Ульяновский завод Vestas, созданный при участии «РОСНАНО» в 2018 году, углубляет локализацию производства лопастей
На территории Ульяновской области стартует производство пултрузионного профиля для ветроэнергетических установок (ВЭУ) Vestas. В рамках исполнения обязательств по специальному инвестиционному контракту (СПИК) компания Vestas обеспечила необходимые условия для размещения производства пултрузионного профиля в России для своего одобренного международного поставщика DowAksa.
DowAksa — ведущий игрок в производстве углеволокна и углепластиковых композитных решений, используемых для промышленного применения. Право на производство композитного профиля в РФ и сертификат резидента особой экономической зоны «Ульяновск» получила дочерняя компания DowAksa — ООО «ДауАкса Рус». Реализация данного проекта стала возможной благодаря совместному запуску завода «Вестас Мэньюфэкчуринг РУС» (ВМР) в Ульяновске по производству лопастей компаниями Vestas и «РОСНАНО». На первом этапе проекта DowAksa планирует обеспечить реализацию производства опытно-промышленной партии профиля, а после сертификации производства поставлять готовую продукцию на ВМР в рамках первой российской программы поддержки ВИЭ 2013–2024 гг. (ДПМ ВИЭ 1.0) и исполнения обязательств ВМР в рамках СПИК.
В рамках индустриальной стратегической кооперации между «РОСНАНО» и Vestas в контексте новой программы поддержки ВИЭ 2025–2035 гг. (ДПМ ВИЭ 2.0), которая может создать дополнительный спрос на локализованный пултрузионный профиль, планируется реализация второй стадии проекта для удовлетворения такого спроса. Для этих целей DowAksa и «РОСНАНО» рассмотрят условия сотрудничества для обеспечения необходимой поддержки со стороны «РОСНАНО», в том числе для расширения (масштабирования) производства на согласованных условиях (в том числе путем осуществления дополнительных инвестиций в проект). Вторая стадия реализации проекта может быть запущена уже во 2-м полугодии 2022 года.
Напомним, что предприятие «Вестас Мэньюфэкчуринг РУС», запущенное в декабре 2018 года компанией Vestas и Группой «РОСНАНО», производит композитные лопасти для турбин ВЭУ, не имеющие аналогов в России. Производственная площадка расположена на территории авиационного кластера в Ульяновске. Лопасти предназначены для ветроустановок мощностью от 3,6 до 4,2 МВт.
В июне 2021 года Группа «РОСНАНО» вышла из проекта согласно изначальным договоренностям с Vestas.
«Компания Vestas, будучи пионером и лидером ветроэнергетической отрасли, стремится к созданию добавленной стоимости во всех регионах своего присутствия. Так ранее благодаря совместным усилиям с „РОСНАНО» нам удалось создать уникальное производство лопастей в Ульяновске. А сегодня мы находимся в следующей точке локализационной эволюции, и уже наши партнеры по цепочке поставок поддерживают Vestas и создают свои производства в России для нужд компании. Мы также приветствуем возможную кооперацию „РОСНАНО» и DowAksa в будущем и надеемся на высокий рост спроса на ветряные турбины на российском рынке, благодаря которому такое сотрудничество может состояться», — отметил директор «Вестас Рус», член Совета Директоров «Вестас Мэньюфэкчуринг РУС» Кимал Юсупов.
«Компании „РОСНАНО» и Vestas последовательно подходят к процессу локализации. Обеспечивается трансфер передовых технологий и выпуск высокотехнологичной продукции на территории России, который, несомненно, имеет огромный экспортный потенциал», — прокомментировал Управляющий директор по инвестиционной деятельности УК «РОСНАНО» Махмуд Буриханов.
Испытания лопастей ветровой турбины | SGS Россия
Отказ лопастей ротора может существенно повлиять на длительность простоя турбины, эксплуатационную надежность и безопасность окружающих. Высокая надежность является важным фактором для обеспечения экономически выгодной эксплуатации ветровой турбины. Наши услуги по испытанию лопастей ветровой турбины помогут вам проверить надежность лопастей ротора и увеличить срок их службы.
Почему для испытания лопастей ветровой турбины следует выбирать услуги SGS?
Мы поможем вашей организации:
- увеличить срок службы лопастей ветровой турбины и минимизировать риск ошибки на стадии проектирования и производства;
- обеспечить соответствие лопастей ротора специфическим для объекта эксплуатации условиям и дальнейшую безопасную и эффективную работу в течение всего срока службы;
- достичь соответствия стандартам безопасности и нормативным актам;
- предотвратить возникновение поломок и их влияние на продолжительность простоя турбины и эксплуатационную безопасность.
Надежные испытания лопастей ветровой турбины от мирового лидера
Являясь мировым лидером в области проведения испытаний, экспертиз и инспекций, мы предлагаем услуги опытных специалистов в секторе ветроэнергетики, передовые технологии и уникальные знания.
Наш современный Международный центр ветроэнергетических технологий (WETC) расположен недалеко от китайского порта Тяньцзинь, в который легко попасть из любого пункта Азиатского региона. Этот центр инновационных исследований лопастей ветротурбин оснащен самыми последними технологическими решениями. Как результат, мы проводим полномасштабные испытания лопастей ветровой турбины для ветродвигателей на суше и на некотором расстоянии от берега. WETC предоставит вам знания и опыт квалифицированных инженеров мирового уровня, где бы ни находилось ваше предприятие.
Услуги WETC включают:
- полномасштабные статические испытания лопастей ротора, а также приложение нагрузки с помощью гидравлической лебедки;
- полномасштабные динамические испытания лопастей ротора с использованием расположенных на лопастях опор для возбудителя или наземных возбудителей;
- определение частоты собственных колебаний.
- сертификационные испытания, соответствующие международным стандартам, например, IEC 61400-23;
- оценка конструкции лопасти ротора;
- испытания качества изготовления;
- оценка ремонтных работ или изменений в конструкции;
- инспекцию производства лопастей, форм для отливки лопастей, вращающихся устройств и обтекателей;
- инспекцию лопастей в процессе эксплуатации и анализ основной причины выхода лопасти из строя;
- испытания образцов составных материалов;
- дополнительные испытания методами неразрушающего контроля (НК), специально разработанные для контроля состояния лопастей ротора;
Чтобы помочь вам избежать задержек и снизить расходы, все тестирования проводятся в кратчайшие сроки и выполняются в соответствии с принципами бережливого производства Lean. Помимо этого, благодаря нашим надежным системам защиты информации вы можете оставаться уверенными в безопасности своей интеллектуальной собственности.
Являясь единственным прошедшим международную аккредитацию местным исследовательским центром в Китае, WETC обладая следующими аккредитациями и работает в рамках следующих систем менеджмента:
- аккредитация Службой аккредитации Великобритании (UKAS) согласно ISO 17025 для проведения полномасштабных испытаний лопастей;
- система менеджмента информационной безопасности (ISMS) согласно ISO 27001;
- система менеджмента охраны здоровья, промышленной безопасности и окружающей среды (HSE).
В WETC проводятся комплексные тестирования, отчеты по которым доступны на английском и китайском языках.
Обратитесь к нам, чтобы узнать, как испытания лопастей ветровой турбины позволяют проверить надежность, предотвратить неисправности и увеличить срок службы лопастей ротора.
АО «Казанский Гипронииавиапром» им. Б.И.Тихомирова»
АО «Казанский Гипронииавиапром» им.
ПАО «Казанский вертолётный завод» г.Казань Республики Татарстан.
Цель реорганизации существующего механообрабатывающего производства – создание комплекса специализированных, оснащенных современным оборудованием производств, обеспечивающих изготовление и поддержание жизненного цикла вертолетов в соответствии с производственной программой.
В процессе реорганизации формируются новые механообрабатывающие и механосборочные участки, сборочные участки, подготовка производства, оптимизируется внутренняя логистика.
2. Реконструкция малярного производства серийных и перспективных вертолетов, включая “Ансат-У”Корпус цеха малярного производства серийных и перспективных вертолетов представляет собой пристрой, к существующему производственному корпусу, на территории Казанского вертолетного завода.
-подготовки собранного изделия к окраске;
-окраски изделий и деталей;
-внутренней отделки;
-сдачи готового изделия
3. Проектирование и строительство корпусов для производства лопастей вертолетов из композиционных материалов
Разработан и реализуется проект создания современного производства лопастей и деталей фюзеляжа из полимерных композиционных материалов на основе реконструкции корпусов и строительстве новых корпусов, связанных единой коммуникационной теплой галереей.
Производственные участки, на которых перерабатываются неотвержденные материалы, чувствительные к микро-климату, выделены в «чистые помещения» с контролируемой средой по содержанию пыли, температуре и влажности.
4.
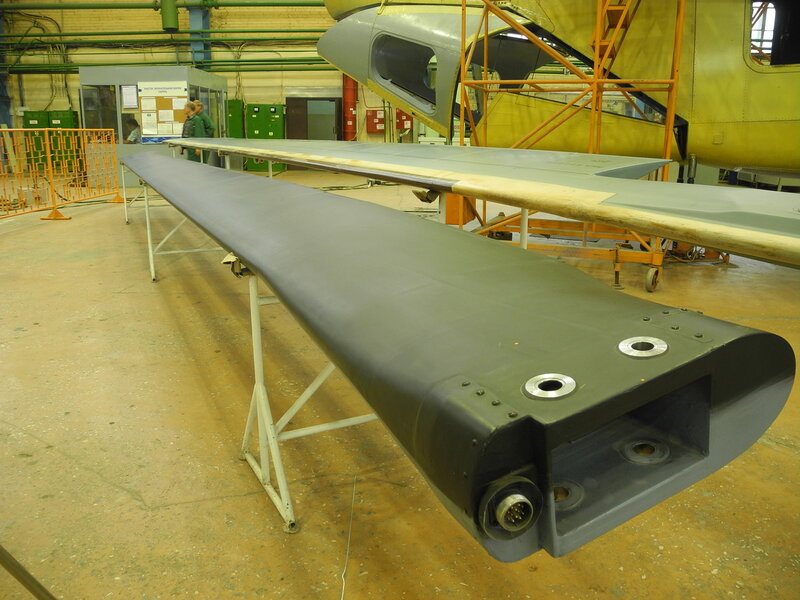
Основной целью проекта является создание серийного производства выпуска лопастей из ПКМ, на базе существующего опытного производства. Применение ПКМ в конструкции вертолетов обеспечивает новый качественный скачок в увеличении прочностных характеристик и уменьшении массы вертолетов.
Целью реконструкции является организация новых участков для изготовления деталей и узлов с целью специализации участков, цехов по видам обработки.
Механизация складированных заготовок, оснастки и готовых деталей за счет внедрения механизированных штабеллеров.
Цеха заготовительно-штамповочного производства группируются в одном корпусе в смежных площадях, минимизируются транспортные операции.
6. Строительство и оснащение гальванического производстваОсновной целью проекта является строительство и техническое перевооружение гальванического производства на базе современного высокопроизводительного оборудования и технологий, обеспечивающих рост уровня производства изделий авиационной техники.
Реконструкция предусматривает строительство корпуса с организацией производственных участков: гальванического, окраски, клеесварки панелей.
7. Реконструкция цехов подготовки производства
Целью разработки проекта является создание производства, обеспечивающего основное производство вертолетов технологической оснасткой в объемах и номенклатуре на уровне современных и перспективных требований.
Реконструкция комплекса цехов подготовки производства включает в себя:
- объединение разрозненных участков, цехов подготовки производства в единый комплекс;
- замену устаревшего оборудования;
- реконструкцию производственных участков, энергетических помещений в соответствии с требованиями технологических, санитарно-гигиенических и противопожарных норм.
8. Реконструкция испытательной базы
Целью реконструкции испытательной базы является создание современных условий для проведения испытаний узлов и агрегатов вертолетов, метрологического обеспечения испытаний, ремонта и выпуска вертолетов.
Основной задачей реконструкции производства является приобретение и внедрение в производство современного высокопроизводительного оборудования, программного обеспечения и технологий.
В состав испытательной базы входят два корпуса: корпус для размещения службы Главного Метролога и лаборатории динамических испытаний; и корпус – оснащение лабораторий испытаний материалов и покупных комплектующих изделий.
9. Реконструкция аэродромной базы
Основной задачей реконструкции является сохранение имеющегося аэродромного комплекса экспериментальной авиации, выполнение работ по его восстановлению и доведению технического и эксплуатационного уровня аэродрома до нормативных показателей за счет восстановления и развития комплекса сооружений, в том числе строительства зданий административного корпуса для размещения служб ЛИК и КДП, ангара обслуживания вертолетов, реконструкции объектов электроснабжения и системы аварийного энергообеспечения объектов аэродрома, комплекса оборудования метеообеспечения, средств связи и радиотехнического оборудования обеспечения полетов.
Макет можно посмотреть здесь…
Изготовление стеклопластиковой лопасти для ветрогенератора
Изготовление лопасти в матрице начинается с подготовки самой матрицы, нужно тщательно натереть форму воском чтобы получился разделительный слой и лопасть не приклеилась к матрице. В данном случае здесь применялся автомобильный воск, он наносился в несколько этапов. То-есть наносилось несколько слоёв с временным интервалом, и каждый слой хорошо растирался, потом вытерался лёгкими движениями сухой тканью, чтобы не было никаких разводов.Потом дополнительно был нанесён слой жидкого воска, который был растворён в бензине, нанесение производилось через бутылочку с брызгалкой, тоже в несколько слоёв. В итоге поверхность матрицы стала матовой с абсолютно гладкой поверхностью, видно что есть достаточный разделительный слой и лопасть точно не прилипнет.
>
Далее следующий этап это нанесение белого гелькоута, который придаёт лопасти белый цвет и создаёт защитный слой. Это специальный двухкомпонентный высокопрочный состав. Он был слишком густой, поэтому 1:10 был разведён растворителем, и только после этого в него добавлен отвердитель и начался процесс нанесения его на матрицу. Нанесение производилось кисточкой, после чего нужно было выждать пока он не схватится.
>
Далее предстоит сделать бортики по краям лопасти чтобы потом две половинки склеились. Для этого и служат специальные планки, которые прикручиваются на обе половинки матрицы. Создание бортиков делалось так, с полиэфирной смолой были смешаны опилки, и этими опилками набивались бортики. В итоге получилось всё вот так.
>
Только после создания бортика начинается следующий этап. Далее заранее вырезанные заготовки стеклоткани укладываются в форму и пропитываются полиэфирной смолой. Вначале нужно нанести некоторый слой смолы на белый гелькоут и можно приступать к укладке слоёв стеклоткани. В данной лопасти укладывается по два слоя стекломата во всю длину лопасти, и далее количество слоёв увеличивается к корню лопасти. Все это заливается смолой и её общее количество 450 грамм. Вес компонентов нужно выдерживать очень точно, иначе лопасти получатся разные по весу.
>
После укладки стеклоткани и пропитки смолой на обе половинки матрицы одеваются пакеты, не обязательно одновременно, просто сразу две половины делать неудобно. Но в общем одеваются пакеты и из пакетов с помощью компрессора откачивается воздух. Пленка плотно обжимает стеклоткань и заставляет ее пропитываться смолой. Белые непропитанные пятна постепенно исчезают, можно помогать руками разглаживая под пленкой скопления смолы и продавливая непропитанные пятна. Когда смола начнёт схватываться то пакеты нужно снять и срезать ровно острым ножом выступающую стеклоткань. Получится в итоге вот так.
>
Процесс подрезания бортика и уже готовые для соединения половинки лопасти.
>
Далее чтобы уже соединить две половинки лопасти и наконец соединить две половины матрицы на бортики лопасти наносится эпоксидная смола. В смолу добавляется мука чтобы она стала гуще. После нанесения смолы по периметру две половины матрицы соелиняются и скручиваются на болты.
>
Теперь матрица оставлена на сутки до полного застывания полиэфирной смолы
>
Ну а вот и результат, готовая стеклопластиковая лопасть. Длина 1302 мм, а вес получился 1.8 кг.
>
Далее технология изготовления изготовления претерпела некоторые изменения, но в общем осталась такой-же. Помните бортики, которые набивались опилками смешанными с полиэфирной смолой, они заменены на специальную шпатлёвку с содержанием стекловолокна. Процесс изготовления стал быстрее и в общем сделаны все три лопасти.
Лопасти подготовлены к покраске, на них всё-таки кое-где есть небольшие раковинки, которые были зашпатлёваны и лопасти зашкурены. В итоге ниже на фото конечный результат.
>
На фото все лопасти в кадр не поместились, но их три штуки. В общем лопасти готовы, теперь дело за созданием хаба для крепления лопастей.
>
Вот и завершился этап изготовления лопастей, они получились, и вроде всё хорошо. Вес лопастей имеет небольшой разбег, но это компенсируется балансировкой винта. Теперь будет изготовлено крепление лопастей и новый винт из профильных стеклопластиковых лопастей будет установлен на ветрогенератор. Продолжение в следующей части, там будет изготовление уже самого винта и показания ветрогенератора с этим винтом.
РосЭнергострой — Производство винтовых свай и лопастей для свай
Изготовление лопастей для винтовых свай от 57 до 325 диаметра, разработка лопастей по индивидуальным размерам заказчика, подгонка лопасти под трубу нестандартного диаметра
Производство винтовых свай и монтаж свайно-винтовых фундаментов согласно всем нормативам и ГОСТам
Плазменный раскрой листового металла на станке ЧПУ
Изготовление любых заборов под ключ
Монтаж свайных винтовых фундаментов в любое время года ручным и механизированным способом
Комплектующие для свай
Винтовые сваи гораздо экономичней сделать своими руками, но самый главный элемент конструкции – это лопасти для винтовых свай. Лопасти должны иметь правильные форму и шаг гибки, только тогда им гарантирован лёгкий заход в грунт. Если вы занимаетесь строительством домов, монтажом винтовых свай и желаете сэкономить на сборке, вы знаете что лопасти лучше приобрести у профессионалов.
Часто компании не желают продавать лопасти отдельно, а стараются продать конструкцию целиком втридорога, да еще и навязать свой монтаж. Лопасти для винтовых свай мы разрабатываем и испытываем сами, присутствуя на монтажах и прислушиваясь к рекомендациям наших опытных монтажников. Вырезаны наши винтовые лопасти на станке ЧПУ, погнуты на профессиональном прессе. Лопасти для винтовых свай мы можем изготовить не только стандартных размеров, но и по индивидуальным размерам заказчика. Уменьшим или увеличим внешний диаметр лопасти, подгоним внутренний диаметр под трубу любого размера, изготавливаем ходовые диаметры, а также очень качественные лопасти больших диаметров.
Винтовые сваи
Наши винтовые сваи дешевле, чем у других производителей. Мы закупаем оптом трубу у производителей без посредников, лопасти делаем сами, и этим удешевляем конечную стоимость винтовых свай. Винтовые сваи нашего производства изготовлены из толстостенной газпромовской трубы, но их цена не превышает стоимость эконом варианта, потому что мы не хотим заработать всё и сразу, а нацелены на прибыль с оборота, который у нас постоянно растёт благодаря хорошим рекомендациям.
Витрина предложений
Заказ на сайте или телефонный звонок менеджеру.
Обсуждение условий, консультирование клиента.
Изготовление изделий в оговоренные сроки .
Выезд бригады для установки (по необходимости).
Доставка в Центральном федеральном округе.
Оплата по безналу или наличными при встрече.
Связаться с нами
Ищете новые решения в строительстве?
Винтовые сваи от производителя
Достойная альтернатива традиционному фундаменту.
Сделайте возведение вашего дома, коттеджа, дачи или забора проще и экономичнее, применив свайную технологию. Воспользуйтесь услугами нашей компании, и мы гарантируем комфортную и быструю строительную кампанию!
Витрина предложений
Завод Vestas и Роснано в Ульяновске осуществил поставку лопастей для 100 ветроустановок
28.09.202025 сентября завод «Вестас Мэньюфэкчуринг Рус», расположенный в Ульяновской области, отгрузил сотый комплект лопастей для ветроустановки. Инновационные компоненты оборудования отправятся на площадку ветропарка в Астраханской области.
«Поздравляю коллектив завода «Вестас» с выпуском юбилейного, сотого комплекта лопастей для ветрогенераторов, произведённых на территории Ульяновской области. Я благодарю каждого, кто причастен к выпуску очередной партии лопастей. Продукция предприятия — это элемент сверхсовременного энергетического комплекса. «Вестас» совместно с РОСНАНО помогает оставаться нашему региону в числе лидеров России по производству и использованию возобновляемой энергетики. Развитие этой сферы — прекрасная возможность включиться в технологические цепочки мировых компаний на глобальных рынках», — отметил глава региона Сергей Морозов.
Таким образом, с начала 2019 года предприятие, первым в России освоившее выпуск инновационных изделий, поставило на площадки российских и зарубежных ветропарков 300 композитных лопастей. С использованием данных компонентов возведено 100 ветроустановок Vestas общей мощностью около 400 МВт. Выработка низкоуглеродной генерации такой мощности позволяет ежегодно сокращать выбросы углекислого газа на 380 тысяч тонн в год по сравнению с выбросами от традиционной генерации. Чистая электроэнергия, произведенная ветропарками с ульяновскими лопастями, покроет потребление 340 тысяч средних домохозяйств.
Благодаря поддержке правительства Ульяновской области и беспрецедентным мерам безопасности выпуск лопастей не прекращался даже весной 2020 года, в наиболее сложный период пандемии.
Завод «Вестас Мэньюфэкчуринг Рус» ежегодно наращивает выпуск продукции – в 2020 году производство лопастей увеличилось на 40%. Лопасти из Ульяновска установлены на ветропарках Фонда развития ветроэнергергетики, созданного АО «РОСНАНО» и ПАО «Фортум», в Ростовской области и Калмыкии в составе комплексной ветроустановки Vestas. В планах на 2021 год – поставки на площадки Фонда в Астраханской и Ростовской областях.
«Vestas вместе с РОСНАНО и локальными промышленными партнерами успешно развивает производство в Ульяновске. Качество российских изделий подтверждено первой экспортной поставкой в Данию в этом году и долгосрочным портфелем заказов общей мощностью более 1800 МВт по рамочному соглашению с Фондом развития ветроэнергетики для российского рынка ВИЭ. Мы уверены, что наши лопасти смогут соответствовать повышенным требованиям к локализации оборудования в рамках второй программы поддержки в России – на следующем этапе, помимо стеклотканей, в производстве будут использоваться пултрузионный профиль, смолы и другие комплектующие российского производства», — сообщил генеральный директор «Вестас Мэньюфекчуринг Рус» Кимал Юсупов.
Напомним, предприятие «Вестас Мэньюфэкчуринг Рус», введенное в эксплуатацию в декабре 2018 года, производит композитные лопасти для турбин ветроэнергетических установок, не имеющие аналогов в РФ. Производственная площадка расположена на территории авиационного кластера в Ульяновске. Лопасти предназначены для установок мощностью от 3,4 до 4,2 МВт. Партнерами проекта выступают Vestas, РОСНАНО и Консорциум инвесторов Ульяновской области, в состав которого входит Корпорация развития Ульяновской области и Ульяновский наноцентр ULNANOTECH. На высокотехнологичном предприятии создано более 500 рабочих мест.
«Для нас важны такие предприятия, как «Вестас» — инновационный завод, создающий новые для региона компетенции и самое главное – рабочие места для его жителей. Предприятие работает на пересечении отраслей как ветроэнергетики, так и отрасли композитных материалов. Наша задача сейчас – привести для этой компании партнёров — тех, кто будет сотрудничать с ними по производству связующих и композитного сырья. Эти компании смогут поставлять композитные материалы также для отраслей автопрома и авиационной промышленности, что позволит развивать новые направления в регионе», — рассказал генеральный директор Корпорации развития региона Сергей Васин.
Для справки:
Датская Vestas — мировой лидер в производстве ВЭУ — совместно с РОСНАНО осуществляет трансфер технологий ветроэнергетики и наращивает в России свои производственные мощности. Производство лопастей в Ульяновске стало одним из ключевых этапов программы локализации оборудования ветроэнергетики в России (вклад в степень локализации ВЭУ — 18%). Vestas выбрана поставщиком оборудования ВЭУ для Фонда развития ветроэнергетики, реализующего проекты строительства ветропарков общей мощностью более 1800 МВт до 2023 года.
Дополнительная информация:
Фадеева Татьяна, | [email protected] |
Как изготавливаются лезвия | Наш производственный процесс
Независимо от отрасли, вы оцените ценность высококачественных режущих инструментов. Ножи для промышленных машин — незаменимые компоненты вашей системы. Они используются для уменьшения размера материала при переработке продуктов от бумаги до свинины. Хотя вы, возможно, знаете свои процессы, связанные с машинными ножами, пожалуйста, обратите внимание на требования, которые нам необходимы для производства ваших ножей. Большинство производственных систем сосредоточены на производительности, являющейся ключевым элементом прибыльного успеха.Наши высококачественные ножи играют активную роль в этом успехе. Их почти не замечают, если только что-то не идет не так. Как и в любой производственной системе, существует особый процесс изготовления высококачественных машинных ножей. York Saw and Knife Co. — ведущий американский производитель прецизионных ножей и лезвий для лесопилок. Независимо от того, в какой отрасли вы работаете, мы можем предоставить вам режущие инструменты и надежные, точные ножи по доступным ценам. Частью наших обязательств по обслуживанию клиентов является обмен информацией.Сегодня мы хотели бы объяснить, как мы производим машинные ножи.
Распространенных типов машинных ножей, которые мы производим:
Когда дело доходит до машинных ножей, процесс будет немного отличаться в зависимости от типа лезвия, которое вы производите. К распространенным типам лезвий, которые мы производим, относятся:
Характеристики металла лезвияОстрые ножи и лезвия имеют решающее значение во всем, от обработки пищевых продуктов до производства и упаковки. Существует множество материалов, из которых изготавливаются лезвия ножей, однако есть две основные характеристики, которые помогают сохранить остроту ножей.Один из них — твердость материала лезвия. Другой — это прочность материала лезвия.
Не путайте. Это две разные проблемы, и их необходимо уравновесить, чтобы получить отличные лезвия для машинных ножей с долгим сроком службы. Сочетание твердости и прочности позволяет создавать отличные лезвия.
Твердость относится к плотности лезвия ножа. В производстве лезвий для станков мы измеряем твердость металла по шкале С Роквелла. Как правило, чем выше число C по Роквеллу, тем плотнее и, следовательно, тверже материал.Но то, что у определенного металла высокая шкала Роквелла, не означает, что этот материал прочный или жесткий. Многие крупномасштабные металлы легко разрушаются и быстро теряют свою остроту.
Прочность относится к тому, насколько хорошо лезвие ножа противостоит эрозии и истиранию. Мы измеряем вязкость металла по его прочности на разрыв в поперечном направлении (TRS). В науке о металлах модуль упругости Юнга — это физический принцип или руководство, определяющее вязкость металла. Чем выше показатель TRS у металла, тем он прочнее.
Вы могли бы подумать, что лезвия ножей с высокими номерами Rockwell C и TRS будут идеальным материалом. К сожалению, это невозможно. Показатели TSR и Rockwell обратно пропорциональны. Физические свойства диктуют, что более твердые металлы имеют тенденцию быть хрупкими и легко повреждаемыми. Более мягкие металлы могут оказаться невероятно прочными, поскольку они обладают эластичностью, поглощающей внешние силы.
Выбор правильного баланса твердости и прочности металла — это то, от чего зависят клиенты York Saw and Knife.У нас есть выбор проверенных металлов для лезвий, и мы полагаемся на них как на основу нашего производственного процесса. Тем не менее, мы часто заставляем клиентов присылать нам свои собственные лезвия для механических ножей, которые мы можем воспроизвести или воспроизвести.
Первое, что мы делаем, — это анализируем металл и определяем его характеристики, чтобы реконструировать его. Затем мы следуем простому шестиэтапному процессу изготовления машинных ножей. Мы используем этот процесс независимо от того, производим ли мы стандартные ножи или создаем специальные приложения.
Вот как работает процесс производства пил и ножей York: Шаг 1. Отправьте образцыСначала начнем с образца или чертежа лезвия машинного ножа.Обычно это предоставляет наш клиент, у которого уже есть оборудование с конкретными ножами. Нас просят воспроизвести конфигурацию ножа. Часто нас также просят улучшить его рабочие характеристики, чтобы сделать заменяемую модель более жесткой или жесткой.
Мы всегда рекомендуем вам звонить нашим специалистам по продажам или общаться с ними по электронной почте. Полезно прикрепить цифровые фотографии или рисунки вашего клинка. Мы обсудим вашу заявку и постараемся решить вашу проблему и предложить работоспособное решение.Мы также зададим конкретные вопросы о типе материала вашего ножа, геометрии лезвий и типах продуктов, которые вы будете резать.
Затем мы попросим вас отправить нам лезвие или лезвия для тестирования. В York Saw and Knife нет платы за тестирование. Это часть нашей расширенной службы поддержки клиентов. После того, как мы изучим ваши ножи, мы предоставим вам бесплатное ценовое предложение. После этого мы будем ждать, пока вы разрешите нам перейти к шагу 2.
Шаг 2. Обратное проектирование ножаОбратный инжиниринг — это причудливый термин для обозначения вещей в обратном направлении.В нормальном производственном процессе продукт начинает жизнь после того, как инженеры потратили огромное количество времени на исследования и разработки, проектируя и тестируя прототипы. Это задолго до того, как получится конечный продукт.
Когда вы отправляете нам машинный нож для копирования, мы начинаем с готового продукта и должны выяснить, как он был построен. Это инженерия наоборот. Мы можем видеть вашу конфигурацию, но понятия не имеем, из чего она состоит, пока не проведем инженерные испытания.
Во-первых, мы используем оптический компаратор для создания компьютеризированной модели лезвия ножа вашего станка.При этом оцениваются физический размер, точные углы и характеристики, такие как зазубрины лезвия и монтажные отверстия для штифтов. Мы также оцениваем любые трудности, которые мы можем предвидеть при воспроизведении операционной модели.
Затем мы используем испытательную машину Rockwell, чтобы определить твердость вашего лезвия. Мы также оценим прочность вашего существующего металла. Затем мы проводим металлургический анализ, чтобы узнать характеристики вашего металла. Таким образом, мы узнаем, сможем ли мы воспроизвести лезвие из аналогичного металла или порекомендуем перейти на другой сплав.
Наконец, мы делаем точные физические измерения. Это включает в себя компьютеризированный пресс для нагрузки на лезвие, измерения с помощью цифровых штангенциркулей и использования прецизионного микрометра, аналогичного тому, что есть в ящике для инструментов машиниста. После того, как мы выполним реверс-инжиниринг и составим физическую компиляцию вашего клинка вместе со стальными атрибутами, мы отправим эту информацию в наш инженерно-оценочный отдел. Они подготовят для вас подробное и твердое смету на производство. Чтобы узнать больше о реверс-инжиниринге, нажмите здесь!
Шаг 3: Резка и термическая обработка лезвияВся продукция York Saw and Knife начинается с необработанной стали.У нас есть регулярный запас проверенных металлов, которые, как мы знаем, будут хорошо работать с материалами, которые вы режете. Наш основной стальной ассортимент включает пружинную сталь, углеродистую легированную сталь, инструментальную сталь и быстрорежущую сталь. Хотя мы полагаемся на эти проверенные металлы, мы можем изготовить для вас любой профиль ножа станка по индивидуальному заказу.
После того, как вы утвердили заводские чертежи ножа, мы вырезаем его профиль из стальной заготовки. В зависимости от заказа мы используем два разных процесса резки. Один из них — это гидроабразивная резка, при которой вода под очень высоким давлением разрезает металлическую заготовку.Другой метод резки выполняется лазером или усиленным светом. Лазерная резка — наш предпочтительный метод, и мы инвестировали в станок Trumpf Laser 2025 для максимально точной резки.
После того, как ваш нож будет разрезан или профилирован, мы подвергаем его серии тепловых процессов. Это определяет окончательную твердость и жесткость вашего лезвия. Процесс закалки состоит из трех этапов:
. Закалка: Стальные сплавы на основе железа отправляются в печь с температурой 1750 градусов по Фаренгейту.Это ниже точки плавления, но достаточно для того, чтобы произошли металлургические изменения. Тип металла определяет, как долго лезвие остается при таком нагреве. Время является критическим фактором на этапе закалки, и для лезвия очень важно провести точное время под действием тепла.
Закалка: Как только ваше лезвие потратит свое точное время на то, чтобы греться в духовке, оно быстро вынимается и быстро охлаждается. Обычно это делается путем опускания его в воду. Это вызывает трансформацию молекулярной структуры.Опять же, время — главный фактор для успешной закалки. Молекулярные изменения продолжаются, пока ваше лезвие не достигнет комнатной или комнатной температуры.
Отжиг или отпуск: как только лезвие ножа достигает температуры окружающей среды, оно достигает максимальной твердости. Это не обязательно лучший показатель для производительности, учитывая обратную зависимость между твердостью и ударной вязкостью. Специалисты в области металлургии York Saw and Knife знают точную твердость стали, которую они ищут. Теперь они закаляют или отжигают лезвие, чтобы снизить его твердость и добиться оптимальной производительности.Ваше лезвие возвращается в духовку при температуре от 300 до 1000 градусов по Фаренгейту на четыре часа или больше.
После того, как нож будет должным образом закален, он готов к чистовой обработке, шлифовке и заточке. Это начинается со сплющивания и натяжения, которые снимают напряжение внутри лезвия. В York Saw and Knife мы используем проверенные процессы для снятия напряжения и выравнивания вашего лезвия. Некоторые из них включают сложные компьютерные машины.Другие полагаются на зоркий глаз и умелые руки наших машинистов.
Если плоскостность является проблемой из-за того, что лезвие не соответствует действительности, мы используем машину для правки и натяжения. Это устройство разработано специально для производства машинных ножей. Это помогает нашим техническим специалистам в комнате наковальни экономить труд и часы, автоматически обнаруживая неисправности и исправляя их.
Тем не менее, человеческому прикосновению нет замены. Некоторые профили ножей требуют специальных световых осмотров для выявления несоответствий корпуса лезвия.Мы используем разные веса и конфигурации шлифовки лица, такие как подход Dog и Twist. Это может показаться сложным, но часто наши машинисты и техники просто используют специальные молотки, чтобы устранить проблемы.
Другие этапы правки включают выравнивание лезвий с помощью пресса с автоматической подачей, вращение их на оси с одновременной проверкой правильности с помощью циферблатного индикатора, укладку лезвий на плоский стол и визуальный осмотр их с помощью линейки машиниста. На этом этапе рабочие используют прецизионный молоток для исправлений и переделок.
Наконец, ваше новое лезвие отшлифовано для получения острой кромки. Мы используем как автоматические, так и ручные методы шлифовки и заточки. На механических шлифовальных машинах лезвия остаются острыми, а при окончательном хонинговании у готового продукта остается лезвие бритвы. Это последний этап изготовления ножей перед прохождением контроля качества.
Шаг 5: Окончательная проверка качестваКаким бы сложным ни было наше оборудование, мы не можем полагаться только на автоматизацию для контроля качества.Каждый из предыдущих этапов процесса имеет свой параметр контроля качества. Однако время от времени проскальзывает недостаток. В Йорке недостатки недопустимы.
При получении машинных ножей York вы можете быть уверены, что каждое лезвие прошло визуальный осмотр. Мы ищем очевидные недостатки и не столь очевидные ошибки. Любое лезвие, не соответствующее требованиям проверки качества York, снимается с конвейера. Неисправные лезвия переделываются или выбрасываются.
Часть нашего процесса контроля качества основана на опыте.York Saw and Knife начало производство в 1906 году. Это дает нам более чем 100-летний опыт. Мы знаем, как производить высококачественные ножи для станков и пильные полотна. В результате наши первоначальные производственные процессы превосходны, и у нас редко возникают проблемы с нашими продуктами. Если это так, то они попадаются на глаза и никогда не покидают магазин.
Шаг 6. Доставка и использование лезвияГотовые машинные ножи являются изделиями высокой точности. Они заслуживают того, чтобы к ним относились как к таковым.Мы очень гордимся каждым производимым нами клинком и полны решимости обеспечить его доставку к вашим дверям в первозданном виде. Как покупатель York Saw and Knife, у вас просто не было бы другого выхода.
Наш упаковочный отдел уделяет особое внимание защите острых кромок. Мы упаковываем всю поставляемую продукцию с особой тщательностью и вниманием к деталям. Когда мы защищаем основную режущую кромку, мы обеспечиваем индивидуальную упаковку лезвия, чтобы избежать контакта металла с металлом, когда мы отправляем несколько лезвий в одном заказе.
Наш отдел доставки следит за тем, чтобы в любом заказе не было сыпучих продуктов. Мы изолируем все машинные ножи, даже если они массово отправляются на ваш объект. Наши наружные упаковочные материалы доказали свою надежность и защищают ваши ценные лезвия на пути из нашего магазина в ваш.
После того, как вы установите и начнете использовать лезвия New York для пил и ножей, уделите время осмотру готовой продукции. Если по какой-либо причине вы не удовлетворены, немедленно свяжитесь с нами, и мы исправим ситуацию.Проблемы с ножами York Industrial Blades маловероятны. Наша репутация основана на качестве и надежности.
Хотите узнать больше?
Если вы хотите узнать больше о лезвиях для вашей отрасли, нажмите ниже! В York Saw мы производим огромное количество лезвий для самых разных отраслей промышленности.
Производство инновационных лопастей ветряных турбин
КАК КРУПНЕЙШИЕ ВЕТРОВЫЕ ТУРБИНЫ GE СТАНОВАЛИСЬ РЕАЛЬНОСТЬЮ С LM WIND POWER
The Cutting Edge: взгляд изнутри турбина LM Wind Power Производство лопастей Производство — Провинция Кастельон в Испании может быть туристическим направлением из-за наскальных рисунков, но жаркий и сухой климат привлекал кое-что еще в этом регионе — LM Wind Power , которые сочли это прекрасным местом для своего завода , построившего ветряные турбины высокой мощности . Предприятие создает и производит массивные лопасти ветряных турбин, которые составляют такую важную часть турбин GE Renewable Energy. Неудивительно, что когда вы поймете , как строятся ветряные турбины , вы обнаружите в нем немалый подвиг.
Завод по производству ветряных турбин , на котором сейчас работает более 600 рабочих (это вдвое больше, чем было всего два года назад), не всегда создавал некоторые из самых больших лопастей ветряных турбин на сегодняшний день.Десять лет назад, примерно в то время, когда был построен завод, рабочих производили лопастей ветряных турбин, длина которых составляла около 37,3 метра. Сравните это с 73,5-метровыми лопастями, которые сейчас производит LM Wind Power , и вы увидите, что вдвое увеличилась не только рабочая сила.
На изготовление каждой лопасти ветряной турбины требуется два дня и 100 сотрудников. Процесс сборки ветряной турбины тщательно организован — нужно много управлять, включая материалы ветряной турбины.Сначала рабочие делают лезвия из стеклоткани и пробкового дерева. Затем лезвие покрывают воздухонепроницаемой фольгой, и команда устанавливает сеть трубок, которые накачивают и распределяют смолу, которая будет удерживать его вместе.
После этого с пресс-формой выполняется дополнительная работа, обеспечивающая поддержание давления, температуры и вакуума внутри. Команда использует лазеры, чтобы убедиться, что каждое лезвие правильно изогнуто. После этого на лезвие наносится покрытие, которое защищает его от частиц пыли и капель воды и помогает ему развивать правильную скорость. Транспортировка лопастей ветряных турбин включает в себя огромный конвой, который используется для перевозки лопастей на ветряную электростанцию.
Способ изготовления ветряных турбин — это процесс, включающий десятки тысяч деталей, но в результате получился продукт, который делает энергию доступной для миллионов людей во всем мире. Команда LM Wind Power готовится помочь в изготовлении лопастей для самой мощной в мире морской ветряной турбины Haliade-X от GE Renewable Energy, и компания демонстрирует, что большие мысли всегда окупаются.
Узнайте больше об инновационных лопастях ветряных турбин LM Wind Power и производстве , связавшись с нами сегодня.
Прочтите полную информацию о GE Reports.
ветроэнергетических лопастей для производства композитов
Композитные ветровые лопасти обычно формуются из двух половинок, а затем склеиваются эпоксидным клеем. (Фото: LM Glasfiber)
Укладка стекломата для вакуумного вливания смолы ветровым полотном.Тенденция заключается в большей автоматизации производства лезвий. (Фото: LM Glasfiber)
Шлифовка и чистовая обработка — это трудоемкие этапы производства ветряных лопастей, которые можно сократить с помощью автоматизации или улучшения материалов и процессов. (Фото: Gamesa)
Огромный размер ветряных лопастей и высокие требования к качеству — два препятствия на пути производителей композитных материалов.(Фото: компании по производству формованного стекловолокна)
Большинство ветряных лопастей изготавливаются методом вакуумной инфузии, но некоторые отформованы из эпоксидных препрегов. Новые препреги оптимизированы для более быстрого отверждения и уменьшения чистовой обработки. (Фото: Hexcel)
Предыдущий СледующийМировой рынок ветроэнергетики рос на 23% ежегодно в течение последних 10 лет, говорит Чарльз Казмиерски, руководитель проекта Lucintel, консалтинговой фирмы по пластмассам, композитам и другим промышленным рынкам.Он ожидает, что к 2012 году мировой рынок композитных материалов для ветроэнергетики будет стоить около 6 миллиардов долларов.
Ветряная промышленность США исторически переживала цикл роста американских горок, в значительной степени продиктованный налоговыми льготами федерального правительства, которые субсидируют отрасль. По данным Американской ассоциации ветроэнергетики (AWEA), хроническая неопределенность по поводу периодического продления налоговой льготы привела к дорогостоящим циклам подъема и спада в отрасли с 2000 по 2005 год. Доступность кредита способствовала резкому росту с 2005 по 2007 год.Рынок может столкнуться с падением в 2009 году, если законодатели США не продлят кредит до конца 2008 года.
Даже несмотря на то, что судьба федеральных налоговых льгот все еще неизвестна, ветроэнергетическая промышленность США в первом квартале 2008 года с головокружительной скоростью продвинулась вперед с новыми производственными мощностями, в результате чего было введено 1400 мегаватт (МВт), или около 3 миллиардов долларов, новых генерирующих мощностей. место, сообщает AWEA.
Это наращивание производства оказало сильное давление на поставщиков смол, арматуры и материалов для сердцевины, таких как пробковое дерево и пена ПВХ.Поставщики сосредоточены на обеспечении качества и поставках, поскольку производители ветряных турбин глобализируют свою деятельность для удовлетворения растущего спроса. «До сих пор это был преимущественно европейский бизнес, но теперь это глобальный бизнес с поставками во все основные регионы», — объясняет Пол Лангемайер, директор по развитию глобального рынка поставщика эпоксидных смол Hexion Specialty Chemicals.
Большинство наблюдателей сходятся во мнении, что для долгосрочного роста потребуются технические инновации, которые сделают ветер более конкурентоспособным по сравнению с другими видами энергии.Одна из ключевых тенденций — стремление к повышению производительности. Производство лезвий с помощью вакуумной инфузии или формовки препрега является трудоемким процессом, и производители ищут способы сократить время цикла и сократить расходы. Роботизированная укладка, усовершенствованные методы отделки, состоящие из двух частей или сегментированные лезвия и производство на месте — потенциальные инструменты для сокращения затрат на рабочую силу и логистику. Утверждается, что новые методы формования препрега улучшают внешний вид поверхности и облегчают отделку. Поставщики смол и препрегов вводят материалы, которые отверждаются быстрее и при более низких температурах.
По мере увеличения мощности ветроэнергетики наблюдается тенденция к созданию более крупных и легких лопастей. Наблюдатели предполагают более широкое использование углеродного волокна — несмотря на недостатки, заключающиеся в более высокой стоимости и ограниченных расходах — из-за его большей жесткости и меньшего веса, чем у стандартного стекла E-glass. Между тем, традиционное стекло E и специальные изделия из стекла сдерживают конкуренцию со стороны углеродного волокна за счет новой химии и оптимизации для удовлетворения более высоких требований к производительности.
МАТЕРИАЛЫ И МЕТОДЫ
Ветряная турбина состоит из нескольких составных частей; но лезвия, сделанные из армированной волокном эпоксидной смолы или ненасыщенного полиэстера, представляют собой наиболее широко используемый материал.Другие детали турбины, изготовленные из полиэстера, включают гондолу (корпус для коробки передач, генератора и других компонентов) и ступицу. Преобладающий метод обработки — вакуумная инфузия смолы. Он генерирует низкое содержание летучих органических соединений и может равномерно смачивать крупные детали контролируемым количеством смолы, что облегчает производство более легких и менее дорогих лезвий.
Формование препрега из тканого или однонаправленного стеклоткани более дорогое, но обеспечивает большую консистенцию, поскольку уже содержит матричный материал (обычно эпоксидную смолу).В зависимости от размера лезвия, вакуумная инфузия или формование препрега занимает от 12 до 24 часов.
Обычно эти лопасти аэродинамической конструкции состоят из 70-75% стекла по весу и должны отвечать очень строгим механическим требованиям, таким как высокая жесткость и устойчивость к скручиванию и усталости. При 20-летнем сроке службы типичны высокие статические и динамические нагрузки в широком диапазоне температур. Стандартная лопатка длиной от 35 до 40 метров для турбины мощностью 1,5 МВт весит от 6 до 7 тонн.
И эпоксидная смола, и полиэфир, и, в меньшей степени, виниловый эфир, на первых порах были частью бизнеса ветровых лопастей, но эпоксидная смола получила предпочтительный статус по мере того, как лезвия стали длиннее.Полиэстер легче обрабатывать и дешевле, но эпоксидная смола обеспечивает более высокие механические характеристики — особенно прочность на растяжение и изгиб — для лезвий длиной более 26 м (85 футов). В отличие от эпоксидной смолы, полиэстер не требует дополнительного отверждения, но лезвия обычно тяжелее.
СтеклоE является наиболее часто используемым армированием, в то время как более дорогостоящее углеродное волокно используется в ограниченных количествах для большей жесткости и уменьшения веса в более длинных лезвиях.
Препятствия на пути к производству ветряных лопастей огромны.Они включают в себя физический масштаб деталей, потребность в конкурентоспособных технологиях и производственных ноу-хау, хорошую базу поставок, глобальное присутствие и крупные инвестиции. По словам Казмиерски, в мире насчитывается около 12 поставщиков ветряных турбин, четыре из которых занимают около 72% рынка. Большинство этих ведущих производителей изготавливают свои собственные лопасти, но некоторые, например GE Energy, заключают контракты с такими фирмами, как MFG, Ashtabula, Огайо, и TPI Composites Inc., Скоттсдейл, Аризона. Ведущий производитель ветряных турбин в мире. это датская Vestas Wind Systems A / S (23% рынка), за ней следуют GE Energy, испанская Gamesa (17%), немецкая Enercon, индийская Suzlon (10.5%) и немецкой Siemens.
Ведущим производителем лезвий в мире является датская компания LM Glasfiber A / S, которая производит от 8000 до 9000 лезвий в год и занимает 25% рынка. Компания начала производство в 1978 году и расширила свою деятельность по всему миру, открыв новые заводы в США в Гранд-Форкс, Северная Дакота, и Литл-Рок, штат Арканзас. Она утверждает, что на сегодняшний день у нее самая большая общая установленная база лопастей: каждая третья турбина в мире оснащена лопастями.
LM использует вакуумную инфузию и то, что она называет «умной инженерией», для производства ветровых лопастей из полиэстера, которые дешевле, чем эпоксидная смола, но при этом обладают высокими характеристиками.По словам Стина Бруста Нильсена, директора по связям с общественностью, процесс был оптимизирован для создания прочного, однородного ламината с более быстрым отверждением, что сокращает время производства на несколько часов.
LM адаптировала свою технологию для производства самой длинной ветровой лопасти в отрасли. Лопасть длиной 61,5 м (202 фута), созданная для турбины мощностью 5 МВт немецкой компании REpower Systems, весит 17,8 тонны. Турбина имеет диаметр ротора 126 м (413 футов), а три лопасти покрывают площадь, почти равную двум футбольным полям.Наиболее примечательным является способность LM использовать E-стекло для обеспечения жесткости и легкости при длине порога выше 40 м, где обычно рассматривается углеродное волокно.
LM использует роботов и другую автоматизацию для укладки стеклянного мата в формы и склеивания корпусов лезвий вместе. Чтобы оптимизировать процесс и сократить время цикла, LM инвестирует в новую технологию лезвий, основанную на неизвестном новом волокне, которое, как сообщается, сократит время производства лезвий вдвое. Половина 12-миллионного бюджета исследовательской программы LM «Blade King» поступает из Датского национального фонда передовых технологий.Ожидается, что новая технология повысит эффективность укладки и формования волокна. LM сотрудничает с датской Aalborg Univ. и Risoe DTU по разработке волокна, а также с Comfil, датским специалистом в области термопластичных композитов.
В США компания MFG скоро откроет новый завод в Абердине, штат Южная Дакота, по производству лопаток для популярных турбин GE мощностью 1,5 МВт. MFG вышла на рынок, выпустив 9-метровые лопасти в конце 1980-х, и, по словам Карла ЛаФранса, менеджера по ветроэнергетике, за последние шесть лет продажи выросли в восемь раз.
Как и большинство других производителей лезвий, MFG использует вакуумную инфузию для формования стеклопластиковых лезвий длиной от 34 до 49 м. По словам ЛаФранса, оптимизация дизайна и процессов играет решающую роль. «Все дело в деталях; это то, как укладывать ткань, заряжать форму и как получить смолу, чтобы заполнить форму ». Поскольку объемы производства только сейчас предоставляют возможности для автоматизации, MFG полагается на методы бережливого производства и принципы 6-сигм, чтобы добиться всех возможных улучшений процессов.
TPI Composites — еще один сильный игрок в США с новыми расширениями в США, Мексике и Китае. Компания поставляет GE Energy с нового завода площадью 190 000 кв. Футов в Тайканге, Китай, и нового завода площадью 316 000 кв. Футов в Ньютоне, штат Айова. VienTek, совместное предприятие TPI с японской Mitsubishi Power Systems, недавно утроило свои мощности по производству лопастей в Сьюдад-Хуаресе, Мексика, до примерно 500 000 кв. Футов.
TPI использует свою запатентованную технологию SCRIMP, форму вакуумной инфузии, доступную для лицензирования.Утверждается, что компоненты, изготовленные с помощью процесса SCRIMP, имеют более высокое содержание волокна, чем компоненты, уложенные традиционным способом. TPI заявляет, что может быть достигнуто соотношение стекло / смола 70:30 или выше по сравнению с типичным соотношением 50:50, что приводит к более легким и прочным деталям.
УНИКАЛЬНЫЙ ЦЕЛЬНЫЙ ДИЗАЙН
Большинство производителей турбин стремительными темпами глобализируют свою деятельность. Немецкая компания Siemens Wind Power открыла в прошлом году завод по производству ветряных лопастей в Форт-Мэдисоне, штат Айова. Тем временем датская Vestas объявила в августе о планах построить завод по производству лезвий в Брайтоне, штат Колорадо., чтобы дополнить существующий завод в Виндзоре, штат Колорадо. Ожидается, что два завода будут производить 3600 лопастей в год, когда завод в Брайтоне будет запущен в 2010 году.
Компания Siemens разработала инновационный процесс изготовления лезвий как одно целое, в отличие от обычного лезвия, которое состоит из двух частей и склеивается. В технологии Siemens IntegralBlade используется вакуумная инфузия для изготовления стеклянных / эпоксидных лезвий в закрытом процессе. Система формования имеет закрытую внешнюю форму и расширяющуюся гибкую внутреннюю камеру. Эпоксидная смола вводится под вакуумом, и лезвие отверждается при высокой температуре в форме.После отверждения лезвие извлекается из внешней формы, в то время как внутренний баллон сжимается под действием вакуума и снимается с лезвия. В результате получается цельное бесшовное лезвие.
Сообщается, что система IntegralBlade предлагает несколько преимуществ, включая более короткие циклы и более эффективное использование рабочей силы и пространства. «Требуется только один набор пресс-форм», — отмечает Хендрик Стисдал, технический директор Siemens Wind Power. Кроме того, нет проблем с допусками между корпусами и лонжеронами конструкции.Наиболее важно то, что лезвие представляет собой цельную конструкцию без клеевых соединений, которые могут ослабить и потенциально подвергнуть конструкцию растрескиванию, попаданию воды и ударам молнии. Таким способом изготавливаются лопасти длиной от 30 до 52 м.
Испанская компания Gamesa, имеющая заводы по производству лезвий в Эбенсбурге и Фэйрлесс-Хиллз, штат Пенсильвания, производит около 4500 лезвий в год. Компания является одним из двух ведущих поставщиков (другой — Vestas), использующих формование эпоксидного препрега. Согласно Emmanuel Garcia De La Pena, v.п. промышленных операций. По его словам, это обеспечивает постоянную толщину, лучшую ориентацию волокон и меньше слабых мест, что приводит к лучшим механическим характеристикам и меньшему весу, чем при вакуумной инфузии.
Менее крупный игрок в производстве лопастей — Knight & Carver, National City, Калифорния, бывший производитель лодок по индивидуальному заказу, который почти 10 лет назад превратился в специалиста по ремонту и производству ветряных лопастей. Компания нашла свою нишу на рынке замены лезвий, производя 25-метровые лезвия из эпоксидного препрега в Ховарде, С.D. По словам Гэри Канаби, директора по развитию бизнеса, уникальной особенностью является колпачок с пултрузионным лонжероном, обеспечивающий высокую прочность и жесткость.
Knight & Carver также изготовила 9-метровые лопасти для ветряной турбины мощностью 100 кВт, ныне не существующей в US Wind Power. Они были изготовлены из сложного винилового эфира для более быстрого отверждения посредством процесса формования цельного пузыря. В текущем проекте с Министерством энергетики США и Национальными лабораториями Sandia (Альбукерке, Нью-Мексико) Knight & Carver разработали 27-метровую лопасть, которая лучше работает при низких скоростях ветра, но не увеличивает нагрузку на турбину при сильном ветре.
БОЛЬШЕ ПРОИЗВОДСТВЕННЫХ МАТЕРИАЛОВ
Производители лезвий, пытающиеся удовлетворить растущий спрос, ищут новые материалы, которые помогут повысить общую производительность, сократить время цикла и сократить расходы. Например, новая система эпоксидных смол и отвердителей Airstone от Dow Epoxy Systems расширяет ассортимент Dow для ветровых лопастей, не ограничиваясь только смолами. По словам Бернда Хувела, глобального технологического лидера в области ветроэнергетики, компания рассчитывает расширить свою долю на рынке, предлагая системы, которые позволяют адаптировать состав смол к конкретным характеристикам лопастей.Новая линейка эпоксидных инфузионных материалов Airstone 780 E компании Dow обеспечивает увеличенный срок годности, более быстрое отверждение и улучшенное время цикла.
Hexion работает с клиентами над разработкой новых продуктов, которые уменьшают вес, улучшают механику и доставляют «больше лезвий в единицу времени», — говорит Лангемайер. Тем временем компания Huntsman Advanced Materials разрабатывает новые эпоксидные смолы, которые обеспечивают лучшую стойкость к растрескиванию и старению для более длинных лезвий. Эпоксидные смолы также являются основным клеем для склеивания половинок лезвий. Хантсман заявляет, что его новая усиленная система проста в обработке и обеспечивает повышенную устойчивость к старению и распространению трещин.
Поставщики полиэфиров и виниловых эфиров работают над новыми рецептурами с улучшенными механическими свойствами. По словам Билла Шрамма, директора по глобальному развитию бизнеса, в компании Reichhold Inc. новый сорт винилового эфира Dion обеспечивает на 10-15% большую устойчивость к усталости и большую общую вязкость для более длинных и легких лезвий.
Ashland Composite Polymers Div. поставляет полиэфиры Aropol G300 и M300 для LM Glasfiber и других производителей лезвий. Виниловый эфир Derakane 601-200 компании недавно получил сертификат Germanischer Lloyd в Германии, который контролирует мировые стандарты безопасности и производительности ветроэнергетических систем.Сообщается, что по физическим свойствам этот материал лучше полиэфира и приближается к свойствам эпоксидной смолы. Ключевым преимуществом перед эпоксидной смолой является более короткое время постотверждения. А новый полиэстер от AOC используется неизвестным производителем лезвий. Компания AOC отказалась предоставить дополнительную информацию.
Поставщики стекла отреагировали на конкуренцию из углеродного волокна в производстве более длинных и легких лезвий. OCV Reinforcements представила прямой ровинг WindStrand и трикотажное полотно на основе специального стекла, которое, как говорят, почти на 30% прочнее, на 15-20% жестче и на 8-10% легче, чем текущее E-стекло компании.Это дает производителям лезвий менее дорогостоящее решение, чем углеродное волокно, для лезвий длиной 40 м и более, по словам Уисдом Дзотси, американского лидера маркетинга. В эксклюзивном исполнении ведущий производитель лезвий использует WindStrand для вакуумной инфузии.
Усовершенствования химического состава и размеров привели к появлению более производительных изделий из стекла, таких как новый ровинг Hybon 2026 от PPG Industries, который имеет на 10% большую устойчивость к усталости, чем стандартные изделия. PPG также работает над более жесткими арматурами, которые заполняют пробел между стеклом E и более дорогим углеродным волокном.
Финская компания Ahlstrom Corp. (офис в США в Виндзоре, штат Коннектикут) запустила CombiFlow, специальную ткань из стекла E со слоем потока ПЭТ для более простой и быстрой инфузии смолы. ПЭТ зажат между двумя слоями стекла. Компания Ahlstrom также объявила о планах удвоить мощности для специальных укреплений в США к 2011 году. Мощности, предназначенные в первую очередь для ветроэнергетики, будут добавлены в два этапа в Бишопвилле, Южная Каролина
.БОЛЬШЕ, ЖЕСТЧЕ, ЛЕГЧЕ
Чтобы снизить стоимость энергии ветра, разработчики хотят максимизировать количество энергии ветра, которое они могут улавливать.Это стимулировало спрос на турбины с большей мощностью МВт и соответствующим увеличением длины лопаток. За последнее десятилетие средняя мощность ветряных турбин увеличилась вдвое, что привело к сокращению на 50% количества турбин и лопастей, необходимых для выработки определенного количества энергии. Средняя генерирующая мощность турбины увеличивается с 1,5 МВт до 2–2,5 МВт. В будущем нас ждут еще более крупные турбины мощностью 3 МВт и выше, особенно для использования на море. Сегодня самый крупный блок — это прототип морской турбины мощностью 7,5 МВт, разработанный Clipper Windpower Plc, Карпинтерия, Калифорния.Имеет лопасти от 50 до 60 метров.
Многие наблюдатели полагают, что для больших турбин потребуется углеродное волокно, чтобы обеспечить необходимую жесткость и легкий вес. Сегодня глобальное использование углеродного волокна в ветроэнергетике составляет всего от 10 до 12 миллионов фунтов в год по сравнению с более чем 200 миллионами фунтов стекла. Vestas и Gamesa — единственные компании высшего уровня, использующие углеродное волокно, в первую очередь, в конструкционных лонжеронах (центральный стержень) более длинных лопастей (40 м и выше). Углеродное волокно в основном используется в Европе, и его редко применяют со стеклом.
Углеродное волокно по цене от 10 до 13 долларов за фунт стоит в 15-20 раз больше, чем стекло E-glass. Таким образом, цель состоит в том, чтобы избирательно использовать углеродное волокно для обеспечения прочности и жесткости без больших затрат, — говорит Роб Клавонн, президент Toho Tenax America, производителя жгутов 24K.
При вакуумной инфузии углеродное волокно не может эффективно смачиваться, хотя более опытные производители лезвий научились преодолевать эту проблему. Следовательно, более дорогостоящее формование препрега является предпочтительным и наиболее эффективным методом использования углеродного волокна.В то же время углеродное волокно исторически страдает от проблем с ценой и доступностью. Однако производители углеродного волокна утверждают, что новые мощности сегодня в большей степени уравновешивают предложение. Zoltek Inc., ведущий поставщик углеродного волокна для энергии ветра, с 2005 года удваивает мощность своего завода в Венгрии каждый год, достигнув в этом году 26 миллионов фунтов. Zoltek продает паклю 50K под названием Panex 35 для использования в ветряных лопастях.
В зависимости от конструкции, экономичность углеродного волокна может быть благоприятной для лезвий длиной более 40 м, говорит Тим Маккарти, Zoltek v.п. маркетинга и продаж. И наоборот, другие источники указывают на оптимизированный дизайн и конструкцию, которые позволяют использовать E-стекло в более длинных лезвиях, таких как 61,5-метровый гигант LM Glasfiber. «Пройдет много времени, прежде чем углеродное волокно станет широко использоваться из-за его стоимости», — говорит Стисдал из Siemens, чья компания работает над 52-метровым лезвием, изготовленным из E-стекла.
Другой поставщик жгута углеродного волокна 50K — немецкая SGL Group. Компания придерживается стратегии дальнейшей интеграции, которая включает приобретение в 2007 году немецкого производителя препрегов Epo и недавнюю покупку 51% акций немецкой компании Abeking & Rasmussen Rotec GmbH Co., ведущий независимый производитель ветровых лопастей. SGL также принадлежит контрольный пакет акций производителя стеклоткани SGL Kumpers GmbH, Латен, Германия. SGL планирует удвоить объемы производства углеродного волокна до 24 миллионов фунтов к 2012 году.
ПРЕДПРЕГ ПРОДВИЖЕНИЯ
Повышение производительности также подчеркивает последние разработки в формовании препрега. Hexcel Composites Ltd. запустила новый эпоксидный препрег, который, как утверждается, сокращает время отверждения на 15-20%. Основным преимуществом HexPlyM19 является низкий риск неконтролируемого экзотермического воздействия на толстые секции.
Сообщается, чтоHexPly M19 уменьшает горячие точки и позволяет более агрессивно наращивать скорость для достижения максимальной температуры отверждения. Выдержка находится при более высокой температуре и более короткое время, чем с обычными препрегами. Более быстрое общее отверждение снижает затраты на пресс-форму до 10%, потому что можно использовать менее дорогие инструментальные смолы и покрытия, а также менее дорогую систему поддержки инструментов. По словам Хексел, срок службы пресс-формы также может быть увеличен.
Компания работает над системой препрега с улучшенным внешним видом поверхности для уменьшения чистовой обработки.Чтобы удовлетворить растущий спрос в США, Hexcel откроет новый завод по производству препрега для стекла в Колорадо во второй половине 2009 года.
Другой ведущий поставщик препрега, компания Gurit в Великобритании, специализируется на оптимизации содержания стекла и уменьшении пустот в отвержденных ламинатах. Чтобы решить проблемы с внешним видом поверхности, компания Gurit разработала Sprint IPT, грунтовочную пленку для литья под давлением, которая облегчает отделку и покраску. Кроме того, Gurit разработал препреги Sprint, который состоит из чередующихся слоев сухой ткани и эпоксидной пленки, обеспечивающих воздухопроницаемость и уменьшенное количество пустот.
АВТОМАТИЗАЦИЯ ВСТРЕЧАЕТСЯ
Небольшой испанский производитель ветряных турбин и лопастей разработал автоматизированный процесс производства лопастей, который, как сообщается, сокращает трудозатраты, сокращает время цикла на 75% и позволяет производить лопасти большей прочности. MTorres (офис в США в Санта-Ана, Калифорния) разработал запатентованный процесс вакуумной инфузии, который не накладывает ограничений на длину лезвия. Он наполняет форму эпоксидной смолой за один прием, в отличие от многократных инфузий в существующих системах, а также использует холодные формы для управления экзотермией.По словам Дэвида Чампы, генерального менеджера американского подразделения, в инфузионной системе есть специальная головка и средство для повышения клейкости, которое сначала добавляет эпоксидную смолу в небольших количествах для стабилизации укладки стекла.
Система «под ключ» требует всего пяти рабочих для запуска пяти станций укладки, упаковки в пакеты, вулканизации, соединения и покраски. Портальная система автоматизирует укладку стекла. Также имеется автоматическая упаковка в мешки, специальное приспособление для склеивания двух половин лезвия и подвижные формы с автономным приводом. Чампа описывает среду почти чистого помещения с обширными системами контроля температуры и роботизированными операциями отделки.Компания работает с ведущими производителями турбин в США и Европе и планирует коммерциализировать ее в следующем году в США. По словам Чампы, система обработки будет стоить от 5 до 6 миллионов долларов с двухлетней окупаемостью инвестиций.
В обширной исследовательской программе Upwind, финансируемой ЕС, участвуют более 40 специалистов по ветроэнергетике, которые изучат новые материалы и методы производства для больших лопастей от 70 до 120 м. Проект рассматривает натуральные материалы, такие как дерево и бамбук, а также целлюлозные волокна из конопли, льна и дерева.По словам Повла Брондстеда, руководителя исследовательских программ Национальной лаборатории устойчивой энергетики Рисоэ при Техническом университете Дании, они имеют такое же соотношение жесткости и веса, как стекло, и такую же прочность, но их трудно обрабатывать. Также исследуются термопласты, такие как ПЭТ и ПП, а также смолы на биологической основе.
Upwind также рассматривает новые решения для сборки лопастей, состоящих из нескольких частей. Также исследуются возможности улучшения управления процессами и автоматизации.
Энергия ветра в цифрах
По данным Американской ассоциации ветроэнергетики (AWEA), в настоящее время США являются мировым лидером в производстве электроэнергии с использованием энергии ветра. В то время как Германия по-прежнему имеет больше генерирующих мощностей (около 23000 МВт), США фактически производят больше электроэнергии с помощью ветра.
Во всем мире в 2007 году было установлено более 20 000 МВт ветровой энергии, в первую очередь в США, Китае и Испании. По данным Глобального совета по ветроэнергетике в Брюсселе, Бельгия, это на 31% больше, чем в 2006 году.
США сообщили о рекордных 5244 МВт, установленных в 2007 году, что более чем вдвое больше, чем в 2006 году, и это третий год подряд рекордного роста. Эта новая мощность будет производить 16 миллиардов киловатт-часов, чего достаточно для питания более 1,5 миллиона домов. Общая мощность ветроэнергетики в США выросла на 45% в 2007 году до 16,8 ГВт.
Американские ветряные электростанции будут производить около 48 миллиардов киловатт-часов ветровой энергии в 2008 году, что составляет чуть более 1% от общего объема электроэнергии в США, что эквивалентно 4.По данным AWEA, в среднем 5 миллионов домов в США. В период с 2002 по 2007 год средний темп роста в США составлял 29%.
Производство ножей и ковшей HPT
Производство лопаток высокого давления для авиационных и наземных газотурбинных двигателей Hi-Tek Manufacturing является одной из наших сильных сторон. Мы работаем на большом производственном предприятии площадью около 125 000 квадратных футов, на котором размещается большое количество высокоточного производственного оборудования, а также полностью оборудованная лаборатория обеспечения качества.У нас есть команда технически образованных профессионалов в области производства, которые привносят энтузиазм и твердую трудовую этику в каждый проект, чтобы гарантировать, что мы предоставляем нашим клиентам самые качественные и экономически эффективные решения.
Мы производим лопатки турбин в соответствии с четко структурированным и контролируемым процессом. Стратегии бережливого производства регулируют весь производственный цикл, чтобы гарантировать, что операции выполняются организованно, эффективно и с учетом качества. Изготовленные из жаропрочных суперсплавов, мы производим самые сложные конструкции турбинных лопаток с геометрически сложными внутренними охлаждающими каналами и схемами охлаждающих отверстий.Наши инженеры используют сложные системы CAD / CAM, наши специалисты по инструментам и штампам проектируют и создают индивидуальные приспособления и инструменты, а наши техники используют самое современное станочное оборудование, чтобы гарантировать, что наши продукты соответствуют высочайшим стандартам качества.
На многих этапах производственного цикла, а также перед упаковкой и отгрузкой мы проводим многочисленные испытания и проверки для проверки качества материала и конструкции лезвия. КИМ и оптический контроль гарантируют, что все размерные аспекты соответствуют проектным спецификациям, в то время как такие процессы, как проникающий контроль красителя и рентгенография, подтверждают, что лопатка турбины не имеет трещин или дефектов поверхности.У нас есть несколько полностью откалиброванных стоек и стендов для измерения расхода воздуха, чтобы убедиться, что продукция поддерживает точные значения расхода воздуха.
Благодаря нашим передовым методам производства наши турбинные лопатки демонстрируют исключительный уровень качества. Мы поставляем лопасти ступеней 1, 2, 3 и 4 основным отечественным и международным производителям газовых турбин и планеров. Если вы хотите узнать больше о наших возможностях производства турбинных лопаток, свяжитесь с нами сегодня.
Запрос ценПроизводственные мощности турбинных лопаток
- Название продукта
- Лезвия и ковши HPT
- Возможности высокоточной обработки с ЧПУ
Прикладные / Процессы - Первичный: Среднее:
- Штамповка электродов для сверления отверстий EDM
- Удаление заусенцев
- Обезжиривание и очистка паром
- Маркировка деталей
- Оборудование, используемое для производства деталей
- 3-, 4- или 5-осевой шлифовальный станок с непрерывной подачей
5-осевое шлифование CBN
5-осевой горизонтальный и вертикальный фрезерный центр
6-осевой электроэрозионный станок с быстрым отверстием
3-, 4- или 5-осевой плунжер / грузило EDM
5-осевой YAG-лазер
Hi-Tek спроектировал и изготовил инструменты и приспособления для всех процессов
- Используемый материал
- Высокотемпературные суперсплавы
- Испытания / проверка в процессе выполнения
- Испытания воздушного потока — калиброванные цифровые звуковые сопла
Оптический контроль с ЧПУ
Радиографический контроль (рентген)
Инспекция флуоресцентных пенетрантов (FPI)
Координатно-измерительная машина (КИМ)
Hard Gaging
Дополнительная информация
- Промышленность
- Авиационные турбины — коммерческие и военные
Судовые турбины
Энергетический турбинный двигатель
- Детали
- Этапы 1, 2, 3, 4 лезвия / ковши
- Срок поставки / выполнения работ
- Товар поставляется в комплекте с двигателем — в зависимости от размера и объема работ: 4-8 недель после получения заказа и материала.
- Место доставки
- FOB Место происхождения
- Соответствие стандартам
- ISO 9001: 2008
AS 9100
NADCAP
AC7116 Нетрадиционная обработка
AC7114 Неразрушающий контроль
Форматы чертежей — Unigraphics (PRT), STEP, IGES
Современные термопласты для производства лопастей ветряных турбин | Передовые производственные исследования
Отмеченная наградами R&D 100 технология системы термопластической смолы была разработана с партнер Arkema Inc.в образовании и технологиях производства композитов (CoMET) Средство.
Подавляющее большинство лопастей ветряных турбин в Соединенных Штатах в конечном итоге попадают в свалки в конце своего жизненного цикла, что создает как экологические проблемы, так и финансовые убытки из-за отсутствия восстановления материалов. И поскольку энергия ветра продолжается расширится, то же самое будет и с грудой списанных лопастей, оставшихся после него.
Поистине устойчивая, рентабельная революция в области возобновляемых источников энергии уже близка, благодаря новаторским исследованиям термопластической смолы для лопастей ветряных турбин NREL. Наша уникальная технология подорвет производство турбин в ветроэнергетике. процесс, потенциально позволяющий перерабатывать лезвия, которые больше не перестают быть полезными на свалке.
Термопластические смолы в сочетании с методами термической сварки, впервые разработанными NREL и партнеров, предлагают потенциал для более сильных, менее дорогих и более длинных ветряных турбин лезвия, увеличивая захват энергии, снижая затраты на энергию и транспортировку, а также повышение надежности лопастей — критически важное значение для развития рынка ветроэнергетики.
Эти безопасные для соленой воды лезвия из термопласта также служат отличным ориентиром для морской энергетики. успеха, обеспечивая эту развивающуюся область надежными и экономичными материалами на котором отплыть.
Нет необходимости в новых инструментах или производственном оборудовании.
Термопласты Elium могут заменить эпоксидную смолу.
Больше никаких захоронений клинков.
Термопласты и термическая сварка упрощают переработку вторичного сырья.
Чемпион выносливости.
Улучшенная структурная амортизация лопаток из термопласта приводит к улучшенным усталостным характеристикам и долговечность турбины.
Развитие обычных блейд-серверов
Использование множества фундаментальных научных исследований, разработок и деятельность по валидации и сотрудничество с отраслевыми партнерами, такими как General Electric и TPI Composites Inc, NREL и Arkema Inc.разработали революционный, разрушительный инновация для решения завтрашних проблем ветроэнергетики — термопластичная смола система для лопастей ветряных турбин.
Термопласты могут произвести революцию в ветроэнергетике, представив новая эра материалов нового поколения, технологий изготовления, испытаний и сварки. Смола Arkema Elium представляет собой двухкомпонентный жидкий реактивный термопласт, который смешивается друг с другом. преимущества термореактивных и термопластичных смол.
Производственные результаты: создание лезвий
Всего несколько лет назад демонстрация этого захватывающий, новый материал. Наша команда провела количественную оценку и продемонстрировала, как лезвия из термопласта разработан с использованием термопластической смолы Arkema Elium в сочетании с термической сваркой, потенциально могут быть переработаны по окончании срока службы, что сокращает время, затраты и энергию занимается производством.
Фотографии изготовления секции лопасти: сердечник из бальзового лонжерона и лонжерон (слева), второй слой. стекловолокна и проточной среды (в центре) и готового продукта (справа). Фото Райана Бича, NREL
Чтобы протестировать эту революционную термопластичную систему, исследователи NREL впервые построили лопатку турбины длиной 9 м для демонстрации технологичности, а затем лопатку длиной 13 м, которую они подвергнуть испытанию, проверяя лезвие на прочность и другие рабочие характеристики.
9-метровая ветряная лопасть, изготовленная на заводе NREL CoMET, показала впечатляющие результаты. например, снижение затрат на оборудование и время цикла.
Строительство 13-метровой лопасти из термопласта на заводе NREL CoMET. Фото Райана Бич, NREL
Затем команда построила 13-метровое лезвие, задействовав передовые лаборатории структурной проверки в кампусе Flatirons для его тестирования.
Было обнаружено, что лезвие из термопласта имело ту же жесткость, что и лезвие из эпоксидной смолы. Это смоделировал 20 лет использования лезвия для оценки долговечности. Термопласт Elium лезвие показало в пять-семь раз более высокий уровень структурного демпфирования, чем эпоксидная смола. лезвие. Эти результаты показывают, что, используя лезвия из термопласта, мы также можем увеличить срок службы всей турбины.
В нем надолго: NREL смоделировал 20 лет использования лезвия из термопласта для обеспечения долговечности. Фото Райана Бич, NRELУдар
Эти лезвия из термопласта нового поколения являются залогом успеха обычного бизнеса. лезвия из эпоксидной смолы и превращают их в экологически чистые и экономичные лезвия будущего.Исследователи обнаружили, что процесс и материал демонстрируют потенциал для:
- Возможность вторичной переработки: Лезвия из термопласта Elium обладают потенциалом вторичной переработки, сокращая как затраты на захоронение и захоронение отходов.
- Термическая сварка: Материалы можно термически соединять, что позволяет производить потенциально более прочные и более легкие лезвия.
- Производство на месте: Лезвия могут быть изготовлены на месте, что позволяет разрабатывать более крупные лезвия за большие деньги. снижение транспортных расходов.
- Простота ремонта: В отличие от лезвий из эпоксидной смолы, требующих традиционного ремонта шлифованием, термопласты можно подогреть сразу после ремонта и изменить форму.
- Морская энергетика: Термопластический материал работает лучше, чем традиционные материалы в морской воде, поэтому этот материал кардинально изменил правила игры в морской энергетике.
- Снижение капитальных затрат на оборудование , связанных с производством лопастей, до 30%
- Уменьшение критического времени цикла во время производства до 20%.
Технология термической сварки NREL в сочетании с системой смол Arkema была отмечена специальной наградой 2020 года от R&D 100 как «революционная технология». Посмотрите видео, чтобы узнать подробнее об этой революционной инновации в области ветроэнергетики и гидроэнергетики.
Возможности
Производство композитов
Средство CoMET предоставляет широкий спектр возможностей, в том числе:
- Быстрое прототипирование новых материалов для лезвий и методов производства
- Инструменты и приспособления для полномасштабных компонентов лопасти (корень, крышка лонжерона, наконечник, перегородка)
- Инфузия, пултрузия, препрег, RTM, ручная укладка (мелкие детали)
- Полиэстер, винилэфир, эпоксидная смола, термопласт / стекловолокно, углеродное волокно
- Комплексное оборудование для производства композитов (смесители, вакуум, дозаторы)
- Формовка, сборка, приклеивание и отделка
- Термическая сварка
- Сегментированная трехмерная печатная оснастка
- Быстрая неразрушающая оценка больших площадей
- Моделирование и производственное моделирование
- Панели, талоны на испытания материалов и компоненты
- Структурная оценка купонов, компонентов и соединений
- Промышленная роботизированная платформа для исследований в области автоматизации
- Переработка композитов и характеристика материалов
- Развитие и обучение персонала для композитной промышленности.
Узнайте больше о CoMET Facility и ее многочисленных возможностях.
Возможности структурной проверки
Исследователи проводят полномасштабную структурную проверку лопаток из термопласта на заводе Лаборатории структурной проверки NREL.
Публикации
Структурная проверка лопатки ветряной турбины из термопластичного композита со сравнением на лезвие из термореактивного композита, Renewable Energy (2021)
Соединение лопастей ветряных турбин из термопластичного композитного материала: характеристика связи внахлестку, Возобновляемые источники энергии (2019)
Переработка стекловолоконных термопластических композитов из лопастей ветряных турбин, Журнал экологически чистого производства (2019)
Технико-экономический анализ лопасти ветряной турбины из термопластической смолы мощностью в мегаватт, Возобновляемые источники энергии (2019)
Производство и определение характеристик изгиба термопластичного ветра, вступающего в реакцию инфузии Компоненты лопаток турбины, Применяемые композитные материалы (2019)
Инновационные и пригодные для вторичной переработки лопасти ветряных турбин из термопласта, Информационный бюллетень NREL (2019)
Производство 9-метровой лопасти ветряной турбины из термопластичного композитного материала , 32-я техническая конференция Американского общества композитов (2018)
Партнеры
NREL сотрудничает с промышленностью, академическими кругами и национальными лабораториями.В промышленном масштабе рабочее пространство, предназначенное для приема рабочей силы и технологий в композитных материалах промышленности, объект CoMET оборудован для поддержки таких крупномасштабных совместных усилий.
Контакты
Дерек Берри
[email protected]303-384-7372
Производство лопастей ветряных турбин — новые продукты идут в ногу с ростом масштаба
Ветряные турбины Vestas мощностью 2 МВт вырабатывают электроэнергию на ветряной электростанции у побережья Уэльса в Великобритании.(Изображение любезно предоставлено Vestas Wind Systems.) Корневая часть лопастей на заводе по производству лопастей Gamesa в Бургосе, Испания, просверлена и готова к прикручиванию к ступице ротора. (Изображение любезно предоставлено Gamesa.) Ветряные лопасти готовы к окончательной отделке на заводе по производству лопастей LM Wind Power в Китае. (Изображение любезно предоставлено LM Wind Power.) Система MAG Rapid Material Placement System автоматически распыляет покрытия в формы, разрезает и укладывает материалы из стекла и углеродного волокна. (Изображение любезно предоставлено MAG IAS.) Лопасть ветряной турбины, размещенная в автоматизированном покрасочном цехе на предприятии по производству лопастей MFG.(Изображение любезно предоставлено MFG.) Смола равномерно пропитывается толстым коническим слоем преформ RapidRoot 3D. (Изображение любезно предоставлено 3TEX.)Стандартные ветряные турбины для коммунальных предприятий, предназначенные для выработки электроэнергии 1-3 МВт, оснащены тремя лопастями длиной от 30 до 50 м (100–165 футов). Изготовление клинков трудоемкое. Наружные многослойные оболочки поддерживаются колпаком лонжерона или основным лонжероном, служащим центральным стержнем лопасти. Армирующие элементы обычно состоят из 70-75% E-стекла по весу, пропитанного эпоксидной или ненасыщенной полиэфирной смолой.Лезвия обычно формуются пополам, а затем соединяются с помощью эпоксидного клея.
Армирование стекловолокном обычно укладывается в форму в виде сухих штабелей вручную. Бальза, структурный пенопласт и специальные трехмерные материалы используются в качестве сердечников в конструкции лопастей, чтобы поддерживать внешние оболочки лопастей. Некоторые производители используют эпоксидные препреги из E-стекла, углеродного волокна и гибридов, особенно при производстве более длинных лезвий.
тонн композитов в небе
Крупнейшим в мире производителем ветряных турбин является датская компания Vestas Wind Systems.Одна лопасть длиной 80 м, прикрепленная болтами к ступице морской ветряной турбины мощностью 7 МВт, весит 35 тонн. Сборка с тремя лопастями имеет диаметр 164 м (538 футов) и поднимает в воздух множество композитов из армированного волокном пластика (FRP).
Vestas использует углеродные композиты для изготовления лопастей, что позволяет им быть тоньше, жестче и легче стекловолокна. Это снижает нагрузку на турбину и делает ее более эффективной.
Испанская компания Gamesa, еще один лидер мирового рынка, также использует углепластик / эпоксидный препрег в своих самых передовых турбинах.Турбина Gamesa мощностью 4,5 МВт, которую называют самой мощной ветряной турбиной для наземного рынка, возвышается на высоте 120 м (394 фута). Он оснащен уникальными лезвиями Innoblade® длиной 62,5 м (205 футов). Они сегментированы, что позволяет собирать их в полевых условиях.
Крупнейшим производителем лопастей для ветряных турбин в мире является датская компания LM Wind Power. Имея 12 производственных мощностей на трех континентах, компания недавно произвела свои рекордные по длине лопасти — 73,5 м (271 фут) для растущего европейского морского ветроэнергетического рынка, используя стекло E и полиэфирную смолу в смоле для формования с вакуумным переносом смолы (VARTM). процесс настаивания.Лопасти предназначены для установки на ветряную турбину мощностью 6 МВт, произведенную французской компанией Alstom.
Компания LM Wind Power работает со стекловолокном и полиэстером для производства лопастей для ветряных турбин с 1978 года, «расширяя возможности» материалов для достижения наилучшего возможного баланса между ценой и характеристиками, сообщает компания. LM активно вовлекает своих поставщиков в производственные процессы, чтобы оптимизировать смолу и арматуру для вакуумной инфузии.
В результате, по заявлению производителя, получается очень прочный, однородный ламинат без пузырьков воздуха и быстрое затвердевание, что позволило сократить время производства на несколько часов.При армирующих волокнах основное внимание уделяется прочности на разрыв, общей структуре плетения и структуре стекловолоконных матов, а также химическому составу волокна. Фибровые маты, которые использует компания, проще в обращении и дешевле препрегов, отмечает производитель.
«Эпоксидная смола в три раза дороже полиэстера и требует значительно более дорогостоящего производственного процесса, включая нагрев форм», — отмечает LM. «Вместо этого мы решили сосредоточиться на оптимизации более дешевой технологии, чтобы снизить общую стоимость энергии ветра. сохраняя такие же хорошие рабочие характеристики.”
Одним из производителей систем полиэфирных смол является швейцарская компания DSM Composite Resins. Утверждается, что его полиэфирные смолы Synolite ™ обладают улучшенными характеристиками по сравнению с другими традиционными ненасыщенными полиэфирными и эпоксидными смолами. По словам DSM, Synolite 1790-G-3 хорошо подходит для вакуумной инфузии лопастей ветряных турбин, демонстрируя улучшенное смачивание армированного стекла и обеспечивая более быстрые производственные циклы и отверждение при комнатной температуре. Сообщается также, что смола демонстрирует очень низкое экзотермическое тепловыделение в толстых слоистых материалах для более низкого механического напряжения в лезвии и более длительного срока службы формы.
Системы эпоксидных смол
Компания Dow Formulated Systems разработала эпоксидные смолы и отвердители Airstone ™ с пониженным пиковым экзотермическим эффектом во время отверждения для производства лопастей. Утверждается, что смола для инфузии Airstone 780E обеспечивает увеличенный срок жизнеспособности, быстрое отверждение и сокращение времени цикла. Производители могут контролировать свойства отверждения смолы, оптимизируя время цикла без ущерба для прочности и целостности конструкции лезвия, говорит Dow, которая планирует сделать инфузионные системы Airstone коммерчески доступными в 2012 году.
Momentive, образованная в 2010 году в результате слияния компаний Momentive Performance Chemicals и Hexion Specialty Chemicals, предлагает эпоксидные системы Epikote ™ и Epikure ™ для композитных материалов ветряных турбин. Компания заявляет, что они отличаются простотой обработки, превосходной вязкостью разрушения, хорошими пропитывающими свойствами для волокон и выдающейся термической стабильностью. Эпоксидные системы Momentive доступны в рецептурах, адаптированных для различных процессов, включая введение смолы RTM и VARTM, ручную укладку и предварительную обработку.
Sika Deutschland GmbH предлагает эпоксидную смолу Biresin CR83 для производства ветровых лопастей. Считается, что смола хорошо подходит для этого применения из-за ее низкой вязкости, хороших характеристик смачивания и переменной жизнеспособности. В ходе испытаний смола наполняла слой волокон вдвое быстрее, чем в типичной конкурентной системе инфузии, и обеспечивала 100% смачивание волокон, сообщает Sika. Доступны три отвердителя с разной реакционной способностью, позволяющие варьировать жизнеспособность.
Тайваньская компания Swancor разработала систему эпоксидной смолы SW2511-1 для обработки ветряных лопастей методом VARTM.Утверждается, что смола обладает низкой вязкостью, регулируемым временем гелеобразования и низкими экзотермическими температурами, реагируя при комнатной температуре без дополнительного давления. Время гелеобразования для SW2511-1 составляет 9-10 часов, по сравнению с 6-7 часами для традиционных эпоксидных систем, в то время как его экзотермическая пиковая температура 35-40 ° C сравнима с 50-70 ° C для других эпоксидных систем, сообщает Swancor.
Gurit предлагает ряд композитных продуктов для производства ветровых лопастей, включая систему инфузии эпоксидной смолы PRIME ™ 20LV. По словам Гурита, это обеспечивает значительно более низкую вязкость и более длительное время работы, чем традиционные эпоксидные смолы, отмечая, что смола идеально подходит для проплавления очень больших деталей со сложным армированием за одну операцию.Утверждается, что система PRIME поддерживает исключительно низкие экзотермические характеристики, предотвращает преждевременное гелеобразование на толстых участках и увеличивает срок службы пресс-форм. Он доступен с рядом отвердителей для контроля рабочего времени и скорости отверждения.
Компания Materia из Калифорнии разработала Proxima ™, запатентованную систему термореактивных смол в качестве альтернативы эпоксидным смолам в производстве ветровых лопастей. При разработке использовалась технология катализатора метатезиса. Метатезис позволяет синтезировать химические соединения с большей эффективностью в менее жестких условиях реакции и с уменьшенным количеством побочных продуктов, сообщает компания.Утверждается, что смола Proxima обеспечивает большую прочность, меньший вес и меньший углеродный след при более низкой стоимости, чем эпоксидные системы, используемые для производства ветряных лопастей. По заявлению Materia, его более низкая вязкость обеспечивает более высокую скорость инфузии, чем традиционные смолы.
Сложный виниловый эфир для лезвий
AOC производит ряд смол для закрытых форм для композитов ветровых лопастей, в том числе виниловый эфир на основе бисфенола А на основе эпоксидной смолы, изофталевый и ортофталевый полиэфир, а также полиэстер общего назначения. Смолы разработаны с учетом ряда требований к обработке, производительности и стоимости.Ненасыщенный полиэфир общего назначения, серия R920-E, представляет собой высококачественную предварительно промотированную смолу для быстрого смачивания волокон и скорости инфузии. Высокоэффективная винилэфирная смола с высоким удлинением в серии R013-A обеспечивает прочность эпоксидной смолы и время цикла полиэфира, в то время как серия R015-G представляет собой высокореактивную винилэфирную смолу для максимальной прочности и жесткости, обеспечивая быстрое время инфузии, отмечает AOC.
Компания DSM разработала ряд смол на основе сложного винилового эфира с низкой вязкостью для производства лопастей ветряных турбин.Утверждается, что в сочетании со стекловолокном с надлежащим размером, он обеспечивает, по крайней мере, те же механические характеристики, что и системы на основе эпоксидной смолы. Смола обеспечивает быструю продолжительность цикла и может быть отверждена обычными низкоактивными пероксидами MEK, отмечает DSM.
Эпоксидно-винилэфирная смолаDerakane ™ 601-200 от Ashland Performance Materials сокращает время цикла на 25% по сравнению с системами на основе эпоксидных смол при инфузионной обработке ветряных лопастей. По словам Ашленда, смола сокращает разрыв между характеристиками и ценой между дешевыми ненасыщенными полиэфирными смолами и дорогими эпоксидными смолами.Компания заявляет, что Derakane 601-200 затвердевает намного быстрее, чем прямая эпоксидная смола, и может обеспечить экономию затрат на 25-30% на одно лезвие по сравнению с эпоксидными системами.
Reichhold предлагает предварительно продвинутую бисфенол-эпоксидную винилэфирную смолу для производства ветровых лопастей в серии Dion® Impact 9102-75. Он разработан для обеспечения пониженной вязкости и улучшенного отверждения для повышения производительности при вливании больших структурных усиленных композитных ветровых лопастей. Также от Reichhold доступна серия Polylite® 32850-00, ортофталевая ненасыщенная полиэфирная смола, предварительно промотированная и составленная для обеспечения пониженной вязкости и улучшенного отверждения для вливания больших ветряных лопастей.
Новые ПУ системы Bayer
Утверждается, что новая композитная технология на основе полиуретана (PU), разработанная Bayer MaterialScience LLC, значительно улучшает усталостную вязкость и трещиностойкость по сравнению с системами на основе эпоксидной смолы, используемыми при производстве более длинных ветровых лопастей. В материале используется технология армирования углеродными нанотрубками Baytubes®, которая улучшает трещиностойкость на 48%, что вдвое больше, чем у эпоксидной смолы.
Отрасль ветроэнергетики представляет большие возможности роста для поставщиков композитных материалов и производителей ветряных турбин.Исследователи рынка Lucintel прогнозируют, что к 2014 году мировой рынок композитных материалов для производства ветряных турбин достигнет 3,95 миллиарда долларов США. Ожидается, что мировой рынок ветроэнергетики будет расти в среднем на 14% в год с точки зрения ввода новых мощностей в следующие пять лет, прогнозирует Lucintel в новом обзоре рынка. Ветроэнергетика США была лидером в мире по ежегодному приросту ветроэнергетических мощностей с 2005 по 2008 год, но с тех пор Китай опередил США и превратился в крупнейший рынок ветроэнергетических мощностей, говорит Lucintel.И стремление к альтернативному производству электроэнергии продолжается повсюду. Строительство крупнейшей в мире морской ветряной электростанции у побережья Южной Кореи планируется завершить в 2016 году. Ожидается, что композиты из углеродного волокна будут играть более важную роль в производстве ветровых лопастей. По данным Lux Research, в США ветряная энергия, как ожидается, станет более крупным рынком для углеродного волокна и других современных композитных материалов, даже чем для авиакосмической отрасли.США и Китай останутся главными рынками для продаж ветряных турбин до 2020 года, говорится в новом исследовании SBI Energy. |
Новый композитный материал также продемонстрировал превосходные характеристики обработки и обращения, что может снизить общие производственные затраты на целых 16%, добавляет Байер. Разработка финансировалась Bayer, Министерством энергетики США и компаниями по производству стекловолокна (MFG) в рамках партнерства государственного и частного секторов.В компании отмечают, что Bayer работает над производством, тестированием и сертификацией полномасштабных прототипов лопастей в сотрудничестве с экспертами в области ветроэнергетики.
Исследователи Bayer и MFG сравнивали эксплуатационные характеристики полиуретановых систем для вливания смолы Baydur® компании Bayer с характеристиками композитов на основе эпоксидной смолы и сложного винилового эфира для ветряных лопастей. В то время как другие полиуретановые системы разработаны для обеспечения высокой производительности и быстрого гелеобразования / быстрого извлечения из формы, системы Bayer предназначены для обеспечения более низкой вязкости и более длительного времени гелеобразования, необходимых для формования очень больших ветряных лопастей.Результаты испытаний показывают, что новые системы на основе полиуретана превзошли образцы эпоксидной смолы и сложного винилового эфира при испытании на усталость при растяжении, вязкости при межслойном разрушении и испытании на рост усталостной трещины.
Технология препрега
Препрегот Gurit доступен в нескольких сериях. Препрег WE91-1, который входит в линейку препрегов WE и WT, представляет собой эпоксидный препрег без диурона с высокой текучестью, хорошо подходящий для изготовления толстых профилей. Препреги можно отверждать при температуре до 85 ° C или с более быстрым (55 минут) отверждением при 120 ° C.Препреги для однонаправленного (UD) стекла доступны в широком диапазоне плотности стекловолокна E. Также доступен ряд препрегов из углеродного волокна, которые отлично подходят там, где требуются высокие механические свойства. Кроме того, Gurit производит однонаправленный препрег SparPreg ™ со стекловолокном или углеродным волокном для производства лезвий качества SPRINT®.
Hexcel, еще один глобальный поставщик материалов для рынка ветроэнергетики, производит эпоксидные / углеродные волокна и препреги из UD-стекла. Углеродный препрег может быть экономичным вариантом для лезвий очень большого диаметра, говорит производитель, поскольку для достижения такой же прочности требуется меньше материала, чем у стекла.Гибридные армированные стеклом и углеродом материалы также доступны от Hexcel, который управляет шестью заводами по производству препрегов по всему миру. В препрегах используются эпоксидные смолы HexPly® M9.6G и M19G. По словам Хексел, M9G затвердевает на 15-20% быстрее, сохраняя при этом те же манипуляции и механические свойства.
Компания также поставляет системы на основе эпоксидной смолы HexPly M9F для производства ветровых лопастей. Смолы предназначены для обработки при низком давлении и допускают диапазон температур от 85 ° C до 150 ° C.HexPly M11 и M11.5, оба без диурона, что дает дополнительные экологические преимущества, были разработаны для процессов упаковки в мешки с низким вакуумом и быстрых циклов отверждения — 3,6 часа при 80 ° C или 8,7 часа при 75 ° C.
Новое подкрепление
Компания MFG, ведущий контрактный производитель компонентов ветряных турбин в Северной Америке, недавно отгрузила 1000-й комплект лопастей длиной 37 м (121 фут) для 1.Турбины мощностью 5 МВт с завода в Техасе. MFG производит лопасти длиной до 40 м, а также другие ветровые компоненты на заводах в пяти местах. По словам Гэри Канаби, директора по продажам ветроэнергетики MFG, компания планирует начать производство 50-метровых лопастей в 2012 году. «Некоторые производители используют композиты из углеродного волокна в длинных лопастях, которые требуют более высокой прочности и меньшего веса», — говорит он, отмечая, что MFG в настоящее время не использует углеродное волокно в лопастях, но может в будущем.«Я думаю, что тенденция состоит в том, чтобы использовать больше углеродных композитов в более длинных лопастях, чтобы соответствовать повышенным нагрузкам». Компания производит лопасти из стеклопластика, пенопласта и эпоксидных смол, как настойных, так и стандартных марок. По словам Канаби, на заводе по комплектации возле завода по производству лезвий в Гейнсвилле, штат Техас, арматура предварительно нарезается и упаковывается в комплекты в порядке, в котором они будут помещены в форму. Изготовление лезвия занимает четыре дня, начиная с 24-часового цикла формования, чтобы изготовить половинки корпуса лезвия и скрепить их вместе.На второй день выполняется вторичная склейка, обрезка и сверление. Собранные лезвия грунтуются и окрашиваются на третий день и готовятся к отправке на четвертый. Для резки и просверливания корневого конца используется автоматическое оборудование. «Покраска производится с помощью автоматического распылителя», — отмечает Канаби. MFG также поставляет запасные и сменные композитные детали для ветряных турбин, проводит проверки и предлагает ремонт и техническое обслуживание своей сервисной компанией WES.Он добавляет, что большая часть работы выполняется на вышке на платформах, чтобы избежать больших затрат на снятие лопастей и других компонентов с ветряной турбины для обслуживания. |
Компания 3B — The Fiberglass Company представила новую линейку армирующих волокон, разработанных для обеспечения оптимальных характеристик при производстве лопастей ветряных турбин. Каждый продукт разработан для конкретных систем смол. Advantex SE2020 — это первый продукт в этой серии, который представляет собой односторонний ровинг, специально разработанный для систем эпоксидных полимеров, используемых в процессах инфузии смолы или препрега.
«В компании 3B мы фокусируемся на понимании потребностей производителей ветроэнергетики, работая рука об руку с дизайнерами, ткачами и, в конечном итоге, с производителями лопаток турбин», — заявляет компания. «Сотрудничество со всей цепочкой создания стоимости позволяет нам чтобы вывести на рынок новый эталонный ровинг, который еще больше расширит возможности конструкции лезвий из стекловолоконного композитного материала ».
По сравнению с обычными материалами, новый ровинг Advantex SE2020 обеспечивает лучшее смачивание, обеспечивает более стабильное качество ламината и улучшенную адгезию полимерной матрицы, что обеспечивает более высокую прочность на сдвиг и большую прочность между волокнами, добавляет 3B.
(Для получения дополнительной информации о деятельности 3B на рынке ветроэнергетики и ее новом армированном стекле для производства лопастей ветряных турбин, Advantex SE2020, прочитайте интервью Reinforced Plastics с Онуром Токгозом, руководителем глобального бизнеса ветроэнергетики в 3B.)
Новая система пенопласта для ветряных лопастей, COMPAXX ™ 700, была недавно представлена компанией Dow Formulated Systems. Этот продукт является первым в линейке новых материалов сердечника, разработанных, чтобы помочь производителям продлить срок службы лезвий за счет создания высокоэффективных композитных материалов типа «сэндвич».Согласно Dow, обширные усталостные испытания сэндвич-панелей показали, что COMPAXX 700 демонстрирует долговременные динамические характеристики и свойства прочности на сдвиг, что позволяет получать легкие композиты с превосходной механической прочностью и сопротивлением усталости. Эти свойства в сочетании с прочностью на отслаивание, примерно в три раза превышающей историческую справку материала сердечника поливинилхлорида (ПВХ) 60 кг / м 3 , «создают тесное соединение сердечника с кожей, необходимое для обеспечения долговечности лезвия», — отмечает Dow
Продукт имеет определенную шероховатость и бороздки на поверхности, которые помогают достичь отличных характеристик склеивания.Кроме того, COMPAXX 700 обеспечивает высокую стабильность между запусками, что приводит к предсказуемым механическим свойствам, которые инженеры-строители могут использовать для создания более точных лопастей, добавляет компания.
Новая система COMPAXX теперь доступна во всем мире в коммерческих объемах.
PPG Industries производит ровинг из стекловолокна прямого действия Hybon® 2026, который, как утверждается, хорошо подходит для ветряных лопастей, на предприятиях в США, Великобритании и Китае. Ровинг разработан для обеспечения высоких механических характеристик, необходимых для критических конструктивных решений, а также преимуществ при производстве ножей.Армирование также обеспечивает отличную адгезию в различных системах смол, высокую прочность на разрыв и усталостные характеристики, необходимые для применения в ветряных лопастях с высокими требованиями, отмечает PPG.
Армированный волокном композитный материал сердечника для сэндвич-конструкции ветряных лопастей можно приобрести у Webcore Technologies. TYCOR® W5 — новейший продукт в линейке материалов для сердцевины W. Усиление из стекловолокна E в сочетании с пеной низкой плотности создает конструктивную архитектуру для вакуумной инфузии лезвий.По словам представителей компании, TYCOR экономит около 454 кг на лезвие по сравнению с сердечником из бальзы, что позволяет изготавливать более длинные лезвия без перехода на более дорогостоящую арматуру. Один заказчик реализовал 9% -ное сокращение общей стоимости материалов благодаря объединенной экономии сердцевины и смолы, добавляет Webcore.
Автоматизация производства
Система быстрого размещения материалов (RMPS) с ЧПУ от MAG IAS, расположенная в Кентукки, США, предлагает интегрированные производственные возможности для производства лопастей ветряных турбин.Система RMPS состоит из портальной системы с многоосевыми концевыми эффекторами, способными распылять покрытия в форме, распределять армирующие материалы и автоматически наносить клеи.
Толстая корневая часть ветряной лопасти — конец, который крепится болтами к ступице ротора ветряной турбины — представляет собой технологические проблемы, связанные с множеством слоев материала, используемого для создания композитного материала — 100 или более слоев тонкой ткани, которая может морщины во время удаления массы.Корневые части больших лезвий стали настолько толстыми, что переработчики обычно формуют их отдельно от лезвия, по частям, а затем связывают их вместе во время вторичной операции. Чтобы облегчить изготовление толстой корневой части и избежать распространенных проблем, связанных с ее завариванием, компания 3TEX, Северная Каролина, США, производитель тканей и армирующих материалов для композитов, разработала преформы RapidRoot 3D ™. Они производятся из слоев плотно сплетенной, более толстой ткани из стекла E, нарезанной на все более длинные отрезки, чтобы обеспечить конусность, необходимую для корневой части. «RapidRoot был разработан специально для решения трех основных проблем, с которыми сталкиваются процессоры при внедрении корневых разделов», — говорит Дон Вигент, технический менеджер по продуктам, 3TEX. «Это позволяет очень быстро разместить большое количество волокон; морщины избегаются, потому что слои плотные и жесткие; а проточные каналы из вплетенной смолы обеспечивают быстрое и тщательное смачивание всех слоев », — поясняет он. «Нет никаких опасений по поводу невидимых сухих пятен под влажным материалом.Для быстрого и полного смачивания не требуется никаких инфузионных сред или водопровода. Речь идет о масштабировании армирования волокном, чтобы оно соответствовало масштабу детали », — добавляет он. Компания также предлагает специальные ткани и другие преформы для композитных материалов ветровых лопастей, в том числе 3TEX UniGirder 3D Spar Caps, канатоподобные FilletBraid ™ для заполнения зазоров и углов при укладке лопастей, а также тканые соединительные элементы в форме формируемых стыков. Также доступны запатентованные преформы ZPlex ™ Conformal Total Sandwich с пенополиэтиленом, жестким и прочным, как двутавровая балка, но достаточно гибким, чтобы соответствовать изогнутым формам ветряных лопастей. |
Система RMPS имеет модульную платформу с магазином на 10 рулонов для армирования материалов, который разрезает и распределяет слои различной ширины в форму. Размещение материала рассчитано на 3 м / с (10 футов / с). Пара подвижных щеток с электроприводом разглаживает слои по мере их разглаживания. Система также оснащена лазерными и визуальными системами обнаружения морщин. Производитель заявляет, что две смежные друг с другом портальные системы могут произвести половину корпуса лопасти длиной 45 м менее чем за два часа, при этом вдвое меньше ручного труда по сравнению с традиционными методами.Утверждается, что система укладки механически воспроизводима с точностью до 2 мм с допуском нанесения ± 5 мм. ♦
Эта статья была опубликована в выпуске журнала Reinforced Plastics за январь / февраль 2012 года. Чтобы подать заявку на получение бесплатной копии каждого выпуска Reinforced Plastics , заполните форму подписки или , свяжитесь с нами для получения дополнительной информации.
GE нацелена на нулевое количество отходов производства лопастей к 2030 году
Лопасть ветряной турбины, произведенная LM Wind Power, прибыла на оффшорную катапульту возобновляемой энергии в Блит, Англия, 15 августа 2019 года.
Том Уайт | Новости Getty Images | Getty Images
Подразделение возобновляемой энергии GE заявило во вторник, что к 2030 году будет производить лопасти ветряных турбин без отходов, став последним оператором в этом секторе, который пытается разработать более устойчивые производственные процессы.
В заявлении GE Renewable Energy говорится, что ее дочерняя компания LM Wind Power со штаб-квартирой в Дании будет «повторно использовать, перепрофилировать, перерабатывать или восстанавливать все лишние материалы от производства лопастей, отказавшись от захоронения и сжигания в качестве решений по управлению отходами.»
Объявление LM Wind Power касается только отходов производственного процесса и не распространяется на то, что происходит с лопастями по истечении их срока службы.
Фирма пытается решить эту проблему несколькими способами. Это часть консорциума DecomBlades, инициативы, направленной на переработку лопастей и состоящей из нескольких крупных игроков в отрасли.
Она также участвует в ZEBRA или проекте Zero Waste Blade Research, который направлен на разработку и производство полностью перерабатываемых ветряков. лопатки турбины.
Узнайте больше о чистой энергии из CNBC Pro
Вопрос о том, что делать с лопастями ветряных турбин, когда они больше не нужны, стал головной болью для отрасли. Это связано с тем, что композитные материалы, из которых изготовлены лопасти, трудно перерабатывать, а это означает, что многие из них попадают на свалки по истечении срока их службы.
По мере того, как правительства во всем мире пытаются наращивать свои мощности по возобновляемым источникам энергии, количество ветряных турбин во всем мире, похоже, будет только расти, что, в свою очередь, увеличит давление на сектор в поисках устойчивых и управляемых решений по утилизации лопастей.
На этом фоне отраслевая организация WindEurope заявила, что хочет «к 2025 году ввести запрет на захоронение списанных лопастей ветряных турбин во всей Европе», в то время как ряд компаний стремились разработать собственные решения этой проблемы.
В сентябре компания Siemens Gamesa Renewable Energy выпустила то, что, по ее словам, было «первыми в мире перерабатываемыми лопастями ветряных турбин, готовыми к коммерческому использованию на море».
Несколькими месяцами ранее, в июне, датская компания Orsted заявила, что после вывода из эксплуатации «повторно использует, рециркулирует или восстанавливает» все лопатки турбин в своем всемирном портфеле ветряных электростанций.
В том же месяце GE Renewable Energy и производитель цемента Holcim заключили сделку по переработке лопастей ветряных турбин.
А в январе 2020 года Vestas заявила, что нацелена на производство безотходных ветряных турбин к 2040 году.
Все приведенные выше примеры можно рассматривать как усилия по развитию так называемой экономики замкнутого цикла, которая существует в ЕС. называется «моделью производства и потребления, которая включает совместное использование, сдачу в аренду, повторное использование, ремонт, восстановление и переработку существующих материалов и продуктов на максимально возможный срок».«
Энергия ветра — одна из многих отраслей, пытающихся разработать подходы, связанные с идеей экономики замкнутого цикла. Буквально в этом месяце шведская компания по производству аккумуляторов Northvolt заявила, что выпустила свой первый аккумуляторный элемент с тем, что она описала как« 100% переработанный никель, марганец и кобальт ».
В заявлении компании, которая привлекла инвестиции, среди прочего, Goldman Sachs и Volkswagen, говорится, что никель-марганцево-кобальтовый катод элемента был произведен с использованием металлов,« восстановленных в результате переработки отходов аккумуляторных батарей.«
Испытания показали, что производительность была на одном уровне с элементами, сделанными с использованием металлов, которые были недавно добыты, — сказал Нортвольт.