Электролизер PR2 — гарантия качества, по лучшей цене 650 руб.
Прибор для измерения качества воды
Электролизер позволяет наглядно показать разницу между исходной водой из крана и очищенной.
Металлические и алюминиевые электроды посылают электрические разряды через воду. Этот разряд приводит ионы в воде в нестабильное состояние. Происходит электрохимическая реакция, в результате которой растворенные в воде загрязнения начинают оседать на электродах.
Вода с большим содержанием примесей будет более подвержена реакции и станет темней. Вода, пропущенная через осмос, станет желтоватой, показывая, что содержание вредных веществ меньше. Абсолютно чистая вода (дистиллят или 5-6 стадийный осмос) останется чистой. Таким образом, легко наглядно продемонстрировать качество потребляемой воды.
Использование:
- Наполните 2 стакана водой: один с исходной водой, второй – с очищенной.
- Предварительно проверьте солесодержание исходной воды TDS-метром.
- Извлеките электролизер из чехла.
- Опустите первую пару контактов в один стакан, вторую – во второй.
- Включите электролизер в сеть.
- Включите устройство.
- Следите за изменениями в стакане с исходной водой.
- Когда изменения будут видны невооруженным глазом, отключите аппарат.
- По окончанию демонстрации извлеките из воды контакты электролизера.
- ВНИМАНИЕ: протрите железные контакты салфеткой или бумажным полотенцем, сразу как извлечете контакты из воды. В противном случае отложения на контактах потом будет трудно удалить.
ОСТОРОЖНО! НИКОГДА не касайтесь контактов электролизера, если он включен в сеть.
Часто задаваемые вопросы:
Что такое электролиз?
Растворенные в воде частицы можно осадить с помощью процесса, который называется электролизом. Суть процесса заключается в пропускании электрического тока через воду, в результате на концах электролизера начнут осаждаться растворенные в ней вещества.
Вода после электролизера такая же как из крана?
Нет. При работе электролизера меняется химический состав воды, то же самое происходит при замораживании или кипячении воды. Самое главное – насколько изменилась вода после электролизера. Чем чище была вода, тем меньше она будет подвержена реакции.
Можно ли назвать электролизер тестом?
Нет. Это всего лишь инструмент для наглядной демонстрации химического загрязнения воды.
Выпавший осадок это части контактов?
Нет. Все что выпадает в осадок в ходе демонстрации — растворенные в воде вещества. В качестве доказательства вы можете поменять местами контакты чистой и исходной воды местами – результат будет одинаковый.
Спецификация:
- Размер (ДхШхВ): 102х99х24 мм
- Источник питания: 220В
- Предохранитель: 250В, 2А
- Максимальное солесодержание: 500 мг/л
- Вес: 207 г
Внешний вид и цвет товара могут отличаться от изображения.
Производитель оставляет за собой право вносить изменения в комплектацию и конструкцию изделия с целью улучшения его свойств.
Наш магазин предлагает большой ассортимент измерителей и анализаторов.
Приобрести электролизер Вы можете у нас в магазине или оформляйте заказ на сайте.
Добейтесь повышения энергетической эффективности с помощью модуля «Топливные ячейки и электролизёры»
Водородные топливные элементы
В модуле «Топливные ячейки и электролизёры» представлены готовые математические модели для наиболее распространённых типов водородных топливных элементов, которые описывают процессы в электродах, электролитах, а также коллекторах тока и фидерах. Можно моделировать такие типы топливных элементов, как ТЭТПЭ, ЩТЭ, ТЭРКЭ, ТОТЭ и высокотемпературные топливные элементы, и этот список можно продолжить.
Моделирование применяется для анализа распределения электрического тока и потенциала, поля температуры и концентрации химических веществ в топливном элементе. Полученные результаты анализа помогут спроектировать электрохимическую ячейку с наилучшими показателями эффективности и экономичности для заданных условий эксплуатации. В качестве важных факторов, которые приводят к снижению эффективности и сокращению срока службы электрохимических систем, можно выделить накопление воды в ячейке и неравномерное использование активной поверхности, и эти факторы можно исследовать с помощью моделирования. Кроме того, расчётная модель позволяет проанализировать влияние различных микромасштабных факторов, таких как наличие катализатора, распределение частиц по размерам и бимодальное распределение пор, на процессы в газодиффузионных электродах и в активных каталитических слоях.
Расчётные модели позволяют анализировать стационарные и переходные процессы в областях разной пространственной размерности, начиная с нульмерных и заканчивая полноразмерными трёхмерными. Кроме того, для моделирования спектроскопии электрохимического импеданса задачи могут быть сформулированы для решения в частотной области.
Водные электролизёры
Снижение себестоимости ветряной и солнечной электроэнергии привело к увеличению производства электроэнергии в отдаленных районах, ёмкость энергосети которых может быть ограничена. Это означает, что сеть не может потреблять всю вырабатываемую электроэнергию, когда дует ветер и светит солнце. В этом случае могут помочь электролизёры, которые будут расходовать избыток электроэнергии для производства водорода методом электролиза воды. Произведённый таким образом водород можно аккумулировать, чтобы затем использовать его в качестве топлива для генерации электричества в топливных элементах, когда появится спрос со стороны потребителей энергосети.
Конструкция электролизёров воды идентична конструкции водородных топливных элементов. Различаются эти устройства направлением протекающих в них процессов: в топливном элементе катод является положительно заряженным электродом, а в электролизёре — отрицательно. Математические модели, включенные в состав модуля «Топливные ячейки и электролизёры», описывают процессы в газодиффузионных электродах, активных каталитических слоях, электролитических сепараторах и биполярных пластинах с газовыми каналами. Можно строить расчётные модели как для отдельных электролизных ячеек, так и для целого стека. Расчётные модели электролизёров позволяют анализировать стационарные и переходные процессы в областях разной пространственной размерности, начиная с нульмерных и заканчивая полноразмерными трёхмерными.
Промышленные электролизёры
Функциональные возможности модуля «Топливные ячейки и электролизёры» не ограничены моделированием только электролиза воды. Инструменты модуля позволяют смоделировать электрохимическую ячейку или электролизёр любого типа. В том числе можно анализировать процессы образования газовой фазы и ламинарное течение многофазной среды. Для анализа турбулентных течений в хлоратных или хлорно-щелочных мембранных электролизёрах можно подключить модуль «Вычислительная гидродинамика».
Repsol запустит 1-й электролизер на своем НПЗ в Стране Басков | Нефтепереработка
Витория, 20 сен — ИА Neftegaz.RU. Крупнейшая нефтегазовая компания Испании Repsol запустит во 2й половине 2022 г. 1й электролизер на своем нефтеперерабатывающем заводе (НПЗ) Petronor в Стране Басков.Об этом сообщает пресс-служба Repsol.
Объект будет иметь мощность 2,5 МВт.
Для реализации проекта компания выделит 8,9 млн евро.
Эти средства будут направлены в том числе на строительство инфраструктуры для использования и распределения произведенного «зеленого» водорода.
Электролизер будет обслуживать не только НПЗ Petronor, но и различные объекты, расположенные в близлежащем технопарке Parque Tecnológico de la Margen Izquierda в муниципалитете Абанто-и-Зиербена, в том числе Энергетический интеллектуальный центр и 1
Данный проект будет реализован в рамках Баскского водородного коридора (BH2C).
Отметим, он был запущен в феврале 2021 г. компанией Petronor-Repsol.
Его целью является консолидация интегрированной системы региона вокруг водородной производственно-сбытовой цепочки.
К настоящему времени он объединил уже порядка 130 компаний.
Repsol является 1м производителем и 1м потребителем водорода в Испании.
Как правило, компания использует водород для своих промышленных нужд.
Во время презентации своего стратегического плана на 2021-2025 гг. она объявила, что производство «зеленого» водорода является одной из ее стратегических целей для достижения углеродной нейтральности к 2050 г.
Сегодня Repsol стремится занять лидирующие позиции на рынке «зеленого» водорода на Пиренейском полуострове.
Она планирует расширить свои мощности до 557 МВт к 2025 г. и до 1,9 ГВт к 2030 г.
Еще один электролизер – мощностью 10 МВт – будет введен компанией в эксплуатацию в 2024 г. в Бильбао.
Водород, произведенный там, поможет одному из крупнейших заводов в мире по производству синтетического топлива достичь углеродной нейтральности.
Напомним, в июле 2021 г. Еврокомиссия опубликовала первые официальные предложения по введению в ЕС трансграничного углеродного регулирования (ТУР).
План ЕК (Fit-for-55) включает пакет законодательных актов в области климатической, энергетической, сельскохозяйственной, транспортной и налоговой политики ЕС.
Согласно зеленому курсу ЕС, к 2050 г. страны Европы станут климатически нейтральными, т. е. их выбросы CO2 в атмосферу будут сведены к 0 или компенсированы.
Сегодня ключевые меры предусматривают:
- реформирование углеродного рынка ЕС,
- ужесточение требований по выбросам для транспорта,
- повышение налогов на моторное топливо,
- поддержка сектора возобновляемой энергетики и использования водорода,
- меры стимулирования устойчивого лесопользования и сельского хозяйства.
Электролизер — Акватрол
Электролизер — служит для демонстрации загрязнения воды методом сравнения двух образцов, взятых из разных источников. Вы можете, например, сравнить качество воды из крана и бутилированной. В процессе работы электролизер переводит примеси, содержащиеся в воде в нерастворимую форму.
Электролизер — аппарат для электролиза, состоящие из четырех электролитических ячеек и представляет систему сосудов, наполненный электролитом с размещенными в нём электродами — катодом и анодом, соединёнными соответственно с отрицательным и положительным полюсами источника постоянного тока.
Как использовать:
1. Возьмите 2 стакана емкостью 100-150 мл. Первый стакан наполните водой из крана, а второй — водой после фильтра. Установите стаканы на столе.
2. Подключите электролизер в розетку 220 вольт и опустите электроды в оба стакана.
3. Включите питание электролизера и начните тестирование воды.
4. Обычно время испытания составляет 30 секунд.
5. После проведения испытаний выключите питания электролизера и достаньте из воды.
По цвету осадка в воде после электролиза можно сделать выводы о наличии примесей:
Вода После электролиза
- Зеленый: мышьяк, хлороформ, тетрахлорметан, оксид меди, железо (II)
- Синий: бактерии, вирусы, органический фосфор (удобрения, моющие средства и пестициды), сульфат алюминия
- Красный: одновалентная ртуть, железо
- Белый: свинец, цинк, ртуть, асбест, кальций, магний
- Черный: тяжелые металлы (свинец, цинк, ртуть, медь, хром)
- Желтый: растворенный кислород, растворенный микроэлементы, органические минералы
Предупреждение безопасности:
Не дотрагивайтесь электродов во время включенного питания;
Не опускайте руку в воду для испытания;
Не позволяйте детям играть с электролизером;
Протрите электроды и корпус электролизера чистой салфеткой;
Прибор не может быть использован для тестирования минеральной воды.
Электролизер Lan Shan AEB-1 220 вольт
Электролизер — служит для демонстрации загрязнения воды методом сравнения двух образцов, взятых из разных источников. Вы можете, например, сравнить качество воды из крана и бутилированной. В процессе работы электролизер переводит примеси, содержащиеся в воде в нерастворимую форму.
Электролизер — аппарат для электролиза, состоящие из четырех электролитических ячеек и представляет систему сосудов, наполненный электролитом с размещенными в нём электродами — катодом и анодом, соединёнными соответственно с отрицательным и положительным полюсами источника постоянного тока.
Как использовать:
1. Возьмите 2 стакана емкостью 100-150 мл. Первый стакан наполните водой из крана, а второй — водой после фильтра. Установите стаканы на столе.
2. Подключите электролизер в розетку 220 вольт и опустите электроды в оба стакана.
3. Включите питание электролизера и начните тестирование воды.
4. Обычно время испытания составляет 30 секунд.
5. После проведения испытаний выключите питания электролизера и достаньте из воды.
По цвету осадка в воде после электролиза можно сделать выводы о наличии примесей:
Вода После электролиза
- Зеленый: мышьяк, хлороформ, тетрахлорметан, оксид меди, железо (II)
- Синий: бактерии, вирусы, органический фосфор (удобрения, моющие средства и пестициды), сульфат алюминия
- Красный: одновалентная ртуть, железо
- Белый: свинец, цинк, ртуть, асбест, кальций, магний
- Черный: тяжелые металлы (свинец, цинк, ртуть, медь, хром)
- Желтый: растворенный кислород, растворенный микроэлементы, органические минералы
Предупреждение безопасности:
Не дотрагивайтесь электродов во время включенного питания;
Не опускайте руку в воду для испытания;
Не позволяйте детям играть электролизером;
Протрите электроды и корпус электролизера чистой салфеткой;
Прибор не может быть использован для тестирования минеральной воды.
Технические характеристики:
- Максимальное значение TDS (минерализации) тестируемой воды: 500 ppm
- Питание: 220 VAC
- Длина провода (см): 138
- Размеры (мм): 100x90x50
- Вес (грамм): 200
Shell ввел в эксплуатацию «крупнейший в Европе» PEM-электролизер
Нефтегазовый концерн Shell запустил крупнейший в Европе водородный PEM электролизер в энергетическом и химическом парке Rheinland в Германии.
Проект реализован в рамках консорциума Refhyne (Clean Refinery Hydrogen for Europe) и при финансовой поддержке Европейской комиссии. Электролизер мощностью 10 мегаватт производства ITM-Power использует возобновляемую энергию и способен производить до 1300 тонн зеленого водорода в год.
Первоначально h3 будет использоваться на нефтеперерабатывающем заводе для производства топлива «с более низкой углеродоемкостью». Shell также работает над внедрением зеленого водорода в других секторах, таких как автомобильный транспорт.
В планах компании увеличение мощности электролиза до 100 мегаватт.
В соответствии со своей стратегией, Shell обязуется достичь нулевого баланса выбросов (net zero emissions) к 2050 году. Для этого компания, среди прочего, собирается к 2030 году превратить пять основных нефтеперерабатывающих заводов в «интегрированные энергетические и химические парки». Там будет перерабатываться меньше сырой нефти, но больше возобновляемого и вторичного сырья и будет уделяться больше внимания химическим веществам и энергетическим продуктам с низким содержанием углерода, таким как биотопливо и водород.
В результате к 2030 году Shell сократит производство традиционных видов топлива на 55% и «будет производить больше низкоуглеродных видов, химикатов и энергетических продуктов, в которых нуждаются клиенты».
Читайте также: Shell начинает крупнейший в Европе проект по производству зеленого водорода.
Уважаемые читатели !!
Ваша поддержка очень важна для существования и развития RenEn, ведущего русскоязычного Интернет-сайта в области «новой энергетики». Помогите, чем можете, пожалуйста.
Яндекс Кошелёк
Карта Сбербанка: 4276 3801 2452 1241
Возобновляемый электролиз | Водородные и топливные элементы
Исследования в области электролиза возобновляемых источников энергииNREL сосредоточены на проектировании, разработке и тестировании. передовые экспериментальные и аналитические методы улучшения электролизной батареи и системы эффективность.
Связанные виды деятельности включают:
- Характеристика работы электролизера в условиях переменной входной мощности
- Проектирование и разработка общих блоков силовой электроники и контроллеров для уменьшения стоимость системы и оптимизация производительности
- Выявление возможностей снижения затрат за счет прорывной интеграции компонентов
- Тестирование, оценка и оптимизация производительности возобновляемых систем электролиза для
производство водорода и когенерация электроэнергии / водорода.
Узнайте о проекте преобразования ветра в водород, в котором для производства водорода используется электричество ветряных турбин и солнечных батарей.
Системная инженерия, моделирование и анализ
NREL разрабатывает и проверяет модели компонентов и систем для оценки и оптимизации различных системных сценариев и стратегий управления для производства возобновляемого водорода и электроэнергии / водорода когенерация.
На этой диаграмме показаны различные сценарии производства водорода и электроэнергии из возобновляемых источников.
В 2011 году NREL провел обширный анализ затрат на производство водорода с помощью
ветровой электролиз воды на потенциальных объектах по всей стране. Обратитесь к инструменту анализа затрат на производство водорода, чтобы просмотреть результаты этого анализа.
Системная интеграция и разработка компонентов
NREL разрабатывает интерфейсы силовой электроники для возобновляемых систем электролиза для определения характеристик и проверить работу электрохимических устройств.Тестирование также исследует, как колебания выходной мощности ветряной турбины влияют на работу электролизера. Системы производительность оценивается количественно на основе эффективности аккумуляторных и электролизных систем. а также их способность использовать возобновляемые источники электроэнергии.
Системы электролиза возобновляемых источников, которые изучает NREL, включают обычный постоянный ток.
(DC) шина (электрический провод), закрепленная с аккумуляторной батареей, подключенной к ветряной турбине,
фотоэлектрическая матрица и электролизер. Обычно небольшие ветряные турбины устанавливают
для зарядки аккумуляторов и требует подключения к шине постоянного тока постоянного напряжения и питания
электроника для регулирования выходной мощности и преобразования переменного тока (AC)
в округ Колумбия.
В имеющихся в продаже системах электролизера блок электролизера принимает постоянный ток. потребляемая мощность от бортового преобразователя питания. Электролизер регулирует мощность до стек и работает при фиксированном токе стека.Адреса для характеристических испытаний работа водородных батарей при переменном токе без фиксированной мощности поставка.
Характеристики и испытания
NREL работает с национальными и международными лидерами отрасли для разработки на основе консенсуса
характеристики и протоколы испытаний электролизеров на возобновляемых источниках энергии и для сравнения
производительность электролизеров различных производителей.
На основе фактических эксплуатационных данных ветряных электростанций, фотоэлектрических элементов и прогнозируемых с переключением нагрузки, эти протоколы испытаний применимы к работе электролизера при переменном входе условия питания.
NREL использует протоколы для тестирования электролизеров на месте. Конкретные показатели эффективности включают чистоту водорода при малой мощности и долгосрочное воздействие переменных мощность системы электролизера и эффективность батареи.
Помещения
Исследования электролиза возобновляемых источников энергии NREL проводятся в Energy Systems Integration. Лаборатория в Комплексе интеграции энергосистем.
Контакт
Кевин Харрисон
Электронная почта
303-630-2439
Производитель топливных элементов Bloom Energy запускает высокотемпературный водородный электролизер
Производитель топливных элементов Bloom Energy Corp. выходит на рынок производства водорода с коммерческим запуском высокотемпературного электролизера, способного использовать тепловую энергию в качестве источника энергии.
Запуск отличает Bloom Energy от большинства производителей коммерческих электролизеров, которые в основном предлагают низкотемпературные электролизеры, которые полностью полагаются на электроэнергию для разделения воды на водород и кислород. В высокотемпературных электролизерах для расщепления воды используется меньше электроэнергии, что снижает эксплуатационные расходы, препятствующие производству водорода.
Электролизеры — это основополагающая технология экологически чистого водорода, безуглеродной формы топлива, производимого с использованием возобновляемой электроэнергии. Производители электроэнергии, производители автомобилей, газовые компании и производители изучают возможность использования водорода с низким и нулевым содержанием углерода для замены природного газа и ископаемого топлива в своей деятельности.
При питании исключительно от электроэнергии Bloom Electrolyzer потребляет на 15% меньше электроэнергии, чем низкотемпературные электролизеры, говорится в сообщении компании от 14 июля.По его словам, когда электролизер также использует внешний источник тепла для питания, он потребляет до 45% меньше электроэнергии, чем низкотемпературные модели.
Способность использовать тепло в качестве источника энергии делает высокотемпературный электролиз идеальным для промышленных компаний, в том числе производителей стали, химии, цемента и стекла, сообщает Bloom Energy. Высокотемпературные процессы, используемые в этих производственных секторах, трудно электрифицировать, и избыточное тепло от этих процессов можно использовать для питания высокотемпературных электролизеров.Затем этот водород можно использовать в качестве топлива для печей, уменьшая или устраняя необходимость транспортировки водорода на объект, сообщает Bloom Energy.
Компания отметила, что водород, полученный из ее нового предложения электролизеров, также может использоваться для питания ее устаревшего продукта, модульных систем топливных элементов, способных производить электроэнергию на месте из природного газа, биогаза и водорода. По данным Bloom Energy, в высокотемпературном электролизере используется та же технология твердых оксидов и многие из тех же компонентов, что и системы топливных элементов, что позволяет компании использовать существующие цепочки поставок для увеличения производства электролизеров.
«Запуск Bloom Electrolyzer — это большой шаг вперед в нашей миссии по обеспечению и расширению возможностей глобальной водородной экономики и декарбонизированного общества», — сказал в своем выпуске председатель и главный исполнительный директор Bloom Energy КР Шридхар. «Водород позволяет нам использовать обильные и недорогие возобновляемые источники энергии для надежного производства энергии с нулевым выбросом углерода, а не периодически».
Топливные элементы Bloom Energy не застрахованы от опасений, связанных с выбросами в результате потребления природного газа. Поскольку все больше городов в районе залива Сан-Франциско запрещают использование природного газа в новых зданиях, Bloom Energy из Сан-Хосе недавно добилась исключения для своих систем топливных элементов, утверждая, что в будущем они будут все больше работать на водороде с нулевым выбросом углерода и возобновляемом природном газе. .
Компания ожидает, что коммерческие поставки Bloom Electrolyzer начнутся осенью 2022 года. Отвечая на вопрос о предварительных затратах, представитель компании сказал, что Bloom Energy обычно не перечисляет капитальные затраты, поскольку они зависят от размера системы, расположения, конфигурации и другие факторы.
Зеленый водород требует значительных затрат на по сравнению с природным газом. Операторам электролизеров обычно необходимо часто запускать их, чтобы окупить капитальные затраты, но им также требуются низкие затраты на электроэнергию для их рентабельной эксплуатации.
Bloom Energy впервые опробовала свою технологию электролизера в ноябре 2020 года вместе со своим южнокорейским партнером SK ecoplant Co.Ltd. На промышленной площадке в Чангвоне, Южная Корея. В мае компания объявила о партнерстве с Национальной лабораторией штата Айдахо при Министерстве энергетики США для обеспечения электропитания электролизера Bloom избыточным электричеством и паром от атомных электростанций. В том же месяце Bloom Energy начала сотрудничество с Baker Hughes Co., которое включает сочетание электролизера и технологии сжатия для производства, сжатия, транспортировки и хранения водорода.
Произошла ошибка при настройке пользовательского файла cookie
Этот сайт использует файлы cookie для повышения производительности. Если ваш браузер не принимает файлы cookie, вы не можете просматривать этот сайт.
Настройка вашего браузера для приема файлов cookie
Существует множество причин, по которым cookie не может быть установлен правильно. Ниже приведены наиболее частые причины:
- В вашем браузере отключены файлы cookie. Вам необходимо сбросить настройки своего браузера, чтобы он принимал файлы cookie, или чтобы спросить вас, хотите ли вы принимать файлы cookie.
- Ваш браузер спрашивает вас, хотите ли вы принимать файлы cookie, и вы отказались.
Чтобы принять файлы cookie с этого сайта, используйте кнопку «Назад» и примите файлы cookie.
- Ваш браузер не поддерживает файлы cookie. Если вы подозреваете это, попробуйте другой браузер.
- Дата на вашем компьютере в прошлом. Если часы вашего компьютера показывают дату до 1 января 1970 г., браузер автоматически забудет файл cookie. Чтобы исправить это, установите правильное время и дату на своем компьютере.
- Вы установили приложение, которое отслеживает или блокирует установку файлов cookie. Вы должны отключить приложение при входе в систему или проконсультироваться с системным администратором.
Почему этому сайту требуются файлы cookie?
Этот сайт использует файлы cookie для повышения производительности, запоминая, что вы вошли в систему, когда переходите со страницы на страницу. Чтобы предоставить доступ без файлов cookie
потребует, чтобы сайт создавал новый сеанс для каждой посещаемой страницы, что замедляет работу системы до неприемлемого уровня.
Что сохраняется в файле cookie?
Этот сайт не хранит ничего, кроме автоматически сгенерированного идентификатора сеанса в cookie; никакая другая информация не фиксируется.
Как правило, в файлах cookie может храниться только информация, которую вы предоставляете, или выбор, который вы делаете при посещении веб-сайта. Например, сайт не может определить ваше имя электронной почты, пока вы не введете его. Разрешение веб-сайту создавать файлы cookie не дает этому или любому другому сайту доступа к остальной части вашего компьютера, и только сайт, который создал файл cookie, может его прочитать.
Безмембранный электролизер с пористыми стенками для высокой производительности и получения чистого водорода
В безмембранных электролизерах для разделения продуктов электролизного газа вместо твердых барьеров используются гидравлические силы. Эти электролизеры имеют низкое ионное сопротивление, простую конструкцию и возможность работы с электролитами при различных значениях pH. Однако межэлектродное расстояние и скорость потока должны быть большими при высоких дебитах, чтобы предотвратить переход газа.Это не является энергетически выгодным, поскольку ионное сопротивление выше при больших межэлектродных расстояниях, а требуемая мощность накачки увеличивается с увеличением скорости потока. В этой работе предлагается новое решение для увеличения производительности электролизеров без необходимости увеличения этих двух параметров. Новый микрофлюидный реактор имеет три канала, разделенных пористыми стенками. Электролит поступает в средний канал и течет во внешние каналы через поры стенки. По внешним каналам производятся газовые продукты.Переход водорода в этом электролизере составляет 0,14% при расходе = 80 мл · ч −1 и плотности тока ( · ) = 300 мА · см −2 . Этот переход в 58 раз ниже, чем переход водорода в эквивалентном безмембранном электролизере с параллельными электродами при тех же рабочих условиях.
Кроме того, добавление поверхностно-активного вещества к электролиту дополнительно снижает переход водорода на 21% и перенапряжение на 1,9%. Это связано с положительным влиянием ПАВ на динамику отделения и коалесценции пузырьков.Добавление пассивной добавки и использование пористых стенок приводит к удвоению скорости производства водорода в новом реакторе по сравнению с электролизерами с параллельными электродами с аналогичным переходом водорода.
Эта статья в открытом доступе
Подождите, пока мы загрузим ваш контент… Что-то пошло не так.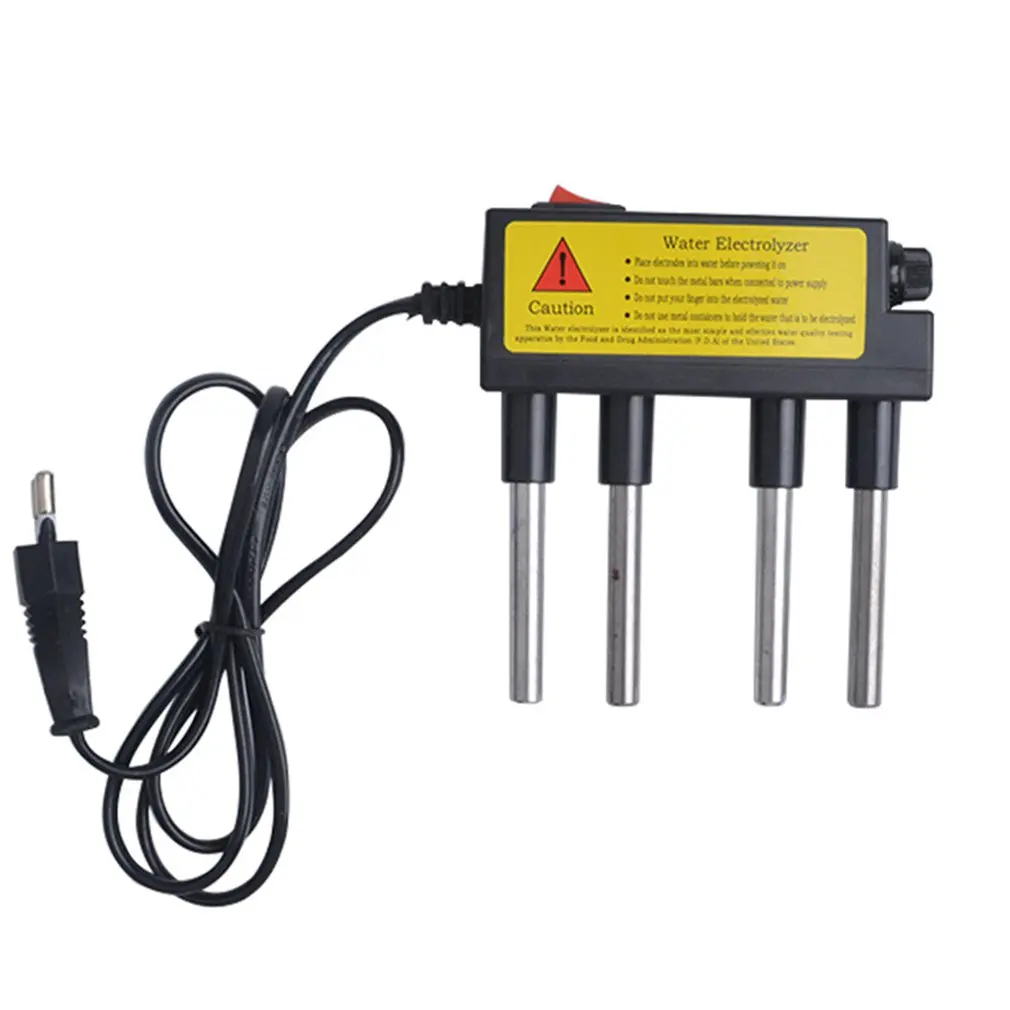
Topsoe построит крупномасштабный завод по производству электролизеров SOEC для удовлетворения потребностей клиентов в производстве экологически чистого водорода и эффективности SOEC
- Topsoe вложит средства в производство высокоэффективных твердооксидных электролизеров (SOEC) общей мощностью 500 мегаватт в год с возможностью расширения до 5 гигаватт в год.
- Обладая эффективностью выше 90%, запатентованные электролизеры Topsoe SOEC обеспечивают превосходные характеристики при электролизе воды в водород по сравнению с сегодняшними стандартными электролизерами с щелочными электролизерами или электролизерами PEM.
- Предполагается, что объект будет введен в эксплуатацию к 2023 году.
Хальдор Топсе Генеральный директор, Руланд Баан.
Благодаря новому предприятию Topsoe удовлетворит быстро растущий спрос на конкурентоспособные технологии электролиза, в основном на экологически чистые водородные установки, основанные на возобновляемой электроэнергии.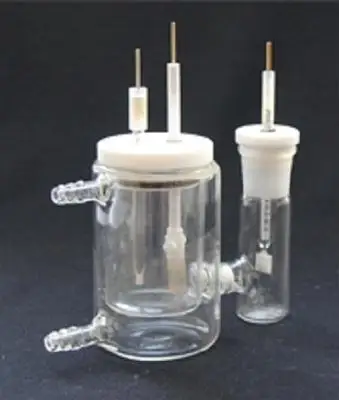
«Этот новый производственный объект — конкретный шаг к тому, чтобы взять на себя ведущую роль в продолжающемся энергетическом переходе к низкоуглеродному будущему. Мы твердо убеждены в том, что один из наиболее жизнеспособных путей достижения этой цели заключается в эффективном использовании возобновляемой электроэнергии для производства экологически чистого водорода, топлива и химикатов.Благодаря электролизеру SOEC компании Topsoe более 90% возобновляемой электроэнергии, поступающей в электролизер, сохраняется в зеленом водороде, который он производит. Это значительно более эффективно, чем другие доступные на рынке технологии. У Топсе уже есть ряд технологий, а также несколько других, которые находятся в стадии разработки, которые обеспечат компании лидирующую роль в переходе к энергетике, сокращая выбросы углерода во всем мире. Решение построить это крупномасштабное производство с использованием нашей технологии SOEC показывает, что мы готовы и можем воплотить наши амбиции в реальность », — говорит Руланд Баан, генеральный директор Haldor Topsoe.
Topsoe в настоящее время является мировым лидером в области водородных технологий, катализаторов и услуг, обеспечивающих эффективное производство водорода. Предложения включают технологии для традиционного производства водорода на основе природного газа с возможностью улавливания углерода, также известного как синий водород, а также экологически чистый водород с технологией электролизера SOEC.
Топсе уже участвует в нескольких проектах по производству зеленого водорода, зеленого аммиака, зеленого метанола и зеленого топлива. Примером может служить проект Helios в NEOM, Саудовская Аравия, объявленный в июле 2020 года, который включает в себя крупнейший в мире аммиачный контур, поставленный Topsoe.Благодаря технологии SOEC и многолетнему опыту работы в качестве ведущего мирового поставщика технологий в области аммиака, метанола, бензина, реактивного топлива, дизельного топлива и водорода, Topsoe является одной из немногих компаний, которые могут предоставить идеи и технологии по всей цепочке создания стоимости. для топлива и химикатов нового поколения.
«Наше уникальное комплексное предложение в области производства зеленого водорода путем электролиза и связанного с ним последующего производства аммиака, метанола и электронного топлива предлагает клиентам высококачественные продукты, безопасную транспортировку и энергоэффективное хранение, и мы уже общение с потенциальными клиентами, которые заинтересованы в том, чтобы стать первопроходцами в этой сфере », — говорит Эми Хеберт, коммерческий директор Haldor Topsoe.
Электролизер SOEC от Topsoe обеспечивает более 90% энергоэффективности при использовании экологически чистой энергии для производства водорода. Текущие электролизеры на 70%.
Факты о крупном производственном предприятии SOEC в Топсе
- Завод будет иметь производственную мощность электролизера 500 МВт в год с возможностью расширения до 5 ГВт Продуктом
- будут промышленные электролизеры, основанные на запатентованной технологии высокотемпературного электролиза Topsoe SOEC, обеспечивающей на 30% больший выход водорода по сравнению со стандартной технологией, такой как PEM и щелочной электролиз.
- Ввод в эксплуатацию к 2023 году.
Избранные проекты с использованием технологий Топсе
- Проект Helios в NEOM, Саудовская Аравия ; Topsoe поставляет аммиачную технологию для крупнейшего в мире завода по производству экологически чистого водорода, строящегося в Саудовской Аравии. Завод будет производить 650 тонн безуглеродного водорода в день для грузовых автомобилей и автобусов.
- DeLille ; первая коммерческая эксплуатация технологии SOEC компании Topsoe по преобразованию CO 2 в CO.Запуск ожидается в первой половине 2021 года.
- Зеленое топливо для Дании ; партнерство датских компаний, которые наладят производство экологически чистого водорода в районе Большого Копенгагена. Топсе вносит свой вклад, используя ноу-хау в области технологий, которые преобразуют улавливаемый CO 2 в экологически чистый метанол и реактивное топливо с использованием водорода из электролиза воды.
- Заводы по производству зеленого метанола в Скандинавии ; как член консорциума Power-to-X, возглавляемого Liquid Wind, Топсе будет производить э-метанол в промышленных масштабах на основе зеленого водорода и улавливания CO2 при сжигании отходов.
Узнайте больше о экологически чистом водородном бизнесе Топсе.
Дополнительная информация
Ульрик Фрёльке, менеджер по связям со СМИ
Телефон: +45 27 77 99 68
Электронная почта: [email protected]
Электрохимический синтез цемента — процесс декарбонизации CaCO3 с получением полезного газа на основе электролизера потоков
Реферат
Производство цемента в настоящее время является крупнейшим промышленным источником выбросов CO 2 , на долю которого приходится ∼8% (2.8 Гт / год) мировых выбросов CO 2 . Глубокая декарбонизация производства цемента потребует устранения как выбросов CO 2 из-за разложения CaCO 3 до CaO, так и выбросов из-за сжигания ископаемого топлива (в основном угля) при прокаливании (~ 900 ° C) и спекании ( ~ 1450 ° С). Здесь мы демонстрируем электрохимический процесс, в котором используется электролиз нейтральной воды для создания градиента pH, в котором CaCO 3 декарбонизируется при низком pH, а Ca (OH) 2 осаждается при высоком pH, одновременно производя O высокой чистоты. 2 / CO 2 газовой смеси (молярное соотношение 1: 2 при стехиометрическом режиме) на аноде и H 2 на катоде.Мы показываем, что твердый продукт Ca (OH) 2 легко разлагается и вступает в реакцию с SiO 2 с образованием алита, основной вяжущей фазы портландцемента. Электрохимическое прокаливание дает концентрированные газовые потоки, из которых можно легко отделить и изолировать CO 2 , можно использовать H 2 и / или O 2 для выработки электроэнергии через топливные элементы или камеры сгорания, можно использовать O 2 . в качестве компонента кислородного топлива в цементной печи для повышения эффективности и снижения выбросов CO 2 , или выходящие газы могут использоваться для других процессов с добавленной стоимостью, таких как производство жидкого топлива.
Анализ показывает, что если бы водород, производимый в реакторе, сжигался для нагрева высокотемпературной печи, процесс электрохимического цементирования мог бы работать исключительно за счет возобновляемой электроэнергии.
Как обсуждалось на Коллоквиуме Саклера в 2018 г. «Состояние и проблемы науки для декарбонизации нашего энергетического ландшафта» и в других недавних анализах (1⇓⇓ – 4), глубокая декарбонизация сегодняшней энергетической системы потребует решения не только производства энергии (24% глобальных выбросов парниковых газов) и транспорта (14% глобальных выбросов парниковых газов), но также секторов, которые трудно декарбонизировать, таких как крупная промышленность, на которую сегодня приходится около 21% глобальных выбросов парниковых газов (5).Промышленность использует ископаемые виды топлива для обогрева и проведения химических и термохимических реакций, но может стать менее зависимым от ископаемого топлива, если 1) станут доступны электрические альтернативы и 2) стоимость и надежность возобновляемой электроэнергии продолжит повышаться (6, 7). Распространение очень дешевой возобновляемой электроэнергии уже стимулировало поиск электрохимических методов для обновления промышленных процессов (1, 8, 9). Среди них до сих пор были ограничены электрохимические пути производства цемента; 1 предыдущий пример представляет собой высокотемпературное электрохимическое декарбонирование с использованием расплавов солей, работающее в том же диапазоне температур, что и печи для термической обжига (10, 11).Здесь мы предлагаем и демонстрируем доказательство концепции электрохимического процесса при температуре окружающей среды, который декарбонизирует CaCO 3 , осаждает твердый Ca (OH) 2 , из которого синтезируются желаемые силикаты кальция, и производит потоки концентрированного газа H 2. и O 2 + CO 2 , которые поддаются улавливанию и улавливанию CO 2 и / или используются в других процессах с добавленной стоимостью (рис. 1).
Схема электрохимического цементного завода с низким уровнем выбросов. Реактор электрохимической декарбонизации, работающий от возобновляемых источников электроэнергии, преобразует CaCO 3 в Ca (OH) 2 для использования в синтезе цемента. В ячейке декарбонизации (рис. 2) используется градиент pH, полученный при электролизе в нейтральной воде, для растворения CaCO 3 на кислотном аноде и осаждения Ca (OH) 2 при pH ≥ 12,5. Одновременно на катоде генерируется H 2 , а на аноде генерируется O 2 / CO 2 . Эти газовые потоки могут выполнять несколько альтернативных функций в устойчивой производственной системе.CO 2 может улавливаться непосредственно из изначально сконцентрированного потока (CCS). Электричество или тепло можно вырабатывать из H 2 и O 2 через топливные элементы или камеры сгорания. Кислородное топливо O 2 / CO 2 может быть рециркулировано в печь для более чистого сжигания в цикле спекания цемента. Можно использовать концепции повторного использования и утилизации CO 2 (CO 2 U), например, использование в EOR или производстве жидкого топлива.
Портландцемент (12) — наиболее широко производимый искусственный материал в мире, производимый со скоростью 4 миллиарда метрических тонн в год (13).За исключением сельского хозяйства, производство цемента является крупнейшим промышленным источником парниковых газов (за ним следует производство стали), на которое сегодня приходится 8% мировых выбросов парниковых газов (14). Около половины выбросов CO 2 связано с использованием CaCO 3 (как правило, известняк) в качестве ключевого компонента, а остальная часть приходится в основном на сжигание ископаемого топлива в цементной печи (15). Спрос на цемент растет по мере того, как население мира увеличивается и становится все более городским, а также по мере развития инфраструктуры в странах с развивающейся экономикой (16).Ожидается, что к 2060 году количество построек на Земле удвоится; это эквивалентно строительству Нью-Йорка каждые 30 дней в течение следующих 40 лет (17). Поскольку каждый килограмм произведенного цемента выделяет около 1 кг CO 2 (15), несколько гигатонн CO 2 в год будут выбрасываться из новой инфраструктуры, что подчеркивает срочность декарбонизации производства цемента.
Текущие усилия по сокращению углеродного следа цемента включают улавливание углерода из дымовых газов, использование альтернативных видов топлива или разработку дополнительных вяжущих материалов (14, 18⇓⇓ – 21).В настоящее время дымовой газ цементных заводов слишком загрязнен для экономичного улавливания углерода с помощью аминовой очистки; использование альтернативных видов топлива (например, изношенных шин) не снижает первичные выбросы CaCO 3 ; а использование дополнительных материалов в бетоне имеет ограниченное влияние на выбросы углерода из портландцемента и может одновременно ухудшить его физические свойства (14, 19⇓ – 21). Другое семейство подходов использует цемент для улавливания и секвестрации большего количества CO 2 , производя обогащенный карбонатом цемент или бетонный продукт (22⇓⇓ – 25).В отличие от вышеупомянутых подходов, мы были мотивированы искать подходы, основанные на электрохимии, которые имеют потенциал для производства наиболее широко распространенных и используемых цементов, тем самым сводя к минимуму риск внедрения, и в то же время используя преимущества появляющейся очень дешевой возобновляемой электроэнергии для уменьшения количества химических веществ. и тепловые источники CO 2 . Как мы показываем, наш процесс может работать синергетически с другими научными и технологическими инструментами устойчивой энергетической системы, обсуждаемыми на коллоквиуме Саклера, включая ветровое и солнечное электричество, расщепление воды и создание топлива, а также хранение химической и электрической энергии.
В нашем реакторе используются преимущества градиентов pH, присущих электролизной ячейке, для декарбонизации CaCO 3 и осаждения и сбора Ca (OH) 2 (рис. 2). Мы показываем, что Ca (OH) 2 , полученный таким образом, который требует меньше энергии для дегидратации до CaO, чем требуется для прокаливания CaCO 3 , легко реагирует с SiO 2 с образованием алита, основной активной фазы. (От 50 до 70% по весу) в портландцементе (12). Работа, близкая к стехиометрической, когда каждые 2 протона электролитически образуются в кислородно-генерирующем анодном декарбонате 1 формула CaCO 3 , демонстрируется в лабораторном масштабе. Мы предлагаем несколько путей, с помощью которых этот реактор электрохимической декарбонизации может быть интегрирован в цементный завод с низким или нулевым выбросом углерода (рис. 1), включая питание от возобновляемой электроэнергии и использование газов, производимых в любой из нескольких альтернативных функций, таких как 1 ) прямой улавливание и связывание изначально концентрированного потока CO 2 , 2) выработка электроэнергии или тепла из H 2 (и, возможно, O 2 ) через топливные элементы или камеры сгорания, 3) обеспечение кислородным топливом для более чистое горение в цикле спекания цемента и 4) производство жидкого топлива.Представлен технико-экономический анализ первого порядка зависимости энергопотребления и стоимости топлива от стоимости возобновляемой электроэнергии.
Схема декарбонизатора на базе электролизера. Реакции 1 и 2 представляют собой полуэлементные реакции выделения кислорода и выделения водорода соответственно при почти нейтральном pH. Реакция 3 — это образование воды из составляющих ее ионов. Реакции 4 и 5 представляют собой разложение карбоната кальция и выделение CO 2 ; см. текст для промежуточных шагов.В реакции 6 гидроксид-ионы в реакции 3 вместо этого идут на образование гидроксида кальция, а протоны протонируют карбонат-ионы (реакция 5). Общая реакция, в которой CaCO 3 превращается в Ca (OH) 2 с сопутствующим высвобождением H 2 , O 2 и CO 2 , показана внизу.
Результаты
Наша ячейка декарбонизации одновременно функционирует как электролизер, а также как химический реактор для преобразования твердого CaCO 3 в твердый Ca (OH) 2 , схематически показанный на рис.2 и продемонстрировано экспериментально на рис. 3 и SI Приложение , рис. S2 и S3. Электролизер, работающий с водой, близкой к нейтральной, имеет следующие реакции анодной и катодной полуэлементов: 2h3O → O2 + 4H ++ 4e‐ [1] 2h3O + 2e- → h3 + 2OH -. [2] В установившемся состоянии электролизер создает градиент pH, который легко визуализируется при добавлении универсального индикатора pH к работающей H-ячейке, как показано на рис. 3 и видеороликах S1 и S2. В таком электролизере H + и OH — обычно рекомбинируют с образованием воды: H ++ OH- → h3O.[3] Наш реактор заменяет эту реакцию реакцией декарбонизации. Когда CaCO 3 добавляется к кислому раствору, образующемуся вблизи анода во время электролиза, химическое декарбонизация происходит по следующей последовательности реакций (26): (K = 6 × 10-9) CaCO3 (s) ⇌Ca ( aq) 2 ++ CO3 (aq) 2- [4] (K = 2,1 × 1010) CO32- + H + ⇌HCO3- [5a] (K = 2,2 × 106) HCO3- + H + ⇌h3CO3 [5b] (K = 5,9 × 102) h3CO3 (водн.) ⇌CO2 (г) + h3O. [5c] Растворенный Ca 2+ (уравнение 4 ) притягивается к аноду и затем осаждается из раствора в виде Ca (OH) 2 при реакции с OH — ; эта реакция предпочтительна при pH выше 12.5: Ca2 ++ 2OH- → Ca (OH) 2.
[6] Сумма электрохимических и химических реакций, протекающих в ячейке, равна 2CaCO3 (s) + 4h3O (l) → 2Ca (OH) 2 (s) + 2h3 ( г) + O2 (г) + 2CO2 (г). [7] Мы определяем стехиометрическую работу этого реактора как условие, при котором каждые 2 моль протонов, образующихся во время электролиза (уравнение 1 ), превращает 1 моль CaCO 3 на 1 моль Ca (OH) 2 , как показано в уравнении. 7 ; это представляет собой максимально возможный выход и кулоновскую эффективность. При стехиометрической операции соотношение произведенных газов также определяется формулой. 7 : каждый моль Ca (OH) 2 дает в результате образование 1 моль H 2 на катоде и 1 моль O 2 и 2 моль CO 2 на аноде.
Покадровые изображения декарбонизированных Н-ячеек с использованием платиновых электродов и 1 М NaNO 3 в деионизированной воде в качестве электролита. Каждая ячейка содержит несколько капель индикаторной краски pH, цветовая шкала которых указана внизу. ( A — E ) Ячейка, содержащая порошок CaCO 3 в анодной (левой) камере и без пористого разделителя между камерами.Электролиз при напряжении ячейки 2,5 В (ток ~ 6 мА) дает цветовой градиент, показывающий кислотный раствор на аноде (слева) и щелочной раствор на катоде (справа). Внимательное изучение поперечной трубы показывает расслоение растворов, связанное с конвекцией, обусловленной плотностью. ( F — I ) Камера обезуглероживания, в которой в обеих камерах используются сепараторы пористого волокна для ограничения конвекции, а источник порошка CaCO 3 находится внутри съемной чашки, что позволяет отслеживать потерю веса.Обратите внимание на отсутствие расслоения. ( J ) Ca (OH) 2 осаждался в поперечной трубке после 12 ч электролиза при высоком напряжении ячейки 9 В для ускорения реакции.
Ранее Рау, наряду с другими (27⇓⇓ – 30), предлагал использовать электролитическое обезуглероживание с использованием возобновляемых источников энергии в качестве средства снижения закисления океана. Их концепция, в свою очередь, аналогична работе кальциевого реактора, используемого для поддержания щелочности в рифовых аквариумах: CaCO 3 реагирует с кислотой (в случае Рау кислота образуется в результате окисления морской воды) с образованием растворенного Ca (HCO 3 ) 2 и Ca (OH) 2 на катоде.Полученный раствор Ca (HCO 3 ) 2 и Ca (OH) 2 является щелочным и улавливает CO 2 из атмосферы для преобразования CaCO 3 и может быть возвращен в морской объект для уменьшения подкисления. . Здесь вместо использования электролитической декарбонизации для улавливания CO 2 мы выделяем CO 2 в виде газообразного продукта, который нужно улавливать и улавливать или использовать в других процессах, и осаждаем Ca (OH) 2 для использования в производство цемента.Обратите внимание, что помимо производства цемента, Ca (OH) 2 является важным компонентом в производстве сахара-рафинада, целлюлозы и бумаги, карбонатов щелочных металлов, для очистки сточных вод и в качестве флюса при рафинировании стали (31). Обычно Са (ОН) 2 получают гашением СаО, полученного прокаливанием СаСО 3 ; Используя наш реактор декарбонизации, Ca (OH) 2 может быть произведен непосредственно для этих применений, позволяя при этом непосредственно улавливать произведенный CO 2 .
Для проверки предложенной схемы построена серия лабораторных реакторов с Н-ячейками. Рис. 3 A — E показывает покадровые изображения реактора, собранного с платиновыми электродами и использующего электролит, состоящий из 1 M NaNO 3 в дистиллированной воде, к которому было добавлено несколько капель универсального индикатора pH. . Цветовая шкала, коррелирующая цвет с pH, показана внизу рисунка. В анодной камере находится порошок CaCO 3 , и в отличие от ячейки на рис.3 F — J , между камерами не используется пористый сепаратор. Первоначально на рис. 3 A желтый оттенок показывает, что электролит имеет pH ~ 6 везде, кроме непосредственно над слоем порошка CaCO 3 , где фиолетовый оттенок показывает, что частичное растворение карбоната привело к повышению pH до > 10. На рис. 3 B — E показана ячейка в разное время после начала электролиза в потенциостатических условиях (напряжение ячейки 2,5 В, ток ∼6 мА).Цветовые градиенты показывают, что со временем развивается более крутой градиент pH, достигающий более экстремальных значений pH в каждой камере, что согласуется с реакциями полуэлементов (уравнения 1 и 2 ). Однако при внимательном рассмотрении раствора в поперечной трубке видно отчетливое расслоение, с кислым (розовым) раствором вверху и щелочным (пурпурным) раствором внизу, что мы приписываем разнице в плотности между двумя растворами. Фильм S1 показывает развитие градиента pH и слоистых слоев жидкости в этой ячейке с течением времени.В этой конфигурации ячейки Ca (OH) 2 наблюдалось осаждение по всей длине ячейки, включая непосредственно на катоде из платиновой проволоки, который в конечном итоге пассивируется. Как показано в приложении SI, приложение , рис. S1, пассивация приводит к резкому падению тока элемента через несколько часов работы.
Рис. 3 F — I показывает ту же конструкцию ячейки, но с пористым бумажным разделителем, размещенным на пересечении каждой камеры с поперечной трубкой для ограничения конвекции.Кроме того, источник порошка CaCO 3 в этой ячейке содержится в съемном стакане, так что растворение CaCO 3 как функция времени можно было измерить путем удаления и взвешивания оставшегося порошка (после сушки). Обратите внимание на отсутствие расслоения; при отсутствии конвективного перемешивания ячейки могут работать> 12 ч без пассивации катода Ca (OH) 2 ( SI Приложение , рис. S1). В этой ячейке щелочной раствор диффундирует равномерным фронтом через ячейку, и при работе в установившемся режиме pH внутри поперечной трубки достаточно высок, чтобы осаждение Ca (OH) 2 происходило преимущественно между сепараторами, где легко собраны для анализа.Также обратите внимание, что в этой конфигурации pH вокруг анода намного менее кислый (то есть без розового оттенка), и на самом деле желтый цвет указывает на pH ∼6. Это важно, потому что 6 приблизительно соответствует pH, при котором HCO 3 — и CO 2 (водн.) находятся в равновесии. Наблюдение предполагает, что по существу все протоны, образующиеся в реакции выделения кислорода (уравнение 1 ), расходуются в реакции с карбонатным ионом (уравнение 5 ). Мы подтверждаем это независимыми измерениями, которые обсуждаются позже.Кроме того, состав выходящих газов подтвержден газовой хроматографией.
Используя конструкцию ячейки, показанную на рис. 3 F — I , мы собрали значительное количество белого осадка на пористом бумажном сепараторе непосредственно перед катодом, как показано на рис. 3 J . После сушки с помощью порошковой рентгеновской дифракции (XRD) было подтверждено, что осадок состоит преимущественно из Ca (OH) 2 с небольшим количеством CaCO 3 (6%, согласно уточнению Ритвельда) (рис.4 А ). Анализ Брунауэра – Эммета – Теллера (БЭТ) показал, что осадок имеет удельную поверхность 0,8 м 2 / г. Примесь CaCO 3 могла образоваться при воздействии воздуха на Ca (OH) 2 при подготовке образцов для XRD или когда часть растворимого HCO 3 — депротонируется при контакте с OH — до реформировать CaCO 3 . Сканирующая электронная микроскопия (SEM) показывает, что частицы Ca (OH) 2 кристаллизованы с 3 различными характерными масштабами длины.Наиболее крупные изолированные кристаллиты (рис. 4 B ) имеют размеры в десятки микрометров и имеют морфологию гексагональной призмы, характерную для Ca (OH) 2 (32). Следующими по шкале размеров являются агрегаты гораздо более мелких кристаллитов, имеющих размеры в несколько микрометров (рис. 4 C и D ), но аналогичную морфологию гексагональной призмы. Наконец, существуют выделения с округлой морфологией клубеньков, которые при большем увеличении выявляют кристаллиты субмикронного размера (рис.4 E и F ). Появление 3 различных морфологий преципитатов Ca (OH) 2 предполагает, что условия зародышеобразования и роста в реакторе сильно различаются. Происхождение этих вариаций — тема для будущих исследований. Однако практически все полученные частицы имеют размер менее 90 мкм, типичный для сырьевых смесей при производстве цемента (12). Анализ состава с помощью энергодисперсионного рентгеновского анализа ( SI Приложение , рис. S2) показал отсутствие примесей выше фоновых уровней в Ca (OH) 2 , за исключением следовых количеств Na, вероятно, возникающих из-за соли Na, используемой в реакторный электролит.Таким образом, настоящий подход, по-видимому, позволяет производить мелкие частицы Са (ОН) 2 высокой чистоты.
Рис. 4. ПорошокCa (OH) 2 , полученный в реакторе декарбонизации. ( A ) Рентгенограмма порошка типичного образца; Уточнение по Ритвельду показывает 94% Ca (OH) 2 и 6% CaCO 3 . ( B — F ) СЭМ-изображение показывает Ca (OH) 2 кристаллитов трех шкал длины. ( B ) Крупнейшие кристаллиты Ca (OH) 2 имеют размеры в десятки микрометров и характерную морфологию гексагональной призмы.( C ) Агрегаты более мелких кристаллитов Ca (OH) 2 , показанные при большем увеличении в D , имеют аналогичную морфологию гексагональной призмы, но имеют микрометровые размеры. ( E ) Ca (OH) 2 с округлой морфологией узелков, которые при большем увеличении ( F ) показывают кристаллиты субмикронного размера.
Была проведена серия экспериментов для определения кулоновской эффективности реактора по сравнению со стехиометрическим пределом.В каждом эксперименте реактор с Н-ячейкой собирали со свежим электролитом, используя 1 М соли NaClO 4 или NaNO 3 и такое же исходное количество порошка CaCO 3 . Реактор работал в потенциостатических условиях (3,5 В) в течение времени от 1 до 14 ч, после чего чашка, содержащая CaCO 3 , была удалена из реактора, высушена и взвешена для получения количества CaCO 3 , потерянного для химическое растворение. Результаты 13 экспериментов представлены на рис.5 как количество молей растворенного CaCO 3 относительно пройденных кулонов (верхняя абсцисса), полученное интегрированием тока за время эксперимента, и газовый эквивалент H 2 (нижняя абсцисса), рассчитанный в предположении, что скорость электролиз равен току ячейки (т. е. побочных реакций нет). Красная пунктирная линия на фиг. 5 представляет стехиометрическую реакцию, в которой каждые 2 протона, образующиеся на аноде в реакции с выделением кислорода, протонируют 1 ион карбоната.Планки погрешностей для каждой точки данных соответствуют накопленной ошибке взвешивания, основанной на точности весов. Аппроксимация методом наименьших квадратов по всем точкам данных дает отношение скорости химической реакции к скорости электролиза 0,85 по сравнению с максимальным значением 1. Это демонстрирует, что высокая кулоновская эффективность возможна даже при использовании неоптимизированного реактора лабораторного масштаба. . Для обоих электролитов данные за самое долгое время (крайние правые точки данных) показывают снижение эффективности, что и в других экспериментах ( SI Приложение , рис.S1) связано с пассивацией катода Ca (OH) 2 при длительном времени работы реактора. Обратите внимание, что некоторые точки данных лежат выше линии максимальной теоретической эффективности. Мы связываем это отклонение с некоторой непреднамеренной потерей CaCO 3 во время удаления чашки, содержащей CaCO 3 , из реактора. Мы также попытались напрямую измерить количество Ca (OH) 2 , продуцируемого в этих экспериментах, но не смогли восстановить весь Ca (OH) 2 , осажденный в клетках (например,g., со стенок ячеек) или для эффективного удаления всего осадка на бумажном сепараторе. Очевидно, что могут быть спроектированы более совершенные реакторы, в которых имеется больший контроль над конвекцией и химическими градиентами, и в которых осажденный Ca (OH) 2 собирается более эффективно, в том числе непрерывно. Такие усовершенствования конструкции реактора выходят за рамки данной статьи. Даже в этом случае нынешний КПД близок к термическому КПД обычного прекальцинатора цемента, который декарбонизирует около 90% поступающего CaCO 3 .
Рис. 5.Кулоновская эффективность реактора декарбонизации, измеренная в 13 экспериментах, каждый из которых начинался со свежесобранной H-ячейкой типа, показанного на рис. 2. Потеря массы CaCO 3 из-за растворения отложена в зависимости от общего пройденного заряда. через систему (верхняя абсцисса) и эквивалентные моли водорода, производимые на катоде (нижняя абсцисса), рассчитанные в предположении, что весь ток идет на электролиз. Красная пунктирная линия представляет стехиометрическую реакцию, дающую максимальную эффективность преобразования на основе заряда, а черная пунктирная линия представляет собой аппроксимацию данных методом наименьших квадратов, наклон которой соответствует ~ 85% кулоновской эффективности.
Продемонстрировав эффективность предложенного реактора декарбонизации, мы обратили наше внимание на оценку пригодности твердого продукта Ca (OH) 2 в качестве предшественника портландцемента. Самым распространенным минералом в портландцементе, составляющим от 50 до 70% по весу, является алит, 3CaO · SiO 2 . Были приготовлены смеси Ca (OH) 2 и мелкодисперсного порошка SiO 2 , а также контрольный образец из покупного порошка CaCO 3 , смешанного с тем же SiO 2 , в молярном соотношении алита 3: 1. соотношение.Смешанные порошки подвергались термообработке в широком диапазоне температур. На рис. 6 A и B показаны рентгенограммы и СЭМ-изображение смеси Ca (OH) 2 + SiO 2 после нагревания до 600 ° C в течение 2 часов на воздухе. В отличие от CaCO 3 , который не разлагается до 898 ° C (при 1 атм P CO2 ), Ca (OH) 2 имеет термодинамическую температуру разложения 512 ° C (при 1 атм P h3O ) и здесь уже разложился до CaO при обжиге при 600 ° C, хотя CaO еще не прореагировал с SiO 2 с образованием алита.После нагревания в течение 2 часов при 1500 ° C, типичной температуре цементной печи, и охлаждения путем отключения питания печи смесь прореагировала с образованием низкотемпературной полиморфной модификации алита T1 (ICSD: 4331), как показано рентгеновской дифрактометрией. узор на рис.6 C . Известно, что полиморфизм алита зависит от природы и количества примесей в сырье, а также от скорости охлаждения от температуры печи (33). В то время как высокотемпературные полиморфы M1 и M2 чаще всего получают в промышленных процессах, полиморф T1, который мы получили в медленно охлаждаемых образцах, считается столь же цементирующим (33–35).Рис. 6 D показывает, что частицы алита, полученные из наших прекурсоров, имеют размер менее 30 мкм, что находится в пределах диапазона, необходимого для коммерческих портландцементов (12). На рис. 6 E и F показаны карты состава кальция и кремния, из которых очевидна однородность состава алита. Фиг.7 A и B показывают рентгенограмму и изображение с помощью сканирующего электронного микроскопа соответствующей смеси CaCO 3 и SiO 2 после нагревания до 600 ° C в течение 2 часов на воздухе, а на рис.7 C и D показывают результаты после нагревания до 800 ° C в течение 2 часов на воздухе. При 600 ° C значительного разложения не произошло, тогда как при 800 ° C CaCO 3 разложился до CaO, но реакция на алит не началась. После нагревания до 1500 ° C в течение 2 ч (рис. 7 E и F ) XRD показывает, что образовалась фаза алита. Однако остается некоторое количество непрореагировавшего CaO, 6% согласно уточнению Ритвельда спектров XRD. СЭМ-изображение на рис.7 F по сравнению с фиг. 6 D показывает, что алиты, производные из Са (ОН) 2 — и СаСО 3 , в конечном итоге достигают аналогичных морфологий и размеров частиц. Эти результаты показывают, что электрохимически полученный Ca (OH) 2 из нашего реактора декарбонизации является подходящим предшественником для синтеза основной гидратирующей фазы силиката кальция в портландцементе. Более того, из-за мелкодисперсной морфологии осадка (по сравнению, например, с измельченным известняком) и его более низкой температуры разложения на> 300 ° C, по-видимому, он имеет улучшенную реакционную способность по сравнению с CaCO 3 , что может привести к сокращению времени обжига и / или температуры, которые снижают потребление энергии на стадии высокотемпературной реакции.
Рис. 6.Синтез алита, 3CaO-SiO 2 , с использованием Ca (OH) 2 , полученного в реакторе декарбонизации. ( A ) Рентгенограмма и ( B ) СЭМ-изображение смеси Ca (OH) 2 и SiO 2 после нагревания до 600 ° C в течение 2 часов на воздухе. Ca (OH) 2 разложился до CaO, но еще не прореагировал с SiO 2 с образованием фазы алита. После обжига при 1500 ° C в течение 2 часов ( C ) XRD-диаграмма показывает однофазный алит, морфология которого показана на SEM-изображении в D .Карты состава ( E и F ) кальция и кремния, соответственно, показывают равномерное распределение обоих элементов.
Рис. 7.Синтез алита с использованием CaCO 3 и SiO 2 показывает более низкую реакционную способность, чем с Ca (OH) 2 . После нагревания до 600 ° C в течение 2 часов на воздухе рентгенограмма ( A ) и изображение ( B ) SEM показывают, что CaCO 3 еще не разложился до CaO. После нагревания до 800 ° C в течение 2 часов на воздухе рентгенограмма ( C ) показывает, что CaCO 3 разложился до CaO, но еще не прореагировал с SiO 2 с образованием фазы алита.( D ) СЭМ-изображение полученной смеси порошков CaO и SiO 2 . После обжига при 1500 ° C в течение 2 часов на воздухе рентгенограмма ( E ) показывает смесь алита с некоторым остаточным CaO. ( F ) СЭМ-изображение этой неполностью прореагировавшей смеси.
Обсуждение
Помимо производства реакционноспособного Ca (OH) 2 , подходящего для синтеза цемента, наш реактор декарбонизации на основе электролиза производит концентрированные газовые потоки H 2 на катоде и O 2 и CO 2 (в молярном соотношении 1: 2 при работе с высоким кулоновским КПД) на аноде.Эти газы являются важными компонентами в широком спектре устойчивых технологий, которые в настоящее время используются во всем мире, и открывают несколько возможных синергий между производством цемента и этими технологиями, которые мы сейчас обсуждаем.
Улавливание и связывание углерода (CCS) на уровне цементного завода на сегодняшний день сосредоточено на улавливании CO 2 после сжигания в сочетании с использованием кислородного сжигания. Поток O 2 / CO 2 из нашего реактора декарбонизации может сделать эти процессы более простыми и эффективными.Улавливание после сжигания относится к технологиям улавливания CO 2 из выхлопных газов печи, таким как образование петель кальция, очистка амином и мембранная фильтрация (36⇓ – 38). Кислородное топливо, или сжигание с повышенным содержанием кислорода, относится к сжиганию ископаемого топлива (здесь, в первую очередь, угля) с кислородом вместо воздуха (37, 39). Кислородное сжигание в первую очередь приводит к повышению эффективности использования топлива, поскольку азот, содержащийся в воздухе, не должен нагреваться. Во-вторых, отсутствие азота допускает более высокие температуры пламени без выделения оксидов азота (NO x ), которые имеют потенциал глобального потепления в 298 раз больше, чем CO 2 в пересчете на массу (40), а также способствуют образованию смога, кислотные дожди и истощение озонового слоя.В-третьих, дымовой газ от сжигания кислородного топлива имеет более высокую концентрацию CO 2 и меньше примесей NO x (37, 41), что делает улавливание углерода более эффективным. Таким образом, на цементном заводе, использующем наш реактор декарбонизации, газовая смесь O 2 / CO 2 может использоваться в качестве кислородного топлива в высокотемпературной печи для снижения энергопотребления и выбросов NO x . Среди других преимуществ обогащения кислородом, 1 эксперимент в промышленном масштабе с использованием обогащения кислородом от 30 до 35% привел к увеличению производства цементных печей на 25-50% (42).Кроме того, кислородное сжигание оказывает незначительное, если не благотворное, влияние на качество портландцементного клинкера (39, 43⇓⇓⇓ – 47).
Концентрация CO 2 в дымовых газах обычных цементных печей составляет ∼25% (48). Для химической абсорбции с аминами, наиболее технологически зрелый метод улавливания после сжигания для комбинированного потока (37, 38), увеличение концентрации CO 2 до 60%, как было показано, снижает потребность в тепле, энергии регенерации растворителя и стоимости пара. захвата (49⇓⇓⇓ – 53).Газовый поток из нашей камеры декарбонизации еще выше (67%), что должно сделать очистку амином более эффективной. Однако большим преимуществом может быть возможность полностью избежать дорогостоящих процессов CCS, таких как очистка амином. Поскольку здесь CO 2 доставляется в высококонцентрированной форме, смешанной только с O 2 (и некоторыми парами H 2 O), прямой улавливание с использованием тех же простых процессов сжатия (54, 55), которые сейчас используются для очищенных и концентрированный CO 2 .
Газообразный водород, производимый на катоде в нашей ячейке декарбонизации, имеет ценность в качестве сырья в основных отраслях промышленности, таких как производство аммиака и удобрений, переработка нефти и газа и перерабатывающая металлургия, и считается ключевым компонентом разработки технологий, которые могут декарбонизировать тяжелую промышленность. дежурный транспорт, авиация и отопление (56, 57). Объединенные газовые потоки также могут быть использованы в процессах утилизации CO 2 , которые производят жидкое топливо, такое как те, которые также используют водород и производят спирты.
Водород также может быть возвращен для поддержки цементного процесса (рис. 1). Его можно сжигать напрямую, чтобы обеспечить тепло или электроэнергию обратно в цементный завод, или потоки газа H 2 и O 2 / CO 2 могут снабжать топливный элемент, который генерирует электричество на месте для питания электрохимических реактор или другие производственные операции, такие как измельчение, перемешивание и транспортировка. При использовании твердооксидного топливного элемента (ТОТЭ) (58), который имеет самый высокий электрический КПД среди всех типов топливных элементов (от 60 до 80%) (59), вредное воздействие CO 2 на топливные элементы с протонообменной мембраной (60, 61) предотвращается, и типичные рабочие температуры ТОТЭ от 500 до 1000 ° C можно легко поддерживать, используя тепло от цементной печи (которая обычно работает при 1450-1500 ° C).Одновременно кислород будет удален из газового потока O 2 / CO 2 , дополнительно очищая CO 2 и упрощая связывание. Обратите внимание, что эта комбинация электрохимического реактора и ТОТЭ создает регенеративный топливный элемент (62), который обладает способностью накапливать энергию, если предусмотрено хранение реагентов, и тем самым может сглаживать прерывистость возобновляемой электроэнергии, используемой для питания цементного завода.
Поток CO 2 , созданный из ячейки декарбонизации, также может иметь значение в приложениях, которые производят повышающий цикл захвата CO 2 .CO 2 уже используется для увеличения нефтеотдачи (EOR) (63, 64) и для производства таких химикатов, как мочевина, салициловая кислота, метанол, карбонаты (65), синтетическое топливо (с помощью процесса Фишера-Тропша) (66) и синтетический природный газ (по реакции Сабатье) (67). Растет интерес к поиску способов электрохимической или фотохимической реакции на CO 2 для создания химикатов и топлива из захваченного CO 2 с использованием возобновляемой электроэнергии (68). Например, была продемонстрирована модельная установка, которая использует захваченный CO 2 для производства синтоплива (69).
Мы также рассмотрели возможность использования электрохимического процесса производства цемента исключительно с использованием возобновляемой электроэнергии. Возможно, наименее капиталоемкий способ использования выходных газов из реактора декарбонизации — это сжигание для нагрева цементной печи. Мы проанализировали потоки энергии в этой конфигурации; подробности приведены в приложении SI . Предполагая, что реактор декарбонизации работает с кулоновским КПД 85%, электролизер работает с КПД от 60 до 75% и сгорает образующиеся H 2 и O 2 для нагрева печи для спекания с КПД от 60 до 80%, входная электрическая энергия, необходимая для изготовления 1 кг цемента, равна 5.От 2 до 7,1 МДж. Это предполагает отсутствие энергетической выгоды от замены Ca (OH) 2 на CaCO 3 в процессе высокотемпературного спекания или других потенциальных преимуществ, таких как снижение капитальных и энергетических затрат на измельчение известняка (при условии, что эта функция заменена путем химического растворения). При эффективном сжигании на 80% H 2 и O 2 , полученных в ячейке декарбонизации, произведенная тепловая энергия немного превышает энергию, необходимую для спекания.Если сгорание имеет эффективность только 60%, 90% тепловой энергии, необходимой для спекания, может быть получено из газов электролизера (т. Е. Требуется ~ 0,5 МДж / кг дополнительной энергии). Этот дефицит энергии, а также электроэнергии для поддержки операций может быть восполнен за счет превышения емкости электролизера над стехиометрически необходимой для декарбонизации. Этот анализ предполагает, что процесс электрохимического цементирования с использованием возобновляемых источников энергии не потребует больших объемов дополнительной энергии, если таковая имеется.
Важный связанный с этим вопрос — это, конечно, стоимость процесса, основанного на электрохимии. Учитывая многочисленные возможные конфигурации, описанные выше, полный технико-экономический анализ выходит за рамки данной статьи. Стоимость срока службы и экономическая отдача для всей системы или любого из ее компонентов зависит от капитальных затрат, эффективности и долговечности, а также от стоимости цемента и газообразных побочных продуктов. Многие факторы стоимости в настоящее время неизвестны; например, стоимость срока службы реактора декарбонизации будет зависеть от его конкретной конструкции и характеристик, ни одна из которых еще не была оптимизирована.Поэтому мы ограничиваем наш технико-экономический анализ сравнением стоимости энергии электрохимического процесса с его аналогом, работающим на угле. Расчетное значение от 5,2 до 7,1 МДж / кг цемента для электрохимического процесса действительно превышает энергию, требуемую для обычного цементного процесса в средней обжиговой печи США, которая составляет 4,6 МДж / кг (70). При цене угля 61 доллар за тонну (для битуминозного угля) (71) стоимость энергии для обычного процесса составляет около 28 долларов за тонну цемента, что составляет 25% от средней цены продажи цемента в США, равной 113 долларов за метрическую тонну (13 ).Соответствующие затраты на электрохимический процесс, естественно, зависят от цены на электроэнергию и в некоторых случаях могут быть нулевыми или даже отрицательными, если они получены из возобновляемых источников. Однако для затрат на электроэнергию 0,02, 0,04 и 0,06 доллара за кВт⋅ч и при условии, что потребность в энергии для электрохимического процесса составляет 6 МДж / кг, что находится в середине нашего расчетного диапазона, стоимость энергии составляет 35-60 долларов, и 100 долларов за тонну цемента соответственно. Это говорит о том, что при отсутствии других соображений электрохимический процесс будет конкурентоспособным по стоимости по сравнению с обычными заводами (~ 28 долларов за тонну цемента), если электричество доступно по цене <0 долларов.02 за кВт⋅ч. Обратите внимание, что оптовая стоимость ветровой электроэнергии сейчас составляет 0,02 доллара США за кВт⋅ч или немного ниже на большей части территории Соединенных Штатов (72). Мы предполагаем, что ветровая электроэнергия будет доступна по этой цене для предлагаемых цементных заводов, например, от расположенной рядом ветряной электростанции.
Однако в этом сравнении затрат не учитываются затраты на улавливание и связывание углерода, которые для аминовой очистки обычного цементного дымового газа оцениваются примерно в 91 доллар за тонну (50).В смоделированной выше электрохимической последовательности, где электролитический H 2 сжигается для нагрева печи, стоимость прямого улавливания CO 2 из потока O 2 / CO 2 , показывающего реактор декарбонизации, должна составлять менее 40 долларов. за тонну (50). Это изменит чистые затраты на электроэнергию в пользу электрохимического процесса в среде, где политика требует удаления углерода и где доступна недорогая возобновляемая электроэнергия.
Наконец, следует учитывать водоемкость такого процесса на основе электролизера.На каждый килограмм цемента, изготовленного с использованием предлагаемой камеры обезуглероживания, потребуется 0,4 кг воды; это означает, что средняя обжиговая печь в США, производящая 1800 тонн цемента в день, потребует ~ 760 тонн воды в день. Однако половина этой воды будет извлечена при дегидратации Ca (OH) 2 . Если в качестве топлива для печи использовался H 2 , другая половина воды могла бы конденсироваться из дымовых газов. В принципе, вся вода, используемая для электролиза, может быть переработана.
Выводы
Мы предлагаем и демонстрируем электрохимический процесс синтеза цемента, в котором CaCO 3 декарбонизируется, а Ca (OH) 2 осаждается в градиенте pH, создаваемом электролизером с нейтральной водой, в то время как концентрированные газовые потоки H 2 и O 2 / CO 2 производятся одновременно.Мелкодисперсный порошок Ca (OH) 2 используется для синтеза фазово-чистого алита, основной вяжущей фазы в обычном портландцементе. Концентрированные газовые потоки из этого процесса могут использоваться синергетически с другими процессами, находящимися в стадии разработки для устойчивых промышленных технологий. Среди нескольких альтернатив CO 2 может быть непосредственно захвачен и изолирован; H 2 и / или O 2 могут использоваться для выработки электроэнергии через топливные элементы или камеры сгорания; O 2 может использоваться как компонент кислородного топлива для дальнейшего снижения выбросов CO 2 и NO x из цементной печи; или выходные газы могут использоваться для синтеза продуктов с добавленной стоимостью, таких как жидкое топливо.Показано, что наши лабораторные прототипы реакторов декарбонизации способны работать с кулоновской эффективностью, близкой к теоретической, когда каждые 2 протона, образующиеся на аноде во время электролиза, растворяют 1 формульную единицу CaCO 3 . В таких условиях произведенный электролитический водород, если он сгорает, может обеспечить большую часть или всю тепловую энергию, необходимую для высокотемпературного спекания цемента. Эти результаты предлагают путь к рентабельному производству цемента без выбросов, при котором вся энергия вырабатывается из возобновляемых источников.
Материалы и методы
Ячейки для декарбонизации.
Н-элементы, разработанные по индивидуальному заказу, были изготовлены James Glass, Inc. Электролитом был 1 М NaClO 4 или NaNO 3 (Sigma-Aldrich, ≥98%), растворенный в деионизированной воде. Эти электролиты были выбраны потому, что их соли кальция растворимы и не разлагаются при высоком напряжении. Оба электрода были изготовлены из платины: стержень у катода и проволока у анода (MW-1032; BASi). Платина была выбрана потому, что она обладает высокой каталитической активностью в отношении выделения водорода и кислорода как в кислоте, так и в основании.Альтернативные недорогие электродные материалы могут включать никель, медь или нержавеющую сталь для катода (pH 12,5) и Al, Sn или Pb для анода (pH 6). Порошок CaCO 3 (Sigma-Aldrich, ≥99%) добавляли в анодное отделение. Фильтровальная бумага (28310-015, задержка частиц 5 мкм; VWR) использовалась в качестве пористого сепаратора. Потенциостатические эксперименты проводили с использованием потенциостата Bio-Logic Science Instruments VMP3. Все тесты проводились при комнатной температуре.
XRD-анализ.
Рентгенограммы были получены с использованием XRPD PANalytical X’Pert PRO с использованием излучения Cu и тета: тета-гониометра с вертикальным кругом с радиусом 240 мм.Конфигурация этого инструмента по умолчанию — геометрия Брэгга – Брентано с высокоскоростным позиционно-чувствительным детектором высокого разрешения X’Celerator, использующим предметный столик Open Eulerian Cradle. Данные XRD анализировали с помощью Highscore, версия 4.7.
SEM Характеристика.
СЭМ-визуализация и анализ состава образцов проводились с использованием прибора Phenom XL, оснащенного энергодисперсионным детектором рентгеновского излучения (nanoScience Instruments), работающего при ускоряющем напряжении 10 кВ для визуализации и 15 кВ для энергодисперсионного рентгеновского излучения. лучевой спектроскопический анализ.
BET Характеристика.
Quantachrome Instruments NOVA 4000E (Anton Paar QuantaTech) использовали для выполнения многоточечного БЭТ-анализа удельной поверхности порошка.
Синтез алита.
Электрохимически осажденный Ca (OH) 2 или CaCO 3 (Sigma-Aldrich, ≥99%) смешивали с SiO 2 (99,5%, 2 мкм; Alfa Aesar) в молярном соотношении 3: 1. Порошки смешивали в суспензии с этанолом, а затем сушили. Полученные хорошо перемешанные порошки прессовали в таблетки.Гранулы помещали в платиновые тигли и нагревали со скоростью 2 ° C в минуту до 1500 ° C в муфельной печи (Thermolyne F46120-CM). Температуру поддерживали на уровне 1500 ° C в течение 2 ч, затем окатыши охлаждали в печи путем отключения питания. Рентгеноструктурный анализ подтвердил алитность полученных порошков.
Благодарности
Эта публикация основана на работе, финансируемой Сколковским институтом науки и технологий (Сколтех), программой «Центр исследований, образования и инноваций в области электрохимического хранения энергии» по контракту 186-MRA.L.D.E. выражает признательность за поддержку программы стипендий для докторантов Banting, осуществляемой правительством Канады. Мы благодарим Исаака Меткалфа, Натана Корбина, Киндл Уильямс и Картиша Мантирама (Массачусетский технологический институт) за помощь в проведении экспериментов; Мухаммаду Адилу и 24 M Technologies, Inc. за выполнение измерений BET; и Form Energy, Inc. за предоставление доступа к Phenom XL SEM. В этой работе использовались общие экспериментальные установки, частично поддерживаемые Программой центров материаловедения и инженерных центров Национального научного фонда в рамках награды DMR-1419807.
Сноски
Автор: L.D.E. и Y.-M.C. спланированное исследование; L.D.E., A.F.B., M.L.C. и R.J.-Y.P. проведенное исследование; L.D.E., A.F.B. и Y.-M.C. проанализированные данные; и L.D.E., A.F.B. и Y.-M.C. написал газету.
Заявление о конфликте интересов: Y.-M.C., L.D.E. и A.F.B. являются изобретателями по патентным заявкам, поданным Массачусетским технологическим институтом в отношении определенного предмета статьи.
Эта статья является результатом исследования Артура М.Коллоквиум Саклера Национальной академии наук «Состояние и проблемы декарбонизации нашего энергетического ландшафта» прошел 10–12 октября 2018 г. в Центре Арнольда и Мейбл Бекман Национальной академии наук и инженерии в Ирвине, Калифорния. Коллоквиумы НАН начались в 1991 г. и с 1995 г. публикуются в PNAS. С февраля 2001 г. по май 2019 г. коллоквиумы поддерживались щедрым подарком от Дамы Джиллиан и д-ра Артура М. Саклера Фонда искусств, наук и гуманитарных наук в память мужа дамы Саклер, Артура М.Саклер. Полная программа и видеозаписи большинства презентаций доступны на веб-сайте NAS http://www.nasonline.org/decarbonizing.
Эта статья представляет собой прямое представление PNAS.
См. В Интернете сопутствующий контент, например, комментарии.
Эта статья содержит вспомогательную информацию в Интернете по адресу https://www.pnas.org/lookup/suppl/doi:10.1073/pnas.1821673116/-/DCSupplemental.
Рыночная стоимость электролизера к 2030 году достигнет 53 миллиардов долларов, утверждает
Селбивилль, Делавэр, август.30, 2021 (GLOBE NEWSWIRE) —
Ожидается, что выручка мирового рынка электролизеров превысит 53 миллиарда долларов к 2030 году, как сообщается в последнем исследовании Global Market Insights Inc., в связи с крупномасштабной интеграцией возобновляемых источников энергии. и постоянное развитие водородной инфраструктуры. Увеличение доли автомобилей с водородным двигателем наряду с нормативными нормами, направленными на снижение выбросов углерода, положительно повлияет на спрос на продукцию.
Сегмент мощности <500 кВт получит заметный импульс благодаря устойчивому росту в коммерческом секторе и смещению акцента на устойчивые источники производства электроэнергии.Повышение применимости к малым ТЭЦ, автономному и мобильному электроснабжению усилит рост бизнеса. Постоянное развитие умных и эффективных предприятий наряду с крупномасштабными программами электрификации будет стимулировать отраслевую статистику.
Запрос образца этого исследовательского отчета @ https://www.gminsights.com/request-sample/detail/4787
Выделение водорода по мере расширения производственной базы связано с его давний потенциал в качестве решения для экологически чистой энергии, ускоряющий спрос на продукцию.Текущие инициативы соответствующих государственных органов по использованию топлива с низким уровнем выбросов в сочетании с мандатами по ограничению общих уровней выбросов в промышленности призваны активизировать динамику отрасли.
Некоторые основные выводы отчета о рынке электролизеров включают:
- Отрасль электролизеров растет за счет увеличения инвестиций государственных и частных игроков в экологически безопасные варианты.
- Сдвиг в сторону FCEV как альтернативы обычным автомобилям будет способствовать проникновению продукции.
- Ключевыми игроками, работающими на рынке, являются Air Liquide, Siemens Energy, Plug Power, ITM Power и McPhy Energy.
- Растущие инвестиции в крупномасштабное производство водорода на месте для хранения возобновляемой энергии послужат топливом для промышленности щелочных электролизеров.
Просмотрите ключевые отраслевые идеи на 340 страницах с 475 таблицами рыночных данных и 36 рисунками и диаграммами из отчета «Прогнозы рынка электролизеров по продуктам (щелочной электролизер, электролизер PEM, твердооксидный электролизер), технологический процесс (≤ 500 кВт ,> 500 кВт — 2 МВт, более 2 МВт), Применение (производство электроэнергии, транспорт, промышленность, сырье, отопление зданий и электроэнергетика), Отчет об анализе отрасли, региональный прогноз, потенциал применения, рыночная доля и прогноз на 2021 год — 2030 ”подробно вместе с оглавлением:
https: // www.gminsights.com/industry-analysis/electrolyzer-market
COVID-19 оказывает влияние на мировую экономику; даже после возобновления деятельности несколько стран сталкиваются с проблемами при возобновлении производства, и многие крупномасштабные проекты откладываются. Благоприятные правительственные инициативы по ускорению операций и началу внедрения новых проектов будут активизировать бизнес-сценарий.
В период с 2021 по 2030 год рынок электролизеров в Северной Америке должен вырасти более чем на 28% в год.Растущее внедрение легковых и грузовых автомобилей с водородным двигателем в сочетании с растущим парком электромобилей положительно повлияет на отраслевые прогнозы. Например, партнерство California Fuel Cell в 2018 году объявило о достижении цели создания пяти миллионов автомобилей с нулевым уровнем выбросов к 2030 году. Модернизация существующей газовой и жидкостной инфраструктуры для транспортировки топлива будет способствовать расширению бизнеса.
Просмотрите содержание этого отчета @ https://www.gminsights.com/toc/detail/electrolyzer-market
О Global Market Insights
Global Market Insights Inc.со штаб-квартирой в Делавэре, США, является поставщиком глобальных маркетинговых исследований и консалтинговых услуг, предлагающим синдицированные и индивидуальные отчеты об исследованиях наряду с консультационными услугами по развитию. Наши отчеты о бизнес-аналитике и отраслевых исследованиях предлагают клиентам проницательную информацию и практические рыночные данные, специально разработанные и представленные для помощи в принятии стратегических решений. Эти исчерпывающие отчеты разработаны с использованием собственной исследовательской методологии и доступны для ключевых отраслей, таких как химическая промышленность, современные материалы, технологии, возобновляемые источники энергии и биотехнологии.
.