17,5 ± 1,9 мл CH 4 / г ТС при использовании березы (рис. 1).Добавление целлюлолитических ферментов облегчило анаэробное пищеварение и повысило выход метана, получаемого из лесных материалов. Из результатов, описанных выше, можно сделать вывод, что необработанные лесные материалы нельзя использовать в качестве сырья для анаэробного сбраживания, поскольку полученные урожаи были очень низкими даже с добавлением целлюлазы.
Обычно, когда лигноцеллюлозные материалы используются для анаэробного переваривания, считается, что лимитирующей стадией процесса является гидролиз полисахаридов (холоцеллюлозы или целлюлозы и гемицеллюлозы) до мономерных сахаров (Parawira, 2012).Из-за сложной природы холоцеллюлозы и лигнина необработанные материалы обладают высокой устойчивостью к атакам микробов. Чтобы снизить устойчивость холоцеллюлозы к деградации, перед перевариванием необходима некоторая предварительная обработка (Bruni et al., 2010). В ходе нашей работы применялась предварительная гидротермальная обработка, в которой в качестве катализатора использовался диоксид серы. Гидротермальная предварительная обработка считается эффективным методом обработки лигноцеллюлозной биомассы и широко изучалась при производстве этанола из лигноцеллюлозной биомассы (Negro et al., 2003; Мацакас и Христакопулос, 2013 г .; Nitsos et al., 2013; Paschos et al., 2015). Все предварительно обработанные материалы продемонстрировали увеличение выхода метана, достигающее максимального значения 254,1 ± 3 мл CH 4 / г ТС при использовании березы. Урожайность сосны и ели была ниже, чем у березы, при этом у мягкой предварительно обработанной ели были самые низкие результаты среди всех предварительно обработанных материалов. Разницу в выходе метана, полученную при использовании березы и других лесных материалов, можно объяснить тем фактом, что береза относится к твердым породам, тогда как ель и сосна относятся к мягким породам.Известно, что древесина хвойных пород более стойкая, чем древесина твердых пород (Kim and Hong, 2001; Palonen et al., 2004; Mirahmadi et al., 2010), и это различие в устойчивости обычно объясняется различными типами лигнина, поскольку древесина твердых пород содержит смесь гваяцильных и сирингильных звеньев, а древесина хвойных пород содержит в основном гваяцильные звенья в лигнине (Taherzadeh and Karimi, 2008). Этим можно объяснить более низкие урожаи хвойных пород в ходе этой работы.
Такое же значительное улучшение выхода метана было также описано Салехианом и Карими (2013) из ветвей сосны, когда они были предварительно обработаны щелочью.Такой же положительный эффект предварительной обработки на выход метана из лигноцеллюлозных материалов был обнаружен также у березы после парового взрыва (Vivekanand et al., 2013), у ели и сосны после предварительной щелочной обработки (Mirahmadi et al., 2010) и у ели, предварительно обработанной ионные жидкости (Тегаммар и др., 2012).
Хотя процесс предварительной обработки приводит к более легкой гидролизуемой биомассе и последующему более высокому образованию метана, во время этого процесса могут образовываться ингибирующие соединения. Эти соединения в основном получают из углеводной фракции или лигниновой фракции.Этими ингибиторами могут быть гидроксиметилфурфурол (HMF) от разложения сахаров C6, фурфурол от разложения сахаров C5 и полимерный лигнин или ароматические соединения, такие как сиреневый альдегид или 4-гидроксибензойная кислота, от разложения лигнина. Кроме того, могут быть получены слабые органические кислоты, такие как муравьиная кислота и уксусная кислота. Во время анаэробного сбраживания алифатические кислоты не являются проблемой (в отличие от ферментации этанола), поскольку они могут потребляться на стадии метаногенеза. Более того, не было обнаружено, что HMF и фурфурол ингибируют переваривание ксилозы, и они могут потребляться илом с образованием метана (Barakat et al., 2012). С другой стороны, фенольные соединения, которые выделяются из лигнина, такие как фенол, коричный альдегид или 4-гидроксибензойная кислота, могут быть потенциальными ингибиторами анаэробного осадка (Sierra-Alvarez and Lettinga, 1991; Hernandez and Edyvean, 2008). Такие фенольные соединения были обнаружены в гидролизатах влажного окисленного и взорванного паром жома сахарного тростника (Martín et al., 2007; Kayembe et al., 2013).
Ферментативная обработка на основе лакказы использовалась для улучшения ферментируемости предварительно обработанных суспензий за счет уменьшения количества фенольных соединений (Jönsson et al., 1998; Хурадо и др., 2009; Морено и др., 2012). С другой стороны, преимущество использования химических восстановителей для детоксикации заключается в том, что их можно применять во время ферментации, и нет необходимости в отдельном этапе (Cavka et al., 2011). Также было упомянуто, что обычно оксианионы серы (например, дитионит натрия) действуют посредством сульфонатных ароматических соединений и фурановых альдегидов (Cavka et al., 2011). Дитионит натрия оказался полезным для улучшения ферментируемости предварительно обработанной лигноцеллюлозной биомассы (Alriksson et al., 2011; Ксирос и Олссон, 2014). Несмотря на то, что обработка дитионитом натрия была эффективной в снижении ингибирующего эффекта во время ферментации этанола, во время нашего испытания это привело к снижению выхода метана (рис. 5). С другой стороны, обработка лакказы улучшила выход метана на ели и сосне, подвергнутых интенсивной обработке. В обоих материалах SF был выше 4, и это могло привести к образованию большего количества ингибиторов, чем для материалов, обработанных с более низким SF. Для материалов, которые были предварительно обработаны при более низком SF, обработка лакказой не оказала никакого влияния на выход метана.Различие в эффекте детоксикации лакказы также можно объяснить концентрацией ингибиторов в жидкой фракции. Как видно из Таблицы 2, количества HMF и фурфурола были выше у ели и сосны, подвергнутых строгой предварительной обработке, за которыми следовали береза и ель, подвергавшаяся легкой предварительной обработке. Более того, левулиновая кислота была обнаружена только у ели и сосны, подвергнутых строгой предварительной обработке (Таблица 2).
Наконец, мы исследовали влияние обработки суспензий целлюлазой на выход метана. Как упоминалось ранее, гидролиз углеводов до мономерных сахаров считается ограничивающей скорость частью анаэробного переваривания лигноцеллюлозной биомассы.Консорциум, присутствующий в анаэробном иле, обладает способностью секретировать лигноцеллюлолитические ферменты и расщеплять полимерные углеводы. С другой стороны, было показано, что добавление раствора внешнего фермента может повысить эффективность разложения нерастворимых углеводов (Antonopoulou and Lyberatos, 2013; Matsakas et al., 2014). Использование целлюлолитических ферментов для увеличения выхода метана, когда лигноцеллюлозная биомасса используется в качестве сырья, не очень распространена в литературе, несмотря на положительный эффект, который она оказывает.С другой стороны, ферменты больше используются для обработки других материалов, таких как зерна пшеницы (Sonakya et al., 2001), твердые бытовые отходы (Rintala and Ahring, 1994) и сточные воды молочных производств (Mendez et al., 2006). Также было продемонстрировано, что стадия добавления ферментов имеет важное влияние на выход метана. Например, Romano et al. (2009) пришли к выводу, что добавление фермента — либо на той же стадии пищеварения, либо в качестве предварительного гидролиза — не улучшило выход метана из ростков пшеницы Jose Tall.С другой стороны, они обнаружили улучшение с 220 мLCH 4 / г VS до 290 мLCH 4 / г VS, когда ферменты добавляли на первой стадии двухэтапного анаэробного расщепления. Во время нашей работы присутствие ферментов было полезным для выхода метана независимо от стадии, на которой ферменты были включены (до или одновременно с перевариванием), и ферментной нагрузки. В целом одновременная ферментативная обработка была более эффективной для всех материалов, кроме березы. Добавление более высоких ферментов было полезно для ели и предварительно гидролизованной сосны.С другой стороны, более высокая активность ферментов не влияла на выход метана из березы и оказывала негативное влияние на сосну, когда ее обрабатывали одновременно с перевариванием. Наивысшие результаты были получены для березы, достигающей 304,8 ± 6,35 мLCH 4 / г VS, когда ферментная нагрузка составляла 15 FPU / г VS, применялась перед перевариванием. Это хорошо согласуется с результатами, полученными ранее, когда береза была признана наиболее эффективным сырьем независимо от обработки. Лесные материалы также использовались другими исследователями после различных видов предварительной обработки (Таблица 3).Доказано, что береза является наиболее эффективным материалом для анаэробного сбраживания, тогда как предварительная обработка всегда приводила к увеличению выхода метана. Хотя некоторые работы продемонстрировали более высокий выход метана, улучшение выхода метана по сравнению с необработанными материалами, достигнутое во время нашей работы, было самым высоким (Таблица 3).
ТАБЛИЦА 3. Сравнение результатов, полученных в ходе этой работы, с другими исследовательскими работами в литературе.
Заключение
Мы продемонстрировали, что лесные остатки могут быть эффективным сырьем для анаэробного сбраживания. Из-за их сложной структуры необходима предварительная обработка материалов для увеличения выхода метана. В ходе нашей работы мы обнаружили, что предварительная гидротермальная обработка может быстро увеличить производство метана из всех используемых материалов. Если предварительная обработка проводится в тяжелых условиях, необходима детоксикация. Мы также обнаружили, что детоксикация дитионитом натрия приводит к частичному ингибированию процесса — в отличие от ферментации этанола, где такая детоксикация полезна.С другой стороны, детоксикация с помощью лакказы может улучшить выход метана. Наконец, введение ферментативной обработки приводит к дальнейшему повышению выхода метана. Обработка, проводимая вместе с пищеварением, оказалась полезной для ели и сосны, тогда как предварительное осахаривание было более подходящим для березы. Все материалы были успешно использованы для эффективного анаэробного сбраживания, что привело к высоким выходам 179,9 мл CH 4 / г VS и 304,8 мл CH 4 / г VS для сосны и березы, соответственно, и 259.4 мл CH 4 / г VS и 276,3 мл CH 4 / г VS для ели, подвергнутой легкой и жесткой предварительной обработке, соответственно. Эти выходы являются одними из самых высоких, продемонстрированных в литературе, в то время как мы также продемонстрировали способность облегчить анаэробное пищеварение путем ферментативной детоксикации и осахаривания.
Авторские взносы
Все авторы (LM, UR и PC) совместно участвовали во всех аспектах работы, описанных в рукописи. Все авторы читали и одобрили окончательный вариант рукописи.
Заявление о конфликте интересов
Авторы заявляют, что исследование проводилось при отсутствии каких-либо коммерческих или финансовых отношений, которые могут быть истолкованы как потенциальный конфликт интересов.
Благодарности
Мы благодарим Bio4Energy, среду стратегических исследований, назначенную правительством Швеции, за поддержку этой работы. LM также благодарит Фонд Кемпе за финансовую поддержку.
Сноски
- http: // www.svenskttra.se/MediaBinaryLoader.axd?MediaArchive_FileID=eb34da70-248d-4e78-b7cf-9592aca6c0db&FileName=Forest.pdf
Список литературы
Аду-Гьямфи, Н., Рао Равелла, С., и Хоббс, П. Дж. (2012). Оптимизация анаэробного сбраживания путем выбора иммобилизующей поверхности для увеличения производства метана. Биоресурсы. Technol. 120, 248–255. DOI: 10.1016 / j.biortech.2012.06.042
PubMed Аннотация | CrossRef Полный текст | Google Scholar
Альрикссон, Б., Кавка, А., и Йонссон, Л. Дж. (2011). Повышение ферментируемости ферментативных гидролизатов лигноцеллюлозы за счет химической детоксикации in-situ с помощью редуцирующих сахаров. Биоресурсы. Technol. 102, 1254–1263. DOI: 10.1016 / j.biortech.2010.08.037
PubMed Аннотация | CrossRef Полный текст | Google Scholar
Антонопулу, Г., Либератос, Г. (2013). Влияние предварительной обработки биомассы сладкого сорго на образование метана. Валоризация отходов биомассы 4, 583–591.DOI: 10.1007 / s12649-012-9183-x
CrossRef Полный текст | Google Scholar
Баракат А., Монлау Ф., Стейер Дж. П. и Каррере Х. (2012). Влияние производных лигнина и фурановых соединений, содержащихся в лигноцеллюлозных гидролизатах, на производство биометана. Биоресурсы. Technol. 104, 90–99. DOI: 10.1016 / j.biortech.2011.10.060
PubMed Аннотация | CrossRef Полный текст | Google Scholar
Бауэр А., Беш П., Фридл А. и Амон Т. (2009). Анализ метанового потенциала соломы пшеницы, взорванной паром, и оценка выхода энергии при комбинированном производстве этанола и метана. J. Biotechnol. 142, 50–55. DOI: 10.1016 / j.jbiotec.2009.01.017
PubMed Аннотация | CrossRef Полный текст | Google Scholar
Бруни Э., Дженсен А. П. и Ангелидаки И. (2010). Сравнительное исследование механической, гидротермальной, химической и ферментативной обработки расщепленных биоволокон для улучшения производства биогаза. Биоресурсы. Technol. 101, 8713–8717. DOI: 10.1016 / j.biortech.2010.06.108
PubMed Аннотация | CrossRef Полный текст | Google Scholar
Каннела, Д., Свединг, П. В., и Йоргенсен, Х. (2014). Детоксикация PEI предварительно обработанной ели для ферментации этанолом с высоким содержанием твердых веществ. Appl. Энергия 132, 394–403. DOI: 10.1016 / j.apenergy.2014.07.038
CrossRef Полный текст | Google Scholar
Кавка, А., Алрикссон, Б., Анлунд, М., и Йонссон, Л. Дж. (2011). Влияние оксианионов серы на ингибиторы ферментации на основе лигноцеллюлозы. Biotechnol. Bioeng. 108, 2592–2599. DOI: 10.1002 / бит. 23244
PubMed Аннотация | CrossRef Полный текст | Google Scholar
Де Оливейра, М.Э. Д., Воган, Б. Э., и Рикель, Э. Дж. (2005). Этанол как топливо: энергия, баланс углекислого газа и экологический след. Bioscience 55, 593–602. DOI: 10.1641 / 0006-3568 (2005) 055 [0593: EAFECD] 2.0.CO; 2
CrossRef Полный текст | Google Scholar
Эрнандес, Дж. Э., и Эдивин, Р. Дж. Дж. (2008). Подавление производства и биоразлагаемости биогаза замещенными фенольными соединениями в анаэробном иле. J. Hazard. Матер. 160, 20–28. DOI: 10.1016 / j.jhazmat.2008.02.075
PubMed Аннотация | CrossRef Полный текст | Google Scholar
Хорн, С. Дж., Эстевес, М. М., Нильсен, Х. К., Линьордет, Р., и Эйсинк, Г. Х. (2011). Производство биогаза и осахаривание Salix, предварительно обработанного в различных условиях парового взрыва. Биоресурсы. Technol. 102, 7932–7936. DOI: 10.1016 / j.biortech.2011.06.042
PubMed Аннотация | CrossRef Полный текст | Google Scholar
Джейханипур, А., Асланзаде, С., Раджендран, К., Баласубраманян, Г., и Тахерзаде, М. Дж. (2013). Высокопроизводительное производство биогаза из текстильных отходов с использованием двухэтапного процесса. Обновить. Энергия 52, 128–135. DOI: 10.1016 / j.renene.2012.10.042
CrossRef Полный текст | Google Scholar
Йонссон, Л. Дж., Палмквист, Э., Нильвебрант, Н. О., и Хан-Хэгердал, Б. (1998). Детоксикация гидролизатов древесины лакказой и пероксидазой из грибка белой гнили Trametes versicolor . Appl. Microbiol. Biotechnol. 49, 693–697.
Google Scholar
Хурадо, М., Прието, А., Мартинес-Алькала, А., Мартинес, А. Т., и Мартинес, М. Дж. (2009). Лакказная детоксикация паровой взорванной пшеничной соломы для получения биоэтанола второго поколения. Биоресурсы. Technol. 100, 6378–6384. DOI: 10.1016 / j.biortech.2009.07.049
PubMed Аннотация | CrossRef Полный текст | Google Scholar
Кабир М. К., Раджендран К., Тахерзаде М. Дж. И Хорват И. С. (2015). Экспериментально-экономическая оценка биоконверсии лесных остатков в биогаз с использованием предварительной обработки органосольв. Биоресурсы. Technol. 178, 201–208. DOI: 10.1016 / j.biortech.2014.07.064
PubMed Аннотация | CrossRef Полный текст | Google Scholar
Кабир М. М., Никлассон К., Тахерзаде М. Дж. И Хорват И. С. (2014). Производство биогаза из лигноцеллюлоз путем предварительной обработки N-метилморфолин-N-оксида (NMMO): эффекты восстановления и повторного использования NMMO. Биоресурсы. Technol. 161, 449–450.
PubMed Аннотация | Google Scholar
Кафле, Г. К., Бхаттарай, С., Ким, С., и Чен, Л. (2014). Влияние соотношения кормов и микробов на анаэробное переваривание отходов китайской капусты в мезофильных и термофильных условиях: биогазовый потенциал и кинетическое исследование. J. Environ. Управлять. 133, 293–301. DOI: 10.1016 / j.jenvman.2013.12.006
PubMed Аннотация | CrossRef Полный текст | Google Scholar
Капди, С. С., Виджай, В. К., Раджеш, С. К., и Прасад, Р. (2005). Очистка, сжатие и хранение биогаза: перспективы и перспективы в контексте Индии. Обновить. Энергия 30, 1195–1202. DOI: 10.1016 / j.renene.2004.09.012
CrossRef Полный текст | Google Scholar
Кайембе К., Басосила Л., Мпиана П. Т., Сикулисимва П. К. и Мбую К. (2013). Ингибирующее действие фенольных мономеров на метаногенез при анаэробном пищеварении. Br. Microbiol. Res. J. 31, 32–41. DOI: 10.9734 / BMRJ / 2013/2291
CrossRef Полный текст | Google Scholar
Ким, К. Х., и Хонг, Дж. (2001). Предварительная обработка лигноцеллюлозы сверхкритическим CO2 усиливает ферментативный гидролиз целлюлозы. Биоресурсы. Technol. 77, 139–144. DOI: 10.1016 / S0960-8524 (00) 00147-4
PubMed Аннотация | CrossRef Полный текст | Google Scholar
Лей, З., Чен, Дж., Чжан, З., и Сугиура, Н. (2010). Производство метана из рисовой соломы с акклиматизированным анаэробным илом: эффект добавления фосфатов. Биоресурсы. Technol. 101, 4343–4348. DOI: 10.1016 / j.biortech.2010.01.083
PubMed Аннотация | CrossRef Полный текст | Google Scholar
Лестер, М., Беллон-Морель, В., Гонсалес, К., Латриль, Э., Роджер, Дж. М., Джанква, Г. и др. (2010). Альтернативные методы определения анаэробной биоразлагаемости: обзор. Process Biochem. 45, 431–440. DOI: 10.1016 / j.procbio.2009.11.018
CrossRef Полный текст | Google Scholar
Ли Ю., Парк С. Ю. и Чжу Дж. (2011). Твердотельное анаэробное сбраживание для производства метана из органических отходов. Обновить. Поддерживать. Energy Rev. 15, 821–826. DOI: 10.1016 / j.rser.2010.07.042
CrossRef Полный текст | Google Scholar
Мартин, К., Клинке, Х. Б., Марсет, М., Гарсия, Л., Эрнандес, Э. и Томсен, А. Б. (2007). Изучение фенольных соединений, образующихся при предварительной обработке жома сахарного тростника мокрым окислением и паровым взрывом. Holzforschung 61, 483–487.
Google Scholar
Мартин, М. Р., Форнеро, Дж. Дж., Старт, Р., Мец, Л., и Ангенент, Л. Т. (2013). Биопроцесс с одной культурой Methanothermobacter thermautotrophicus для улучшения биогаза в варочном котле путем преобразования CO2 в Ch5 с помощью h3. Археи 2013, 157529. doi: 10.1155 / 2013/157529
PubMed Аннотация | CrossRef Полный текст
Мацакас, Л., и Христакопулос, П. (2013). Ферментация сжиженного жмыха сладкого сорго, подвергнутого предварительной гидротермической обработке, в этанол с высоким содержанием твердых веществ. Биоресурсы. Technol. 127, 202–208. DOI: 10.1016 / j.biortech.2012.09.107
PubMed Аннотация | CrossRef Полный текст | Google Scholar
Мацакас, Л., Рова, У., и Христакопулос, П.(2014). Оценка сушеных стеблей сладкого сорго как сырья для производства метана. Biomed Res. Int. 2014, 731731. DOI: 10.1155 / 2014/731731
PubMed Аннотация | CrossRef Полный текст | Google Scholar
Мендес, А. А., Перейра, Э. Б., и де Кастро, Х. Ф. (2006). Влияние предварительной обработки богатых липидами сточных вод ферментативным гидролизом на анаэробное биоразложение. Biochem. Англ. J. 32, 185–190. DOI: 10.1016 / j.bej.2006.09.021
CrossRef Полный текст | Google Scholar
Миллер, Г.Л. (1959). Использование реактива динитросалициловой кислоты для определения редуцирующего сахара. Анал. Chem. 31, 426–428. DOI: 10.1021 / ac60147a030
CrossRef Полный текст | Google Scholar
Мирахмади К., Кабир М. М., Джейханипур А., Карими К. и Тахерзаде М. Дж. (2010). Предварительная щелочная обработка ели и березы для улучшения производства биоэтанола и биогаза. Биоресурсы 5, 928–938.
Google Scholar
Мохсензаде, А., Джейханипур, А., Карими К. и Тахерзаде М. Дж. (2012). Предварительная щелочная обработка ели хвойных пород и березы лиственных пород с помощью NaOH / тиомочевины, NaOH / мочевины, NaOH / мочевины / тиомочевины и NaOH / PEG для улучшения производства этанола и биогаза. J. Chem. Technol. Biotechnol. 87, 1209–1214.
Google Scholar
Молино А., Мильори М., Динг Ю., Биксон Б., Джордано Г. и Браччо Г. (2013). Повышение качества биогаза с помощью мембранного процесса: моделирование масштаба пилотной установки и конечного использования для закачки в сеть. Топливо 107, 585–592. DOI: 10.1016 / j.fuel.2012.10.058
CrossRef Полный текст | Google Scholar
Морено А. Д., Ибарра Д., Фернандес Дж. Л. и Баллестерос М. (2012). Различные стратегии детоксикации лакказы для производства этанола из лигноцеллюлозной биомассы термотолерантными дрожжами Kluyveromyces marxianus CECT 10875. Bioresour. Technol. 106, 101–109. DOI: 10.1016 / j.biortech.2011.11.108
PubMed Аннотация | CrossRef Полный текст | Google Scholar
Морено, А.Д., Томас-Пейо, Э., Ибарра, Д., Баллестерос, М., и Олссон, Л. (2013). Обработка лакказы in situ улучшает ферментируемость взорванной паром пшеничной соломы в процессах SSCF при высокой плотности сухого вещества. Биоресурсы. Technol. 143, 337–343. DOI: 10.1016 / j.biortech.2013.06.011
PubMed Аннотация | CrossRef Полный текст | Google Scholar
Мшандете А., Бьёмссон Л., Киваиси А. К., Рубиндамаюги С. Т. и Маттиассон Б. (2005). Улучшение анаэробного периодического переваривания отходов сизалевой целлюлозы путем мезофильной аэробной предварительной обработки. Water Res. 39, 1569–1575. DOI: 10.1016 / j.watres.2004.11.037
PubMed Аннотация | CrossRef Полный текст | Google Scholar
Наик, С. Н., Гоуд, В. В., Рут, П. К., и Далай, А. К. (2010). Производство биотоплива первого и второго поколения: всесторонний обзор. Обновить. Поддерживать. Energy Rev. 14, 578–597.
Google Scholar
Накамура Ю. и Мтуи Г. (2003). Анаэробная ферментация древесной биомассы, обработанной различными методами. Biotechnol. Bioprocess Eng. 8, 179–182. DOI: 10.1007 / BF02935893
CrossRef Полный текст | Google Scholar
Негро, М. Дж., Мансанарес, П., Баллестерос, И., Оливия, Дж. М., Кабаньяс, А., и Баллестерос, М. (2003). Условия гидротермальной предварительной обработки для увеличения производства этанола из биомассы тополя. Appl. Biochem. Biotechnol. 105, 87–100. DOI: 10.1385 / ABAB: 105: 1-3: 87
PubMed Аннотация | CrossRef Полный текст | Google Scholar
Ницос, К.К., Матис, К. А., Триантафиллидис, К. С. (2013). Оптимизация гидротермальной обработки лигноцеллюлозной биомассы в процессе производства биоэтанола. ChemSusChem 6, 110–122. DOI: 10.1002 / cssc.201200546
PubMed Аннотация | CrossRef Полный текст | Google Scholar
Палонен, Х., Томсен, А. Б., Тенканен, М., Шмидт, А. С., и Виикари, Л. (2004). Оценка предварительной обработки влажным окислением для ферментативного гидролиза мягкой древесины. Appl. Biochem. Biotechnol. 117, 1–17. DOI: 10.1385 / ABAB: 117: 1: 01
PubMed Аннотация | CrossRef Полный текст | Google Scholar
Parawira, W. (2012). Исследования и применение ферментов в биотехнологической интенсификации производства биогаза. Crit. Rev. Biotechnol. 32, 172–186. DOI: 10.3109 / 07388551.2011.595384
PubMed Аннотация | CrossRef Полный текст | Google Scholar
Paschos, T., Xiros, C., and Christakopoulos, P. (2015). Одновременное осахаривание и ферментация совместными культурами Fusarium oxysporum и Saccharomyces cerevisaeen увеличивает производство этанола из разжиженной пшеничной соломы при высоком содержании сухих веществ. Ind. Crops Prod. 76, 793–802. DOI: 10.1016 / j.indcrop.2015.07.061
CrossRef Полный текст | Google Scholar
Ринтала, Дж., И Аринг, Б. (1994). Термофильное анаэробное сбраживание твердых бытовых отходов с разделением источников: влияние добавок ферментов. Appl. Microbiol. Biotechnol. 40, 916–919. DOI: 10.1007 / BF00173999
CrossRef Полный текст | Google Scholar
Романо Р. Т., Чжан Р., Тетер С. и МакГарви Дж. А. (2009). Влияние добавления ферментов на анаэробное переваривание травы пшеницы Jose Tall. Биоресурсы. Technol. 100, 4564–4571. DOI: 10.1016 / j.biortech.2008.12.065
PubMed Аннотация | CrossRef Полный текст | Google Scholar
Салехиан П., Карими К. (2013). Предварительная щелочная обработка для улучшения производства биогаза и этанола из различных отходов сосны. Ind. Eng. Chem. Res. 52, 972–978. DOI: 10.1021 / ie302805c
CrossRef Полный текст | Google Scholar
Салехиан П., Карими К., Зилуэй Х. и Джейханипур А.(2013). Улучшение производства биогаза из древесины сосны путем предварительной обработки щелочью. Топливо 106, 484–489. DOI: 10.1016 / j.fuel.2012.12.092
CrossRef Полный текст | Google Scholar
Сьерра-Альварес, Р., Леттинга, Г. (1991). Метаногенная токсичность лигнинов сточных вод и родственных лигнину соединений. J. Chem. Technol. Biotechnol. 50, 443–455. DOI: 10.1002 / jctb.280500403
CrossRef Полный текст | Google Scholar
Сонакья, В., Райзада, Н., и Кали, В. (2001). Микробиологическое и ферментативное улучшение анаэробного сбраживания биомассы отходов. Biotechnol. Lett. 23, 1463–1466. DOI: 10.3109 / 07388551.2011.595384
PubMed Аннотация | CrossRef Полный текст | Google Scholar
Судэм, В. П., Альрикссон, Б., и Йонссон, Л. Дж. (2011). Восстановители улучшают ферментативный гидролиз целлюлозных субстратов в присутствии жидкости для предварительной обработки. J. Biotechnol. 155, 244–250. DOI: 10.1016 / j.jbiotec.2011.06.026
PubMed Аннотация | CrossRef Полный текст | Google Scholar
Шведская газовая ассоциация (2011 г.). Биогаз в Швеции. Energigas Sverige . Стокгольм: Шведская газовая ассоциация.
Тахерзаде, М. Дж., И Карими, К. (2008). Предварительная обработка лигноцеллюлозных отходов для улучшения производства этанола и биогаза: обзор. Int. J. Mol. Sci. 9, 1621–1651. DOI: 10.3390 / ijms21
PubMed Аннотация | CrossRef Полный текст | Google Scholar
Тегаммар, А., Карими К., Хорват И. С. и Тахерзаде М. Дж. (2012). Повышенное производство биогаза из рисовой соломы, соломы тритикале и ели хвойных пород с помощью предварительной обработки NMMO. Биомасса Биоэнергетика 36, 116–120. DOI: 10.1016 / j.biombioe.2011.10.019
CrossRef Полный текст | Google Scholar
Вивекананд В., Олсен Э. Ф., Эйсинк В. Г. Х. и Хорн С. Дж. (2013). Влияние различных режимов парового взрыва на метановый потенциал и ферментативное осахаривание березы. Биоресурсы.Technol. 127, 343–349. DOI: 10.1016 / j.biortech.2012.09.118
PubMed Аннотация | CrossRef Полный текст | Google Scholar
Ся, Ю., Фанг, Х. Х. П., и Чжан, Т. (2013). Недавние исследования термофильной анаэробной биоконверсии лигноцеллюлозной биомассы. RSC Adv. 3, 15528–15542. DOI: 10.1039 / c3ra40866c
CrossRef Полный текст | Google Scholar
Ксирос, К., и Олссон, Л. (2014). Сравнение стратегий преодоления ингибирующих эффектов при ферментации лигноцеллюлозных гидролизатов в условиях высокой плотности. Биомасса Биоэнергетика 65, 79–90. DOI: 10.1016 / j.biombioe.2014.03.060
CrossRef Полный текст | Google Scholar
Йошида К., Мияфудзи Х. и Сака С. (2010). Производство метана из органических кислот, получаемых сверхкритической очисткой воды из японского бука. J. Wood Sci. 56, 160–165. DOI: 10.1007 / s10086-009-1074-9
CrossRef Полный текст | Google Scholar
Zheng, Y., Zhao, J., Xu, F., and Li, Y. (2014). Предварительная обработка лигноцеллюлозной биомассы для увеличения производства биогаза. Prog. Энергия сгорания. Sci. 42, 35–53. DOI: 10.1016 / j.pecs.2014.01.001
CrossRef Полный текст | Google Scholar
Центр обработки данных по альтернативным видам топлива: Производство возобновляемого природного газа
Этот грузовик для перевозки молока заправляется на станции возобновляемого природного газа. (Фото с сайта ampCNG)
Возобновляемый природный газ (RNG) — это газ трубопроводного качества, который полностью взаимозаменяем с обычным природным газом и, таким образом, может использоваться в транспортных средствах, работающих на природном газе.ГСЧ — это, по сути, биогаз (газообразный продукт разложения органических веществ), который был обработан в соответствии со стандартами чистоты. Как и обычный природный газ, RNG может использоваться в качестве транспортного топлива в виде сжатого природного газа (CNG) или сжиженного природного газа (LNG). ГСЧ квалифицируется как передовое биотопливо в соответствии со Стандартом по возобновляемым видам топлива.
Биометан, который является другим термином для этого очищенного топлива трубопроводного качества, относится к биогазу, который также был очищен и кондиционирован для удаления или уменьшения неметановых элементов.Этот переработанный биогаз вместо этого используется вместо традиционного природного газа для выработки электроэнергии и тепла для электростанций, а не в транспортных средствах.
Биогаз производится из различных источников биомассы с помощью биохимических процессов, таких как анаэробное сбраживание, или термохимических средств, таких как газификация. После небольшой очистки биогаз можно использовать для выработки электроэнергии и тепла. Для заправки транспортных средств биогаз должен быть переработан до более высокого стандарта чистоты. Этот процесс называется кондиционированием или повышением качества и включает удаление воды, диоксида углерода, сероводорода и других микроэлементов.Получаемый в результате ГСЧ или биометан имеет более высокое содержание метана, чем неочищенный биогаз, что делает его сопоставимым с обычным природным газом и, следовательно, подходящим источником энергии в приложениях, где требуется газ трубопроводного качества.
Полный список проектов по модернизации газа для закачки в трубопроводы или использования в качестве автомобильного топлива см. В Базе данных по возобновляемому природному газу, разработанной и поддерживаемой Аргоннской национальной лабораторией.
Биогаз со свалок
Свалки — это специально отведенные места для захоронения отходов жилых, промышленных и коммерческих предприятий.По данным Агентства по охране окружающей среды США (EPA), свалки являются третьим по величине источником выбросов метана в результате деятельности человека в США. Биогаз со свалок также называют свалочным газом (свалочный газ), поскольку процесс разложения происходит в земле, а не в анаэробном варочном котле. По данным EPA, по состоянию на июнь 2020 года в Соединенных Штатах насчитывалось около 564 действующих проектов свалочного газа. Однако в большинстве этих проектов биогаз используется для производства электроэнергии, а не для работы транспортных средств, работающих на природном газе.
Узнайте об этих проектах по транспортировке альтернативного биотоплива:
Биогаз от животноводческих хозяйств
Системы рекуперации биогаза при животноводстве могут использоваться для производства возобновляемого природного газа. Навоз собирается и доставляется в анаэробный варочный котел для стабилизации и оптимизации производства метана. Полученный биогаз можно переработать в ГСЧ и использовать для топлива транспортных средств, работающих на природном газе.
По состоянию на август 2017 года на коммерческих животноводческих фермах в США работало около 250 систем анаэробных метантенков.Большинство этих объектов используют биогаз для производства электроэнергии. Некоторые фермы используют биогаз для производства топлива для транспорта, в том числе Hilarides Dairy в Калифорнии и Fair Oaks Dairy в Индиане. База данных AgSTAR Агентства по охране окружающей среды предоставляет дополнительную информацию об использовании таких систем в Соединенных Штатах.
Биогаз от очистки сточных вод
Биогаз может производиться при сбраживании твердых частиц, удаляемых в процессе очистки сточных вод. По оценкам Агентства по охране окружающей среды, этот потенциал биогаза составляет около 1 кубического фута газа метантенка на 100 галлонов сточных вод.Согласно исследованию, выпущенному Национальной ассоциацией агентств чистой воды и Федерацией водной среды, энергия, вырабатываемая на станциях очистки сточных вод (СОСВ) в США, потенциально может удовлетворить 12% национального спроса на электроэнергию. Это также может стимулировать производство ГСЧ для использования в транспортных средствах.
В Соединенных Штатах насчитывается более 16 000 очистных сооружений, и около 1300 используют анаэробное сбраживание для производства биогаза, который используется на месте. Станция очистки сточных вод Джейнсвилля в Висконсине является примером завода, который использует биогаз для производства ГСЧ для использования в транспортных средствах.
Другие источники биогаза
Другие источники биогаза включают органические отходы промышленных, институциональных и коммерческих предприятий, таких как производство продуктов питания и оптовые торговцы, супермаркеты, рестораны, больницы и образовательные учреждения. Узнайте о Sacramento BioDigester, крупнейшей в своем роде анаэробной системе пищеварения в Северной Америке.
Биогаз также можно производить из лигноцеллюлозного материала (такого как пожнивные остатки, древесная биомасса и специальные энергетические культуры) посредством термохимических преобразований, совместного переваривания и сухой ферментации.Эти технологии реализуются в Европе и имеют ограниченное применение в США.
Производство биогаза путем совместного сбраживания козьего навоза с тремя остатками сельскохозяйственных культур
Abstract
Козий навоз (ГМ) — отличное сырье для анаэробного сбраживания благодаря высокому общему содержанию азота и стабильности ферментации. Было проведено несколько сравнительных анализов анаэробного совместного переваривания ГМ с тремя растительными остатками (CR), а именно пшеничной соломой (WS), кукурузными стеблями (CS) и рисовой соломой (RS), при различных соотношениях смешивания.Все варочные котлы работали одновременно при мезофильной температуре 35 ± 1 ° C с общей концентрацией твердого вещества 8%. Результат показал, что комбинация GM с CS или RS значительно улучшила производство биогаза при всех отношениях углерода к азоту (C / N). GM / CS (30:70), GM / CS (70:30), GM / RS (30:70) и GM / RS (50:50) производили самые высокие выходы биогаза из различных субстратов (14840, 16023, 15608 и 15698 мл соответственно) после 55 дней ферментации. Выходы биогаза GM / WS 30:70 (C / N 35.61), GM / CS 70:30 (C / N 21.19) и GM / RS 50:50 (C / N 26.23) были в 1,62, 2,11 и 1,83 раза выше, чем у CR, соответственно. Эти значения были определены как оптимальные отношения C / N для совместного переваривания. Однако по сравнению с обработками GM / CS и GM / RS, количество биогаза, полученного из GM / WS, было лишь немного выше, чем при однократном переваривании GM или WS. Этот результат был вызван высоким общим содержанием углерода (35,83%) и содержанием лигнина (24,34%) в WS, что препятствовало биоразложению.
Образец цитирования: Zhang T, Liu L, Song Z, Ren G, Feng Y, Han X и др.(2013) Производство биогаза путем совместного сбраживания козьего навоза с тремя остатками сельскохозяйственных культур. PLoS ONE 8 (6): e66845. https://doi.org/10.1371/journal.pone.0066845
Редактор: Чэнью Ду, Ноттингемский университет, Великобритания
Поступила: 28 января 2013 г .; Дата принятия: 12 мая 2013 г .; Опубликован: 25 июня 2013 г.
Авторские права: © 2013 Zhang et al. Это статья в открытом доступе, распространяемая в соответствии с условиями лицензии Creative Commons Attribution License, которая разрешает неограниченное использование, распространение и воспроизведение на любом носителе при условии наличия оригинального автора и источника
Финансирование: Эта работа была поддержана наукой и проекты технической поддержки «Интеграция биологических технологий и демонстрация процесса переваривания биогаза с высоким выходом из смеси ингредиентов» (2011BAD15B03) от Министерства науки и технологий Департамента Китайской Народной Республики и Фонды фундаментальных исследований для центральных университетов (QM2012002) от Министерство образования Китайской Народной Республики.Финансирующие организации не играли никакой роли в дизайне исследования, сборе и анализе данных, принятии решения о публикации или подготовке рукописи.
Конкурирующие интересы: Авторы заявили об отсутствии конкурирующих интересов.
Введение
Китай — одна из крупнейших сельскохозяйственных стран мира. Производство чистых доступных пожнивных остатков (CR) в Китае оценивается более чем в 800 миллионов т / год [1], что является первым в мире. Использование сельскохозяйственных отходов в качестве основного компонента возобновляемой энергии подходит для повышения энергетической безопасности и уменьшения ущерба окружающей среде, вызываемого выбросами углерода [2], [3].Пшеничная солома (WS), рисовая солома (RS) и стебли кукурузы (CS) являются тремя основными сельскохозяйственными отходами в Китае и составляют 80,5% от общего объема производства (15,7%, 24,2% и 40,6% соответственно) [1]. Таким образом, важно изучить потенциал производства энергии этими тремя отходами.
Анаэробное сбраживание (AD) — это биологический процесс, который производит биогаз из биоразлагаемых отходов бактериями в условиях плохого содержания кислорода или его отсутствия. В последние два десятилетия AD применялась как эффективная технология для решения проблем нехватки энергии и загрязнения окружающей среды в биотехнологических отраслях и жилых домах, вызванных отоплением и производством электроэнергии [4], [5], [6].
CR и навоз недавно были использованы вместе для производства биогаза AD. По сравнению с однократным сбраживанием сырья совместное сбраживание CR и навоза увеличивает скорость производства биогаза из-за большего баланса между углеродом и азотом [7] и повышает эффективность AD [8]. Годовой урожай козьего навоза (ГМ) в Китае составляет примерно 3,21 × 10 8 т, за ним следуют молочный навоз, свиной навоз и куриный навоз [9]. Содержание общего азота (TN) в свежем GM (1.01%) и куриного помета (1,03%) значительно выше, чем у молочного навоза (0,35%) и свиного навоза (0,24%) [10]. Высокое содержание TN полезно для совместного переваривания с CR, потому что оно снижает отношение углерода к азоту (C / N) отдельных субстратов CR. GM также нечувствителен к подкислению во время анаэробной ферментации [11], [12]. Следовательно, GM — отличное сырье для AD. Хотя различные виды сырья, такие как сельскохозяйственные отходы, навоз животных, ил сточных вод и пищевые отходы, были зарегистрированы как потенциально пригодные для совместного сбраживания [7], [13], [14], [15], [16], [17] ], [18], [19], [20] подходящие соотношения смешивания многокомпонентных субстратов между GM и различными CR в значительной степени неизвестны.
Мы исследовали эффективность производства биогаза при анаэробном совместном сбраживании под влиянием различных соотношений смешивания GM и CR. Наилучшее соотношение между этими субстратами было получено при сравнении результатов. Кроме того, были предложены оптимальные условия совместного сбраживания для производства биогаза.
Материалы и методы
Сырье и посевной материал
GM был получен на местной животноводческой ферме недалеко от Северо-Западного университета сельского хозяйства и лесоводства (NWAFU), Янлин Шэньси, Китай.WS, CS и RS были собраны с экспериментального поля СЗФУ. Все эти соломинки были разрезаны на секции длиной от 2 см до 3 см с помощью измельчителя. Инокулят представлял собой анаэробный осадок молочного навоза, который был получен из анаэробного варочного котла в местной деревне.
Экспериментальный реактор и конструкция
Эксперимент проводился согласно Song et al. (2012) с использованием лабораторных анаэробных варочных котлов, изготовленных из колб Эрленмейера объемом 1 л. Реакторы периодического действия использовали для определения совместного вываривания ГМ, смешанного с тремя CR.Рабочий объем каждого варочного котла составлял 700 мл, включая 140 г инокулята и соответствующее количество перевариваемого материала. В варочные котлы добавляли деионизированную воду для поддержания общего содержания твердых веществ (TS) на уровне 8% [5]. Все реакторы осторожно перемешивали вручную в течение приблизительно 1 мин / день перед измерением объема биогаза.
Для получения наилучшего соотношения смешивания при совместном сбраживании ГМ, дополненного тремя CR в качестве внешних источников углерода, были протестированы пять различных соотношений масс при смешивании при 90∶10, 70∶30, 50∶50, 30∶70 и 10∶90. в мезофильных условиях (35 ± 1 ° C) в течение 55 дней.Несмешанные GM (100 ± 0) и CR (0 ± 100) переваривали анаэробно в качестве контролей. Каждую обработку проводили трижды с контролем, чтобы исследовать влияние различных соотношений смеси на производство биогаза.
Анализ и статистика
TS, летучие твердые вещества (VS), pH, содержание летучих жирных кислот (VFA) и TN в материалах были определены в соответствии со Стандартными методами исследования воды и сточных вод Американской ассоциации общественного здравоохранения [21 ].Содержание общего углерода (ОС) и лигнина анализировали с использованием метода, описанного Cuetos et al. и Song et al. [5], [22]. Количество биогаза, произведенного из каждого варочного котла, регистрировали каждый день с использованием метода вытеснения воды в течение периода варки. Каждую серию экспериментов считали завершенной, когда в течение 10 дней наблюдалась четкая тенденция к снижению суточного объема производимого биогаза.
ANOVA был выполнен для определения значимых различий между каждым лечением с использованием SAS версии 8.12 (SAS Institute Inc., Кэри, Северная Каролина, США).
Результаты и обсуждение
Характеристики основания
Соотношение C / N различных субстратов и смесей субстратов в AD сильно влияет на производство биогаза [23], [24]. Более высокое содержание углерода обеспечивает больше углерода для производства CH 4 , тогда как более низкое содержание азота ограничивает микробную активность, поскольку микробам требуется значительное количество азота для поддержания роста [8]. Идеальное соотношение C / N составляет от 9 до 30 для анаэробных варочных котлов [25].Химические характеристики субстратов, использованных в этом исследовании, показаны в таблице 1. Отношение C / N GM составляло 17,97, что слишком мало для производства биогаза. Однако отношения C / N WS, CS и RS были значительно выше (91,17, 88,13 и 92,91, соответственно), чем у GM ( P <0,01). Этот результат свидетельствует о том, что CR увеличивают производство метана при совместном переваривании с GM при оптимальном соотношении C / N.
Выходы и производительность биогаза при различных соотношениях GM / CR
Суточное производство биогаза при совместном переваривании ГМ и CR в течение 55 дней переваривания было рассчитано при различных соотношениях смешивания (рис.1). Образцы из соотношений смешивания GM / WS 30:70, GM / CS 30:70 и GM / RS 50:50 были измерены, и их пиковые значения выхода составили 570, 585 и 525 мл / день 17, 19 и 11 числа. d соответственно (рис.1). Переваривание одного субстрата GM (100: 0) давало биогаз раньше, чем другие комбинации, но имело два относительно небольших пика (402 и 500 мл / день) (рис. 1). Напротив, переваривание любого отдельного субстрата CR (0: 100) имело только один пик (GM / WS 547, GM / CS 540 и GM / RS 477 мл / день), который произошел раньше, чем другие комбинации (с 3-го по 6-й. г) и быстро уменьшалась после 16-го дня (рис.1). Эти результаты показывают, что совместное переваривание ГМ и CR может значительно замедлить достижение максимальной добычи газа.
Рис. 1. Ежедневное производство биогаза при совместном сбраживании GM и WS (A), CS (B) и RS (C) при различных соотношениях смешивания.
Средние значения получены в трех независимых повторностях. Вертикальные полосы представляют собой стандартные отклонения.
https://doi.org/10.1371/journal.pone.0066845.g001
Окончательные совокупные производства биогаза при совместном сбраживании ГМ и CR при различных соотношениях смешивания показаны на рис.2. Совокупное производство биогаза для GM / WS 10:90, 30:70, 50:50, 70:30 и 90:10 составило 11890, 12765, 11253, 12685 и 9650 мл соответственно (рис. 2A). Эти результаты показали увеличение на 51,0%, 62,1%, 42,9%, 61,1% и 22,6% по сравнению с одиночным WS (7874 мл) и увеличение на 51,0%, 62,1%, 42,9% и 22,6% по сравнению с одиночным GM ( 10375 мл). Однако производство биогаза GM / WS 90:10 (9650 мл) было ниже, чем у одного GM (рис. 2A). Такие же тенденции наблюдались для обработок GM / CS и GM / RS, которые имели значительно более высокий рост (рис.2Б и 2С). Эти данные показали, что совместное переваривание ГМ и CR значительно улучшает биоразлагаемость и производство биогаза при большинстве соотношений смешивания по сравнению с перевариванием одного субстрата. Наши результаты подтвердили результаты Wu et al. [26], которые обнаружили, что совместное переваривание свиного навоза с CS, овсяной соломой и WS значительно увеличивает производство биогаза и чистый объем CH 4 при всех соотношениях C / N.
Рисунок 2. Совокупное производство биогаза при совместном сбраживании GM и WS (A), CS (B) и RS (C) при различных соотношениях смешивания.
Средние значения получены в трех независимых повторностях. Вертикальные полосы представляют собой стандартные отклонения.
https://doi.org/10.1371/journal.pone.0066845.g002
Для сравнения эффекта переваривания одного субстрата и совместного переваривания с ГМ и CR общий выход биогаза для каждой комбинации показан на рис. 3. Общее производство биогаза в большинстве систем совместного сбраживания было выше, чем при однократном сбраживании ГМ или CR, за исключением GM / WS 90:10 и GM / RS 10:90.GM / CS 70:30 показал самый высокий общий выход биогаза 16,02 л во всех вариантах обработки, что на 83,02% и 54,44% выше, чем у CS и GM, соответственно. Среди всех обработок GM / RS общее производство биогаза GM / RS 50:50 (15,70 л) было на 111,28% и 51,31% выше, чем у одного CS и одного GM, соответственно. Совместное переваривание GM / WS 30:70 было на 62,12% и 23,04% выше, чем у WS и GM, соответственно. По сравнению с содержанием TC в CS (28,82%) и RS (31,96%) более высокое содержание TC в WS (35.83%) подавляли рост микробов и метаногенез из-за дефицита аммонийного азота и низкого pH [22], [27], [28].
Рисунок 3. Общее производство биогаза от анаэробного совместного сбраживания GM с WS, CS и RS при различных соотношениях смешивания.
Средние значения получены в трех независимых повторностях. Вертикальные полосы представляют собой стандартные отклонения. Тест ANOVA был проведен для определения различий между каждым сортом. Значения с одинаковыми буквами указывают на отсутствие существенной разницы при P <0.01.
https://doi.org/10.1371/journal.pone.0066845.g003
Эти результаты показали, что совместное сбраживание с подходящими смесями ГМ и CR является эффективным способом продления периода наибольшего газообразования и повышения выхода биогаза. ANOVA показал, что общее производство биогаза при совместном переваривании было значительно выше ( P <0,01), чем при однократном переваривании GM или CR (рис. 3).
Влияние соотношения C / N на производство биогаза
Отношение C / N представляет собой соотношение между количеством углерода и азота, присутствующих в органических материалах, и является важным показателем для контроля систем биологической очистки [23].С одной стороны, высокое отношение C / N указывает на быстрое потребление азота метаногенами и приводит к снижению производства газа. С другой стороны, низкое соотношение C / N приводит к накоплению аммиака и увеличению значений pH, что токсично для метаногенных бактерий [29]. Среднее значение отношений C / N для каждой комбинации совместного переваривания и однократного переваривания варьировалось от 92,79 до 17,97 (таблица 2). Отношения C / N при совместном переваривании были значительно ниже, чем для материалов CR ( P <0,01, таблица 1), что указывает на то, что совместное переваривание эффективно снижает отношения C / N AD.Экспериментальные данные показали, что выходы биогаза при большинстве совместных перевариваний были выше, чем при соответствующих однократных перевариваниях. Согласно совокупному производству биогаза (рис. 3), самый высокий выход биогаза (12765, 15698 и 16023 мл) при GM / WS 30:70 (C / N 35,64), GM / CS 70:30 (C / N 21,26). и GM / RS 50:50 (C / N 26,28) были в 1,62, 2,11 и 1,83 раза выше, чем у CR, соответственно. Однако общий выход биогаза при трех обработках GM / CR 10:90 не увеличился и был даже ниже, чем при использовании одного субстрата.Причина этого результата заключалась в том, что отношения C / N для каждой обработки GM / CR 10:90 были менее 20 (таблица 2). Результаты показали, что идеальный диапазон отношения C / N составляет от 20 до 35 при совместном переваривании ГМ с CR, что согласуется с отчетом Verma [29], который показал, что оптимальные отношения C / N в анаэробных варочных котлах были от 20 до 30.
CR обычно содержат высокое содержание лигноцеллюлозы. Такие проблемы, как низкий выход газа во время AD этих материалов, обычно были связаны с высоким отношением C / N или высоким содержанием лигнина [30].Хотя соотношение C / N снижалось при большинстве совместных перевариваний, не наблюдалось явной тенденции к увеличению производства биогаза GM / WS, которое даже немного снизилось (GM / WS 90:10) по сравнению с только GM. Этот феномен, возможно, является результатом значительно более высокого содержания лигнина (24,34%) в субстрате WS, чем в CS и RS (15,38% и 9,47%, соответственно) ( P <0,01, таблица 1). Чтобы преодолеть низкую разлагаемость лигнина, уменьшение размера частиц субстрата CR может увеличить скорость разложения лигноцеллюлоз и дополнительно улучшить производство биогаза [31].
Влияние pH и VFA
VFA и pH являются двумя ключевыми факторами AD [4]. Величина pH и общее количество летучих жирных кислот отражали изменяющиеся процессы в реакторах (рис. 4). Кривые индивидуального pH и общего количества летучих жирных кислот для всех смесей и отдельных субстратов имели сходные тенденции. На рост метаногенов может существенно влиять уровень pH [32]. Начальные значения pH в варочных котлах постепенно снижались с 6,5 до 6,0 с увеличением процента CR, и GM / RS 10:90 имел самое низкое значение pH (5.5). Значения pH увеличивались с 6,5 по мере увеличения процента GM на 6-й день, а затем оставались на уровне приблизительно 6,8 до 30-го дня. Эта стабильность подтвердила, что суточное производство биогаза каждой смесью достигло стадии метаногенеза, и что значение pH оставалось на уровне примерно 6,8. После этого значения pH немного снизились до 6,0, что указывает на то, что расщепление изменилось на более поздних стадиях. Однако значения pH GM / CR 0: 100 быстро снижались после 18-го дня, показывая, таким образом, буферную способность GM.Эти результаты показали, что наилучшие значения pH для совместного переваривания GM и CR находятся в диапазоне от 6,5 до 7,5.
Рис. 4. Концентрации VFA и значения pH при совместном переваривании GM и WS (A), CS (B) и RS (C) при различных соотношениях смешивания.
Средние значения получены в трех независимых повторностях. Столбцы представляют ЛЖК, линии представляют значения pH, а вертикальные полосы представляют собой стандартные отклонения. ЛЖК, летучие жирные кислоты.
https://doi.org/10.1371/journal.pone.0066845.g004
ЛЖК являются промежуточными продуктами органических кислот, и общая концентрация ЛЖК считается важным показателем метаболического статуса в дополнение к значению pH во время БА [33], [34]. Однако кривые ЛЖК показали явно противоположные тенденции по сравнению со значениями pH. Первоначально VFA составляла приблизительно от 7380 мг / л до 11767 мг / л для всех обработок, а затем снизилась до 4519 мг / л до 5484 мг / л на 24 день. ЛЖК снова увеличились и, наконец, снизились до 9812 мг / л до 11791 мг / л в конце переваривания (рис.3 и 4).
Аммиак, образующийся в результате биологического разложения белков и мочевины, часто приводит к накоплению ЛЖК. Накопление VFA приводит к снижению значения pH, что влияет на рост метаногенов во время процесса AD [6], [24], [30]. Наши результаты показали, что pH и VFA были связаны с выходом биогаза в AD. Таким образом, значения рН были пропорциональны выходу биогаза, тогда как ЛЖК были обратно пропорциональны. Эти результаты также показали, что pH снижается с увеличением накопления VFA.Высокие концентрации ЛЖК токсичны для метаногенов и снижают скорость гидролиза в реакторах [35]. Взаимодействие между pH и ЛЖК может привести к «ингибированному устойчивому состоянию» с более низким выходом метана [30], [36], [37]. Увеличенные пики газообразования при каждой обработке смешения можно объяснить совместным перевариванием ГМ и CR, которое эффективно снимает подавленное устойчивое состояние, вызванное pH и ЛЖК. Совместное переваривание ГМ и CR улучшает буферную способность к накоплению ЛЖК и ингибирует процесс ацидогенеза, что согласуется с предыдущим исследованием [38].
Заключение
Совместное анаэробное переваривание ГМ с CR является многообещающим способом улучшения производства биогаза. Такое совместное сбраживание не только решает проблемы окружающей среды, вызванные горением соломинок, но также устраняет дисбаланс отношения C / N в отдельных субстратах для разложения и усиливает процесс AD.
Наши результаты показали, что анаэробное совместное переваривание GM с CS и RS было эффективным и производило больше кумулятивного биогаза за счет снижения отношения C / N субстратов.Лучшие соотношения были GM / CS 30:70, GM / CS 70:30, GM / RS 30:70 и GM / RS 50:50. Однако совместное переваривание ГМ с WS не привело к значительному увеличению выхода биогаза, что согласуется с результатами предыдущих исследований [26]. Более высокое содержание ОС в WS подавляло рост микробов и метаногенез из-за дефицита аммонийного азота и низкого pH. Для диапазонов pH и ЛЖК в этом исследовании значение рН снижалось с увеличением накопления ЛЖК, что приводило к ингибированию скорости гидролиза биоотходов.
Благодарности
Мы благодарим доктора Xiaodong Wang, Dr Furong Liu и Dr. Yuheng Yang за критическое прочтение этой рукописи и редакционные рекомендации.
Вклад авторов
Задумал и спроектировал эксперименты: TZ YZF GHY. Проведены эксперименты: ТЗ ЛЛЛ ЗЛС. Проанализированы данные: TZ GXR XHH. Написал статью: TZ GHY.
Список литературы
- 1. Цзян Д., Чжуан Д., Фу Дж., Хуанг Ю., Вэнь К. (2012) Биоэнергетический потенциал пожнивных остатков в Китае: наличие и распространение.Renew Sustain Energy Ред. 16: 1377–1382.
- 2. Поле CB, Кэмпбелл Дж. Э., Лобелл Д. Б. (2008) Энергия биомассы: масштаб потенциального ресурса. Тренд Ecol Evolut 23: 65–72.
- 3. Ян З., Чжан Х. (2008) Стратегии развития чистой энергии в Китае. Petrol Sci 5: 183–188.
- 4. Мадсен М., Холм-Нильсен Дж. Б., Эсбенсен К. Х. (2011) Мониторинг анаэробных процессов пищеварения: обзорная перспектива. Renew Sustain Energy Rev 15: 3141–3155.
- 5. Song Z, Yang G, Guo Y, Zhang T (2012) Сравнение двух химических предварительных обработок рисовой соломы для производства биогаза путем анаэробного сбраживания. Биоресурсы 7: 3223–3236.
- 6. Вейланд П. (2010) Производство биогаза: текущее состояние и перспективы. Appl Microbiol Biotechnol 85: 849–860.
- 7. Эль-Машад Х.М., Чжан Р. (2010) Производство биогаза путем совместного сбраживания молочного навоза и пищевых отходов. Биоресурсы Technol 101: 4021–4028.
- 8.Чжу Д. (2010) Совместное сбраживание различных отходов для увеличения производства метана: Университет штата Огайо.
- 9. Чжан П, Ян И, Тиан И, Ян Х, Чжан И и др. (2009) Развитие биоэнергетической промышленности в Китае: дилемма и решение. Renew Sustain Energy Rev 13: 2571–2579.
- 10. Ван Ф.Х., Ма WQ, Доу ZX, Ма Л., Лю XL и др. (2006) Оценка объемов производства навоза и его воздействия на окружающую среду в Китае. China Environ Sci 26: 614–617.
- 11. Джайн М., Сингх Р., Тауро П. (1981) Анаэробное переваривание отходов крупного рогатого скота и овец. Сельскохозяйственные отходы 3: 65–73.
- 12. Канвар С., Калиа А. (1993) Анаэробная ферментация овечьего помета для производства биогаза. Всемирный журнал J Microbiol Biotechnol 9: 174–175.
- 13. Дай X, Дуан Н., Донг Б., Дай Л. (2012) Совместное анаэробное сбраживание осадка сточных вод и пищевых отходов с высоким содержанием твердых частиц по сравнению с моно-сбраживанием: стабильность и производительность. Управление отходами.
- 14. Creamer K, Chen Y, Williams C, Cheng J (2010) Стабильное термофильное анаэробное сбраживание ила растворенной воздушной флотации (DAF) путем совместного сбраживания со свиным навозом. Биоресур Технол 101: 3020–3024.
- 15. Луостаринен С., Лусте С., Силланпяя М. (2009) Увеличение производства биогаза на очистных сооружениях за счет совместного сбраживания осадка сточных вод с осадком жироуловителя мясоперерабатывающего завода. Биоресур Технол 100: 79–85.
- 16. Bouallagui H, Lahdheb H, Ben Romdan E, Rachdi B, Hamdi M (2009) Повышение эффективности и стабильности анаэробного сбраживания фруктовых и овощных отходов с добавлением дополнительных субстратов.J Environ Manage 90: 1844–1849.
- 17. Альварес Дж., Отеро Л., Лема Дж. (2010) Методология оптимизации состава кормов для анаэробного совместного сбраживания агропромышленных отходов. Bioresour Technol 101: 1153–1158.
- 18. Масиас-Коррал М., Самани З., Хансон А., Смит Дж., Функ П. и др. (2008) Анаэробное сбраживание твердых бытовых и сельскохозяйственных отходов и влияние совместного сбраживания с навозом молочных коров. Bioresour Technol 99: 8288–8293.
- 19.Xie S, Lawlor P, Frost J, Hu Z, Zhan X (2011) Влияние соотношения свиного навоза и травяного силоса на производство метана при периодическом анаэробном совместном сбраживании концентрированного свиного навоза и травяного силоса. Bioresour Technol 102: 5728–5733.
- 20. Nguyen VCN, Fricke K (2012) Рекуперация энергии в результате анаэробного совместного переваривания свиного навоза и использованного грибного компоста в дельте Меконга. J Vietnamese Environ 3: 4–9.
- 21. APHA (1995) Стандартные методы исследования воды и сточных вод: Вашингтон.Округ Колумбия, Американская ассоциация общественного здравоохранения.
- 22. Куетос М.Дж., Фернандес С., Гомес Х, Моран А. (2011) Анаэробное совместное сбраживание свиного навоза с остатками энергетических культур. Biotechnol Bioprocess Eng 16: 1044–1052.
- 23. Ван Х, Ян Г, Фэн И, Рен Г, Хан Х (2012) Оптимизация состава корма и соотношения углерода и азота для повышения выхода метана во время анаэробного совместного переваривания молочных продуктов, куриного помета и пшеничной соломы. Bioresour Technol 120: 78–83.
- 24.Кайханян М. (1999) Ингибирование аммиака в биогазификации с высоким содержанием твердых веществ: обзор и практические решения. Environ Technol 20: 355–365.
- 25. Сиддики З., Хоран Н., Анаман К. (2011) Оптимизация соотношения C: N для совместных переработанных промышленных пищевых отходов и осадка сточных вод с использованием теста BMP. Int J Chem React Eng 9 ..
- 26. Wu X, Yao W, Zhu J, Miller C (2010) Biogas and CH 4 продуктивность за счет совместного переваривания свиного навоза с тремя пожнивными остатками в качестве внешнего источника углерода.Bioresour Technol 101: 4042–4047.
- 27. Паничнумсин П., Нофаратана А., Аринг Б., Чайпрасерт П. (2010) Производство метана путем совместного переваривания мякоти маниоки с различными концентрациями свиного навоза. Биомасса Биоэнерг 34: 1117–1124.
- 28. Каруччи Г., Карраско Ф., Трифони К., Майоне М., Беккари М. (2005) Анаэробное сбраживание отходов пищевой промышленности: влияние совместного переваривания на выход метана. J Environ Eng 131: 1037–1045.
- 29. Verma S (2002) Анаэробное сбраживание биоразлагаемых органических веществ в твердых бытовых отходах: Колумбийский университет.
- 30. Chen Y, Cheng JJ, Creamer KS (2008) Ингибирование процесса анаэробного пищеварения: обзор. Bioresour Technol 99: 4044–4064.
- 31. Palmowskl L, Müller J (2000) Влияние уменьшения размера органических отходов на их анаэробное переваривание. Water Sci Technol: 155–162.
- 32. Дуарте А., Андерсон Г. (1982) Моделирование ингибирования при анаэробном пищеварении. Water Sci Technol 14: 749–763.
- 33. Фернандес А., Санчес А., Font X (2005) Анаэробное совместное сбраживание смоделированной органической фракции твердых бытовых отходов и жиров животного и растительного происхождения.Biochem Eng J 26: 22–28.
- 34. Хабиба Л., Хассиб Б., Моктар Х (2009) Улучшение стабилизации и фильтруемости активного ила во время анаэробного сбраживания путем добавления фруктовых и овощных отходов. Биоресур Технол 100: 1555–1560.
- 35. Викен А., Хамелерс Б. (1999) Влияние температуры на скорость гидролиза выбранных компонентов биоотходов. Bioresour Technol 69: 249–254.
- 36. Ангелидаки И., Аринг Б. (1992) Влияние свободных длинноцепочечных жирных кислот на термофильное анаэробное пищеварение.Appl Microbiol Biotechnol 37: 808–812.
- 37. Ангелидаки И., Аринг Б. (1993) Термофильное анаэробное сбраживание отходов животноводства: влияние аммиака. Appl Microbiol Biotechnol 38: 560–564.
- 38. Ангелидаки I (1997) Анаэробное пищеварение в Дании. Прошлое, настоящее и будущее. Servicio de Publicaciones. С. 335–342.