Осаждение меди электролизом — Справочник химика 21
Электролиз. Медную пластинку очистить наждачной бумагой до блеска, погрузить на 3—4 мин в 15%-ный раствор азотной кислоты и после травления хорошо промыть водой под краном. Смонтировать установку так, как показано на рис. 69. В стакан-электролизер налить столько раствора для электролиза, чтобы пластинки были на /4 погружены в раствор. Опустить электроды в раствор, включить реостат на полное сопротивление. Замкнуть ключом электрическую цепь, отметить время начала опыта (включить секундомер) и уменьшить сопротивление так. чтобы напряжение было 1,2—1,4 вольта. Отметить по амперметру силу тока. Точно через 15 мин разомкнуть цепь и промыть железную пластинку водой. Осажденная медь имеет вид плотного [c.196]Характеристика процесса осаждения. Условия полного выделения меди. Электролиз 1 н. раствора соли меди начинается при напряжении, равном приблизительно 1,4 е.
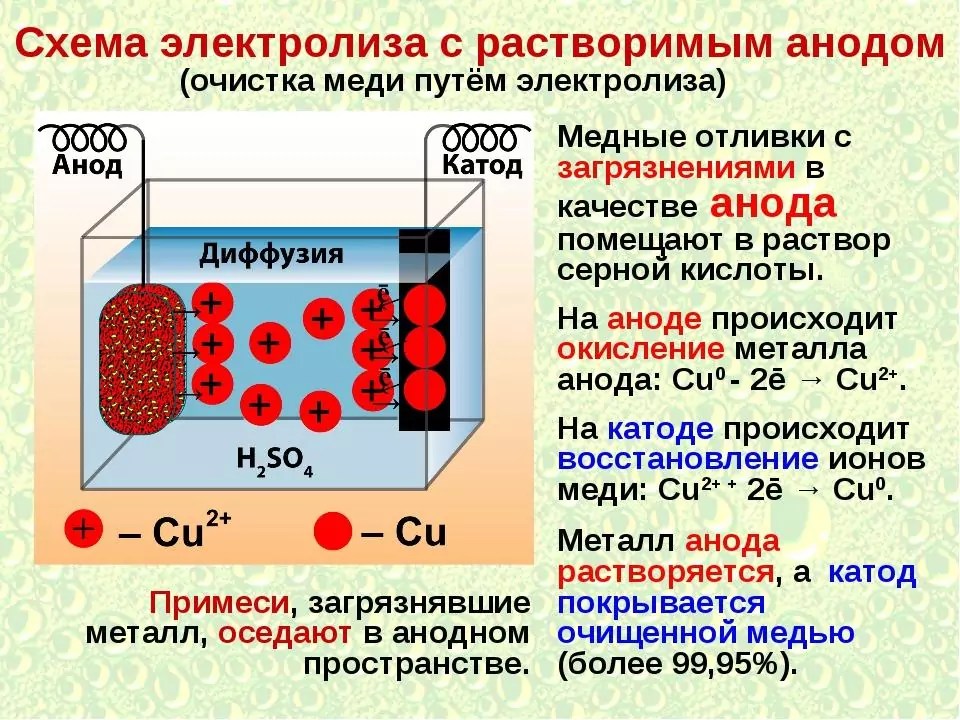
Осаждение меди электролизом Растворы [c.228]
Для электролитического рафинирования меди использован реверсивный режим электролиза с длительностью катодного периода 39 с и плотностью тока 320 А/м . Для анодного периода эти параметры составляют 1,0 с и 290 А/м соответственно. При катодном периоде выход по току для осаждения меди составляет в среднем 98 % растворение меди в анодные периоды проходит с выходом по току 101 %. Процесс проводят в электролизерах с общей катодной поверхностью 50 м при среднем рабочем напряжении 0,34 В на один электролизер.
В понятие структуры входит не только размер, но и форма кристаллов. Варьируя состав электролита и условия электролиза, можно влиять не только на размер кристалла, но также на его геометрическую и кристаллографическую форму. Характерным примером изменения геометрической формы в зависимости от условий электролиза является осаждение меди. При осаждении меди из растворов сульфатов и фторборатов без добавок образуются осадки с колончатой структурой (рис. 47, а). Введение в электролит добавок желатины, фенолсульфоновой кислоты и многих других добавок приводит к образованию волокнистой структуры (рис. 47,6).
Характеристика процесса осаждения. Для осаждения меди можно применять аноды из различных металлов никеля, свинца, алюминия и т. д. Как и при обычном электролитическом осаждении меди, присутствие азотистой кислоты недопустимо осаждение также сильно замедляется в присутствии ионов трехвалентного железа. В связи с тем, что содержание железа в металлическом никеле почти всегда незначительно, перед электролизом к азотнокислому раствору прибавляют немного сернокислого гидразина.
Осаждение меди на свинцовом катоде в начальный момент электролиза проходит при более положительном потенциале по сравнению с другими электродами. Это вызвано тем, что свинцовый катод покрывается в кислом сернокислом электролите контактно вытесненной медью, которая увеличивает его активную поверхность, в результате чего поляризация уменьшается.
При электролитическом методе определения меди требуется получение прозрачного раствора, свободного от мышьяка, сурьмы, олова, молибдена, золота, платиновых металлов, серебра, ртути, висмута, селена (IV) и теллура (IV), загрязняющих осадок выделяющейся меди. Кроме того, должны отсутствовать роданистоводородная кислота, присутствие кото-рЬй делает осадок меди губчатым, и соляная кислота, действующая аналогично и, кроме того, вызывающая растворение платины на аноде и переход ее на катод.
В регенерационных ваннах с нерастворимыми анодами и 2) отбором части электролита на переработку в отделение регенерации. При электролизе в регенерационной ванне на аноде вместо растворения металла происходит выделение кислорода, а на катоде — обычный процесс осаждения меди из раствора. Таким образом, в целом процесс в регенерационной ванне выражается следующей реакцией [c.18]
В противном случае в стакан добавляют еще дистиллированной воды и продолжают электролиз до тех пор, пока проба на полноту осаждения меди не даст отрицательного результата.
Таким образом, электролиз раствора сульфата меди (II) сводится к растворению анода и осаждению меди на катоде. Концентрация сульфата меди (II) в растворе при этом остается постоянной. [c.98]
Группа щелочных электролитов немногочисленна цианистые, пирофосфатные, тиосульфатные, роданистые и некоторые другие. Преимущественно используют цианистые электролиты благодаря их высокой рассеивающей способности и хорошему качеству получаемых покрытий недостаток — высокая токсичность. Применяют пиросульфатные электролиты, по рассеивающей способности близкие к цианистым, для получения мелкокристаллических осадков. При осаждении меди из пирофосфатных электролитов на цинковые сплавы и сталь необходимо наносить подслой из цианистого электролита меднения или резко увеличивать силу тока в начале электролиза.
Структура и твердость осажденной меди могут значительно меняться в зависимости от состава электролита н условий электролиза. На рис. 16 показана микроструктура меди с различной твердостью. [c.108]
Катодное осаждение меди при электролизе раствора. При этом из раствора удаляются ионы меди в виде металлической меди, выделившейся на электроде [c.19]
Состав отложившегося на электроде вещества не должен изменяться под действием кислорода воздуха. При некоторых условиях электролиза (высокой плотности тока) получаются мелкокристаллические, но пористые осадки с весьма развитой поверхностью. Такие осадки легко окисляются. Например, при электролитическом осаждении меди из аммиачных растворов при высокой плотности тока металл образует на поверхности катода губчатый порошкообразный осадок, легко окисляющийся на воздухе в процессе сушки. Результаты определения в этом случае получаются повышенными.
Электролиз продолжают до полного выделения катиона, что определяют по обесцвечиванию раствора или капельной качественной реакцией на осаждаемый катион. При осаждении меди в раствор добавляют воду, чтобы уровень жидкости поднялся на 2—3 мм. Если на вновь погруженной части сетчатого катода не появляется цветного налета меди, значит электролиз закончен. [c.255]
Высушенные и взвешенные электроды присоединяют к прибору для электролиза, погружают в раствор и накрывают двумя половинками часового стекла. Электролиз проводят без перемешивания при плотности тока 0,6 А/дм (при 2—2,5 А и 2,2—2,5 В). Когда раствор станет бесцветным, плотность тока уменьшают до 0,3 A/дм , половинки стекла, стержни электродов и стенки стакана промывают водой. Далее продолжают электролиз до полного выделения меди. Для проверки полноты осаждения меди катод опускают в раствор глубже на 0,5 см и наблюдают, появляется ли на чистой платине окраска меди. Если окраска катода не наблюдается, то стакан, не выключая прибора, заменяют таким же стаканом с 350 мл воды. Электролиз продолжают еще 15 мин. После этого катод вынимают из электролита, промывают над стаканом и отключают напряжение.
На полноту выделения меди оказывает вредное влияние присутствие в растворе даже незначительных следов азотистой кислоты. Это объясняется тем, что при взаимодействии меди с азотистой кислотой образуется окись азота N0, которая быстро окисляется кислородом воздуха до двуокиси. Последняя образует с водой азотную и азотистую кислоты, а НЫОз снова окисляет осажденную медь. Чтобы з далить азотистую кислоту, нужно перед электролизом тщательно прокипятить раствор. [c.206]
Возможными примесями в бронзах являются А1, Fe, Ti, Ni. Si. Медь можно отделить предварительно электролизом [698, 699] или в виде сульфида и купфероната [719]. Электролитическое осаждение меди удобно тем, что в этом методе исключается захват бериллия. Однако при электролизе медь может выделяться неполностью. Железо, кобальт и никель также осаждаются на ртутном катоде. [c.173]
Рассмотрим метод электролитического разделения меди и цинка. Медь и цинк занимают различные места в ряду напряжений (см. рис. 12.3). Для разделения таких металлов можно ограничиться определенными физическими условиями, а именно приложить к электродам напряжение, достаточное для количественного осаждения меди, но недостаточное для выделения цинка даже из концентрированных растворов его солей. Для электролиза Г М раствора сульфата цинка необходимо напряжение =1,7 — (—0,8) = = 2,5 В. Если приложить меньшее нагряжение, например 1,7 В, цинк выделяться не будет. Полноту выделения меди в этих условиях можно вычислить из уравнения Нернста. Напряжение разложения 1,7 В при выделении на аноде кислорода в ряду напряжений соответствует потенциалу на катоде, равному нулю, т. е. потенциалу стандартного водородного электрода. Подставляя это значение в уравнение Нернста , находим [c.227]
Влияние среды. Точные результаты получаются при осаждении меди в сернокислой среде в присутствии свободной азотной кислоты, действующей как деполяризатор и препятствующей выделению на катоде газообразного водорода. Но если электролиз протекает только в азотнокислой среде, то процесс электроосаждения проходит медленно и осадок выделяется неполностью. [c.321]
Осаждение меди из аммиачных растворов приводит к менее точным результатам, так как в процессе электролиза вместе с металлической медью осаждаются окислы и гидроокись меди и других металлов. [c.321]
Электролиз продолжают до полного обесцвечивания раствора (на что требуется около 1 ч), после чего делают пробу на полноту осаждения меди. Для этого добавляют в стакан столько дистиллированной воды (ополоснув ею часовые стекла), чтобы уровень жидкости поднялся на 2—3 мм, и снова приблизительно 10 мин продолжают электролиз. Если при этом на вновь погруженной части электрода не появляется золотистый налет меди, берут каплю исследуемого раствора на капельную пластинку (или на часовое стекло) и, добавив к ней 2—3 капли раствора ацетата натрия, действуют каплей раствора К4[Ре(СЫ)б]. Если красноватобурая муть u2[Fe( N)e] не появляется, осаждение меди можно считать практически полным. Наоборот, если образовался налет меди на вновь погруженной части катода, добавляют еще воды и продолжают электролиз до тех пор, пока проба на полноту осаждения меди не даст отрицательного результата, после чего повторяют описанную выше реакцию на Сц2+ с K4[Fe( N)e] в присутствии Ha OONa. [c.443]
Ход определения. Навеску сплава (1 г) растворяют в смеси 100 мл разбавленной (1 4) h3SO4 с 1 мл разбавленной (1 1) HN0.1. По окончании растворения навески к раствору прибавляют несколько миллилитров 10%-ного раствора сульфата гидразина (N2h5-h3SO4) для восстановления азотистой кислоты и окислов азота, мешающих осаждению меди на катоде. Разбавляют раствор до 150 мл, нагревают до 60—65° С и подвергают внутреннему электролизу. Для этого опускают в раствор электродную пару, состоящую из цинкового анода и платинового сетчатого катода , собранную, как показано на рис. 63. Предварительно тщательно зачищают контакты анода и катода, поверхность цинкового анода и хорошо закрепляют их в соответствующих клеммах. [c.451]
Катод и анод закрепляют в электродержателях, присоединяя к источнику тока соответственно полюсам. В электролизер помещают анализируемый раствор, добавляют 1 мл 2 Ai раствора HNO3, погружают в него электроды и разбавляют исследуемый раствор таким количеством дистиллированной воды, чтобы часть катода (5—7 мм) выступала над поверхностью раствора. Это необходимо для проверки в дальнейшем полноты осаждения меди. Электроды не должны касаться друг друга, а также дна и стенок стакана. Включают магнитную мешалку и регулируют перемешивание раствора. Включают ток и проводят электролиз 35—40 мин, контролируя напряжение (2—2,5 В) или ток (1— 0,5 А) по прибору. По мере осаждения меди катод окрашивается в красный цвет, а раствор постепенно обесцвечивается. Затем для проверки полноты осаждения меди приливают в электролизер 10—15 мл дистиллированной воды. Если через 10 мин на вновь погруженной поверхности катода не наблюдается дальнейшего выделения меди, электролиз заканчивают. В противном случае электролиз продолжают еще 10—15 мин. [c.182]
Определение цинка на платиновом катоде, предварительно покрытом медью. После отделения меди электролизом, как описано выще, раствор переносят в мерную колбу вместимостью 250 мл и доливают до метки дистиллированную воду. Отбирают 50 мл раствора в электролизер, добавляют 25%-ный раствор NaOH в количестве, необходимом для растворения гидроксида цинка, и еще 5 мл избытка щелочи. Осаждение проводят на взвещенном омедненном платиновом катоде, проверяют полноту осаждения и промывают электроды, как описано выще. Катод ополаскивают этиловым спиртом, высушивают при 110°С в сушильном шкафу, охлаждают в эксикаторе и взвешивают на аналитических весах. Содержание цинка вычисляют по формуле [c.183]
Промывные воды следует пропускать через отстойники с железным скрапом для осаждения меди и драгоценных металлов, сточные воды из цехов — через ионообменные смолы. Для цеха электролиза Л. АддИкс дает норму потерь меди 0,04— [c. 206]
Более поздние шаги по извлечению меди из руд электролизом относятся к периоду 1886—1905 гг. Фирма Сименс — Гальске запатентовала способ выщелачивания медного колчедана (СигЗ) в растворах сульфата окиси железа с последующим электролитическим осаждением меди. [c.219]
В дехе устанавливают большое количество ванн. Электролизеры электрически соединены в серии. Электролит циркулирует через все ванны и проходит через подогревающее устройство. В специальных матричных ваннах получают тонкие листы чистой меди, которые используют затем в качестве катодов для получения меди. В матричные ванны вешают катоды-матрицы из прокатанной тонкой меди, алюминия или нержавеющей стали. Матрицы перед осаждением меди смазывают маслом или керосином, а кромки матриц защищают специальными накладками. При достижении толщины осадка меди на матрице 0,4—0,7 мм его сдирают и готовят из него катоды для основного электролиза. [c.305]
Медь в составе контактной массы выполняет роль катализатора. Чистую медь получают электролизом медного купороса Си304. Для прямого синтеза применяется медь двух марок — и М1 с содержанием меди 99,95—99,9%. Суммарное содержание примесей (В1, ЗЬ, Аб, Ре, N1, РЬ, 3 и др.) не должно превышать 0,05—0,1%. Для обеспечения высокой активности контактной массы необходимо применять медные порошки с хорошо развитой поверхностью. Хорошие результаты при прямом синтезе получаются и при использовании мелкодисперсной меди, приготовленной механическим распылением медного порошка или осаждением меди из медных солей. [c.36]
Раствор нагревают на слабом пламени горелки (до 50— 70 °С) для ускорения электролиза. Проводят электролиз до полного обесцвечивания раствора (примерно 1 ч), после чего проводят пробу на полноту осаждения меди. Для этого добавляют в стакан воду, чтобы уровень жидкости поднялся на 2 — 3 мм и снова продолжают электролиз — 10 мин. Если после этого на вновь погруженной части элекхрода не появится золотистый налет меди, следует взять каплю анализируемого раствора на капельную пластинку, добавить к ней 1—2 капли 10 %-ного раствора ацетата натрия и каплю раствора ферроцианида калия К4[Ре(СЫ)б]. Если не появится красновато-бурая муть фер-роцианида меди, то выделние меди можно считать законченным. Если же на вновь погруженной части электрода образуется налет меди, то необходимо добавить воды и продолжить электролиз до получения отрицательной реакции на полноту осаждения меди. [c.256]
Хлорная кислота в электрохимическом анализе. Гендриксон описал осаждение меди, серебра и кадмия из разбавленных растворов хлорной кислоты электрохимическим путем. Были опубликованы работы по осаждению кобальта и никеля , железа и свинца . Норвиц привел общий обзор этой области применения НСЮ. Сообщалось , что анион перхлората в меньшей степени восстанавливался, чем сульфат-ион, и во время электролиза не-давал побочных реакций. [c.126]
Электролизом водных растворов можно отделить галлий от многих металлов Поддерживая катодный потенциал меньшим потенциала выделения галлия, можно выделить из раствора более электроположительные элементы, оставляя галлий и другие электроотрицательные элементы в растворе. Если затем поднять потенциал катода до значения потенциала выделения галлия, то он будет осажден на катоде и таким образом отделен от более электроотрицательных элементов Так разделяют, например, медь (100—250 мг) и галлий (0,5—20 мг) [146] в азотнокислом растворе (pH 1,1, потенциал—0,3 в, 40—50° С). Во всех случаях получается плотный спектральночистый мелкокристаллические осадок меди. Разделение может быть проведено выделением меди электролизом из сульфатных растворов, не содержащих С1 июна при напряжении 2—2,2 в [993]. [c.69]
Электролиз продолжается около 1 ч (до полного обесцвечивания раствора). Для проверки полноты осаждения обмойте часовые стекла дистиллированной водой, долейте в стакан 20—25 мл дистиллированной воды и продолжайте электролиз еще 10 мин. Если на свежепогруженной части катода не будет наблюдаться нового выделения меди, электролиз можно считать законченным. [c.323]
Применения электрохимического выделения меди — emew Corporation
Электрохимическое выделение меди – это электролитический процесс, в котором электрическая энергия используется для восстановления растворенной меди в виде медной пластины, называемой “катодом”.
Cu2+(раствор) + 2e– –>Cu(твердый) (E0 = +0.34В)
Медь легко растворяется в кислотах, включая серную, азотную и соляную. Электрохимическое восстановление медного катода из раствора серной кислоты широко известно и является достаточно простым процессом, коммерчески применяемым с конца 19го века.
Появление технологии вихревого электролиза emew расширило границы возможностей электрохимического восстановления меди. Благодаря своему положительному восстановительному потенциалу (E0 = +0.34В) ионы меди достаточно легко присоединяют электроны при пропускании через раствор электрического тока. Благодаря значительному массопереносу электрохимическое восстановление по технологии emew позволяет получить медь высокой чистоты из сырья с низкой концентрацией, со смешанным составом металлов и содержащего примеси.
Остановимся подробнее на некоторых широко распространенных применениях электрохимического восстановления меди.
Заводы, занимающиеся электролитической очисткой меди, должны постоянно контролировать концентрацию меди в ванной с электролитом. В технологии электрохимической очистки меди используются анод из меди с примесями и инертный катод. При пропускании электрического тока с анода на катод медь анода растворяется и оседает на катоде в виде чистого металла. Растворение меди анода происходит быстрее, чем осаждение на катоде, поэтому концентрация растворенной меди растет. Для поддержания концентрации меди в электролите в заданном диапазоне используется электрохимическое извлечение. Кроме того, содержащиеся в медном аноде примеси также растворяются в электролите и без очистки электролита их концентрация также растет со временем. Эта очистка, “слив” примесей, происходит в специальных ваннах для удаления металла (“liberator” cells, ячейках освобождения). Они представляют собой обычные электролитические ячейки, которые оптимизированы для поэтапного контроля концентрации меди и удаления примесей из рабочего электролита для обеспечения получения высокочистой катодной меди (LME Grade A).
Традиционные методы электрохимического извлечения, несмотря на широкое применение, неэффективны для процесса очистки, так как приводят к следующим негативным факторам:
- Получению некондиционной меди, стоимость переработки которой достаточно велика или трудозатратна
- Выделению канцерогенного кислотного тумана и смертельно ядовитого газообразного мышьяка
- Образованию третичного шлама
Использование передовых технологий электролиза меди emew, имеет следующие преимущества:
- Производство товарной катодной меди высокой степени чистоты при снижении концентрации меди в растворе до 1 г/л
- Значительное снижение стоимости переработки и трудозатрат
- Отсутствие выделения кислотного тумана или летучих газов вроде мышьяка, так как ячейки emew полностью закрыты
- Лучший контроль за содержанием примесей
- Использование субпродуктов от восстановления никелевого катода
Медеперерабатывающие предприятия пользуются этими преимуществами и заменяют типовую технологию более совершенными ячейками emew. В качестве свежего примера можно привести Hindustan Copper Limited, правительственное предприятие в Индии, которое установило ячейки emew для восстановления меди и никеля из стоков медеочистительных цехов.
Важность вторичной переработки металлов постоянно возрастает по соображениям как разумного использования ресурсов, так и экономическим. При переработке потребляется на 85% меньше энергии на выход 1 кг меди по сравнению с первичным производством (добычей), и она оказывает меньшее воздействие на окружающую среду1. Общемировая переработка меди ежегодно экономит потребление 100 млн МВт·ч электрической энергии и сокращает выброс CO2 в атмосферу на 40 млн тонн. Предприятия по вторичной переработке металлов и переработчики играют основную роль в превращении лома и изделий с истекшим сроком службы в пригодный для использования металл, который может быть возвращен в цепочку поставок.
Обычно переработка цветных металлов состоит из следующих 5 этапов:
- Сбор
- Предварительная обработка и сортировка
- Дробление и измельчение
- Физическое разделение
- Пиро- или гидро-металлургическая переработка
В зависимости от оснащенности предприятия по переработке все эти этапы могут либо проводиться в одном месте, либо быть разнесены. После сборки, сортировки, дробления и измельчения изделий с истекшим сроком годности различные компоненты (стекло, пластик, черные и цветные металлы) могут быть разделены исходя из их физических свойств, таких как плотность и магнитные свойства. Медь и ее сплавы вместе с другими цветными металлами поступают в переработку и могут быть извлечены в печи (пирометаллургия) или растворены в проводящем электролите вроде серной кислоты и извлечены электрохимически (гидрометаллургия).
Для отделения благородных металлов (золото, серебро, платина, палладий и другие) от так называемых основных металлов (медь, никель, олово и другие) могут быть использованы методы селективного выщелачивания. Затем для разделения и очистки отдельных металлов может использоваться комбинация прямого электрохимического извлечения и других методов гидрометаллургии, таких как ионный обмен (ion exchange, IX) и селективное осаждение. Медь может быть напрямую выделена из электролита серной кислоты и цветных металлов электрохимически с использованием технологии emew с получением чистой катодной меди.
Большинство правительств и регулирующих органов при них ограничивают сброс отходов. Для соответствия этим все более строгим ограничениям, а также добровольным целям вроде разумного использования ресурсов, многие компании внедряют политику “нулевого сброса”. Это означает, что все образующиеся твердые отходы и сточные воды либо перерабатываются сразу же, в той же технологической операции, где они получены, либо подвергаются дальнейшей переработке до тех пор, пока они не станут безвредными. К сожалению, это может привести к образованию сложных низкокачественных субпродуктов, которые либо имеют низкую ценность, либо должны быть утилизированы на специализированных предприятиях. Как правило, субпродукты низкой ценности сложно переработать традиционными способами, следовательно, варианты их утилизации ограничены.
И именно здесь такая передовая технология как электрохимическое извлечение по методу emew может быть использована для извлечения меди и других металлов из сточных вод и твердых отходов. Медь может быть напрямую извлечена из сточных вод гальванических установок, производства полупроводников, аффинажных заводов, перерабатывающих предприятий и других. В результате получается катодная медь высокой степени чистоты, стоимость которой превышает затраты на ее получение и раствор с крайне низкой (<50 частей на миллион) концентрацией меди, который можно утилизировать в существующих установках очистки сточных вод. В некоторых случаях система электрохимического выделения меди из отходов, установленная на предприятии, может окупиться за несколько месяцев за счет экономии на утилизации опасных отходов.
Твердые отходы, летучая зола, шлаки и т. д. часто представляют собой сложную, низкокачественную смесь металлов, которые могут быть растворены в проводящем электролите (таком как серная кислота) с целью извлечения ценных металлов. Например, низкокачественные отходы, содержащие только несколько процентов меди, могут быть переработаны для электрохимического извлечения катодной меди высокой степени чистоты. Другие металлы, такие как золото, серебро, свинец, олово, кадмий и никель также могут быть извлечены вместе с медью при помощи электрохимического извлечения или комбинации гидрометаллургических методов.
Электролиз меди значительно развился с тех пор, как был открыт в 1807. Сегодня электрохимическое извлечение меди применяется во множестве областей – от контроля концентрации меди и примесей на медеочистительных заводах до извлечения меди из сточных вод производства полупроводников со снижением концентрации целевого металла в растворе до нескольких части на миллион. Хотя цели использования и могут значительно различаться, основы электрохимического извлечения меди остаются теми же и передовые электролизные технологии, таки как emew, продолжают расширять границы применимости этой надежной технологии.
Источники:
1. European Copper Institute. (n.d.). Recycling Saves Energy and CO2. http://copperalliance.eu/about-copper/recycling
«Чистый металл», или Электролитическое рафинирование меди
Рафинирование — заключительный этап в цепочке получения из медной руды «чистого» металла. Он состоит из двух последовательных этапов — пирометаллургическое и электролитическое рафинирование. В первом черновая медь (содержит до 4 % примесей) обрабатывается в печах и из неё удаляются все примеси, кроме включений серебра, золота, селена и теллура, при этом чистота основного металла может достичь 99,6 %. Во втором с помощью электролитических ванн получают полностью очищенную медь, доля примесей в которой не превышает 0,001 %.
Рассмотрим подробнее процесс электролитического рафинирования. Речь идёт исключительно о промышленном производстве, в работе чаще всего используются гальванические ванны объемом 4-12 м3 метра, в качестве электролита выступает смесь из сернокислой меди (CuSO4), подкисленной серной кислотой (H2SO4). В смесь погружаются аноды из меди, прошедшей пирометаллургическое рафинирование, и катоды из «чистой» меди. В ходе электролиза все примеси остаются в растворе электролита, а на катоде оседает очищенный металл. После завершения процесса катод, по сути, представляет собой готовый слиток меди, который можно как отправить предприятиям-потребителям напрямую, так и переплавить в слитки или иной требуемый тип проката. Часть «вымытых» из меди примесей оседает на дно ванны (т.н. шлам), в дальнейшем их можно подвергнуть последующей переработке с целью получения ценных металлов.
Промышленный процесс электролитического рафинирования предполагает работу с большими объёмами металлов, электролитов и, как следствие, высокие сопутствующие затраты (стоимость электролитов, электричество, потери и т. д.). В ходе рафинирования анод («загрязнённая» медь) постепенно растворяется, теряя в объёме — часть примесей оседает на дно ванны, часть растворяется в электролите. При этом чистая медь нарастает на катоде, постепенно увеличивая его в размерах. Начальная фаза изображена на рисунке ниже.
В рафинировании меди применяется такое понятие как экономическая плотность тока — плотность тока, при которой затраты электроэнергии на получение 1 тонны чистой меди будут минимальными (не путать с таковой при расчете сечения проводов, когда идет расчет электрических потерь в ЛЭП).
При этом время процесса зачастую бывает не оптимальным или вовсе не принимается во внимание из-за решающей роли стоимости электричества. Так, в среднем, на растворение анода требуется 20-30 суток, а катоды достигают оптимального размера за 6-12 суток при стандартной плотности тока 170-200 А/м2 и напряжении между анодом и катодом 0,3-0,4 В. Расход электроэнергии при этом составляет в среднем 230-350 кВт⋅ч на 1 тонну меди.
Тем не менее, время тоже является важным фактором, напрямую влияющим как на себестоимость процесса получения медного проката, так и на общую производительность предприятия. Уменьшить время процесса рафинирования можно одним способом — увеличением плотности тока до более высоких, по сравнению со стандартными, значений. При этом, разумеется, придётся изменять многие параметры процесса, чтобы использование токов высокой плотности оставалось в рамках «экономической плотности». Для выполнения этого условия в ход идут различные методики, дополняющие друг друга:
- Поиск сочетаний поверхностно-активных веществ (ПАВ), которые улучшают свойства электролита.
- Использование различных схем циркуляции электролита, позволяющих повысить скорость до 20 л/мин на 1 см2 поверхности (при этом плотность тока может достигать 860 А/м2).
- Применение реверсного тока в процессе рафинирования. Оптимальным на данный момент является соотношение прямого и реверсного тока 200:10. Этот метод является в настоящее время самым эффективным, но требует надёжного источника питания, позволяющего генерировать импульсы тока, строго соответствующие заданным параметрам.
Все описанные выше средства в настоящее время активно исследуются и совершенствуются на многих металлургических предприятиях в России и за рубежом. Основной их целью является не только ускорение процесса, но и обеспечение его непрерывности и повышение эффективности, в том числе экономической.
Первые два способа, как правило, обкатываются непосредственно на предприятиях в ходе экспериментов:
- проверяются новые комбинации ПАВ,
- меняется состав электролита,
- строятся новые системы подачи электролита для повышения скорости его циркуляции.
Использование же реверсных токов зачастую становится самым доступным методом — для его внедрения в промышленный процесс достаточно изменить схему питания гальванической ванны, применив современный источник тока и обеспечив циркуляцию электролита.
Хорошим решением этой задачи будет использование источников питания российского предприятия «Навиком», разрабатывающего источники питания для промышленного применения.
РАЗДЕЛЕНИЕ МЕДИ И НИКЕЛЯ ПРИ ЭЛЕКТРОЛИЗЕ ГРАНУЛИРОВАННОГО ФАЙНШТЕЙНА | Нечвоглод
1. Чижиков Д.М., Гуляницкая З.Ф., Плигинская Л.В., Субботина Е.А. Электрометаллургия медно-никелевых сульфидных сплавов в водных растворах. М.: Наука, 1977.
2. Nechvoglod O.V., Selivanov E.N., Mamyachenkov S.V. The electrolysis of granulated copper-nickel matte // Metals and materials processing in clean environment. Aqueous, low temperatures and electrochemical processing: Fray Intern. Symp. (Cancun, 27 Nov. — 1 Dec. 2011). Wilmington: FLOGEN Technologies Inc., 2012. Vol. 6. P. 601—620.
3. Selivanov E.N., Nechvoglod O.V., Lobanov V.G. The effect of the nickel sulphide alloys structure on their electrochemical oxidation parameters // 15th IFAC Symp. on control, optimization and automation in mining, minerals and metal processing proceedings (San-Francisco, 25— 28 Aug. 2013). Wilmington: FLOGEN Technologies Inc., 2013. P. 259—262.
4. Фокеева И.Г., Цымбулов Л.Б., Ерцева Л.Н., Нафталь М.Н., Фомичев В.Б. Выбор оптимального режима охлаждения файнштейна с повышенным содержанием меди // Цвет. металлы. 2005. No. 7. С. 42—45.
5. Selivanov E.N., Nechvoglod O.V., Udoeva L.Yu., Lobanov V.G., Mamyachenkov S.V. Electrochemical oxidation of coppernickel metal-sulfide alloys // Metall. Nonferr. Met. 2009. Vol. 6. P. 577—581.
6. Ерцева Л.Н., Цемехман Л.Ш., Цымбулов Л.Б., Фомичев В.Б. О строении твердых штейнов никелевого производства // Цвет. металлы. 2008. No. 3. С. 21—23.
7. Нафталь М.Н., Шестакова Р.Д., Петров А.Ф. Особенности технологии выщелачивания высокомедистого файнштейна // Цвет. металлы. 2000. No. 6. С. 44—49
8. Ремень Т. Ф., Рябко А.Г., Кострицын В.Н., Иванова А.Ф. Способы переработки медно-никелевых файнштейнов // Цвет. металлургия (Бюл. ЦИИН). Сер. Пр-во тяжелых цветных металлов. 1982. Вып. 7. С. 1—36.
9. Nechvoglod O.V., Selivanov E.N., Mamyachenkov S.V. Effect of structure on the electrochemical oxidation rate of copper and nickel sulfides // Defect Diffus. Forum. 2012. Vol. 326—328. P. 383—387.
10. Травничек М.И., Масляницкий И.Н. Изменение структуры медно-никелевых файнштейнов в зависимости от режима их охлаждения // Изв. вузов. Цвет. металлургия. 1970. No. 1. С. 31—34.
11. Ayers M.D. Production of powders, strip and other metal products from refined molted: Pat. 3502446 (USA). 1967.
12. Tsantrizos P.G., Francois A., Ehtezarian M. Method and apparatus for production metal powders: Pat. 08515425 (USA). 1995.
13. Чантурия В.А., Вигдергауз В.Е. Электрохимия сульфидов. Теория и практика флотации. М.: Руда и металлы, 2008.
14. Каковский И.А., Набойченко С.С. Кинетика окисления и растворения халькогенидов цветных металлов. М.: Наука, 1986.
15. Peters E. Direct leaching of sulfides: chemistry and application // Metall. Trans. B. 1976. Vol. 7B. P. 505—517.
16. Ghali E., Maruejouls A., Deroo D. Electrodissolution de la millérite en milieu chlorhydrique // J. Appl. Electrochem. 1980. Vol. 10. P. 709—719.
17. Price D.C., Davenport W.G. Anodic reactions of Ni3S2, β-NiS and nickel matte // J. Appl. Electrochem. 1982. Vol. 12. P. 281—290.
18. Watling H.R. The bioleaching of nickel-copper sulfides // Hydrometallurgy. 2006. Vol. 91. Iss. 1—4. P. 70—88.
19. Durga I.K., Srinivasa S.R., Reddy A.E., Chandu V., Gopi M., Kim H. Achieving copper sulfide leaf like nanostructure electrode for high performance super capacitor and quantum-dot sensitized solar cells // Appl. Surf. Sci. 2018. Vol. 435. P. 666—675.
20. Набойченко С.С. Порошки цветных металлов. М.: Металлургия, 1997.
21. Кляйн С.Э., Селиванов Е.Н., Воронов В.В., Нечвоглод О.В., Набойченко С.С. Способ извлечения элементной серы из серосодержащих материалов: Пат. 2427529 (РФ). 2011.
22. Frank K.C., Michael S.M., Venkoba R., Timothy G.R., William G.D. Extractive metallurgy of nickel, cobalt and platinum-group metals. 2-nd ed. Oxford: Elsevier, 2011.
23. Schlesinger M.E., Mattew J.K., Kathryn C.S., Davenport G.W. Extractive metallurgy of copper. 2-nd ed. Oxford: Elsevier, 2011.
Вихревой электролиз. Как это работает?
В современном мире все больше внимания уделяется вопросам рационального использования природных ресурсов и повышению экологической безопасности промышленных предприятий, в том числе предприятий по добыче и обогащению меди, никеля, серебра, олова и некоторых других металлов.
Обменный электролиз vs emewКомпания emewCorporation (Ванкувер, Канада) в 1992 году разработала и запатентовала уникальную и передовую технологию «вихревого» электролиза, при которой рабочий раствор прокачивается между катодом и анодом под определенным давлением в закрытой системе.
При этом все параметры процесса контролируются датчиками системы emewNet, благодаря чему достигается максимальная скорость извлечения металла.
Благодаря повышенному массопереносу увеличивается общее количество извлекаемого металла из раствора, вследствие чего значительно снижается его концентрация в растворе после процесса электролиза.
Применение заводов и технологии emew возможно как в качестве основной производственной системы, так и в качестве встраиваемой технологии в существующее производство.
На примере получения катодной меди, можно выделить следующие преимущества заводов и уникальной технологии emew:
— увеличение общих объемов извлекаемой меди в сравнении со стандартным обменным процессом, а значит получение дополнительной прибыли;
— производство товарной катодной меди высокой степени чистоты (>99,99%) в соответствии с требованиями Лондонской биржи металлов;
— снижение содержания меди в растворе после процесса электролиза – до 1 г/л в сравнении с более чем 20-30 г/л после стандартного обменного процесса;
График, обменный электролиз vs emew— в связи со снижением содержания меди в сернокислом растворе, при его возврате в процесс кучного выщелачивания, повышается эффективность выщелачивания и увеличивается общее количество извлекаемой дополнительной меди из кучи;
— снижение добавляемых объемов серной кислоты, а значит дополнительное снижение затрат;
— закрытые электролизеры, отсутствие
испарений кислоты, значительная экономия
средств на проектировании, внедрении
и обслуживании системы вентиляции. Снижение
затрат на средства защиты для персонала;
— повышение экологической безопасности;
— низкие эксплуатационные расходы, снижение трудовых затрат;
— постоянный контроль за содержанием примесей;
— срок окупаемости <12 месяцев против >2 лет окупаемости завода стандартного обменного процесса.
При соблюдении определенных условий применение технологии emew возможно без предварительной подготовки рабочего раствора.
Но при наличии некоторых примесей, для повышения эффективности использования emew существует ряд дополняющих технологий, таких как выщелачивание, жидкостная экстракция, ионный обмен.
За 26 лет существования, компания emew установила на 6 континентах более 65 заводов по извлечению цветных металлов. Дополнительная информация представлена на сайте https://ru.emew.com
Основные реакции процесса электролиза меди
31.03.2013 | Опубликовано в: Литейное производство
В процессе электролиза меди постоянный ток проходит от плюса источника тока, через анод в раствор медного купороса и серной кислоты в воде, а затем через катод на минус источника. Принято считать, что движение электрического тока происходит от положительного полюса (+) к отрицательному (-). Иначе говоря, мы имеем следующую электрохимическую систему: (Cu с примесями) – (CuSO4, h3SO4, h3O) – (Cu чистая).
Рис. 1. Схема процесса электролиза
Как известно из теории электролитической диссоциации, соли в
водных растворах представлены ионами:
CuSO4 ↔Cu2+ + SO4 2-. (1)
Под действием постоянного электрического тока катионы меди движутся к катоду, где разряжаются и осаждаются
Cu2+ + 2e → Cu (2)
Разряд менее положительных ионов водорода при этом не происходит, пока концентрация меди не снизится до 10÷12 г/л.
В это время на аноде в зависимости от материала, из которого он изготовлен, могут происходить два процесса:
1. Если анод выполнен из меди (хотя бы не чистой) или её сплава, растворяющегося в серной кислоте, то металлы анода переходят в раствор, например:
Cu — 2e → Cu2+ (3)
2. Если анод выполнен из чистой меди (или почти чистой), количество разряжающихся на катоде ионов меди примерно равно количеству образующихся у анода. В этом случае раствор теоретически должен оставаться без изменений. Однако чтобы разница в концентрациях ионов меди у анода (где они переходят в раствор) и у катода (где они осаждаются), а также у верхней и нижней частей электродов не стала слишком большой, её выравнивают путем циркуляции (перемешивания) раствора. В результате происходит растворение и перенос меди с анода электрическим током на катод. Такой вариант электролиза с растворимым анодом лежит в основе электролитического рафинирования меди.
Теоретически имеется возможность осложнения электролиза меди с растворимыми анодами образованием её одновалентных ионов:
Cu — e → Cu1+ (4)
Ионы одновалентной меди в условиях электролиза весьма неустойчивы и образуют ионы двухвалентной меди с выделением медного порошка, оседающего на дно ванны:
2Cu1+ = Cu2+ + Cu (5)
Константа равновесия этой реакции в присутствии металлической меди
К = [Cu1+]2 / [Cu2+] = 0,62∙10-6 (6)
указывает на низкое содержание в растворе одновалентной меди. Кроме того, исследования Ю.В.Баймакова и других показали, что в практических условиях работы электролитных ванн на заводах скорость образования ионов одновалентной меди и выпадения медного порошка ничтожно мала, поэтому ими практически можно пренебречь.
Если применяется анод, не содержащий меди, т.е. выполненный из материала, не растворяющегося в сернокислом растворе, на аноде не происходит образования ионов металла. Такой не¬растворимый анод изготовляют чаще всего из свинца или его сплава с небольшим количеством сурьмы для большей твёрдости и стойкости против коррозии. Так как анод не содержит растворимых в сернокислом растворе металлов, то на аноде должны разряжаться анионы. В нашем растворе имеются анионы ОН1- и SO42-. Из них с меньшей затратой энергии (при потенциале около 1,7В) будет разряжаться ион ОН1-. Для того чтобы начался разряд иона SO42-, потенциал анода должен быть доведен до 3В, однако такой потенциал практически не достигается. Следовательно, при электролизе меди на аноде будет про¬исходить процесс разряда ионов гидроксила по суммарной реакции:
2h3O = O2 + 4Н1+ – 4е (7)
с выделение кислорода на аноде.
На катоде будет протекать тот же процесс разряда ионов Cu2+ .
В итоге обоих электродных процессов в растворе будут накапливаться ионы Н1+, т.е. будет увеличиваться концентрация серной кислоты.
Таким образом, первый вариант электролиза сводится к растворению с помощью постоянного электрического тока меди на аноде и осаждению её на катоде, т.е. к двум взаимно противоположным явлениям. В целом этот процесс происходит с затратой энергии лишь на перенос меди от анода к катоду, преодоление поляризации и сопротивления на пути прохождения тока (шины, контакты и т.д.).
Во втором варианте (с нерастворимым анодом) электрический ток разлагает сульфат меди CuSO4 и воду с выделением меди на катоде, образованием серной кислоты и выделением кислорода на аноде. Эти процессы могут быть изображены следующей суммарной реакцией.
Такой вариант электролиза применяется в том случае, когда следует извлечь медь из раствора, например в гидрометаллургии меди, при регенерации электролита и т. д. На проведение такого процесса необходимо израсходовать значительное количество электроэнергии, определяемое по уравнению Гиббса — Гельмгольца.
Расход энергии при прохождении постоянного электрического тока (в Ватт-часах) равен количеству электричества (в Ампер-часах), умноженному на напряжение (в Вольтах), затраченное на преодоление всех сопротивлений на пути прохождения тока.
Теоретически количество Ампер-часов, требующихся для осаждения одного и того же количества меди, будет для обоих вариантов процесса электролиза одинаковым (1А∙час на 1,186г меди). Практически требующееся количество Ампер-часов может быть различным в зависимости от коэффициента ис¬пользования тока (выхода по току), заметно отличающегося в этих процессах.
Нужное напряжение (в Вольтах) для преодоления всех сопротивлений на пути прохождения тока можно рассчитать по общей формуле:
V = la — lk + l поляр. + IR1 + IR2 (9)
где V — общее напряжение, В;
— потенциал анодного процесса;
— потенциал катодного процесса;
— потенциал поляризации, т. е. преодоление обратной электродвижущей силы, создаваемой из-за неравномер¬ности концентрации меди в растворе у анода и у катода;
I — сила тока, А;
R1 — сопротивление электролита, Ом;
R2 — все прочие сопротивления (контакты, шины и т.д.).
Последние два члена (IR1 и IR2) представляют напряжение, требующееся для преодоления сопротивления электролита (раствора) и всех прочих сопротивлений. Для электролиза с растворимыми анодами разность (la – lk)при малой силе тока близка к нулю. На практике при больших силах тока разность ( la – lk ) немного (до 0,05В) отличается от нуля.
Однако, основным по величине, определяющим напряжение всего процесса, является четвертый член, т.е. напряжение, необходимое для преодоления сопротивления электролита (раствора).
При электролизе с нерастворимым анодом разность (la – lk) уже не равна нулю, а является довольно большой величиной.
Минимальная величина этой разности может быть точно рассчитана, если известна убыль изобарного потенциала реакции
(10)
Зная ∆Z образования всех этих соединений, можно рассчитать эту работу, т. е. найти требующееся напряжение разложения
Σ∆Z=-0,239•n•F•E (11)
Это значит, что общее напряжение процесса по второму варианту электролиза (с нерастворимым анодом) будет в несколько раз выше, чем в первом.
На практике при первом варианте электролиза (с растворимым анодом) напряжение на паре электродов (от анода до катода) колеблется в пределах 0,2÷0,4В (считается нормальным 0,3В). Для второго варианта с нерастворимым анодом напряжение на паре электродов (от анода до катода) значительно выше — в среднем около 2,4В (т. е. при¬мерно в 8 раз больше).
В соответствии с этим при электролизе с нерастворимым анодом энергии постоянного тока расходуется не менее 2400 кВт•час вместо 300÷350 кВ•час на 1т меди при электролизе с растворимым анодом, т.е. тоже примерно в 8 раз больше. Рас¬ход электроэнергии на осаждение 1т меди может быть подсчитан по уравнению
(12)
где W – расход электроэнергии, кВт•час;
— напряжение на ванне, В.
— выход по току – 0,92÷0,97;
k – 1,186 т/А-час.
Источник — Медь Вторичная: Монография
Перейти: Медное литье
Электролитическое рафинирование меди » Все о металлургии
29.04.2015
Электролитическое рафинирование меди преследует две основные цели: 1) получение меди высокой чистоты (99,90—99,97% меди), удовлетворяющей требованиям электротехнической промышленности и промышленности производства чистых сплавов; 2) извлечение драгоценных и редких металлов, которые присутствуют в большинстве сортов черновой меди.
Все затраты на электролитическое рафинирование меди окупаются стоимостью извлекаемых благородных и редких металлов
Подлежащею электролитическому рафинированию черновую медь предварительно рафинируют огневым способом до содержания меди 99,0—99,5% Литые пластины из такой меди в электролитных ваннах соединяют с положительным источником тока (аноды), в качестве катодов применяют тонкие листы из электролитической меди. Электролиз на всех медеэлектролитных заводах ведут в водном растворе сульфата меди, содержащем свободную серную кислоту.
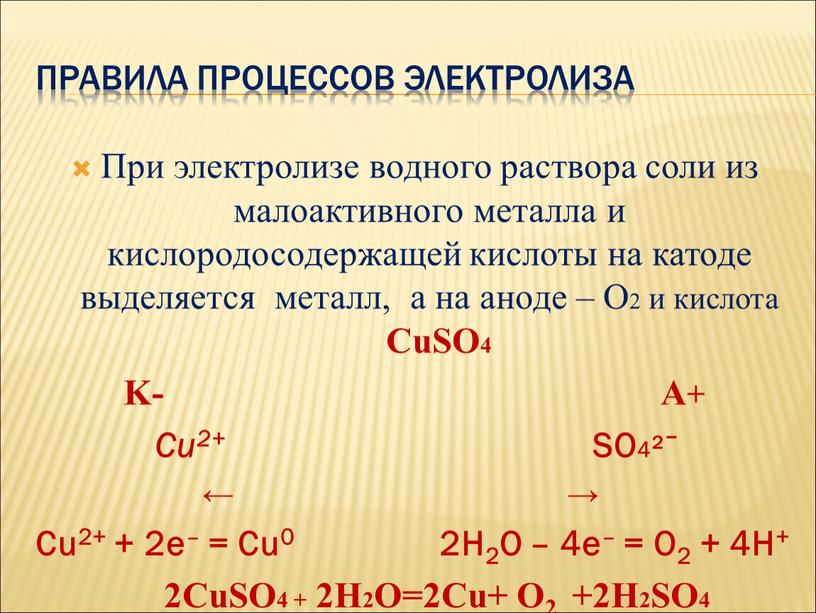
В результате разности потенциалов между электродами ванны происходит электрохимическое растворение меди на аноде и осаждение чистой меди на катоде. Большая часть примесей, содержащихся в анодной меди, осаждается на дне ванны в виде шлама, меньшая часть переходит в раствор, загрязняя электролит. Разряд ионов водорода на катодах возможен только при весьма малых концентрациях ионов меди в прикатодном слое электролита, что в заводских условиях при достаточной циркуляции электролита и высокой концентрации ионов меди в общей массе электролита никогда не наступает. Например, при 40° возможный совместный разряд ионов водорода и меди наступает при концентрации ионов меди 3,8*10в-25 г-ион/л, а это — весьма малая концентрация, которая в практике трудно достижима.
При электролизе меди желателен процесс растворения меди с образованием двухвалентных ионов меди. Разряд ионов гидроксила и SO4в2- в практике не происходит, так как он возможен при весьма высокой концентрации ионов меди в растворе (CСu2+ = 10в16 г-ион/л), во много раз превосходящей растворимость сульфата меди в воде.
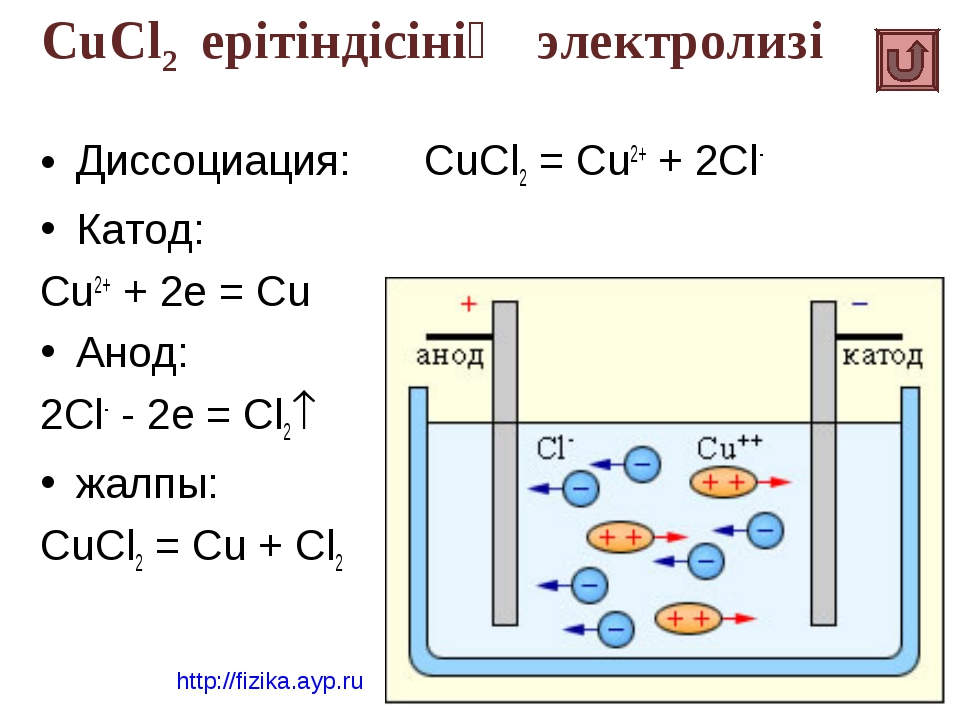
Анодное растворение в сернокислотном растворе дает преимущественно ионы двухвалентной меди, но возможен и электрохимический процесс с образованием иона одновалентной меди:
Cu — е → Cu+.
Повышение температуры электролита способствует образованию одновалентной меди
При охлаждении электролита, насыщенного Cu2SO4 вследствие eго низкой растворимости, выделяется металлическая медь по уравнению
Cu2SO4 → CuSO4 + Cu.
Образование одновалентной меди при электролизе — процесс нежелательный, обогащающий электролит медью и увеличивающий выход порошкообразной меди в шлам.
Поведение примесей при электролизе меди
В анодной меди, поступающей на электролитическое рафинирование, присутствует до 1 % примесей. Это чаше всего элементы: Au, Ag, Pt, Se, Te, As, Sb, Bi, Pb, Sn, Ni, Co, Fe, Zn, Al, а также химические соединения меди; Cu2O, Cu2S, Cu2Se, Cu2Te.
При анодном растворении в сернокислом электролите примеси-металлы ведут себя согласно их нормальным потенциалам.

Примеси в анодной меди можно разбить на четыре группы: 1) металлы более электроположительные, чем медь: золото, серебро, платина и ее спутники, селен, теллур и др.; 2) металлы, обладающие потенциалами, весьма близкими к потенциалу меди, мышьяк, сурьма, висмут; 3) металлы, имеющие более электроотрицательные потенциалы, чем медь: свинец, олово, никель, кобальт, железо, цинк и др.; 4) различные химические сеединения — пассивные в электрохимическом отношении вещества: Cu2O, Cu2S, Cu2Se, Cu2Te.
Первая группа примесей. Благородные металлы, а также селен и теллур, обладая более положительным потенциалом при анодном растворении, чем медь, почти полностью переходят в шлам. Такое поведение указанных элементов используют для выделения их в процессе электролиза в концентрированном виде в шлам. Из этой группы в электролит переходит лишь серебро в виде Ag2SO4, и то в незначительных количествах. Принятая практикой добавка в электролит ионов хлора способствует выпадению из раствора в шлам серебра в виде хлористого серебра.

Замечено, что благородные металлы частично все же попадают в катодную медь. По мнению большинства исследователей, это происходит механически в результате увлечения частичек шлама на поверхность катода, что подтверждается наблюдающимся на практике возрастанием концентрации благородных металлов в катодной меди при увеличении скорости циркуляции и при ухудшении поверхности катодного осадка. Содержание золота и серебра в дендритообразных наростах («шишках») на нижней поверхности полотна катода во много раз превышает среднее содержание этих металлов в катоде.
Возможно также и электрохимическое осаждение благородных металлов (особенно серебра) за счет образования сильно электроположительных ионов, однако ввиду весьма малых концентраций их количество оседающих благородных металлов должно быть значительно меньше того, что получается практически.
Вторая группа примесей. Потенциалы примесей этой группы весьма близки к потенциалу меди, а это значит, что при увеличении концентраций примесей в электролите возможен совместный разряд их с медью на катоде.

При повышенной плотности тока, низком содержании меди в прикатодном слое из-за слабой циркуляции электролита увеличивается вероятность электроосаждения этих примесей на катоде.
Нормальным считается содержание менее 0,002% примесей второй группы, что можно достичь только при малом содержании этих примесей в анодной меди из-за близости их потенциалов к потенциалу меди. Поэтому необходимо эти примеси полнее удалять при огневом рафинировании меди.
Нa практике для того, чтобы свести к минимуму попадание примесей в медь, проводят следующие мероприятия:
1) регенерируют электролит за счет вывода части его (как правило, наиболее загрязненной) из производственного цикла;
2) работают на повышенных концентрациях серной кислоты, так как концентрации ионов Sb3+ и Bi3+ сильно понижаются с увеличением концентрации SO4в2-;
3) вводят в электролит ион хлора, добавляя соляную кислоту или поваренную соль, чтобы уменьшить концентрацию ионов As3+;
4) работают при достаточно энергичной циркуляции электролита, чтобы устранить обеднение концентрации ионов меди в прикатодном слое.

Третья группа примесей. Металлы, относящиеся к примесям этой группы, имеют повышенный электроотрицательный потенциал, поэтому при электролизе ионы этих металлов не разряжаются на катоде. Никель, кобальт, цинк, железо накапливаются в растворе в виде сернокислых соединений, свинец дает труднорастворимую сернокислую соль PbSO4 и почти целиком попадает в шлам; образующийся при электрохимическом растворении олова сульфат SnSO4 легко подвергается гидролизу, давая основные малорастворимые соли, также выпадающие в шлам.
В практике электролиза часто приходится встречаться со значительным количеством никеля в анодной меди, содержание которого в электролите достигает 15—30 г/л (цехи Норильского и Московского медеэлектролитных заводов). Присутствие столь значительных количеств никеля в растворе резко ухудшает катодные осадки, потому что снижается содержание сульфата меди в растворе, так как в силу большой растворимости сульфата никеля в электролите в присутствии значительных количеств его понижается растворимость сульфата меди.

Для удаления сульфата никеля приходится долго промывать катодную медь проточной горячей водой.
Следует учитывать также, что с переходом металлов третьей группы в раствор в сернокислой форме уменьшается концентрация свободной серной кислоты в электролите, значит увеличивается ее расход.
Четвертая группа примесей. Соединения меди: Сu2О, Cu2S, Cu2Se, Cu2Te, являясь в электрохимическом отношении пассивными, при анодном растворении отрываются в виде мельчайших частиц от анода и попадают в шлам. Закись меди, кроме этого, частично растворяется серной кислотой, обогащая электролит медью, отчего увеличивается расход серной кислоты.
Конструкция электролитных ванн и показатели их работы
Электролитическое рафинирование меди ведут в деревянных и железобетонных ваннах прямоугольной формы.

На зарубежных заводах Эль-Пасо, Перт Амбой, Муфулира ванны железобетонные, футерованные свинцом, содержащим 6% сурьмы. На заводах Нкана, Такома, Балтимора, Болиден установлены комбинированные ванны из дерева и бетона дно ванны и торцовые стенки деревянные, перегородки бетонные. Ванны футерованы различными кислотоупорными веществами — асфальтом, смолой, кислотоупорной плиткой и т. п.
Ширина и глубина ванны зависят от размеров анодов и катодов, длина — от их количества. Между краями электродов и боковыми стенками оставляют свободное пространство 70—90 мм для предупреждение коротких замыканий с футеровкой ванны, от нижней кромки электродов до дна ванны — 150—200 мм — для накопления шлама. Основные размеры ванн, установленных на заводах, приведены ниже, м.
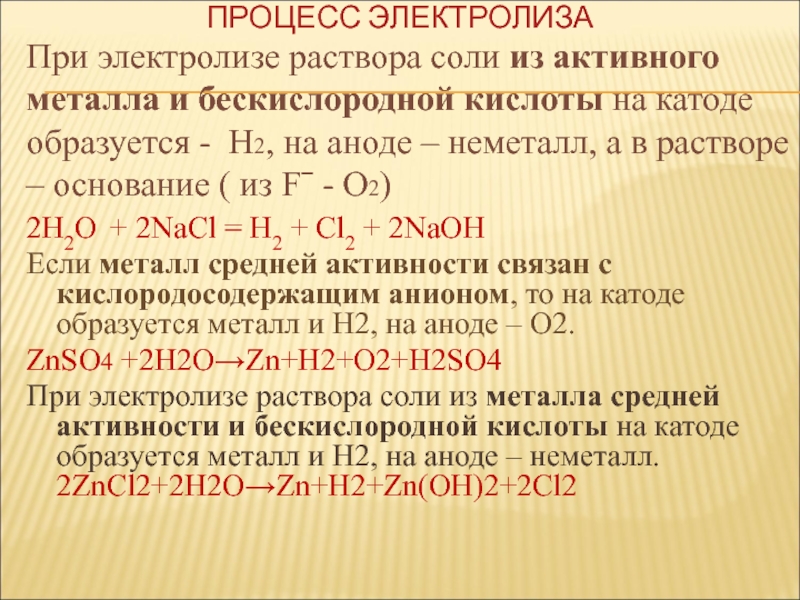
По конструктивным соображениям и для экономии места ванны соединяют в отдельные группы — серии, например на Пышминском медеэлектролитном заводе серия состоит из 24 ванн.
Ванны установлены на кирпичных опорах или массивных железобетонных балках, покрытых сверху для изоляции толстыми стеклянными или фарфоровыми пластинами. Днище каждой ванны снабжено ворон кой для спуска шлама, впаянной в футеровку ванны. На торцовой стенке каждой ванны имеется карман для подвода электролита, на противоположной торцовок стенке — специальный лоток для отвода электролита в желоб, общий для ряда серий (рис. 15).
На наружных бортах крайних ванн серии (блока) уложены медные токоподводящие шины, примерное сечение которых 200X50 мм; средние ванны имеют промежуточные тонкие трехгранные шины Токоподводящие шины изолированы от бортов ванны резиной, трехгранные шины — деревянными планками. На ряде заводов за последнее время болтовые соединения токоподводящих шин заменены сварными что снизило падение напряжения в контактах.
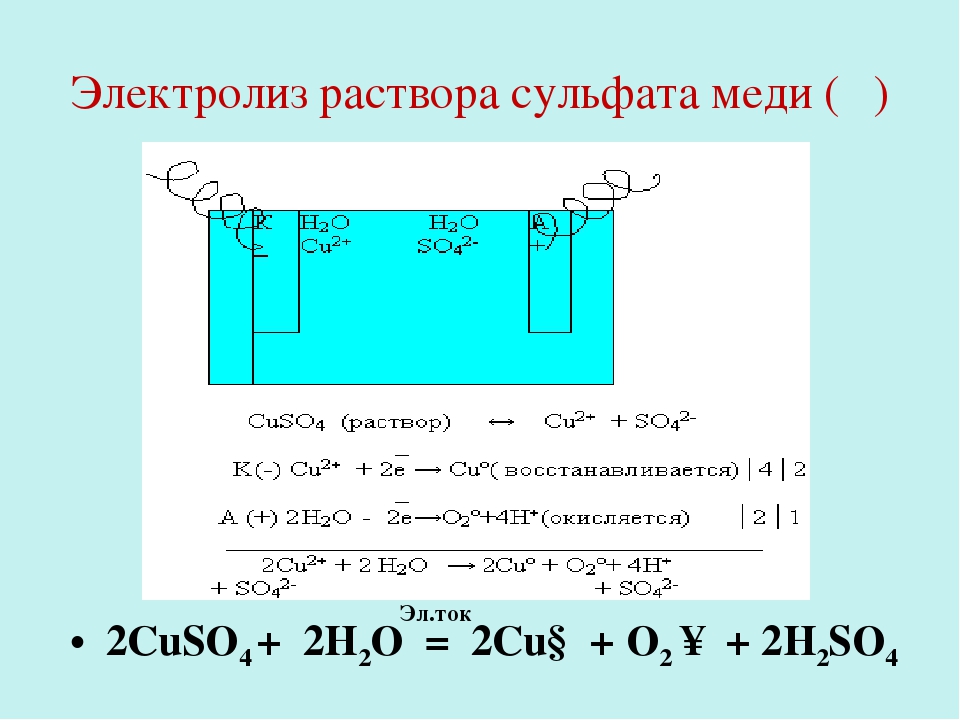
Аноды обычно отливают из рафинированной огневым методом меди в виде квадратных пластин размером не более 1000×1000 мм с ушками вверху для подвешивания анода и для подвода тока. Толщина анода в верхней части от 30 до 40 мм, внизу на 10—15% меньше. Вес анода примерно 200—300 кг, обычно не превышает 350 кг. Продолжительность растворения анодов в зависимости от плотности тока и толщины анодов составляет в среднем 20—30 дней. После растворения анода остается скрап — ушки и часть пластины; выход скрапа 10—20%. Примерные анализы анодной меди различных заводов приведены в табл. 29.
Характеристика анодов различных заводов приведена в табл. 30.
Работа на тяжелых анодах и удлинение срока растворения их позволили, например, на Пышминском заводе сократить выход анодного скрапа, уменьшить число перегрузок и затраты труда на эти операции, а также снизить себестоимость передела и сократить время простоев серий ванн.
Катодами служат листы меди, полученные электролитическим осаждением — маточные листы.

Заготовку маточных листов производят в электролитных ваннах обычной конструкции.
Ванны для заготовки маточных листов имеют свою систему циркуляции электролита и питаются более чистым раствором, чем рафинировочные (коммерческие). Матричные ванны включаются последовательно в общую электрическую сеть с рафинировочными ваннами. Матричный передел на заводах составляет 5—10% от общего количества ванн в цехе. Аноды — медь того же состава, а катодами служат матрицы — медные листы холодной прокатки толщиной 4—5 мм или листы из нержавеющей стали. Для облегчения сдирки маточных листов на рабочих поверхностях вдоль краев матрицы прорезаны узкие желобки. Чтобы на кромках матрицы не осаждалась медь, практикуется их защита деревянными планками, резиной, фаолитом.

Перед загрузкой в ванны поверхность медных матриц смазывают смесью керосина с небольшим количеством солидола.
Практикой Пышминского завода установлено, что срок службы матриц из меди марки M1 не превышает четырех лет, а матрицы из меди марки М2 служат всего 1,5—2 года. Матрицы изнашиваются в результате коррозии их на наиболее опасном участке — у зеркала электролита, контактирующего с воздухом.
Для увеличения срока службы матриц в 1957 г. рационализаторами разработан и внедрен в производство электролитический способ покрытия свинцом верхней части матриц. На рис. 16 изображена ванна по электролитическому свинцеванию головок матриц.
На некоторых отечественных заводах вместо медных матриц успешно применяют матрицы из нержавеющей стали Характеристика катодов, маточных листов и матриц различных заводов приведена в табл.
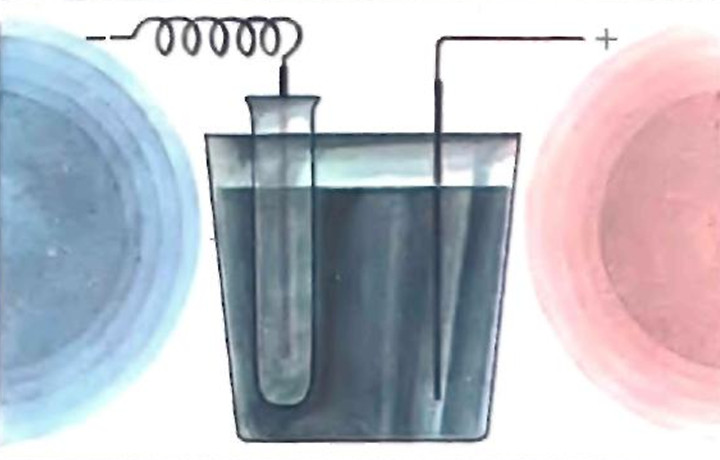
На заводах применяют две схемы включения электродов в ванне: параллельную (схема мультипль) и последовательную (схема серий).
До настоящего времени применяется почти исключительно параллельная схема, последовательная схема употребляется при электролизе меди, содержащей незначительное количество благородных металлов, потому что преимущество этой схемы в отношении экономии энергии полностью теряется вследствие значительных потерь благородных металлов, так как шлам из-за малых расстояний между электродами не успевает полностью осесть на дно ванны, часть его механически прилипает к катоду и включается в осадок меди.
На большинстве заводов, работающих по системе мультипль, при меняют непосредственное соединение катодных штанг с анодами. В этом способе соединения (контакте) конец катодной штанги положен на ушко анода предыдущей ванны, для чего в ушке имеется соответствующее углубление. Промежуточная шина (трехгранная) служит для более равномерного распределения тока по всем электродам.

Для рафинирования меди применяют, как правило, растворы сернокислой меди с высоким содержанием серной кислоты. Такие растворы обладают хорошей электропроводностью, очень устойчивы, нелетучи, что позволяет вести электролиз при высокой температуре, благоприятствующей повышению электропроводности электролита. Кроме того, в сернокислых растворах выделение благородных металлов происходит гораздо полнее, чем, например, в солянокислых. Как правило, заводы работают на электролите, содержащем от 32 до 45 г/л меди (125—180 г/л медного купороса) и 150—220 г/л серной кислоты. Если концентрация серной кислоты в электролите более 220 г/л, то уменьшается растворимость медного купороса, а если содержание медного купороса меньше 120—125 г/л, то на катоде могут осесть вредные при меси (мышьяк и сурьма) и ухудшиться качество катодной меди. Растворимость сернокислой меди в зависимости от содержания серной кислоты при 25° приведена ниже.
Выше было сказано, что в результате растворения примесей, содержащихся в анодах, в электролите накапливаются сернокислые соли никеля, цинка, железа, сурьмы, висмута и мышьяковистые соединения.
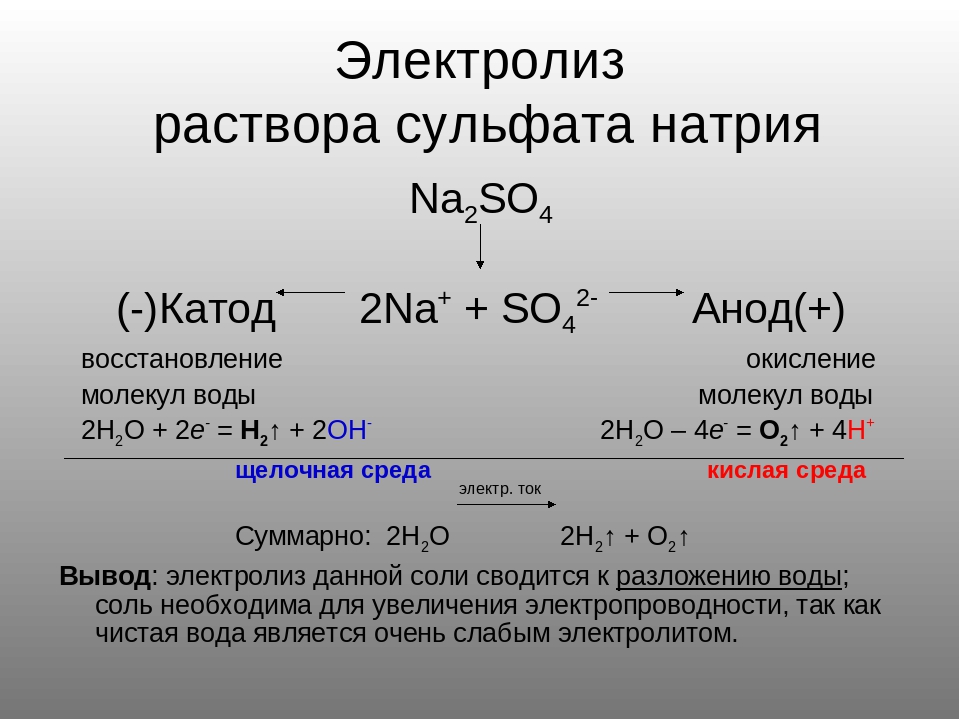
Принято считать максимальным следующее содержание примесей в электролите: 12—20 г/л Ni, 1—3 г/л Fe, 10—15 г/л As, 5—6 г/л Sb.
Кроме указанных примесей, в электролите содержится небольшое количество хлора, вводимого для осаждения в шлам серебра, и сурьма, а также поверхностно активные вещества и коллоиды, вводимые для улучшения качества катодного осадка (см. ниже)
Каждый завод в зависимости от местных условий, качества анодов и требований, предъявляемых к катодной меди, выработал свой состав электролита, который дает удовлетворительные технические и экономические показатели электролиза. В табл. 32 дан состав электролита различных заводов.

Плотность промышленных электролитов 1,18—1,28 г/см3, некоторые данные об удельном сопротивлении электролита в зависимости от кислотности и температуры приведены в табл. 33.
Обычно для расчета сопротивления медного электролита применяют метод Сковронского, который подробно описан в литературе.
В настоящее время все медеэлектролитные заводы применяют подогрев электролита (50—65°), в результате которого сопротивление электролита понижается в 2,5 раза по сравнению с сопротивлением при 25°. При дальнейшем повышении температуры электролита сильно увеличивается его испарение и ухудшаются условия труда, а также повышается химическое растворение электродов в электролите.
На большинстве заводов электролит подогревается паром в специальных баках-подогревателях, снабженных свинцовыми змеевиками. В настоящее время на Пышминском заводе баки-подогреватели электролита сварные, из 6-мм нержавеющей листовой стали марки 1Х18Н9Т, а не железобетонные, футерованные на 8 мм свинцом На некоторых заводах для уменьшения испарения электролита либо зеркало электролита покрывают маслом, либо ванны накрывают стеклополотном или различными пластиками.
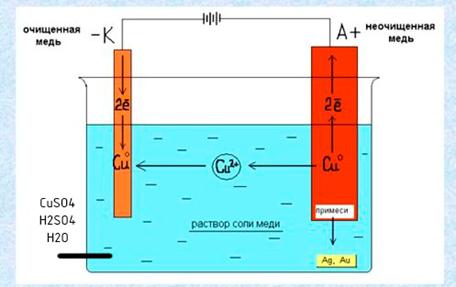
Для выравнивания состава электролита по всей ванне применяют переточную систему циркуляции электролита: подогретый раствор вводят с одного конца ванны и удаляют с другого (обычно электролит вводят со дна ванны и отводят сверху). На некоторых заводах (например, на Норильском) применяется обратная система циркуляции — ввод электролита сверху и отвод снизу. Обратная циркуляция целесообразна при высоком содержании благородных металлов в анодной меди, так как поток электролита создает некоторое взмучивание шлама, увеличивая при этом переход благородных металлов в катодную медь.
Скорость циркуляции электролита выбирают в зависимости от плотности тока и состава анодной меди. Чем выше плотность тока и температура электролита, тем интенсивнее должна быть его циркуляция. На различных заводах в зависимости от плотности тока применяют различную скорость циркуляции электролита, что видно из следующих данных:
Для поддержания постоянного состава электролита и для предупреждения накопления в нем вредных примесей определенную часть его постоянно выводят из процесса и направляют в так называемые регенеративные ванны для извлечения меди.
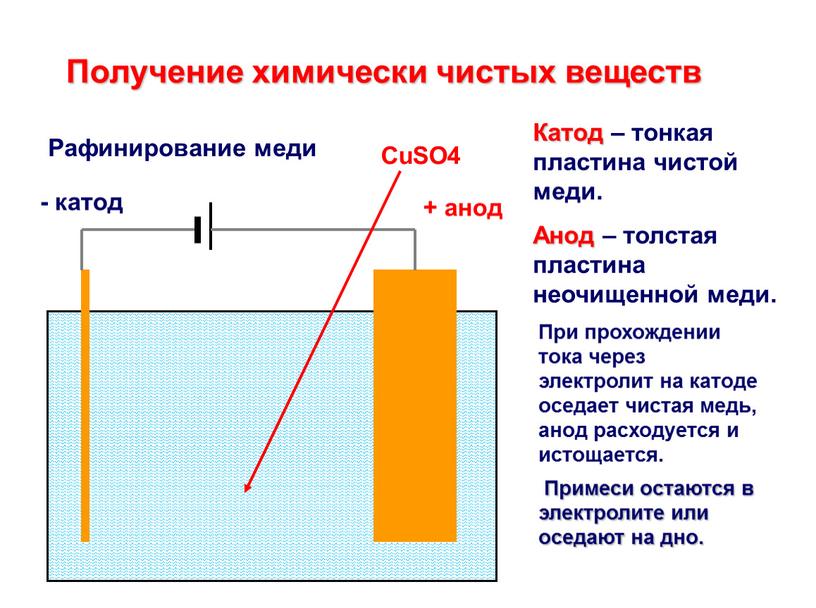
Падение напряжения в регенеративной ванне изменяется в пределах 2,3—2,5 в; вследствие высокого вольтажа расход электроэнергии на осаждение меди в регенеративных ваннах достигает 2500—4000 квт*ч на 1 т катодной меди.
Катоды из регенеративных ванн содержат 99,5—99,9% Cu и иногда значительное количество мышьяка, сурьмы и других примесей. Как правило, такие катоды направляют в анодную плавку. Обычно в электролитных цехах на каждые 100 ванн в одной или двух ваннах ведут извлечение меди из электролита.

На многих электролитных заводах наряду с выводом электролита в регенеративные ванны применяют ежесуточный вывод части электролита из общего цикла в купоросный цех для производства медного и никелевого купоросов. Вместо выведенного электролита добавляют необходимое количество серной кислоты и воды (обычно используется вода от промывки катодов, производственный конденсат и т. п.). При этом в электролите снижается содержание меди и примесей.
Падение напряжения при электролизе слагается из разности электродных потенциалов, вызываемой концентрационной поляризацией, омического падения напряжения в электролите и потерь во всевозможных контактах и металлических проводниках тока, включая потери в шламе.
Падение напряжения в электролите зависит от силы тока и сопротивления раствора. При мультипльной системе из обшей величины падения напряжения на ванне порядка 0,22—0,4 в около 70—88% падает на преодоление сопротивления электролита, до 15% — на преодоление сопротивления металлических проводников и шлама, 5—6% — на преодоление обратной электродвижущей силы, обусловленной концентрационной поляризацией.
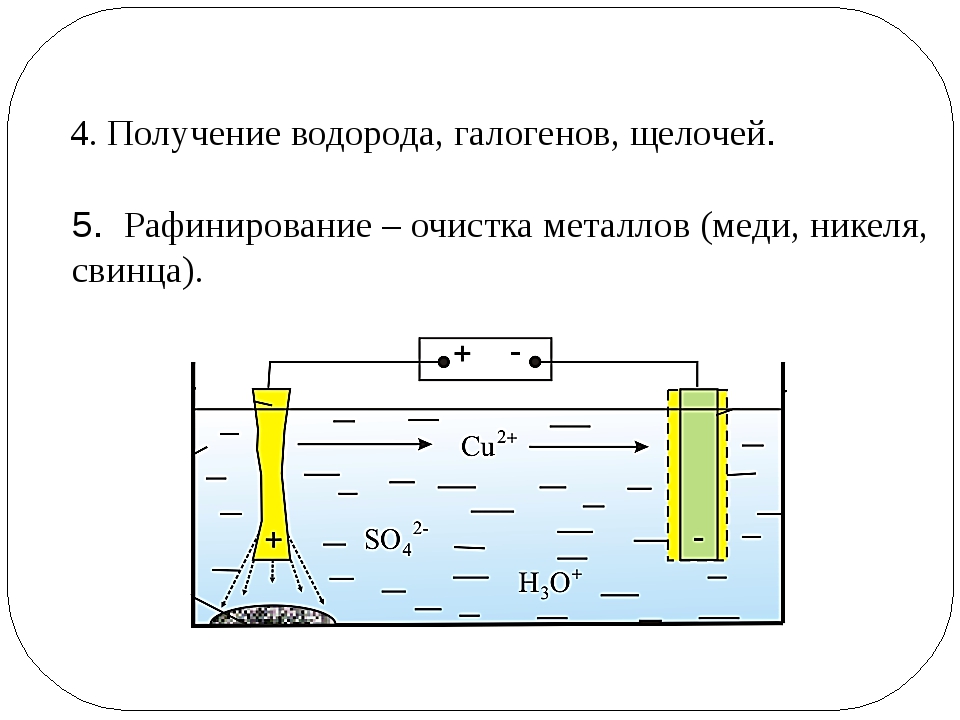
Расход энергии зависит от большого количества факторов, в первую очередь от омического сопротивления ванны и плотности тока Количество затрачиваемой энергии на весовую единицу катодов увеличивается прямо пропорционально увеличению плотности тока (силы тока, отнесенной к 1 м2 поверхности катодов в ванне).
Практически расход, энергии постоянного тока колеблется от 200 до 450 квт*ч, обычно 250—300 квт*ч на 1 т катодной меди. Из отечественных заводов наименьший расход электроэнергии достигнут на Пышминском заводе, на котором по сравнению с 1947 г. расход электроэнергии снизился на 45%.
Вопрос экономии электроэнергии является чрезвычайно важным, поскольку затраты на электроэнергию при электролизе меди составляют 30—40% стоимости передела. Чтобы добиться уменьшения удельного расхода электроэнергии при постоянной плотности тока, необходимо следующее. 1) увеличение концентрации серной кислоты в ваннах для повышения электропроводности электролита и снижения напряжения; 2) повышение температуры, благодаря чему понижается поляризация электродов и увеличивается удельная электропроводность электролита; 3) уменьшение расстояния между электродами; 4) применение наиболее совершенной конструкции контактных устройств и поддержание их в чистоте.
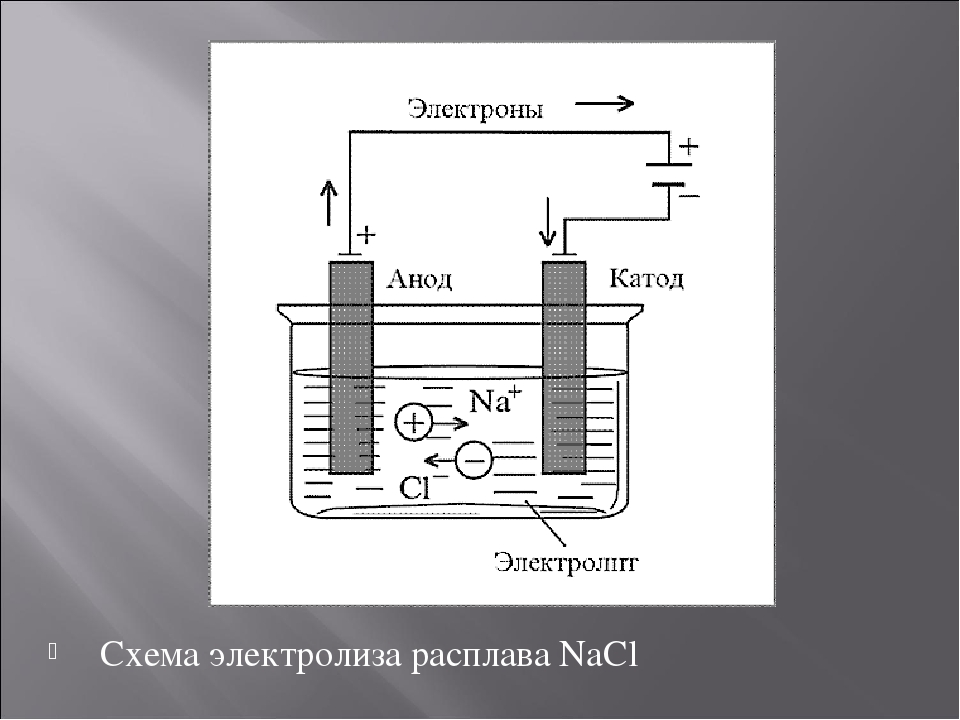
Плотность тока служит одним из основных технических показателей, выбор которого определяется техническими и экономическими условиями. При данных размерах ванны с повышением плотности тока растет и его сила, а следовательно, увеличивается производительность ванны и снижается стоимость оборудования и анодной меди, находящейся в обороте, на единицу мощности. Уменьшается также расход пара на подогрев электролита, так как увеличивается количество джоулева тепла, выделяющегося в ванне. Однако, повышение плотности тока вызывает повышение напряжения на ванне, а значит и расхода электроэнергии, а также повышение потерь благородных металлов.
Существуют специальные формулы для расчета наивыгоднейшей экономической плотности тока в зависимости от конкретных условий. Часто применяют формулу, предложенную в 1909 г П.М. Аваевым, впоследствии несколько усовершенствованную А.И. Гаевым.
К техническим показателям электролиза относится также степень использования тока или выход по току, определяемый как отношение между весом выделившейся меди и теоретическим количеством, которое должно было быть выделено прошедшим через ванну током.
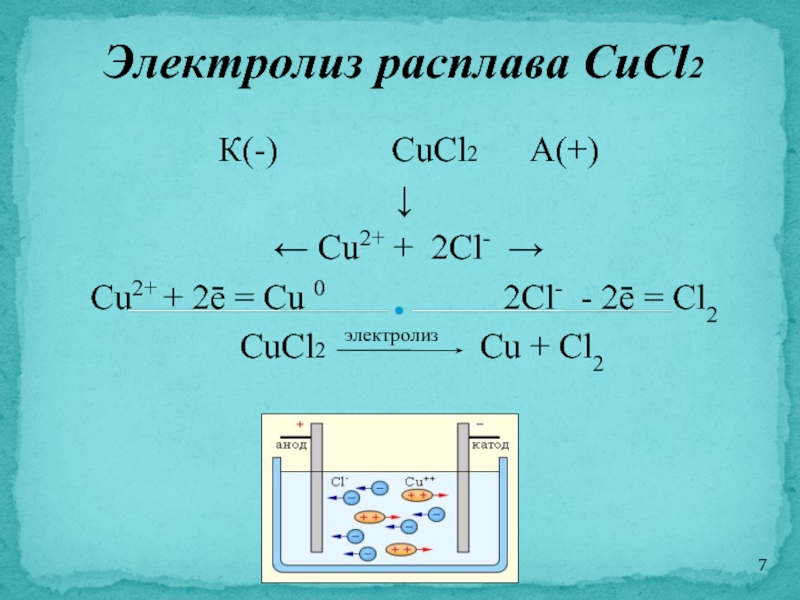
Причины, уменьшающие выход по току, следующие: 1) утечка тока в землю через циркуляционную систему и между стенками ванны; 2) побочные реакции; 3) короткие замыкания вследствие образования на катоде шишек, веточек (дендритов) и т. п. наростов, а также вследствие неравномерного растворения анода (падение крупных кусков металла). В достижении высокого выхода по току решающее значение имеет тщательный надзор за работой электролитных ванн и квалифицированное их обслуживание (тщательная установка электродов в ванне, систематическое обнаружение и устранение коротких замыканий, правка катодов). При плохом обслуживании ванн выход по току падает до 85—90%, при хорошем — его можно устойчиво поддерживать на уровне 95%. Технические показатели работы ванн различных заводов приведены в табл. 34.
Пути улучшения качества катодного осадка
Медь выделяется на катодах в виде прочного осадка. Осадок хорошего качества должен иметь достаточно гладкую поверхность и плотную мелкокристаллическую структуру с характерной вертикальной штриховатостью, цвет осадка должен быть бледно-розовый с шелковистым оттенком.
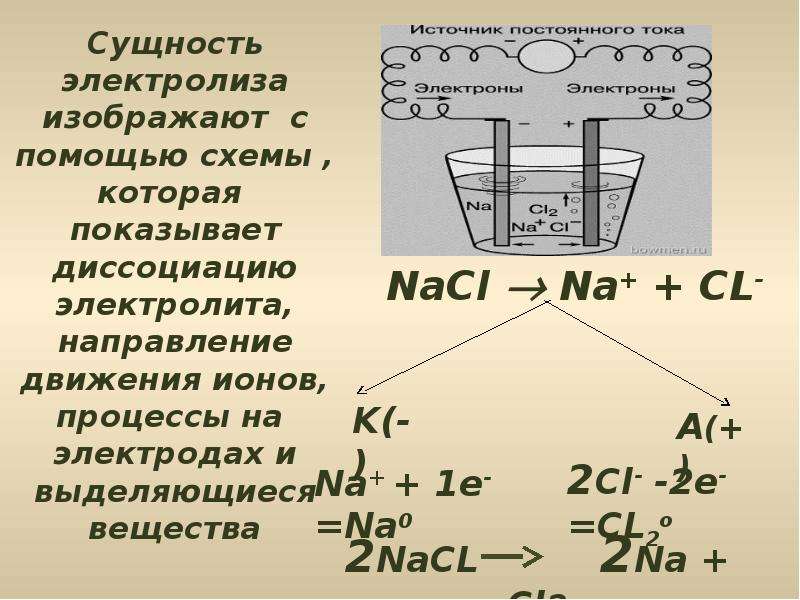
Общее содержание примесей в катодной меди обычно не превышает 0,05%, причем содержание каждой в отдельности выражается тысячными и десятитысячными долями процента. Эти примеси, как было указано выше, заносятся в катодный осадок в процессе электролиза в основном механически в виде анодного шлама и частично электролита, в связи с чем среди них находится также некоторое количество благородных металлов, обычно золота десятые доли грамма на тонну катодной меди и нисколько больше серебра (в зависимости от отношения его к золоту в анодной меди).
Чем лучше качество катодного осадка, плотнее его структура и глаже поверхность, тем он чище, меньше им захвачено шлама и электролита и совершеннее его отмывка.
Осаждению гладкого, плотного осадка меди способствует добавка в электротит поверхностно активных веществ и коллоидов: сульфитцеллюлозных щелоков (отходы бумажного производства), столярного клея, желатины, солидола, козеина и др. При исследовании факторов, улучшающих качество катодной меди при введении добавок, было выяснено, что наряду с кристаллохимическими особенностями здесь особую роль играют адсорбционные явления, приводящие к полной или к частичной пассивации катода.
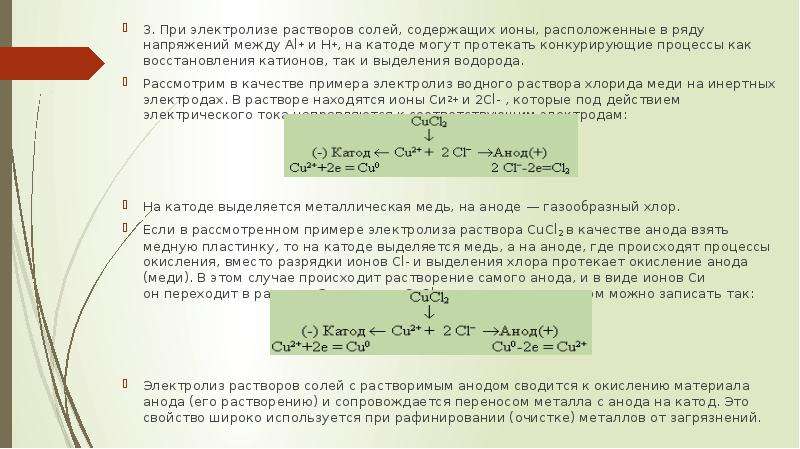
Работы А.И. Левина и T.H. Рогаткиной показали, что только определенные группы поверхностно активных веществ способствуют образованию на катоде мелкокристаллических осадков. Например, было выяснено, что тормозящий эффект при использовании технических продуктов, представляющих собой сложные смеси поверхностно активных агентов, всегда проявляется значительно сильнее, чем при использовании индивидуальных веществ. С увеличением концентрации добавки в растворе так заметно тормозится реакция, что наряду с разрядом ионов меди на катоде в некоторых случаях начинает выделяться водород. Экспериментальные данные показывают, что общая концентрация добавочных агентов, вводимых в электролит, должна находиться в определенных пределах, установленных практикой; при избытке добавки осадки получаются низкого ,качества: губчатые, полосчатые.
Рационализаторами Пышминского завода в 1957 г. был предложен измененный режим электролиза с целью получения более качественных осадков катодной меди и снижения удельного расхода электроэнергии.

Катоды, получаемые при измененном режиме электролиза, выгодно отличаются по качеству от обычных катодный осадок менее шишковатый и более плотный. Кроме того, в результате изменения режима расход электроэнергии снизился на 20%.
В целях интенсификации процесса электролиза на Пышминском заводе были проведены опыты по применению высоких плотностей тока, показавшие возможность применения плотности тока до 330 а/м2 с получением катодной меди, кондиционной по содержанию мышьяка и сурьмы и с нормальным содержанием благородных металлов. При указанной плотности тока напряжение ванны при благоприятных условиях составляет 0,42 в и расход электроэнергии 380 квт*ч на 1 т катодной меди.
Таким образом, применяемые в настоящее время плотности тока при электролитическом рафинировании меди не являются предельными, возможна значительная интенсификация .процесса без заметного ухудшения его показателей, но для этого требуется подбор оптимальных условий процесса (оптимального состава электролита, скорости его циркуляции, величины межэлектродного расстояния и т.
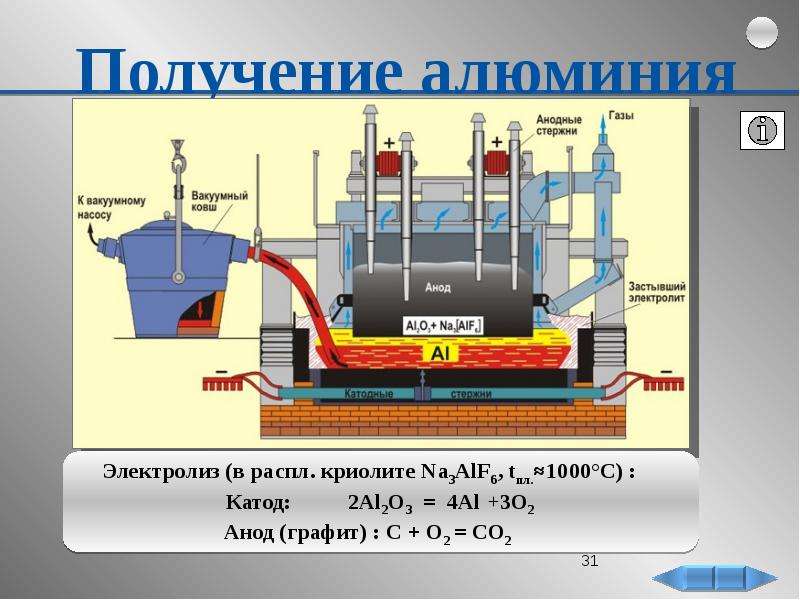
Дальнейшее улучшение качества катодной меди возможно в результате подбора и введения в электролит эффективно действующих поверхностно активных веществ, улучшения регенерации электролита и организации непрерывного фильтрования циркулирующего раствора через фильтр-прессы.
Материальный баланс по меди при электролитическом рафинировании
При составлении баланса по меди приняты данные Пышминского завода, пересчитанные на условную производительность 100 000 т катодной меди в год (табл. 35).
Потери меди вследствие утечки растворов обычно составляют 0,05—0,1% от веса поступающих на рафинирование анодов; выход шлама зависит от чистоты анодной меди и содержания благородных металлов и составляет 0,2—0,5%, иногда до 1% от веса анодов.
Очистка меди электролизом — Электролиз — GCSE Chemistry (Single Science) Revision — Other
Во время электролиза анод теряет массу по мере растворения меди, а катод набирает массу по мере осаждения меди.
Слайд-шоу показывает, что происходит во время очистки меди электролизом:
Очистка меди электролизом
1. Четыре иона Cu прикреплены к стержню справа, а четыре иона Cu² + плавают в пространстве между стержнями
2.Между стержнями подсоединена батарея, и ионы Cu притягиваются к левому стержню.
3. Теперь к левому стержню присоединены четыре иона Cu, а в середине — четыре иона Cu² +.
Полуравнение показывает, что происходит на одном из электродов при электролизе. Электроны показаны как e — .
1uuv3yon7ye.0.0.0.1:0.1.0.$0.$2.$4″> Это полууравнения:анод: Cu → Cu 2 + + 2e — (окисление)
катод: Cu 2 + + 2e — → Cu (восстановление )
Окисление происходит на аноде из-за потери электронов.Восстановление происходит на катоде, потому что электроны приобретаются.
Один из способов запомнить это — использовать мнемонику 0.1:0.1.0.$0.$2.$8.$1″> OIL RIG :
O xidation I s L oss электронов, R eduction I s G ain электронов.
МЕДЬ На этой странице рассказывается об извлечении меди из ее руд, ее очистке электролизом и некоторых ее применениях.Прежде чем вы слишком увязнете в добыче меди, убедитесь, что она вам нужна для любой учебной программы, которую вы используете. Извлечение меди из руд Метод, используемый для извлечения меди из ее руд, зависит от природы руды. Получение меди из халькопирита, CuFeS 2 Халькопирит (также известный как медный колчедан) и аналогичные сульфидные руды — самые распространенные руды меди.Руды обычно содержат низкое процентное содержание меди и должны быть сконцентрированы, например, с помощью пенной флотации перед рафинированием. | |
Примечание: Краткое описание пенной флотации вы найдете на странице «Введение в извлечение металлов». | |
Процесс Концентрированная руда сильно нагревается с помощью диоксида кремния (кремнезема), карбоната кальция и воздуха или кислорода в печи или нескольких печах.
Общее уравнение для этой серии шагов: Произведенный сульфид меди (I) превращается в медь при окончательной продувке воздухом. | |
Внимание! Это упрощенная версия процесса — попытка сжать все это до двух довольно простых уравнений. Проблема в том, что существует множество разновидностей этого извлечения.Один из них делает все в одной печи, и приведенные выше уравнения, вероятно, лучше всего представляют этот конкретный процесс. Это краткое изложение, вероятно, не подходит для чего-либо, кроме британского уровня A. | |
Конечный продукт этого продукта называется черновой медью — пористая хрупкая форма меди, примерно 98-99.5% чистота. Изучение окислительно-восстановительных процессов в этой реакции Стоит потратить некоторое время на выяснение того, какой восстанавливающий агент используется в этих реакциях, потому что на первый взгляд его нет! Или, если смотреть поверхностно, кажется, будто это кислород! Но это же глупо! | |
Примечание: Вы не сможете понять этот следующий бит, если у вас нет хороших практических знаний о степенях окисления (числах окисления).Если вы не уверены, либо перейдите по этой ссылке (что может занять некоторое время), либо полностью пропустите этот бит, если вам это не нужно. ![]() Если вы решите перейти по этой ссылке, используйте кнопку НАЗАД в браузере, чтобы вернуться на эту страницу позже. | |
Я могу смотреть только на вторую реакцию, потому что это единственная реакция, в которой я могу быть уверен. Давайте посмотрим на степень окисления всего.
Это означает, что и медь, и кислород были восстановлены (снижение степени окисления). Сера окислилась (степень окисления увеличилась). Таким образом, восстановителем является ион сульфида в сульфиде меди (I). С другой реакцией справиться труднее, потому что вы не можете определить все степени окисления, следуя простым правилам — слишком много переменных в некоторых веществах. В литературе также существуют очевидные разногласия относительно того, содержит ли халькопирит Cu (II) и Fe (II) или Cu (I) и Fe (III). Я не чувствую себя достаточно квалифицированным, чтобы идти дальше с этим. | |
Примечание: До тех пор, пока я не добавил вопросы в июле 2015 года, я всегда предполагал (без веских доказательств — никогда не было хорошей идеей!), Что халькопирит содержит медь и железо в степени окисления +2 — но это вполне может быть неверным. . Если это правда, то вы можете показать, что сульфид-ионы восстанавливают Cu (II) до Cu (I). Однако, если медь изначально была в состоянии +1, то сульфид-ионы восстанавливают Fe (III) до Fe (II). Из-за неуверенности я только что удалил абзацы об этом. В любом случае об этом не следует спрашивать на этом уровне. | |
Извлечение меди из других руд Медь может быть извлечена из несульфидных руд другим способом, включающим три отдельные стадии:
Очистка меди Когда медь получают из сульфидных руд первым способом, описанным выше, она не чистая.Черновая медь сначала обрабатывается, чтобы удалить оставшуюся серу (уловленную в виде пузырьков диоксида серы в меди — отсюда «черновая медь»), а затем отливается в аноды для рафинирования с помощью электролиза. Электролитическое рафинирование При очистке используется электролит из раствора сульфата меди (II), загрязненные медные аноды и полоски меди высокой чистоты для катодов. На схеме показан очень упрощенный вид ячейки. На катоде ионы меди (II) осаждаются в виде меди. На аноде медь переходит в раствор в виде ионов меди (II). На каждый ион меди, который осаждается на катоде, в принципе переходит в раствор на аноде. Концентрация раствора должна оставаться прежней. Все, что происходит, — это перенос меди с анода на катод. На практике это не так просто из-за примесей. Что происходит с примесями? Любой металл в загрязненном аноде, который ниже меди в электрохимическом ряду (ряду реактивности), не переходит в раствор в виде ионов. Он остается как металл и падает на дно электролизера в виде «анодного шлама» вместе с любыми инертными материалами, оставшимися от руды. Анодный шлам будет содержать ценные металлы, такие как серебро и золото. Металлы выше меди в электрохимическом ряду (например, цинк) будут образовывать ионы на аноде и переходить в раствор. Однако они не будут разряжаться на катоде, если их концентрация не станет слишком высокой. Концентрация ионов, таких как цинк, со временем будет увеличиваться, а концентрация ионов меди (II) в растворе будет падать. Очевидно, что на каждый ион цинка, переходящий в раствор, образуется на один ион меди меньше. Для компенсации этого раствор сульфата меди (II) необходимо постоянно очищать. | |
Примечание: Если для вас не очевидно, что на каждый ион цинка, переходящий в раствор, будет на один ион меди меньше, подумайте об этом так. Для каждого иона меди, который осаждается в виде металлической меди на катоде, два электрона должны протекать по цепи. Откуда они? По сути, их снабжение — это работа анода.Они высвобождаются там, когда атомы меди или цинка теряют электроны и переходят в раствор в виде ионов. Затем источник питания перекачивает их по внешней цепи к катоду. Итак, чтобы нанести один ион меди на катод, нужно два электрона. Они могут поставляться или за счет ионизации атома цинка на аноде или за счет ионизации атома меди — для этого не требуется одновременно . Это означает, что на каждый дополнительный ион цинка, попадающий в раствор, будет приходиться на один ион меди меньше. | |
Применение меди В том числе медь используется для:
В меню извлечения металла. В меню «Неорганическая химия». . . В главное меню. . . © Джим Кларк 2005 (изменено в июле 2015 г.) |
Непрерывный процесс электролитического рафинирования катодной меди с не растворяющимся анодом
Основные моменты
- •
Нерастворяющийся электрод использовался в качестве анода при электролитическом рафинировании.
- •
Порошок CuO был добавлен для поддержания концентрации Cu 2+ в электролите.
- •
Систематически проанализировано влияние трех электролитов на электролитический процесс.
- •
После использования измененных параметров и технологии электролит можно утилизировать.
Реферат
В традиционном промышленном производстве катодную медь получают совместно пирометаллургическим способом и методом мокрого электролитического рафинирования. В этой работе не растворяющийся электрод из диоксида свинца использовался в качестве анода в эксперименте по электролизу, а оксид меди был добавлен для поддержания концентрации ионов меди в электролите, чтобы улучшить качество катодной меди и выход по току в электролитической меди. обработать.Этот метод позволяет избежать потребления энергии в пирометаллургическом процессе. Проанализировано влияние трех видов электролитов на макроскопическую морфологию, микроструктуру, выход по току, чистоту и кристаллический состав катодной меди. В эксперименте по электролизу фазы Cu 2 O и CuO наблюдались в катодной меди при использовании электролита А в течение длительного времени. При использовании электролита Б чистота продуктов не соответствовала стандарту катодной меди.При использовании электролита С продукты, полученные электролизом четыре раза по 8 или 2 часа каждый раз, соответствовали стандартам морфологии, эффективности по току и чистоты. Средняя эффективность электролиза в течение 8 часов составила 96,33% с новым нерастворенным анодом, что на 2,58% выше, чем у традиционного растворенного анода.
Более того, электролит может быть переработан после использования с улучшенным электролитом и технологическим процессом. Этот новый процесс может сэкономить энергию и снизить расход материалов для производства меди в гидрометаллургической промышленности.Кроме того, в этой статье предлагается новый метод повышения эффективности по току и качества продукции в электролитическом процессе промышленного производства металлов.
Графический реферат
В традиционном промышленном производстве катодную медь получают совместно пирометаллургическим способом и методом мокрого электролитического рафинирования. В этой работе не растворяющийся электрод из диоксида свинца использовался в качестве анода в эксперименте по электролизу, а оксид меди был добавлен для поддержания концентрации ионов меди в электролите, чтобы улучшить качество катодной меди и выход по току в электролитической меди. обработать.Средняя эффективность электролиза в течение 8 часов составила 96,33% с новым нерастворенным анодом, что на 2,58% выше, чем у традиционного растворенного анода. Более того, электролит может быть переработан после использования с измененными параметрами и технологией. Этот новый процесс может сэкономить энергию и снизить расход материалов для производства меди в гидрометаллургической промышленности. Кроме того, в этой статье предлагается новый метод повышения эффективности по току и качества продукции в электролитическом процессе промышленного производства металлов.
- Загрузить: Загрузить изображение в высоком разрешении (125KB)
- Загрузить: Загрузить полноразмерное изображение
Ключевые слова
Электролитическое рафинирование
Катодная медь
Нерастворяющийся анод
Эффективность тока
Рекомендуемые статьи статьи (0)
Полный текст© 2019 Elsevier Ltd. Все права защищены.
Рекомендуемые статьи
Ссылки на статьи
Новый способ извлечения меди | MIT News
Исследователи Массачусетского технологического института определили подходящую температуру и химическую смесь для избирательного отделения чистой меди и других металлических микроэлементов от минералов на основе серы с помощью электролиза в расплаве. Этот одностадийный экологически чистый процесс упрощает производство металла и устраняет токсичные побочные продукты, такие как диоксид серы.
Постдоктор Сулата К. Саху и аспирант Брайан Дж. Хмеловец ’12 разложили богатые серой минералы на чистую серу и извлекли три разных металла очень высокой степени чистоты: медь, молибден и рений. Они также количественно оценили количество энергии, необходимое для запуска процесса экстракции.
Электролизная ячейка представляет собой замкнутую цепь, как аккумулятор, но вместо выработки электроэнергии он потребляет электрическую энергию для разделения соединений на их элементы, например, для разделения воды на водород и кислород.Такие электролитические процессы являются основным методом производства алюминия и используются в качестве заключительного этапа для удаления примесей при производстве меди. Однако, в отличие от алюминия, нет никаких процессов прямого электролитического разложения медьсодержащих сульфидных минералов для получения жидкой меди.
Исследователи Массачусетского технологического института нашли многообещающий метод образования жидкой металлической меди и серного газа в своей ячейке из электролита, состоящего из сульфида бария, сульфида лантана и сульфида меди, с выходом более 99.9 процентов чистой меди. Эта чистота эквивалентна лучшим современным методам производства меди. Их результаты опубликованы в статье Electrochimica Acta со старшим автором Антуаном Алланором, доцентом кафедры металлургии.
Одношаговый процесс
«Это одностадийный процесс, в котором сульфид непосредственно разлагается на медь и серу. Другие предыдущие методы состоят из нескольких шагов », — объясняет Саху. «Принимая этот процесс, мы стремимся снизить стоимость.”
Медь пользуется растущим спросом для использования в электромобилях, солнечной энергии, бытовой электронике и других целях повышения энергоэффективности. Большинство современных процессов добычи меди сжигают сульфидные минералы в воздухе, в результате чего образуется двуокись серы, вредный загрязнитель воздуха, который необходимо улавливать и перерабатывать, но новый метод производит элементарную серу, которую можно безопасно повторно использовать, например, в удобрениях. Исследователи также использовали электролиз для получения рения и молибдена, которые часто встречаются в сульфидах меди в очень небольших количествах.
Новая работа основывается на статье , опубликованной в журнале The Electrochemical Society за 2016 год, , предлагающей доказательства электролитического извлечения меди, авторами которых являются Самира Соханваран, Санг-Квон Ли, Гийом Ламботт и Алланор. Они показали, что добавление сульфида бария к расплаву сульфида меди подавляет электрическую проводимость сульфида меди в достаточной степени для извлечения небольшого количества чистой меди из высокотемпературной электрохимической ячейки, работающей при температуре 1105 градусов по Цельсию (2021 по Фаренгейту).Соханваран в настоящее время является научным сотрудником компании Natural Resources Canada-Canmet Mining; Ли — старший научный сотрудник Корейского научно-исследовательского института атомной энергии; Ламботт в настоящее время является старшим инженером-исследователем в Boston Electrometallurgical Corp.
«Эта статья была первой, которая показала, что вы можете использовать смесь, в которой предположительно электронная проводимость преобладает над проводимостью, но на самом деле нет 100%. Есть крошечная ионная фракция, которая достаточно хороша для производства меди », — объясняет Алланор.
«Новая статья показывает, что мы можем пойти дальше и сделать его почти полностью ионным, то есть снизить долю электронной проводимости и, следовательно, повысить эффективность производства металла», — говорит Алланор.
Эти сульфидные минералы представляют собой соединения, в которых металл и элементы серы имеют общие электроны. В расплавленном состоянии ионы меди лишены одного электрона, что дает им положительный заряд, а ионы серы несут два дополнительных электрона, что дает им отрицательный заряд.Желаемая реакция в электролизной ячейке заключается в образовании элементарных атомов путем добавления электронов к металлам, таким как медь, и отбору электронов у серы. Это происходит, когда дополнительные электроны вводятся в систему под действием приложенного напряжения. Ионы металла реагируют на катоде, отрицательно заряженном электроде, где они приобретают электроны в процессе, называемом восстановлением; тем временем отрицательно заряженные ионы серы реагируют на аноде, положительно заряженном электроде, где они отдают электроны в процессе, называемом окислением.
В ячейке, в которой использовался только сульфид меди, например, из-за его высокой электронной проводимости, дополнительные электроны просто протекали бы через электролит, не взаимодействуя с отдельными ионами меди и серы на электродах, и разделения не происходило бы. Исследователи Allanore Group успешно идентифицировали другие сульфидные соединения, которые при добавлении к сульфиду меди изменяют поведение расплава, так что ионы, а не электроны, становятся первичными носителями заряда в системе и, таким образом, обеспечивают желаемые химические реакции.С технической точки зрения, добавки увеличивают ширину запрещенной зоны сульфида меди, поэтому он больше не проводит электронное соединение, объясняет Хмеловец. Доля электронов, участвующих в реакциях окисления и восстановления, измеряемая как процент от общего тока, то есть общего потока электронов в ячейке, называется ее фарадеевской эффективностью.
Удвоение эффективности
Новая работа удваивает эффективность электролитического извлечения меди, о которой сообщалось в первой статье, которая составляла 28 процентов с электролитом, где к сульфиду меди был добавлен только сульфид бария, до 59 процентов во второй статье с добавлением сульфида лантана и сульфида бария. к сульфиду меди.
«Демонстрация того, что мы можем проводить фарадеевские реакции в жидком сульфиде металла, является новинкой и может открыть дверь для изучения множества различных систем», — говорит Хмеловец. «Это работает не только с медью. Мы смогли производить рений и молибден ». Рений и молибден являются промышленно важными металлами, которые, например, используются в двигателях реактивных самолетов. Лаборатория Алланора также использовала электролиз в расплаве для производства цинка, олова и серебра, но свинец, никель и другие металлы возможны, считает он.
Количество энергии, необходимое для запуска процесса разделения в электролизной ячейке, пропорционально фарадеевской эффективности и напряжению ячейки. Для воды, которая была одним из первых соединений, разделенных электролизом, минимальное напряжение ячейки или энергия разложения составляет 1,23 вольт. Саху и Хмеловец определили напряжение в своей ячейке как 0,06 вольт для сульфида рения, 0,33 вольта для сульфида молибдена и 0,45 вольт для сульфида меди. «Для большинства наших реакций мы применяем 0.5 или 0,6 вольт, так что три сульфида вместе восстанавливаются до металла, рения, молибдена и меди », — поясняет Саху. При рабочей температуре элемента и приложенном потенциале от 0,5 до 0,6 вольт система предпочитает разлагать эти металлы, потому что энергия, необходимая для разложения сульфида лантана — около 1,7 вольт — и сульфида бария — около 1,9 вольт, — сравнительно намного выше. Отдельные эксперименты также доказали способность селективно восстанавливать рений или молибден без восстановления меди из-за их разной энергии разложения.
Промышленный потенциал
Важные стратегические и товарные металлы, включая медь, цинк, свинец, рений и молибден, обычно находятся в сульфидных рудах и реже в рудах на основе оксидов, как в случае алюминия. «Обычно их сжигают на воздухе, чтобы удалить серу, но при этом вы производите SO 2 [диоксид серы], и никому не разрешается выпускать его прямо в воздух, поэтому они должны каким-то образом улавливать его. «Улавливание SO 2 и его преобразование в серную кислоту сопряжено с большими капитальными затратами», — поясняет Хмеловец.
Самый близкий производственный процесс к электролитическому извлечению меди, который они надеются увидеть, — это производство алюминия с помощью электролитического процесса, известного как процесс Холла-Эру, который дает ванну расплавленного металлического алюминия, который можно непрерывно выпускать. «Идеальным вариантом является запуск непрерывного процесса», — говорит Хмелёвец. «Итак, в нашем случае вы должны поддерживать постоянный уровень жидкой меди, а затем периодически отбирать ее из электролизной ячейки. Для алюминиевой промышленности в это было вложено много инженерных разработок, так что мы надеемся воспользоваться этим.”
Саху и Хмеловец провели свои эксперименты при температуре 1227 ° C, что примерно на 150 ° C выше точки плавления меди. Это температура, обычно используемая в промышленности для извлечения меди.
Дальнейшие улучшения
Системы электролиза алюминия работают с 95-процентной фарадеевской эффективностью, поэтому есть возможности для улучшения по сравнению с заявленной исследователями 59-процентной эффективностью. По словам Саху, для повышения эффективности их ячеек им, возможно, потребуется изменить конструкцию ячеек, чтобы извлечь большее количество жидкой меди.Электролит также можно дополнительно настроить, добавив сульфиды, кроме сульфида бария и сульфида лантана. «Не существует единого решения, которое позволило бы нам это сделать. Это будет оптимизация, чтобы переместить его в более крупный масштаб », — говорит Хмеловец. Эта работа продолжается.
Саху, 34 года, получила докторскую степень по химии в Мадрасском университете в Индии. 27-летний Хмеловец, аспирант второго курса и научный сотрудник Салапатаса в области материаловедения и инженерии, получил степень бакалавра химической инженерии в Массачусетском технологическом институте в 2012 году и степень магистра химической инженерии в Калифорнийском технологическом институте в 2014 году.
Работа вписывается в работу Allanore Group по высокотемпературным расплавленным материалам, включая недавние открытия в разработке новых формул для предсказания полупроводимости в расплавленных соединениях и демонстрацию расплавленного термоэлектрического элемента для производства электричества из промышленных отходов тепла. Allanore Group ищет патенты на определенные аспекты процесса добычи.
Произведения новые и значимые
«Используя разумный подход к химическому процессу, эти исследователи разработали совершенно новый способ производства меди», — говорит Рохан Аколкар, специалист F. Алекс Нейсон, адъюнкт-профессор химической и биомолекулярной инженерии в Университете Кейс Вестерн Резерв, который не принимал участия в этой работе. «Исследователи разработали процесс, в котором есть много ключевых ингредиентов — это более чистый, масштабируемый и простой одностадийный процесс производства меди из сульфидной руды».
«С технологической точки зрения авторы осознают необходимость сделать процесс более эффективным при сохранении внутренней чистоты производимой меди», — говорит Аколкар, посетивший лабораторию Allanore в конце прошлого года.«Если технология получит дальнейшее развитие и ее технико-экономические показатели будут выглядеть благоприятными, то это может стать потенциальным путем для более простого и чистого производства металлической меди, что важно для многих приложений». Аколкар отмечает, что «качество этой работы отличное. Исследовательская группа Allanore в Массачусетском технологическом институте находится в авангарде продвижения исследований электролиза расплавленных солей ».
Профессор химического машиностроения Рочестерского университета Джейкоб Хорне говорит: «Текущие процессы экстракции включают несколько этапов и требуют больших капиталовложений, поэтому дорогостоящие улучшения запрещены.Прямой электролиз сульфидных руд металлов также выгоден, поскольку он устраняет образование диоксида серы, загрязнителя кислотных дождей. «
«Электрохимия и термодинамика расплавленных солей сильно отличаются от водных [водных] систем, и исследование Алланора и его группы демонстрирует, что многие хорошие химические методы игнорировались в прошлом из-за нашей рабской преданности воде. — предлагает Хорне. «Прямой электролиз металлических руд открывает путь к возрождению металлургии, когда могут быть реализованы новые открытия и процессы, которые могут модернизировать стареющую добывающую промышленность и повысить ее энергоэффективность.Новый подход может быть применен к другим металлам, имеющим большое стратегическое значение, таким как редкоземельные металлы ».
Эта работа была поддержана Norco Conservation и Управлением военно-морских исследований.
Принцип электролиза медного сульфатного электролита
Электролиз
Электролиз — это электрохимический процесс, при котором ток проходит от одного электрода к другому в ионизированном растворе, который является электролитом. В этом процессе положительные ионы или катионы попадают на отрицательный электрод или катод, а отрицательные ионы или анионы — на положительный электрод или анод.
Прежде чем понять принцип электролиза , мы должны знать, что такое электролит или определение электролита
Определение электролита
Электролит — это такое химическое вещество, атомы которого прочно связаны друг с другом ионными связями, но когда мы растворяемся В воде его молекулы расщепляются на положительные и отрицательные ионы. Положительно заряженные ионы называются катионами, а отрицательно заряженные ионы — анионами. И катионы, и анионы свободно перемещаются в растворе.
Принцип электролиза
В ионных связях один атом теряет свои валентные электроны, а другой атом приобретает электроны. В результате один атом становится положительно заряженным ионом, а другой атом становится отрицательным. Из-за противоположного заряда оба притягиваются друг к другу и образуют связь между собой, называемую ионной связью. В ионной связи сила, действующая между ионами, является кулоновской силой, которая обратно пропорциональна диэлектрической проницаемости среды. Относительная диэлектрическая проницаемость воды составляет 80 при 20 o C.Таким образом, когда любое химическое соединение с ионной связью растворяется в воде, сила связи между ионами становится намного слабее, и, следовательно, его молекулы расщепляются на катионы и анионы, свободно перемещающиеся в растворе.
Теперь мы погрузим два металлических стержня в раствор и приложим разность электрических потенциалов между стержнями снаружи с помощью батареи.
Эти частично погруженные стержни технически называются электродами. Электрод, соединенный с отрицательной клеммой батареи, известен как катод, а электрод, соединенный с положительной клеммой батареи, известен как анод.Свободно движущиеся положительно заряженные катионы притягиваются катодом, а отрицательно заряженные анионы притягиваются анодом. В катоде положительные катионы забирают электроны с отрицательного катода, а на аноде отрицательные анионы отдают электроны положительному аноду. Для непрерывного приема и передачи электронов в катод и анод, соответственно, должен быть поток электронов во внешней цепи электролита. Это означает, что ток продолжает циркулировать по замкнутому контуру, создаваемому батареей, электролитом и электродами.Это самый основной принцип электролиза .
Электролиз сульфата меди
Всякий раз, когда сульфат меди или CuSO 4 добавляется в воду, он растворяется в воде. Поскольку CuSO 4 является электролитом, он расщепляется на ионы Cu + + (катион) и SO 4 — — (анион) и свободно перемещаются в растворе.
Теперь мы погрузим в этот раствор два медных электрода.
Ионы Cu + + (катион) будут притягиваться к катоду i.е. электрод подключен к отрицательной клемме аккумулятора. Попадая на катод, каждый ион Cu + + забирает у себя электроны и становится нейтральным атомом меди.
Аналогичным образом ионы SO 4 — — (анион) будут притягиваться анодом, то есть электродом, подключенным к положительной клемме батареи. Итак, ионы SO 4 — — будут двигаться к аноду, где они отдают два электрона и превращаются в радикал SO 4 .
Но поскольку радикал SO 4 не может существовать в электрически нейтральном состоянии, он атакует медный анод и образует сульфат меди.
В описанном выше процессе после захвата электронов нейтральные атомы меди осаждаются на катоде. В то же время SO 4 реагирует с медным анодом и превращается в CuSO 4 , но в воде он не может существовать в виде отдельных молекул, вместо этого CuSO 4 расщепится на Cu + + , SO 4 — — и растворить в воде. Таким образом, можно сделать вывод, что при электролизе сульфата меди с помощью медных электродов медь осаждается на катоде и такое же количество меди удаляется с анода.Если при электролизе сульфата меди мы будем использовать угольный электрод вместо медных или других металлических электродов, то реакции электролиза будут немного другими. На самом деле SO 4 не может реагировать с углеродом, и в этом случае SO 4 будет реагировать с водой в растворе с образованием серной кислоты и высвобождением кислорода.
Описанный выше процесс известен как электролиз .
Видео-презентация основных принципов электролиза
Учебное пособие по химическому рафинированию
Электролитическое рафинирование меди
На стадии электролитического рафинирования при производстве меди в резервуаре подвешивают ряд загрязненных медных анодов и тонких стартовых катодов (таких как тонкая медная фольга).
Электролит, содержащий ионы меди, протекает через резервуар. Электролит часто представляет собой медь, растворенную в серной кислоте, которая дает водный раствор ионов меди.
Внешний источник питания используется для вытягивания электронов из анода и подталкивания их к катоду.
На анимации ниже представлена одна из этих электролитических ячеек, использующая водный раствор Cu 2+ в качестве электролита.
Анод (положительный электрод)
| Катод (отрицательный электрод)
|
Примечание: H + из электролита не восстанавливается до H 2 (г) на катоде.
Cu 2+ находится ниже H + в таблице стандартных восстановительных потенциалов.
Cu 2+ — более сильный окислитель, чем H + .
Cu 2+ восстанавливается легче, чем H + .
анодная реакция: | Cu (т) | → | Cu 2+ (водн.) + |
катодная реакция: | Cu 2+ (водн.) + | → | Cu (т) |
общая реакция: | Cu (с) + Cu 2+ (водн.![]() | → | Cu 2+ (водн.) + Cu (s) |
Обратите внимание, что концентрация ионов меди в электролите остается постоянной. Для каждого иона меди, образующегося на катоде, ион меди восстанавливается до металлической меди на катоде. |
Некоторые из примесей, которые содержатся в нечистой меди, — это серебро, золото и свинец.
Каждый из этих металлов имеет коммерческую ценность, поэтому их стоит собирать из резервуаров для очистки.
Серебро и золото находятся ниже меди в таблице стандартных электродных потенциалов, поэтому они являются более слабыми восстановителями, чем медь, и не окисляются на аноде.Они будут найдены в слизи на дне резервуара.
Свинец встречается выше меди в таблице стандартных восстановительных потенциалов, поэтому свинец является более сильным восстановителем, чем медь, и будет окисляться на аноде:
Pb (с) → Pb 2+ (водн. ) + 2e —
Однако свинец образует нерастворимый осадок с ионами сульфата в электролите:
Pb 2+ (водн.) + SO 4 2- (водн.) → PbSO 4 (с)
PbSO 4 (s) можно найти в иле на дне резервуара.
Электролиз раствора сульфата меди (II) | Эксперимент
Этот эксперимент в классе может быть проведен учащимися, работающими парами или тройками.
Оборудование
Аппарат
- Защита глаз
- Стакан, 250 см 3
- Графитовые электроды, диаметр около 5 мм, 2 шт.
- Стойка реторты и зажим для удержания электродов (примечание 1)
- Источник питания постоянного тока, 6 В
- Лампочка, малая, 6 В, 5 Вт (опция; примечание 2)
- Поводки и зажимы типа крокодил
Примечания к аппаратуре
- Есть несколько способов закрепления графитовых электродов.
Пожалуй, наиболее удобно использовать подставку для реторты и зажим. Их также можно прикрепить с помощью Blutac на небольшую деревянную полоску, лежащую на вершине стакана.
- В цепь можно включить лампочку, чтобы указать, что есть ток.
Химия
- Водный сульфат меди (II), около 0,5 M, 200 см 3
- Медные полосы x2 (необязательно; их можно использовать вместо графитовых стержней в качестве дополнения к основному эксперименту)
- Мелкие кусочки наждачной бумаги
Примечания по технике безопасности, охране труда и технике безопасности
- Прочтите наше стандартное руководство по охране труда и технике безопасности.
- Используйте защитные очки. Студенты должны мыть руки по окончании всех практических занятий.
- Раствор сульфата меди (II), CuSO 4 (водн.) — см. CLEAPSS Hazcard HC027c и книгу рецептов CLEAPSS RB031. При предлагаемых концентрациях раствор сульфата меди (II) является НИЗКОЙ ОПАСНОСТЬЮ.
Если концентрации увеличиваются, растворы должны иметь правильные предупреждения об опасности. Раствор сульфата меди (II) ВРЕДНО, если его концентрация равна или больше 1 М.
Процедура
Показать в полноэкранном режимеУчебные заметки
Учащиеся должны увидеть на катоде отложение меди. Часто он будет рассыпчатым и неравномерным. Вы должны объяснить, что если сила тока намного меньше, то твердое покрытие будет блестящим, непроницаемым и его очень трудно стереть; этот процесс лежит в основе гальваники.
На аноде образуются пузырьки газа (кислорода).
Катодная реакция: Cu 2+ (водн.) + 2e — → Cu (s)
Анодная реакция: 2H 2 O (л) → O 2 (г) + 4H + (водн.) + 4e —
В случае угольных (графитовых) электродов кислород обычно реагирует с анодом с образованием CO 2 .Если для электродов используется медь, медный анод растворяется. Реакция противоположна катодной.
Результаты этого эксперимента могут привести к дискуссии о гальванике и электролитическом рафинировании меди.
Может быть поучительным разрешить учащимся покрыть медью металлические предметы, поставляемые школой и предварительно проверенные на их пригодность. Личные вещи использовать нельзя. Во многих случаях альтернативная окислительно-восстановительная реакция часто имеет место до того, как действительно будет пропущен ток.Это происходит, например, с изделиями из металлов выше меди в ряду реактивности. Разумно не усложнять электролитическое осаждение химическим вытеснением — ценные изделия могут быть испорчены.
Расширенные эксперименты по рафинированию меди- После проведения электролиза, как описано выше, электроды можно поменять местами. Затем студенты могут увидеть, как медь исчезает с поверхности покрытого медью анода:
Cu (s) → Cu 2+ (водный) + 2e —
Это приводит к обсуждению того, почему во время электролитического рафинирования :
- анод состоит из неочищенного образца металла;
- катод изготовлен из чистой меди или металлической основы, такой как нержавеющая сталь.